Visitors to a Harris shredder plant can see the difference. Sturdier design. Thicker plates of steel. Larger, heavier, castings. Interlocking fabrication using the most rugged bolts and fasteners on the market.
Owners of Harris shredders know that the differences go beyond appearances and into the critical operations aspects of production and output, ease of maintenance, minimization of downtime and dependability and reliability.
From the double feed roll assembly through the shredding plant and up to the technologically-advanced control booth, Harris shredders offer features that make them stand out from the rest of the market. The engineers, designers, fabricators and installers at Harris work with one goal in mind: to produce shredders that endure. Harris shredders are designed for maximum production that minimizes downtime and will provide quality scrap for years and years to come.
Total Control |
The output and production of a shredder is dependent in part on the skill and attention of the operator in the booth, and Harris does everything it can to keep that operator comfortable, informed, and in control. The custom operator’s seat provided by Harris offers comfort and intuitive joystick controls, putting the operator in the right place and in the right frame of mind. Just a mouse click away from the operator at all times is information collected and presented via the Harris HPM v.1 (Harris Production Manager) system. HMP v.1 offers real-time access to production rates, energy usage and other critical operational feedback. Summary reports can be created and e-mailed by the operator at the end of each workday so that the data can be reviewed by the people who need to see it. This Harris HPM v.1 advanced system of production management controls is available not only with new Harris shredders, but can also be offered as a retrofit product for existing shredder systems. |
"We’re confident that our design reduces delays and unexpected downtime," states Harris VP Doug Sebastian. "We do it through our advanced engineering design, heavy-duty construction, large castings and overall solid construction of the machine."
To build shredders that are up to the tough daily task of turning trucks, cars, appliances and plate steel into a shredded product, Harris starts with design features and parts specifications that ensure a rugged machine is being created.
Harris engineers and fabricators work closely together to provide a complete system design that leaves nothing to chance. A system is created for each customer that suits the specific application and the scrap stream that will be encountered.
The custom design starts with the infeed conveyor and runs through to the downstream system that will identify, extract and sort materials to meet customer requirements.
The Harris difference starts with Base Weldment and spring box-mounting technology that isolates vibrations and reduces vibration-related damage to key components.
Cast To Last |
Castings and other components of a shredder that take part in the fierce metal-on-metal contact of the shredding process—inside the mill—are destined to take a beating as they try to withstand the fury of flying metal. Toughness is required, and fortunately for buyers of Harris shredders, Harris is a company that knows toughness. "Harris has put the same heavy-duty design standards in our shredders that we have in our shears and balers," says Harris VP Doug Sebastian "These shredders will last a lot longer under pressure." Rotors, grates, liner walls and the other key wear parts are designed and cast with metallurgical qualities that give them the sturdiness they need to endure within the shredding environment. Being tough also means knowing when to choose your battles, and Harris shredders also are designed to do that. The oversized, outward-opening reject door ejects unshreddables faster than competing shredders. "Our customers really like that it ejects the unshreddable item quicker. It means they’re not beating up their door or liners," says Sebastian. Other subtle design differences that lead to longer component life include an enlarged top grate that increases material throughput, rotors with increased hardness to reduce cracks that need to be welded, and rear wall castings that are slightly offset from the path of the material. |
It continues with Harris’ exclusive heavy-duty double feed roller design, built with a sturdy steel plate yoke and equipped with hydraulic-actuated locks and a quick release connection to allow for easier maintenance. "It’s a terrific safety feature, providing a better way to maintain that part of the plant than previous designs," notes Javier Herrera. "We’re getting a lot of good response to this, even from operators of existing shredders who would like to have it installed."
The shredding mill itself is designed and manufactured with thicker steel, larger castings and fewer liner bolts—all working together to allow operators to shred at a lower cost per ton while taking less downtime for maintenance.
Harris-built rotors are available in disc or four-arm spider configurations and are made from specified, hardened alloys for longer wear life. Replaceable heavy-duty helmet caps further protect the spiders.
The Choice is Yours |
Harris knows scrap recycling operations come in different shapes and sizes, which is why its line of shredders is available in four different configurations. Harris Shredder can meet a customer’s request as well as help design a shredding system to meet the current and anticipated requirements of the customer. Whether the situation calls for an HS6090 model with a 60-inch rotor width and 90-inch infeed width, or the mammoth HS125125 with its rotor that measures more than 10 feet wide sitting inside a chamber with a 125-inch infeed width—the largest shredder on the market—Harris can deliver the necessary power and production. Harris can design everything that comes before and after the shredder as well, including a heavy-duty infeed conveyor and an automated sorting system that addresses the separation of ferrous, nonferrous and stainless steel metals. The goal of Harris Shredder is to design a system to meet the needs and budget of any scrap recycler wishing to upgrade a current shredding plant or wishing to enter the shredding sector for the first time. |
The rotor sits inside an innovative, reversible hood that has also been designed for longer component life. "The reversible hood means that after it wears on one side, you can reverse it and use it on the other side for another long stretch of shredding," says Sebastian.
Harris shredders are operated from a control booth that features a combination of the latest in operator comfort, easy-to-use controls, and an operations and output reporting system that will provide operators with the information they need to monitor the shredding process and make adjustments if necessary.
This combination of sturdy, high-strength metallurgy, innovative design, ease of maintenance, critical safety features and state-of-the-art information technology has quickly vaulted Harris shredders to the forefront of the industry, explains Sebastian.
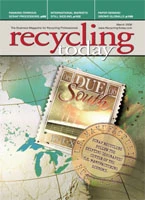
Explore the March 2006 Issue
Check out more from this issue and find your next story to read.
Latest from Recycling Today
- Radius experiences sixth consecutive quarterly loss
- US ferrous market exhibits upward pricing pressure: Davis Index
- Glass Packaging Institute applauds regulation change
- Engcon adds to Tiltorotator line
- Paper recycling is focus of two January webinars
- Disruption likely for material flows in mid-January
- Blue Whale Materials to expand Oklahoma lithium-ion battery recycling plant
- CARI names new president and CEO