Operating a green (environmentally sound) business while staying in the black is the goal of most C&D recyclers. At least one green-waste recycling business started in South Florida in 2001 is already showing signs of success after just two years.
At a site located near growing population centers and equipped with high-production equipment, Nu-Way Recycling Corp. is positioning itself to capitalize on its production capacity, while at the same time diverting a sizeable stream of organic waste from landfills and into the landscaping market.
Same Industry, Different Materials
Nu-Way Recycling Corp., Hobe Sound, Fla., is owned by three waste industry veterans: Bill Brennan, John Porter and Anthony Masiello. Before they started Nu-Way Recycling, Porter and Masiello owned a successful waste processing and transfer company in South Florida, and Brennan was regional director of operations for Waste Management of New York.
Porter and Marciello sold their business to a larger company, and Brennan left Waste Management. All three were eager to re-enter the industry and found the perfect vehicle in a distressed 26-acre site that began as a FEMA (Federal Emergency Management Agency) organic debris dump following Hurricane Erin’s destructive sweep across the state in August, 1995.
The last of the site’s previous tenants was overwhelmed by trying to operate both this and another site, and the property contained a significant amount of unprocessed material when Brennan, Porter and Masiello acquired it. Although this was the new owners’ first foray into the horticultural business, their experience in waste handling told them that high productivity would be crucial in processing the old material and in making room to handle new incoming debris.
Immediate Productivity Essential
Buying the right grinding equipment was critical, so the three owners attended a trade show in Georgia for a close look at a variety of the latest products. Nu-Way Recycling Corp.’s owners soon found themselves talking to Morbark Inc., based in Winn, Mich.
Nu-Way Recycling Corp. needed a grinder immediately, but the owners were not sure what size they needed at the site. "Morbark worked with us," explains Brennan. "They said, ‘Try this one. If it’s too big or too small, we’ll try something different.’ That was a pleasant surprise."
Because clearing room to operate on the site was Nu-Way Recycling Corp.’s first priority, the company purchased Morbark’s largest horizontal grinder, the Model 7600 "Boss Hog" Wood Hog.
Brennan explains that Morbark’s regional support facility in Sarasota, Fla., was a big factor in equipment selection. "Being in business on our own for the first time, we didn’t have a high degree of sophistication or infrastructure developed," he says. "It’s nice to have Morbark on site within a few hours when needed, addressing the issues."
Good For Business, Good For The Environment
Nu-Way Recycling Corp. saw the opportunity to keep horticultural materials out of the landfill and to return them to the environment for more beneficial uses. The company quickly secured several municipal contracts to take in yard waste that was previously going into a landfill to be used for daily cover. "There’s enough material going into landfills currently," says Brennan. "The more we recycle, the more will be here for future generations."
Brennan also points out that the soils, compost and decorative mulch made from Nu-Way Recycling Corp.’s grindings have a higher commercial value than landfill cover.
Incoming materials range from branches, leaves and palmetto fronds to logs and stumps. Clean logs are separated and green material is windrowed to dry out for a short time. The logs are ground in the Morbark Model 7600 and sold as coarse feedstock to several retail suppliers with whom Nu-Way Recycling has formed strategic partnerships. These producers regrind, screen, color and bag the mulch. "Because we only grind material coarse, our product fits their regrinding processes," explains Brennan.
Foreign Objects No Problem
The diversity of incoming material was another reason that Nu-Way Recycling Corp. chose the large grinder it selected. "We wanted something that was one shot, one kill," Brennan recalls. "We didn’t want a variety of specialized equipment, but we needed a machine that would handle green waste and produce a wood product as well."
Because most of the materials come from municipalities, foreign objects frequently find their way into the waste stream. Brennan notes that its machine’s torque-limiting technology keeps it from self-destructing, as opposed to some other machines that are equipped with shear pin assemblies.
"Pins are running $150 to $200 every time you have something hard," he warns. "This costs you money." By contrast, says Brennan, his grinder disengages itself to allow for easy removal of foreign objects.
In addition to wood grindings, Nu-Way produces soils and compost from the finer materials and green wastes, which are stockpiled after grinding, then sized by a trommel screen. These products are also sold to the company’s retail partners.
A Sound Investment
With the grinder being the key element in Nu-Way Recycling Corp.’s processing circuit, Brennan says that investing in the largest model is justified by its high productivity and reliability. "If we had gone with something smaller, we’d be processing 150 to 200 yards per hour. With this machine, we’re exceeding 500 to 600 yards per hour. So that cuts our operating cost in half."
The Model 7600 is fed by a Kobelco SK200 excavator with a grapple. Incoming and processed materials are moved and stockpiled by a Caterpillar 950F wheel loader. Nu-Way Recycling recently purchased a Morbark shear to mount on the excavator. "We look forward to turning this pile of debris into a pile of cash," beams Brennan, pointing to a long stack of land-clearing debris.
The Right Place At The Right Time
As Nu-Way Recycling Corp. secures more business with municipalities and land-clearing contractors, its owners are looking at future growth. The company’s business plan is being far exceeded and Brennan, Porter and Masiello are already looking at potential expansion sites.
For now, Bill Brennan says that an additional excavator and front-end loader are needed to keep up with the volume of material that the large grinder is capable of processing. "With the ever-expanding population of South Florida, we are well-situated to participate in and support that growth," says Brennan.
This story was submitted by an agency working for Morbark Inc., Winn, Mich.
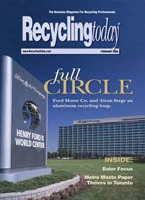
Explore the February 2003 Issue
Check out more from this issue and find your next story to read.
Latest from Recycling Today
- Nextek, Coveris to recycle food-grade plastic film
- Recyclekaro expands recycling capacity
- USTR hears comments on port fee proposal
- C&D World 2025 hits record attendance and exhibitor numbers
- Denali now offers mobile depackaging service
- Hyundai confirms Louisiana as EAF mill site
- ASCE sees infrastructure progress, but more to be done
- Global steel output tapers downward