The electronics recycling industry is still in its infancy, with many questions concerning best practices yet to be answered. Perhaps some of the most consuming questions have centered on how to manage the plastics used in electronics. Foremost among these questions, as with any commodity, is the intrinsic value of the plastics recovered from end-of-life (EOL) electronics.
Despite the high intrinsic value of thermoplastics related to their engineering characteristics, high-value markets for these materials have been developing slowly. In addition to the fledgling electronics-recycling infrastructure in the U.S., the cost and demands of producing clean, homogeneous grades of plastics from EOL electronics have contributed to this delay in market development.
DISASSEMBLY VS. SHREDDING. According to "Ten Facts to Know about Plastics from Consumer Electronics," a paper prepared by the American Plastics Council (APC), Arlington, Va., plastics represent 17 percent of the materials from end-of-life electronics. According to the paper, high-impact polystyrene, or HIPS, accounts for 56 percent of this plastics stream.
"That is not to say there are no variations among plastic grades or that additives are not used to give some plastics special properties, which can make recycling more complex," the paper states. "But even taking that into account, plastics recyclers contend that the number of plastics found in EOL electronics is not an insurmountable barrier to recycling."
Despite the industry’s ability to manage the diversity of grades, separating plastics from the other materials found in electronics is neither easy nor inexpensive.
"Basically, there is technology out there for material identification, but it is just too time consuming at the dismantling phase," Donald Edens of RC Plastics International, Katy, Texas, says. "Until there’s higher demand for the plastics, you’ve got to use a high-speed process to try to get any margin back."
Bobby Ferris, operations manager, eCycling Services, Recycle America Alliance, Lewisville, Texas, agrees. "The cost of sorting and processing the plastic precludes recycling on a large scale at this time." He adds, "Although there are disassembly and sorting procedures, the cost is prohibitive."
Jim Greenberg of Gold Circuit Inc., Chandler, Ariz., has been able to find two companies willing to take the plastics his company recovers from EOL electronics. While Gold Circuit does some limited disassembly, removing the housings from the monitors and computers it handles, Greenberg says further disassembly isn’t economically feasible. "What we’ve had to do, because of economics, is pull off the [largest] parts that cost us the least amount to pull off," he says.
Five years ago, MBA Polymers of Richmond, Calif., typically received the exterior "hulks," similar to those recovered by Gold Circuit. However, MBA Polymers’ Dr. Michael Biddle says that within the last year, he has noticed a shift away from disassembly toward shredding.
"We’re seeing more of what I would characterize as an automobile approach to recycling electronics," Biddle says. He adds that the material recovery approach has been popular in Europe and Japan and that the practice appears to be growing in the U.S.
Biddle says with this material recovery practice, electronics are most often shredded, with the ferrous and nonferrous metals removed using magnets and eddy current separators, as in automobile recycling. The remaining material, or electronic scrap residue (ESR), has become MBA Polymers’ most common feedstock.
"We’ve basically evolved with the recycling industry to take that stream," Biddle says. "The good news for us is that it’s more shippable because it’s already been shredded. It does tend to have more stuff in it because it has not been hand dismantled." The ESR generally contains high-grade stainless steel, circuit boards and wires in addition to plastics.
MBA Polymers has had to adapt the front end of its process to remove metals remaining in the ESR. "They are not simple metal separation techniques, because if you could have taken the metal out simply, the recyclers would have gotten it out."
GROWTH INHIBITORS. Although Biddle and Michael Fisher of the APC say few technical barriers inhibit the expanded recycling of plastics from EOL electronics, fundamental issues remain. "There are collection issues and infrastructure issues, but the technology is certainly there to apply to the recycling of a good part of the high-volume plastics used in electronics," Fisher says.
He adds, "I think the real challenge comes in trying to understand what will be the best practice for the collection and the management of the end-of-life electronics, especially from residential sources."
Buddy Graham of the Polymer Alliance Zone, Ripley, W.V., says his organization, in partnership with Electronics Industries Alliance (EIA) and through dialogue with stakeholders through such programs as NEPSI (National Electronics Product Stewardship Initiative), is trying to determine the best way to make the collection and recycling of electronics more cost efficient. Graham is confident that within the next two to three years, the plastics recovered from EOL electronics will be remanufactured into usable products, rather than used in energy recovery or incineration.
Heather Bowman of the EIA, Arlington, Va., says the NEPSI dialogue hopes to resolve some of the funding issues surrounding electronics recycling in the U.S., but that developing a federal system in an area that is currently monitored by states has proved challenging.
While NEPSI hopes to develop a system that is sustainable and environmentally sound, Bowman stresses, "No system is going to be successful without participation." Therefore, Bowman hopes the outcome of the NEPSI dialogue will be fair for all stakeholders involved.
"When you have a coalition working together – the electronics manufacturers working with the resin producers and the recyclers – then you are going to see a better system all together," Graham says. "Certainly closing the loop is the way to go."
While established markets for plastic scrap from electronics exist in Asia, the options are limited domestically, Ferris says. Because of the relatively cheap labor available in countries such as China, hand sorting of plastics remains a viable option capable of producing clean, homogenous streams of plastic. This type of manual sorting is often cost prohibitive in the U.S., resulting in the commingling of plastic grades whether during disassembly or shredding.
Edens attributes the markets limitations in the U.S. to this commingling, which restricts the plastics to non-critical applications, such as bumper stops and road patch.
In light of the identification and sorting technology available, Fisher and Biddle don’t see commingling of plastics as a hindrance.
Once the infrastructure matures, Fisher says he is optimistic high-end markets for the plastics will develop. "Even markets for recovered metals took time to develop. When you want to replace virgin materials in high-end applications, there is a lot of qualification and confidence building that has to develop," he says. "But the markets will eventually come. Hopefully, they will come at the same time the collection starts seriously."
Biddle is also optimistic about the potential for these recycled plastics to return to the electronics manufacturing process, which represents the ideal market.
The lingering issue that prevents more manufacturers from using recycled resins in electronics manufacturing concerns recycled resin supply, he adds.
"The issue for the manufacturers is that they don’t want to go through the effort of specifying and qualifying material for a large application unless they feel assured that there is going to be a supply of that material available," Biddle says. In light of the fledgling infrastructure, he says manufacturers are rightfully cautious about specifying recycled plastics until they can be assured of consistent supply.
DESIGNING WITH FORETHOUGHT. While Biddle finds the diversity of plastics used in electronics is not a hindrance to recycling, he says manufactures have tried to reduce the number of resins used in electronics under the principle of Design for Recycling or Design for Environment.
"I certainly think the manufacturers are trying to do things to help promote recycling," Biddle says. "I would say that the bigger issue is not limiting the number of plastics—though that certainly wouldn’t hurt—but not painting them, for example. Unfortunately, we’re seeing a bigger trend of manufacturers painting plastic parts, which makes our job harder because that is a contaminant we have to deal with."
Biddle adds that the global economy is also driving Design for Recycling. In Japan, Europe and a growing number of countries, electronics manufacturers are being asked to take some responsibility for their EOL equipment. "If they are going to be somewhat responsible for that, they certainly want to make things that are more easily recyclable," he says.
The standardization of resins also helps to reduce costs for electronics manufacturers by reducing the number of resins they have to have in stock and improving purchasing volumes, Bowman says.
Biddle says electronics manufactures are expressing increasing interest in closing the loop and incorporating more recycled plastic content into their products. "It’s hard to perfectly close the loop unless you’re taking back only your equipment and recycling that plastic. It doesn’t really matter at the end of the day," Biddle says. "The more important thing is that we’re getting plastics out of the waste stream and putting them back into the same type of applications. We still consider that to be closed loop, and they do too."
Edens also says manufacturers need to believe that the supply of recycled resins is assured before they begin specifying the material. "That would be the ideal situation, where they know that by working within the developing recycling infrastructure, a certain percentage of their take backs are converted to make their own new units. That would be something that any one of the electronic OEMs would be interested in," he says.
Fisher says electronics manufacturers will be interested in closing the plastics loop once they are assured that doing so is economically, as well as environmentally, beneficial. "From our perspective, what market it goes into is not as important as the fact that it’s being recycled," he adds.
As answers emerge concerning electronics recycling within the U.S., the future for plastics is looking a bit brighter. As collection programs expand, so should the availability of recycled resins, making these commodities more attractive to electronics manufacturers.
The author is assistant editor of Recycling Today and can be contacted via e-mail at dtoto@RecyclingToday.com.
Get curated news on YOUR industry.
Enter your email to receive our newsletters.
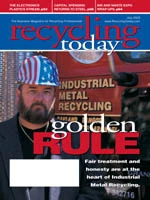
Explore the July 2003 Issue
Check out more from this issue and find your next story to read.
Latest from Recycling Today
- ReMA opposes European efforts seeking export restrictions for recyclables
- Fresh Perspective: Raj Bagaria
- Saica announces plans for second US site
- Update: Novelis produces first aluminum coil made fully from recycled end-of-life automotive scrap
- Aimplas doubles online course offerings
- Radius to be acquired by Toyota subsidiary
- Algoma EAF to start in April
- Erema sees strong demand for high-volume PET systems