The story of International Aggregate, based in Raleigh, N.C., is a common entrepreneurial one in the aggregate recycling industry.
The company was started by a person who had been in the natural aggregate business and later worked for another company that recycled concrete and asphalt. He decided he could do it better, and mortgaged just about everything to buy his first small crushing system. Apparently he could do better, and now International Aggregate has three crushing spreads.
That person was Derwin Charles, who is president of International Aggregate, and a member of the Construction Materials Recycling Association (CMRA). Charles’ previous experience had “pretty much taught me what not to do,” he said, when he decided to go on his own in November of 1995.
PROVIDING A SERVICE
It also has helped that the Raleigh/Durham area has experienced tremendous construction growth for the past decade, and there was and is a tremendous demand for infrastructure improvements. Of course, natural aggregate has long dominated North Carolina, and it is no different today. Large aggregate plants run by big companies dot the state, and they control the aggregate market. And Charles admits that even with three plants, he doesn’t process that many tons of material in comparison to the aggregate industry.
In addition, there are few other recycling players in the state. Hence, the amount recycled “is a drop in the bucket,” he says. “With the growth rate in the state, I am sure [aggregates companies] have done nothing but watch their sales go up. They are not worried about us.”
That doesn’t mean those big aggregate companies don’t pay much attention to his activities. Some of them hire his outfit all the time to perform their recycling work, especially for recycled asphalt pavement (RAP).
“Most of our customers are asphalt plants, and a few contractors,” says Charles. “They have tried doing it themselves. But they really don’t have the tonnage per year to justify having a crusher. What these large companies with multiple asphalt plants run into is that they never get a set crew on a [crushing] plant. They move the plant from one site to the next, and the people who work on it are from that site, and are not the same crew. The equipment is not cared for because the crew knows the crusher is just going to go away in a little while, so they just run it and don’t maintain it.”
Charles does maintain his crushing spreads, which are all made by IROCK, Wooster, Ohio. The three plants are relatively similar, single-stage systems with horizontal impact crushers.
Typical is a system on one frame that starts with a 14 feet by 40 inches feeder that sends material to a horizontal impact crusher with a 30 inches by 42 inches opening. The rotor is 42 inches wide. The processed aggregate is screened by a 5 feet by 14 feet double-deck unit that usually has wire cloth screens in it. “We are usually making a 5/8-inches minus for asphalt with it, so it’s 5/8 on the bottom screen and 1 inch on the top,” Charles says. “The overs re-circulate on a conveyor back to the crusher. We can do 1,000 to 1500 tons per day with this plant.”
The entire system is powered by a Caterpillar diesel engine with 440 hp. The headboard at the end of the conveyor comes off so that the overhead magnet there doesn’t have to be in place for the plant to run. “We don¹t put it up there when running asphalt,” he notes. “And we don’t use this plant, and the other one almost exactly like it, for concrete very often. We use the big plant for that.”
The big plant is still a single-stage unit, but the screen is separate, so there are two trailers. The feeder is 54-in. wide and 14-ft long, with the crusher opening 30 in. tall and 54-in. wide. It has a feeder underneath the crusher so that rebar is not a problem. One trailer has the hopper and the crusher and the engine, the feeder underneath the crusher. The second trailer is backed underneath the first, making a “T” shape. The screen is 5 feet by 16 feet, a little more capacity. The magnet is mounted on the tongue of the screen trailer. “All we have to do its pull a couple of pins, pull a lever and it just flips right up in place. It takes about a minute to do,” says Charles.
Total set up time for the one-trailer plants is about 3 hours, he says, and tear-down is about the same. It’s six hours for the big plant each time. However, it can take longer to tear down because of the need for clean up.
International Aggregate is very conscientious of making sure no rock is on the plant before it is moved to make sure there are no busted windshields as they go down the road. It’s extra work, and Charles says only half jokingly, “I have tried and tried to get them to build a plant that cleans itself, but nobody has done that.”
Interestingly, when knocked down for travel, the bigger plant is shorter than the smaller plants: 13 feet, six inches versus 13 feet, eight inches. Charles says the extra height is not a big problem.
INFEED DILEMMAS
What has been a problem is getting the correct-sized material to feed the plant, he remarks. International Aggregate uses excavators with two-cubic-yard buckets to feed the operations “because it makes it a whole lot easier to make sure you are getting the right sized material in there. You can dig it easier with the excavator than the loader. Usually we don’t get much help from the customer as far as getting the material prepped. That excavator does real well with asphalt.”
The company does use a loader with a five-cubic-yards bucket to move finished product. For concrete, a second excavator with a hammer attachment can be brought in to handle oversize, while just dropping big pieces of asphalt breaks them up enough to feed, says Charles.
Three people run each of the two smaller plants: loader operator, excavator operator, and plant operator. Four are on the big plant, with the other person watching out for trash and rebar. A skid-steer at each plant helps with clean up. “That saves a lot of shoveling. The guys love that.”
How well do these crushing systems work? Charles, who estimates his first plant has done about 1 million tons of asphalt since he bought it, said he has no problem meeting the North Carolina specifications for RAP use in hot-mix asphalt. “We have been able to meet their gradation requirements. How much they allow depends on the plant and the mix design,” he comments. “Some are using 25% when they have an abundance of RAP. Some are only using 10%.”
Business is good, he adds, “because liquid asphalt is $200 per ton, so they want every pound we can recover.”
The concrete side is different, Charles notes. “Concrete you can dump anywhere, any hole in the ground. And somebody’s always finding a hole where to dump it.”
That’s not the only problem, Charles continues. “Recycled concrete has not been tried here in highway work. Most of the concrete is for contractors on private jobs. I have talked to the state about using recycled as a base, and they were receptive. However, there never has been enough quantity at any place to do a full highway job, and they didn’t want to jump around among materials.” There have been no complaints from the contractors using the recycled concrete as it meets the 1-1/2-inch minus requirement.
Most of International Aggregate’s work is done on a set price per ton basis, usually with no mobilization fee. That is because the company never had its own yard in which to accumulate material. But now the firm is developing a small yard for people to dump their concrete so the crusher can be brought in once in a while to process it.
As natural aggregate base from the quarry costs about $8 per ton, recycled concrete can be an economic alternative, even in a state where natural aggregate is so dominating. It is all part of the development process of aggregate processing in North Carolina, Charles says.
“In 1995, I saw the need for someone to recycle asphalt for these plants, and there was nobody doing concrete then,” Charles remarks. “We encouraged everyone to save their concrete, and it is slowly catching on. You talk one person into doing it this year, 10 people see him do it and then next year those 10 are doing it. It has really gone up in those six years, probably not as much in highly urban areas, but more all the time. And it will continue to grow.” C&D
The author is associate publisher of C&D Recycler. He can be reached via e-mail at turley@cdrecycling.org .
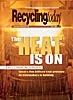
Explore the July 2001 Issue
Check out more from this issue and find your next story to read.
Latest from Recycling Today
- Nucor receives West Virginia funding assist
- Ferrous market ends 2024 in familiar rut
- Aqua Metals secures $1.5M loan, reports operational strides
- AF&PA urges veto of NY bill
- Aluminum Association includes recycling among 2025 policy priorities
- AISI applauds waterways spending bill
- Lux Research questions hydrogen’s transportation role
- Sonoco selling thermoformed, flexible packaging business to Toppan for $1.8B