
Scrap yards are one of the toughest and most challenging environments for hand-held alloy analyzers.
Shocks, drops, vibration, rain, dust and sharp objects are all real, everyday risks. With some precautions, proper training and a bit of common sense, many incidents can be avoided, but accidents still happen.
Modern hand-held instruments are designed to be used outdoors in tough environments and to withstand heavy treatment—up to a certain point. This article looks at what it takes to convert high-precision laboratory instruments into rugged hand-held tools and the limits of today’s technology.
The Achilles’ heel
Almost anyone who’s operated hand-held X-ray fluorescence (XRF) instruments for a significant time has become painfully aware of the sensitivity of the instrument’s nose and, more specifically, the vulnerable X-ray detector. Detector punctures are costly accidents that everyone would like to avoid whenever possible.
To ensure the best possible performance and detection of even the lightest elements such as magnesium, aluminum, silicon, sulfur and phosphorous, the detector must be placed very close to the measurement window.
The window also must be manufactured from the thinnest material possible to ensure the signal reaches the detector without any attenuation. This combination makes the XRF analyzer’s nose very sensitive, and detector punctures are among the most common reasons for accidental damage to the instrument.
Throughout the past couple of years, the industry has developed ways to prevent detector punctures. Solutions are typically different kinds of shields that protect the measurement window or the detector itself. The shields provide an additional layer of security for field operation.
However, shields have a downside: When anything is put in the path between the detector and sample being measured, it can compromise the analytical performance to some extent. This is the limitation set by basic XRF physics. Typically, using a shield means slightly longer measurement times and higher detection limits for light elements.
For example, if you need to monitor phosphorous content in stainless steels or sort close aluminum grades based on magnesium and silicon content, then using a shield might not be possible and this needs to be taken into account when choosing an instrument.
Hand-held laser-induced breakdown spectroscopy (LIBS) analyzers work with a completely different technique and, therefore, aren’t sensitive to sharp items, such as turnings.
The measurement optics in LIBS analyzers are protected by sapphire glass. Some measurement windows are even recessed, meaning the glass itself won’t come into contact with the sample. The only thing users need to remember is to keep the measurement window clean to ensure the best possible performance.

Keep a firm grip
Dropping a precision instrument with a five-digit price tag is always a bad idea. Many instruments these days are marketed as being compliant with MIL-STD-810G, a U.S. military standard.
However, what does MIL-STD-810G compliance mean, and what kind of protection does it provide against accidentally dropping the instrument?
The MIL standard was created by the United States Armed Forces and includes a series of tests that simulate ruggedness in the laboratory rather than performing the tests in real field conditions. The MIL-STD-810G standard includes several subtests from drop tests to the growth of fungus on the surface of the tested instrument.
When taking a closer look at the instruments’ technical specifications, typical tests carried out for hand-held analyzers are related to drop, shock, vibration and transport. It’s also worth checking if the tests are carried out according to the specifications or if there are exceptions, such as dropping the instrument from a lower height than specified.
To pass the MIL-STD-810G drop test, the instrument must be dropped 26 times at different angles from a height of 4 feet onto a 2-inch plywood platform. Up to five different units can be used to pass this test, so a single unit does not need to withstand all 26 drops. The latest developments in the design of hand-held analyzers have made it possible to pass this test without breaking key components or the electronics inside.
It’s important to understand that passing the military standard test is usually not a warranty statement. This means the user can’t drop the instrument and expect it to be covered by the product warranty.
Instruments often are equipped with shock sensors that will reveal during servicing whether the instrument has been dropped.
Also, dropping the unit on a hard surface, such as asphalt or concrete, is a completely different story than the simulated drop on plywood.
Even though instruments today are significantly more robust than those manufactured in the past, always use the attached wrist straps or lanyards.
Don’t sweat water and dust
Water, dust, oils and cutting fluids are always present in scrap yards. Luckily, hand-held analyzers can withstand these conditions well these days. Most of the instruments are IP54 (Europe) or NEMA 3 (U.S.) classified and can tolerate splashing water and dust.
Even higher classifications for water ingress are available, but these limit the analytical performance of the instrument by taking the light elements out of the equation as thicker film needs to be used to protect the instrument’s nose.
In light rain and dusty environments, most hand-held analyzers are fine as long as they are cleaned on a regular basis and the cleanliness of the measurement window is monitored frequently. Instruments shouldn’t be used in heavy rain, and no part of the analyzer should be submerged in water.
In wet and dusty environments, the sample surface presents a bigger challenge to the accurate operation of the analyzer as water and dust particles can affect the analytical performance to some extent. Therefore, the recommended practice is to dry and clean the sample surface before taking a measurement. This is very important, especially when operating LIBS analyzers that are more sensitive to sample surface conditions than XRF analyzers.

Stronger, but not indestructible
The latest developments in the design of hand-held analyzers have made it possible to operate the instruments safely in even the harshest environments. However, the laws of physics set certain limitations that are not possible to overcome, and building an indestructible instrument is a challenge that remains.
Using the instrument carefully and according to the instructions provided is still the best way to ensure long and trouble-free operation. However, in case of unavoidable accidents, the instruments nowadays have a significantly higher chance of survival without the need to visit the service depot.
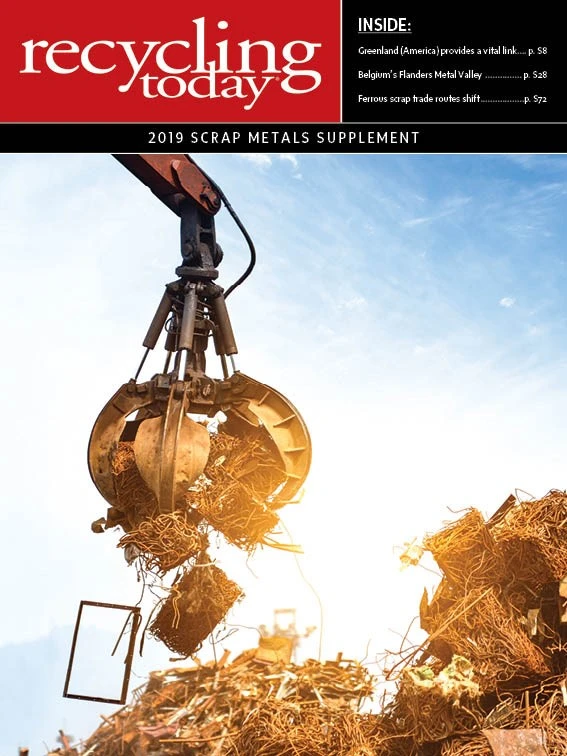
Explore the January 2019 Scrap Metals Supplement Issue
Check out more from this issue and find your next story to read.
Latest from Recycling Today
- AF&PA report shows decrease in packaging paper shipments
- GreenMantra names new CEO
- Agilyx says Styrenyx technology reduces carbon footprint in styrene production
- SABIC’s Trucircle PE used for greenhouse roofing
- Hydro to add wire rod casthouse in Norway
- Hindalco to invest in copper, aluminum business in India
- Recycled steel price crosses $500 per ton threshold
- Smithers report looks at PCR plastic’s near-term prospects