
The owner of AFS Recycling in Tennessee calls installing a two-ram Harris Gorilla baler one of the best decisions he has ever made.
A career that spans decades in the recovered paper business has taught Keith Wilson of AFS Recycling, Jackson, Tennessee, that having a reliable baler is the cornerstone of a productive recycling facility.
Wilson spent two decades processing and trading recovered paper for two global companies before venturing out on his own and founding All Fiber & Scrap (AFS) Recycling in Jackson. While old corrugated containers (OCC) and other paper grades make up a large percentage of what AFS handles, the company also bales and ships several grades of plastic, plus aluminum and steel cans and aluminum siding.
Throughout his career, Wilson became familiar with the reliability of the balers made by Georgia-based Harris, including Harris HRB models and those carrying the legacy Selco model names, such as Gorilla and Badger. “The Harris balers performed well, and the service on the balers was easily maintained by many different companies,” Wilson says.
Therefore, Wilson says he was glad to see a Harris/Selco baler in place when he purchased an existing recycling plant that would serve as the home of AFS Recycling. He turned to Ohio-based Harris dealer Ely Enterprises for “a complete reline of the inner parts of the baler and both rams,” Wilson says. “This gave new life for an additional eight years of service."“I would totally recommend the Harris Gorilla baler for any plant with various grades to process.” – Keith Wilson, AFS Recycling
However, after 32 years on the job, the older Gorilla model finally reached the end of its useful life and Wilson was confronted with the need to make a quick decision to keep his plant up and running. He had no qualms about notifying Ken Ely at Ely Enterprises that he trusted Harris.
“I knew then I wanted a newer, faster and bigger Harris baler to handle the growth of my plant volume and the multiple grades I was processing as well,” the veteran recycler says.
The growth AFS was experiencing and the changing nature of the recycling sector prompted certain requirements. “I ordered this new baler with a [bale separation] door, larger hopper size and larger motors to give us speed and export size bales with good bale weights,” he says. “This gave us more options on the sell side of the business and the opportunity to process various grades of nonpaper items as well.”

The model that met the productivity and materials diversity aspects of what AFS needed was the two-ram Gorilla. “The Gorilla model gave us all the options above and the proven track record in the field; it made this an easy decision for us,” Wilson says. “The toughness needed for this industry and the solid build/design of the baler meant it was no question the choice to make for our business model.”
Just as crucially for AFS, Harris and its dealer Ely Enterprises were able to deliver and install the Gorilla at a speed almost unheard of in today’s world of equipment back orders and supply chain-related delays.
“Ely Enterprises was able to get us up and running and quickly making new bales within a six-day window of removal of the old baler followed by delivery and installation of the new Harris Gorilla,” Wilson says. “The process was streamlined and helped us catch up with our processing schedule in less time. This allowed us to have really no effect on cash flow and production at the facility, with limited overtime."
The workforce at AFS has appreciated the Gorilla since it arrived on the job. “The operation of the baler is easy, and the employees love the baler,” Wilson says. “The [bale separation] door has helped us with grade changes with less mess and clean up, as well. The ease of the operational screen and the fully automatic system gives the operator time to do other things around the baler and help prepare for other grades to bale.”
The Gorilla’s impact on AFS also has been noticeable on the income statement. “We currently run the baler an average of seven hours per day,” Wilson says. “This gives us one hour to clean and maintain any issues during normal work time.
“Our volume has grown with new grades of plastic and metals,” he continues. “So, we are processing more in fewer hours at the facility, which has helped us to pay off the investment at a faster pace.”

Wilson adds, “The baler is producing heavier bales, and less wire is needed for the same tonnage. This is an additional savings as well for the facility.
“I would totally recommend the Harris Gorilla baler for any plant with various grades to process,” he continues, saying that Harris has been a reliable brand for recyclers for decades for good reasons. “Harris has a proven track record, and they stand behind the equipment as well. The balers are well-built, service after the sale is great and the production and speed of the baler will make the facility more efficient and profitable for the owner.”
Wilson concludes, “I am so glad I made the choice to spend the money to have the Harris Gorilla installed. It is one of the best decisions I have made with my own money.”
More information on the Gorilla and other high-productivity, two-ram Harris balers is at https://harrisequip.com/products/two-ram-balers.

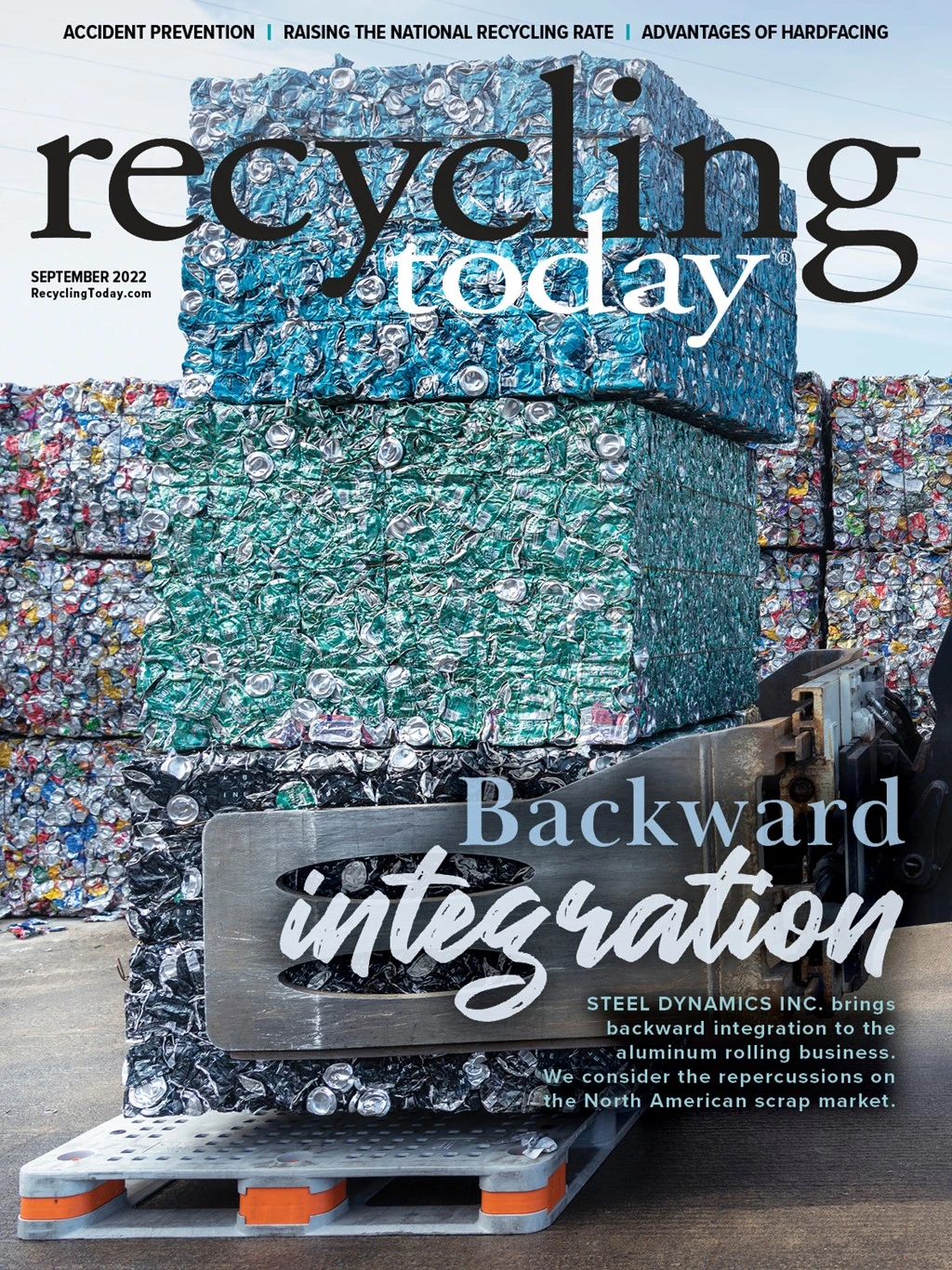
Explore the September 2022 Issue
Check out more from this issue and find your next story to read.
Latest from Recycling Today
- ReMA opposes European efforts seeking export restrictions for recyclables
- Fresh Perspective: Raj Bagaria
- Saica announces plans for second US site
- Update: Novelis produces first aluminum coil made fully from recycled end-of-life automotive scrap
- Aimplas doubles online course offerings
- Radius to be acquired by Toyota subsidiary
- Algoma EAF to start in April
- Erema sees strong demand for high-volume PET systems