
A reclaimer producing food-contact- grade recycled polyethylene
Bale quality
“Bale quality at the beginning of 2017 dropped for some unknown reason by as much as 5 percent,” the reclaimer says. “By the summer, quality seemed to recover to the norm at the end of 2016, but the 2016 numbers are far below 2014 in terms of total PET and total clear PET.”
He says paper comprises a good deal of that shortfall, adding that the material is “terrible for our washing systems.”
Ken Prevette, procurement manager, recycled bottles, for Greensboro, North Carolina-based Unifi Manufacturing Inc., makers of Repreve fabric, also addressed the issue of bale quality in mid-October during the 2017 Paper & Plastics Recycling Conference, which was organized by the Recycling Today Media Group. In September of last year, Unifi opened its Repreve Bottle Processing Center in Reidsville, North Carolina. In March of this year, the company announced that it had received a Letter of No Objection from the U.S. Food and Drug Administration (FDA), allowing its rPET flake to be used in manufacturing food-contact packaging.
According to Prevette’s presentation, backward integration into bottle processing and bottle flake production
Bale contamination is an issue the plant must contend with. Prevette said PET bottle bales the company purchases have a typical yield of from 60 to 65 percent. As yield decreases, the plant is essentially paying more for the usable PET in the bale. He gave two theoretical examples: Example A, with a yield of 60 percent, and Example B, with a 65 percent yield. Bales of PET bottles priced at 18.5 cents per pound, including freight, would have a true cost of 28 cents per pound with 35 percent yield loss and 31 cents per pound with 40 percent yield loss.
“We don’t do justice to communicating back to the MRFs (material recovery facilities) on bale quality in a meaningful way,” Prevette said.
To address this, he said the Repreve Bottle Processing Center was going to actively engage the MRFs that supply the plant, reaching out monthly to address a specific bale quality issue, providing photos illustrating good- and poor-quality bales and emphasizing the implications for shipping nonconforming bales, namely adjustments,
“I think it is inherent upon us to try to message back to folks about why it is important to produce a quality bale,” he said.
Ryan Pawlinski, supply chain manager and director of new business development for Phoenix Technologies, Bowling Green, Ohio, says his company sources roughly 80 percent of incoming bales from Ohio and surrounding states to keep its carbon footprint low. He works closely with suppliers on quality, saying relationships are key to addressing any issues in this area. If Phoenix has quality issues with a supplier, he says the company is given a corrective action plan to implement. “I will actually visit MRFs if I need to,” he says.
While not considered a contaminant, the presence of thermoforms in PET bottle bales is increasing, the reclaimer says. Thermoforms comprise almost 10 percent of PET bottle bales on average, whereas three years ago they accounted for 4 to 5 percent, he said. “We have seen loads from major cities, where consumer habits trend toward prepared foods, as high as 15 percent to 20 percent.”
However, Pawlinski says thermoforms average 2 to 5 percent in the bales Phoenix processes, adding, “Their overall effect is very small.”
The reclaimer says thermoforms yield less than bottles. “Thermoforms yield a much higher percentage of fines (30 to 50 percent), which for most operations have no value and are unrecoverable yield loss.”
He adds that flakes produced from thermoforms have a lower intrinsic viscosity (IV)—which is a measure of the polymer’s molecular weight, reflecting its melting point,
The reclaimer says his company is washing the fines produced during its process but says markets for this material are immature “and the dollar loss is still a big hole in our pockets.”
Prevette said, “Not all PET is equal by nature,” adding that reclaimers can try to increase yield by processing more export bales, which generally contain thicker-walled PET bottles, bottle-bill bales or material generated through product destruction and other postindustrial material.
Demand and pricing
Despite these quality concerns, PET bale demand remains strong, two MRF sources say, though pricing doesn’t reflect that.
Lee Cornell of First Star Recycling, Omaha, Nebraska, says PET generation is up nearly 30 percent in the company’s service area, which includes Omaha and Lincoln, Nebraska.
The company is seeing prices for mixed-color PET bales range from 10 cents per pound to 16 cents per pound, he says. “We include thermoforms in our PET bales and our buyer allows this,” he says.
Prevette said when oil prices are in the $46-to-$52-per-barrel range, not accounting for seasonal differences, PET bales range from 12 to 16 cents per pound.
Maite Quinn, the business development and marketing manager for Sims Municipal Recycling, Brooklyn, New York, says Sims also includes thermoforms in its mixed-color PET bottle bales. “We do not restrict the percentage, and to
Quinn describes demand for PET bales as “the same as usual,” adding that while the company has customers, pricing is “mediocre.”
Quinn says bale prices for the year “started out very, very low and now they are still low, but slightly higher. I assume they will go down soon.”
This expected decline is related to China’s intention to ban postconsumer plastic scrap imports, which could potentially flood the domestic market with
According to figures from U.S. Customs that Prevette shared during his presentation, the U.S. exports 450 to 500 million pounds of baled bottles to China annually. He said year-over-year exports of this material to China have increased in 2017; however, exports from June through August declined by double digits compared with the same period in 2016.
Prevette said China’s ban on imports of PET bottles from the U.S. beginning in January 2018 could improve bale bottle supply in North America and ease pricing for bales here.

However, Pawlinski believes this ban will affect the byproducts generated by PET reclaimers and not the PET bottle bales themselves.
“There is some debate as to whether there is excess reclaimer capacity in the U.S. sufficient to cover
Pricing for rPET flake and pellets also is soft. “Pricing of finished goods has been awful,” the reclaimer says. He attributes this to pressure from low virgin spot and contract prices and from
“Recent pricing has been uneconomical given price and quality of raw materials,” he says of rPET. “Pricing is better today than last month, but the economics are still unfavorable absent changes in bale pricing.”
He describes demand for rPET as “strong but extremely price sensitive,” adding, “No matter what brands may say to the contrary about their commitment to sustainability, their purchase of rPET is price driven to a far, far greater extent than by any other factor.”
Virgin production
Virgin PET prices spiked in the U.S. spot market during October, the reclaimer says, which has eased price pressure on rPET.
This spike was the result of the curtailment of U.S. production deriving from credit problems at M&G, he says, which made it difficult for the company to get purified terephthalic acid (PTA). Also contributing to the spike was anti-dumping lawsuits, which might have curtailed PET imports, particularly from Asia.
“The virgin addition, which has caused tremors in the last year, is the M&G plant in Corpus Christi (Texas),” the reclaimer says. “It is unclear whether those concerns were overblown because the new capacity may have actually been replacement capacity (albeit at a lower production cost), not
He adds, “In any event, Corpus Christi is on hold—perhaps for a year or more—while a control/credit battle plays out.”
The reclaimer says he’s seen estimates that M&G could be out of the NAFTA (North American Free Trade Agreement) market for all of 2018, removing 900 million pounds of
It appears that uncertainty and bale quality will continue to plague the rPET sector for the immediate future.
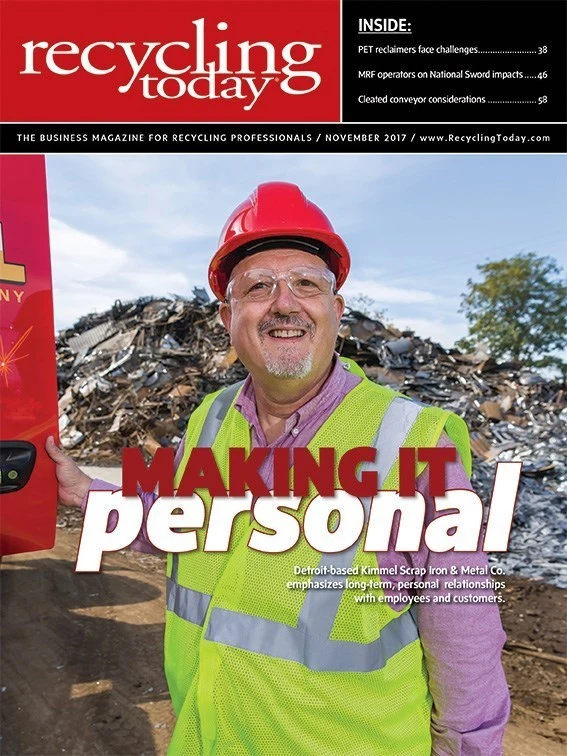
Explore the November 2017 Issue
Check out more from this issue and find your next story to read.
Latest from Recycling Today
- Eagle Dumpster Rental identifies its MRF-unfriendly items
- American Securities acquires Integrated Global Services Inc.
- Fleetio integrates Maintenance Shop Network add-in
- 3rd Eye expands suite of fleet safety solutions
- Newsom orders SB 54 revision
- Biffa sees recycling, composting opportunities at events
- Copper market navigation stress lingers
- IWS ramps up NJ MRF