
Scrap metal processing yards have a reputation in every equipment sector that supplies them as harsh work environments. Metal-on-metal compression, shearing and size reduction is part of the process; dust is produced and can cause damage to sensitive components; and some operations are outdoors in ever-changing weather.
Two scrap metal shears made more than four decades ago in Cordele, Georgia, by Harris have endured these conditions in northern Ohio—where the seasons strike hot and cold as much as anywhere else in the country—in yards currently owned and operated by New Jersey-based Metalico Inc.
In Akron, Ohio, a 1980-vintage Harris BSH-1025-26 stationary shear cuts through steel I-beams, pipe, cast iron rebar and other types of structural steel, as well as oversized aluminum, according to Metalico Akron General Manager Don Fleming.
Not to be outdone, a Harris BSH-1003-26 shear that dates back to the mid-1970s is cutting through the same types of steel and aluminum, as well as fencing, farm machinery and metal tanks that flow into a Metalico Youngtown, Ohio, yard, according to Mark Chapman, operations manager there.

Harris BSH shears serve in such capacities around the world. The units are designed with a “tuck-and fold” compression box that squeezes large and bulky items fed into the shear hopper. Once compressed, the metal is sheared by a blade driven by a powerful hydraulic system designed to produce sufficient power while consuming minimal energy.
As the 40-years-plus lifespans of the two units on the job for Metalico show, a decades-old Harris BSH shears brochure promoting “heavy-duty construction” to provide “many years of proven life and durability” was more than just advertising copy.
Chapman says the Harris shear in Youngstown has likely processed more than 100,000 tons of scrap just since 2005, with no way for him to know how much it may have handled in the 30 years before then when “it was with another company.”
In Akron, Fleming says that shear has processed at least 300,000 tons of scrap metal, and even at 40 years old, it continues to cut through 50 to 60 tons per day three to five days per week.
Fleming and Chapman says they work with Harris directly and with an authorized dealer to obtain parts and help with non-routine service. Even though the units are 40 and 45 years old, Chapman says service from Harris is impeccable. “Support from Harris has been great here. If the dealer doesn’t have it, Harris gets it made and to us in a timely manner,” he comments.
More information on the newest models of durable, reliable and productive Harris scrap metal shears can be found at https://harrisequip.com/products/shears.
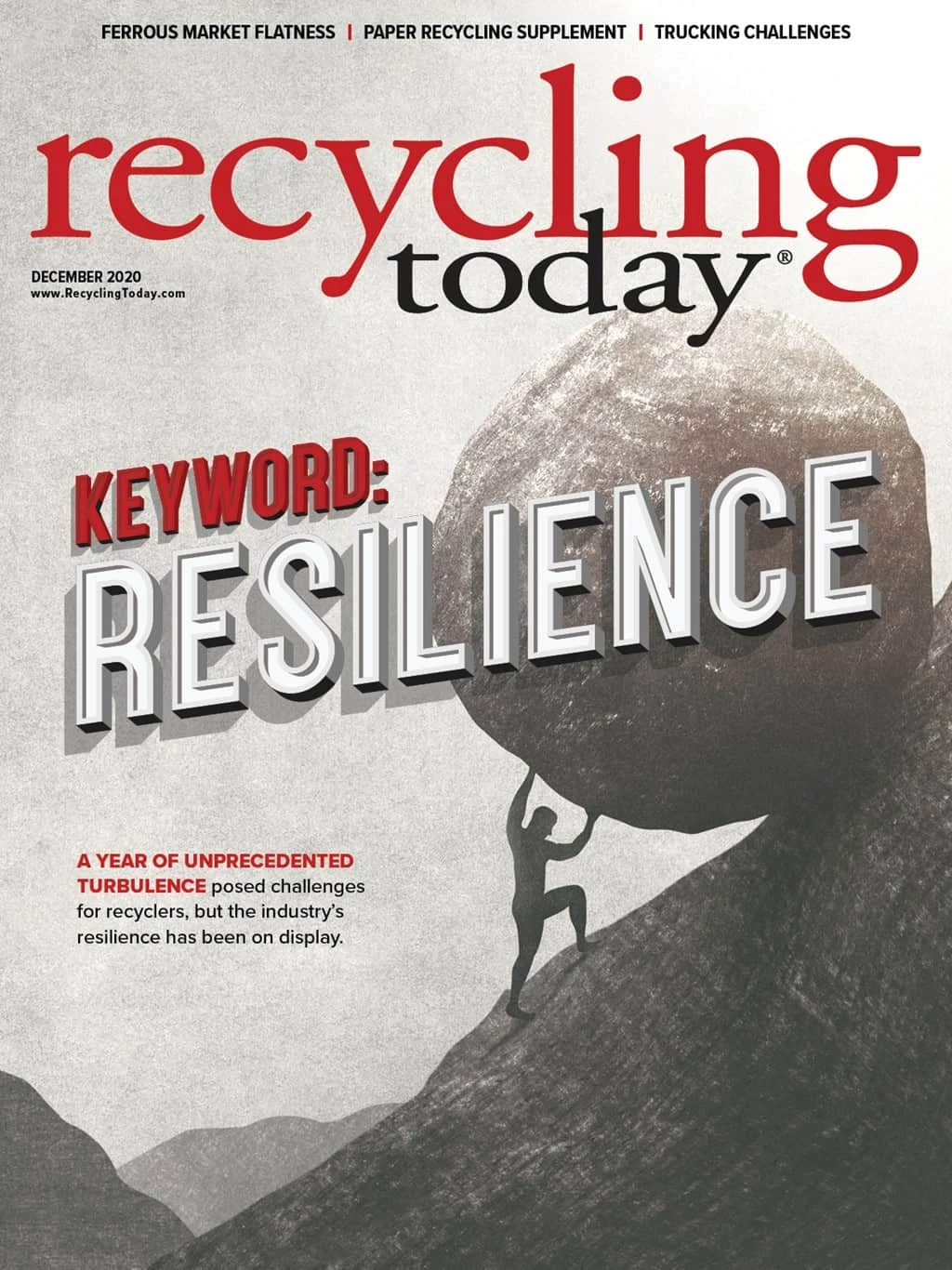
Explore the December 2020 Issue
Check out more from this issue and find your next story to read.
Latest from Recycling Today
- Athens Services terminates contract with the city of San Marino, California
- Partners develop specialty response vehicles for LIB fires
- Sonoco cites OCC shortage for price hike in Europe
- British Steel mill’s future up in the air
- Tomra applies GAINnext AI technology to upgrade wrought aluminum scrap
- Redwood Materials partners with Isuzu Commercial Truck
- The push for more supply
- ReMA PSI Chapter adds 7 members