
Waste Connections is an integrated solid waste services company that provides waste collection, transfer, disposal and recycling services in mostly exclusive and secondary markets in the United States and Canada. It is the third-largest waste management company in North America. In 2017, the company acquired Groot, which was founded more than a century ago and is the largest privately owned solid waste services company in Illinois.
In 2021, the Groot single-stream material recovery facility (MRF) in Plainfield, Illinois, was lost in a catastrophic fire-related incident. The former plant primarily used manual sorting, with no optical sorters.
After the fire, Waste Connections entrusted the construction of a new state-of-the-art single-stream MRF to system supplier Van Dyk Recycling Solutions, out of Norwalk, Connecticut. The new facility, completed earlier this year, can process more than 35 tons per hour (TPH) with only four manual sorters.
An advanced MRF

Pellenc ST; Jerry Evans, Groot; and Adam Lovewell,
Van Dyk Recycling
The idea was to create a brand-new plant in Plainfield at the cutting edge of technology and safety, with sorting solutions capable of addressing the most demanding quality needs.
To meet this challenge, Waste Connections chose French supplier, Pellenc ST, for the optical sorters.
In all, 11 optical sorters were installed to recover valuable materials. On the container line, six Mistral+ CONNECT machines recover PET, HDPE (mixed color and natural) and PP. On the fiber line, five Mistral+ CONNECT units recover and purify various fiber grades.
The choice to use these machines followed careful consideration of anticipated market trends. Indeed, The Mistral+ CONNECT range of machines is renowned for providing modular solutions that can be adapted to evolving incoming material streams thanks to flexible sorting recipes and customized options. For instance, machines dedicated to 2D sorting are equipped with Turbosorter and Top Speed. These two options combine to stabilize light objects on the high-speed conveyor and drive the belt up to 4.5 meters per second while maintaining a similar level of sorting performance. Fiber quality control also uses technology that can detect black plastic. In addition, this range is completely future-proof. Thanks to the Central Nervous System (CNS) software platform, operators can integrate future technologies with the Pellenc ST scanners, such as the IIoT, watermarking and artificial intelligence, through upgrades.
“Thanks to these advanced sorters, we dramatically reduced the number of manual sorters, and the plant is now running at a level of automation that we never before thought was achievable. The quality of our final products is remarkable—even more so when you consider that there is no manual QC on these commodities.”
— David Kawa Groot Plainfield Plant Manager
The fruit of a lasting partnership
“This is now our 22nd project with Pellenc ST, and we have a trusting relationship with real experience and know-how that we can put to good use in our customer performance,” says Adam Lovewell of Van Dyk. “Close relationships between our teams are key and enable us to bring projects to a successful completion. We still have many projects to carry out together at the end of the year and in 2025, and we’re already looking forward to working with the Pellenc ST teams.”

pellencst.com
Get curated news on YOUR industry.
Enter your email to receive our newsletters.
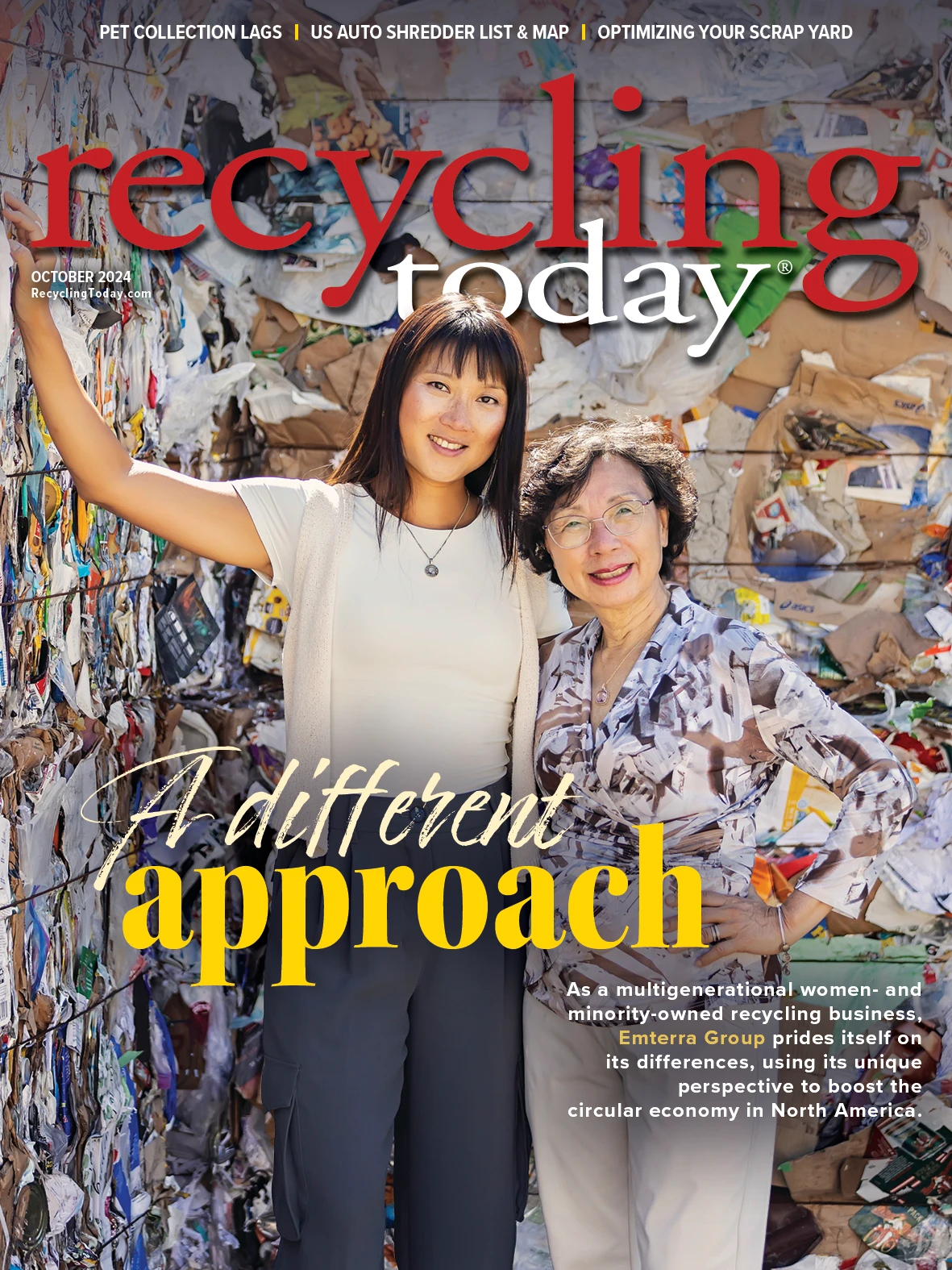
Explore the October 2024 Issue
Check out more from this issue and find your next story to read.