Veteran scrap recyclers have seen ups and downs before, so they’re holding out through the current slump.
The numbers associated with the current steel industry and scrap market slump are grim:•More than two dozen steelmakers have filed for bankruptcy in the past few years
•Average prices for ferrous scrap have not risen above $94 dollars this year
•Steelmakers in North America continue to melt at low capacity (70.4 percent in one recent week) in the face of slack demand and a glut of competing imports.
The slump has been not just discouraging for some recyclers, but downright devastating, as some yards have shut their gates permanently.
Current economic indicators are not signaling an immediate rebound for the market, which could mean that processors who can’t squeeze a margin out of $80 per ton ferrous scrap may be joining the roster of shuttered operations.
On the other hand, those who are managing to maintain both a suitable volume flow and squeak out a profit will be poised to ride the roller coaster back up when stronger markets return.
MORE WOES FOR BIG STEEL
If the strength of the ferrous scrap market ultimately depends on the health of the steel industry, then market weakness remains part of the outlook.
Nearly all observers of the global steel industry point to overcapacity as a reality in good economic times and a tremendous burden during economic slowdowns.
Steelmakers in the U.S. believe they are particularly harmed by overcapacity because of the federal government’s open trading policies. There are still many U.S. manufacturers who are reluctant to offer tariffs or other trade protection to domestic steelmakers, even in the face of a rash of mill shutdowns and bankruptcies in the past few years.
But a stronger, louder alliance of steelmakers (both integrated steelmakers and traditionally pro-trade mini-mill operators), unions and elected officials from steelmaking states and districts seem to have finally caught the attention of lawmakers in Washington.
Two of America’s largest steelmakers and operators of integrated steelmaking complexes—LTV Corp., Cleveland, and Bethlehem Steel Corp., Bethlehem, Pa.—are in bankruptcy and continue to bleed cash.
Several smaller steel companies have shuttered their operations and/or have shifted from Chapter 11 reorganizations to Chapter 7 liquidations.
Without question, domestic consumers of ferrous scrap are struggling. “Domestic producers are hemorrhaging cash at a rate that cannot be sustained,” Charles Gedeon, an executive vice president with U.S. Steel, Pittsburgh, told attendees at October’s ISRI Ferrous Roundtable in October.
Gedeon contends that North American steelmakers have done their share to help reduce global steelmaking overcapacity, although he says excess capacity cuts will have to come “a little bit from everywhere, and that includes here.”
He also notes, though, that since 1981 60 million tons of steelmaking capacity has been eliminated in the U.S., while many overseas countries continue to support what Gedeon calls “50 years of foreign government intervention in the steel industry.”
Responses to pleas for help from steelmakers have been slow in coming from the federal government, but there is hope in the current proceedings taking place under Section 201 of the U.S. Trade Act of 1974.
Under those proceedings, a dozen of the largest volume types of steel will be protected by tariffs or other means available to the U.S. government. The Bush Administration is scheduled to announce the steps it will take by mid-February of 2002.
To what extent these steps will help domestic steelmakers—after four years of competing with a flood of low-cost imports—is the next question.
“It can’t hurt,” Bill Heenan of the Steel Recycling Institute, Pittsburgh, says of the Section 201 ruling. “It sends a message of stability,” Heenan notes.
This could be important to an industry that, according to U.S. Steel’s Gedeon, “for the first time in two decades does not have the financial means to make investments” in its operations.
The Stainless Perspective Although stainless steel competes with carbon steel on some fronts, the fortunes of the materials are often tied together by overall industrial demand. As with other metals segments, the stainless steel industry began experiencing an abrupt slowdown in the second half of 2000, and dealers of the material are awaiting the economic rebound that will reinvigorate markets. Also similar to the carbon steel industry, a strong U.S. dollar has limited the international shipping opportunities for some exporters of the material. Attendees of ISRI’s annual Nickel-Stainless Roundtable, held earlier this fall in Pittsburgh, heard nonetheless that “the U.S. lost a lot of stainless scrap to China, to India” and to other destinations, according to Friedrich Teroerde, chairman of ELG Metals Inc., McKeesport, Pa. Domestic stainless mills are not necessarily suffering to the same extent as carbon steelmakers, but the most recent quarters have not been bright. Richard Wardrop, chairman and CEO of AK Steel Corp., Middletown, Ohio, says that in its carbon steel segment the company is trying to “distance ourselves from commodity . . . carbon products” while also concentrating on its stainless production. The company operates a stainless steel research center that focuses on increasing the presence of stainless steel in autos, and also actively pursues wider markets in the appliance industry. “The stainless steel industry has a lot to do to educate [manufacturers] about the capabilities of stainless,” he remarked. In the short-term, stainless scrap traders are awaiting an economic rebound to increase demand at melting facilities and offer a return to respectable margins.
MELTING AWAY
While economic conditions and trade policy combine to affect where steel is made, ferrous scrap continues to be melted both here and abroad.
The market is far from boisterous, however, as low prices for scrap begets lighter peddler traffic and thinner margins. The wider economic slowdown, meanwhile, has trimmed the amount of industrial scrap that flows into the yards of processors.
It has been more than twelve months since the number one heavy melt grade has traded for more than $100 per ton, according to the American Metal Market composite.
The situation has made things difficult for small operators and at feeder yards that rely on the peddler trade. Some scrap recyclers worry about the long-term prospect that peddlers they have relied on for years are leaving the trade for good during this prolonged pricing slump.
While the supply of scrap might be low right now, demand has also stalled to the point where prices continue to hover in the $80 per ton range.
Electric arc furnace (EAF) mini-mills remain a growing segment of the overall steel industry, but even that circumstance cannot counteract the current glut of melting units (ferrous scrap as well as alternative iron materials used by mills). That is the finding of Sara Hornsby Anderson and her colleagues at Midrex Technologies, Charlotte, N.C., a maker of alternative iron production systems.
Whether they are called scrap alternatives or scrap substitutes, these alternative iron units are themselves one lid on the price of ferrous scrap. According to Midrex figures, alternative iron has grown as an EAF feedstock globally from less than one percent of the market in 1980 to a 21 percent share in 2000.
In a forecast presented by Hornsby Anderson at the ISRI Ferrous Roundtable held in October in Chicago, the company foresees slower gains for alternative iron in the next ten years, with market share creeping upward to 24.3 percent in 2010.
The fact that in 2000 steelmakers used 65 million tons of the materials worldwide is one factor keeping ferrous scrap demand and pricing in check.
In the U.S., abundant scrap and high natural gas prices (natural gas is used in the making of DRI) has kept the scrap melting percentage higher. But the global supply and demand situation ultimately sets prices, and even domestically alternative iron has made inroads in the past five years.
Environmentalists have decried the carving up of the rain forests of Brazil, and scrap dealers may have a reason to lament the practice as well. Much of the timber harvested there has fueled the operation of furnaces churning out low-cost pig iron, which has been exported by Brazil to compete as melting stock in nations such as the U.S.
According to Midrex, the melting of pig iron by EAF mills in the U.S. doubled from 1998—when just 2.6 million tons were melted—to 2000, when 5.5 million tons were consumed.
Pig iron, direct reduced iron (DRI) and new hot iron technologies that utilize iron ore and furnace byproducts are all now competing as melting stock with scrap. In 2000, these alternatives accounted for 18.2% of feedstock in U.S. EAF mills.
It is too early to calculate what percentage these materials will account for in 2001 or 2002, but what is certain for this year and likely for next is that they will all be competing for a smaller total domestic melting market, as several furnaces have shut down and nearly all have cut back compared to their melting schedules in 2000.
The combination of slower melting activity and vigorous competition from alternative iron sources has cooled any previous speculation that the EAF industry will be faced anytime soon with a metallics shortage.
According to Hornsby Anderson, the steel industry is still faced with 200 million to 300 million metric tons of excess capacity. Should a shakeout of some producers continue over the next year or two, this will be one more signal that metallics supply is “sufficient,” and that ferrous scrap dealers should continue to plan on per ton prices below $100.
SLOW, BUT NOT SILENT
Even in the face of tough markets, EAF mill operators are still exploiting new opportunities for their segment of the industry, and scrap companies are supplying the ferrous shred and other grades demanded by this segment.
While the majority of publicly traded steel and scrap companies report gloomy financial results, a few others are remaining profitable. Schnitzer Steel Industries Inc., Portland, Ore., managed to increase its income while recording smaller revenues for the quarter ending Aug. 31, 2001.
The company squeezed out $3 million in income from $65 million in revenues during its most recently completed quarter. In the same three months of 2000, the steelmaking and scrap trading company earned only $2.2 million from $92 million in revenues.
“Despite the continued slowdown of the world economy that contributed to our revenue decline, Schnitzer Steel was able to increase its margins and significantly improve fourth quarter results,” says company president Robert Philip.
Philip credited systematic improvements to the company’s financial system and the efforts of employees for the results. “These dedicated people focused on streamlining processes, improving the efficiency of our operations and producing and selling products that had the highest margins,” he remarks.
A strong dollar has kept the market for exported ferrous scrap in check, meaning many processors continue to concentrate on selling to domestic mills despite the woes of steelmakers in the U.S.
Thus, processors have continued to invest in upgrading their auto shredder systems and in taking other steps to provide grades demanded by U.S. mini-mills.
The trick for processors has been to remain aggressive enough to encourage a flow of incoming scrap while preventing a build-up of inventory while mills keep their orders low. “You operate as lean as you can, and you still want to provide a level of service that you’re proud of and that you require of yourself to perform,” says Manny Bodner of Bodner Metal & Iron, Houston. “You’ve always had to be price sensitive, but now it’s even more a case of watching costs versus revenues,” he adds.
There is little in the way of economic forecasts to indicate that the situation will change soon, although some hope a Section 201 relief package for steel producers could help the domestic industry feel more confident in planning a long-term future.
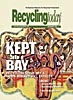
Explore the November 2001 Issue
Check out more from this issue and find your next story to read.
Latest from Recycling Today
- Magnomer joins Canada Plastics Pact
- Electra names new CFO
- WM of Pennsylvania awarded RNG vehicle funding
- Nucor receives West Virginia funding assist
- Ferrous market ends 2024 in familiar rut
- Aqua Metals secures $1.5M loan, reports operational strides
- AF&PA urges veto of NY bill
- Aluminum Association includes recycling among 2025 policy priorities