![]() Kendrick Burgess |
When members of the Burgess family decided it was time to add shredding capacity to their St. Joseph, Mo., scrap processing business, they had many options. But Kendrick Burgess and his father Kenneth Burgess of Midwest Scrap Management were particularly impressed with the product offered by Harris.
In 2002, Harris Shredder and the Burgesses installed a Harris 6090 model, with a 60-inch wide rotor and a 90-inch internal width from liner to liner at their St. Joseph facility.
The new shredding plant instantly upgraded the ability of Midwest Scrap Management to take in more material and to do its own processing, and the Harris reputation for quality that they bought into has proven to be accurate.
A Winning Wager |
Just because its scrap company is based in Las Vegas doesn’t mean Silver Dollar Recycling wanted to gamble with its purchase of a shredder in 2001. To some extent, though, Silver Dollar did place a wager when it became one of the first companies to house a Harris shredder at its North Las Vegas, Nev., facility. The company’s HS98115 model was installed in late 2001 and immediately began chewing through inventory the company had collected throughout the summer. "The machine has been fantastic," says Jim Brewer, chief operating officer of Silver Dollar Recycling. Brewer has been impressed with the quietness of the plant and the innovative design of the reject door, which allows unshreddables to be rejected quickly, before any damage is done and with almost no blocking of material flow through the plant. The company runs a wide variety of material through the plant, with auto bodies making up about 50 percent of what is shredded, according to Brewer. Shredder operator Cindy Jo Gorman says the controls were easy to learn, and that the plant offers good monitoring capabilities in the control room. "The ferrous tonnage is measured on the outgoing belt. You can see the hourly output rate, as well as daily, weekly or monthly tonnage totals," says Gorman. Adds Brewer, "This is the best-built shredder I have ever operated. It’s easy to operate, maintenance is a breeze and the mill is extremely well built and quiet. Since we have installed the Harris shredder, we have increased production more than 300 percent from our previous unit while decreasing our overall maintenance costs by 200 percent." Though not necessarily wishing to place a wager on it, Brewer adds, "I expect this machine will outlive us all here at Silver Dollar." |
"We looked at a lot of mills, and with most of them, after two or three years, it looked like they were falling apart," says Kendrick.
But their own experience with Harris has been much different. "We run it to death, powered by a 1500 hp motor and it still looks like new," Kendrick remarks
The Harris unit’s productivity also gets high marks. "It chews through an automobile in about 35 seconds, which is competitive with a lot of 80-inch mills out there," Kendrick comments.
The shredder overall has won rave reviews from the Burgesses. "We’re more than happy with it; we’ve seen it do things and handle materials that competing 60-inch machines just can’t do," says Kendrick.
The positive reviews have also resulted in a big-budget sequel. Less than three years after taking delivery of their Harris 6090 Shredder, the Burgesses signed on to install a Harris 125125 super-sized shredder at a new Midwest Scrap Management facility in Kansas City, Mo.
The mammoth shredder is being installed at the site of the former Georgetown (GST) steel mill in Kansas City, where Midwest Scrap Management is setting up shop to extend its market reach.
In terms of anticipated return on investment, Kendrick is quick to point to the machine’s productivity. "This shredder will replace the work currently being done by a guillotine shear, a baler and what would have been done by a smaller shredder. It’s a three-in-one machine that can process plate steel, tank steel and any number of important grades," he notes.
His experience with the Harris HS6090 has convinced him that key design features and the ease of maintenance of Harris shredders will also help keep operating costs down. "The Harris side-feed system is automatically a competitive edge," Kendrick comments. "Maintenance is virtually reduced to a little bit of greasing that needs to be done and pulling and flipping hammers, which can take about 45 minutes per day. With a lot of other mills, it seems like it’s half of their production time going to maintenance."
Global Attention |
The Harris reputation for quality and durability extends far beyond North America. The success of Harris in international markets reaches back many years, and as in America, it is understood by scrap recyclers on other continents that once a Harris machine is in place, it will stay on the job for decades. Americans in the scrap industry who travel abroad will commonly find Harris equipment deployed in scrap yards in Europe, Latin America and other parts of the world Its reputation for quality and reliability has helped Harris become a shredder of choice right from the beginning in international markets, with plants being installed in Mexico, Guatemala and Peru, and another installation underway in Italy. In 2004, Harris Shredder installed an HS 98115 shredder for South American steel company Corporacion Aceros Arequipa S.A., located in Pisco, Peru. The shredder plant, with a 98-inch-wide rotor, is now on the job producing between 120 and 160 tons per hour of scrap feedstock for the Peruvian steel mill. |
Another factor that has kept the cost of ownership low is the incredible lifespan of wear components in the HS6090. "We run the HS6090 seven days a week, sometimes, but probably have only bought about five containers of wear parts in the past three years," says Kendrick. "The eject door quickly rejects unshreddables, so they don’t bounce around off the grates. It results in a lot less damage and longer wear life."
The super-sized Harris 125125 will allow Midwest Scrap Management to take on any and all forms of scrap, and Kendrick Burgess is confident the machine will live up to its potential. "A lot of other manufacturers produce machines that can never produce at the rate they say; the Harris Shredder has not only lived up to what was promised, but has actually produced more than what was quoted," Kendrick remarks.
Support and service have also exceeded expectations, says Kendrick, who credits Javier Herrera of Harris for getting everything off to a good start and the Harris organization for committing to its product.
"Their maintenance and troubleshooting system connects right to our shredder control booth, and they usually know when something is wrong before we do," says Kendrick. "They have technical people who can help us troubleshoot and answer any questions in a time frame from a few minutes to an hour."

The high production rate and low cost of ownership have convinced Kendrick that the new plant will quickly pay off, especially with the added bonus of trucking fuel savings for keeping Kansas City scrap in Kansas City rather than taking it to the St. Joseph shredder 60 miles away. "This shredder will justify itself after a few months of labor savings and trucking costs saved, so it solves a couple of problems at once."
There is no doubt in Kendrick’s mind that the HS125125 will match the HS6090 his company already runs in terms of quality and durability—making Harris the right choice.
"For anyone considering buying a shredder, I would tell them to look at a few other shredders and then come see a Harris. The durability is unimaginable, and you have to see the difference. They’re very sturdy—I’d never go with another shredder, and it’s safe to say that Harris will be producing all of our equipment from now on."
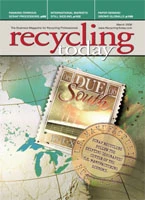
Explore the March 2006 Issue
Check out more from this issue and find your next story to read.
Latest from Recycling Today
- Radius experiences sixth consecutive quarterly loss
- US ferrous market exhibits upward pricing pressure: Davis Index
- Glass Packaging Institute applauds regulation change
- Engcon adds to Tiltorotator line
- Paper recycling is focus of two January webinars
- Disruption likely for material flows in mid-January
- Blue Whale Materials to expand Oklahoma lithium-ion battery recycling plant
- CARI names new president and CEO