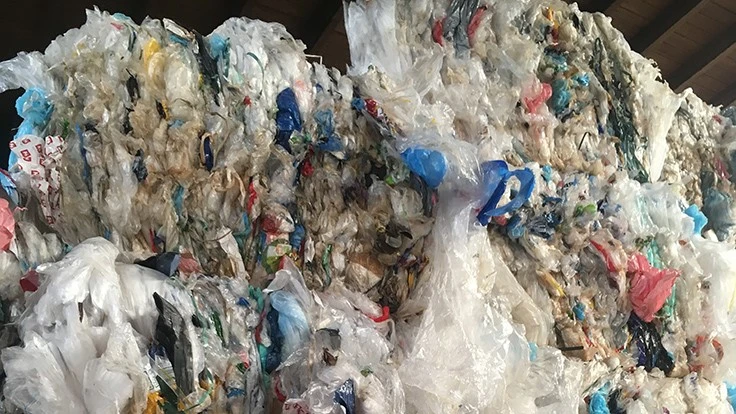
Recycling Today archives
Debate continues over what place mechanical and chemical recycling technologies have in the recycling industry.
Is one of the two technology types better than the other? Is chemical attempting to edge out long-standing mechanical technologies with nowhere near the market maturity? Or can these systems and processes coexist, each with its own beneficial capabilities?
The two processes are complementary, without hesitation, especially seeking to maximize repurposing the secondary materials we generate through the discarding of materials.
Supposing the billions in investments announced by brand owners and petrochemical companies over the last year are appropriate indicators, ground-breaking solutions to the plastic recycling challenge appear right around the corner. In truth, there is work to be done. But we are doing that work.
Chemical or molecular recycling (pyrolysis and a magnificent variety of other technologies) is poised to be a growing subsector of the plastics recycling industry in the remainder of this decade and beyond. According to Plastics Technology Magazine, 1.1 million tons per year of plastic are already being recycled this way in the European Union, and planned investments may triple that volume by 2030.
Plastic recycling is now a public matter. Brand owners and governments are committed to increasing plastic recyclability and the percentage of recycled content in plastic packaging.
The case for coexistence
Mechanical recycling is perhaps the more traditionally accepted recycling method and has been around for quite some time. Essentially, plastic scrap is sent to a waste management and recycling company along with other materials, such as metal, paper and cardboard. It is then sorted into bales of a single polymer type, for instance, polyethylene terephthalate (PET), from which beverage bottles are made. These are sorted from high-density polyethylene (HDPE), low-density polyethylene (LDPE) and polypropylene (PP).
These bales are, usually at different facilities, shredded into small flakes and washed. In most cases, the plastic is then melted down and extruded into small pellets. During this process, the polymer structure is never broken. However, it can be degraded at some level, depending on the processing conditions. And that’s where mechanical recycling differs from chemical recycling.
The recycling market is experiencing a lack of supply and ever-growing demand. Demand comes from voluntary commitments to use more recycled plastics and reduce reliance on virgin plastics, as well as from legislation to enforce the same.
To help fill this gap, companies are increasingly looking toward chemical recycling. Where mechanical processes can be challenged by material type, grade, degradation or contamination, chemical recycling processes can step in, taking the scrap back to monomers or recycled feedstocks, and keeping it out of the landfill. As time goes on, as collection rates improve, and as brands meet their 30-percent-recycled content goals, mechanical recycling could become more challenged to cope with the underlying demand and its limitation to some end-use applications, such as direct food-contact products.
Many industrial participants count on chemical recycling to solve the problem of hard-to-recycle mixed plastic scrap. Chemical recycling converts plastic scrap back into hydrocarbons, monomers such as styrene, ethylene, propylene or glycols or even back to chemical feedstocks such as naphtha. The process in scope used is called pyrolysis.
Compared with mechanical recycling, the most valuable aspect of chemical recycling is that you can convert plastics back to whatever application you want to use the plastic in, as the recycled material produced will be incorporated in the chemical and plastics production to partially replace fossil feedstocks.
Take widely used and difficult-to-recycle flexible packaging. Chemical recycling has the potential to recycle postconsumer flexible plastic packaging materials and other mixed, degraded or contaminated PE- and PP-based plastic scrap that is hard to recycle today – turning it into materials suitable for use in new food-grade plastic that meets European regulations.
Some end-use applications are where we run into some problems with mechanical recycling. The demand for these end applications doesn’t match up with the bulk of supply coming out of the mechanical recycling market. So, some end applications, or what you can use recycled plastic to make, depend entirely on the quality of the recycled material and legislation.
Because of contamination and difficulties in sorting mixed plastic scrap, much of the plastic is not high-quality enough for these applications via mechanical recycling methods. So, we get a lot of supply out of mechanical recycling that goes into fiber applications, construction pipes, industrial applications or end applications where the final look isn’t the biggest concern. This bulk of supply may need to change if the market will improve and meet targets set on recycled plastic inclusion.
The bulk of recycled plastic from mechanical recycling is still striving to be of high enough quality to go into the applications that see the most significant demands: food-contact applications or consumer packaging.
A growth solution for plastic recycling
The centers of demand for recycled plastics and the availability and quality of supply are mismatched. You only need to look at the number of voluntary commitments made across various industries to use recycled plastics, as well as the growing legislation, to get a picture of how and why demand might be changing.
The proposed solution in chemical recycling relies on its ability to produce a higher quality product because scrap is turned back into its original material, or monomers, or feedstocks and back into a naphtha-type product to be used again—and to make new packaging with recycled content equal in its chemical structure to a virgin-based polymer.
Even with chemical recycling, having a clean and uncontaminated feedstock or materials stream is crucial. However, some technologies and processes are more flexible than others in accepting a wider array of scrap input.
The challenge is building a large-scale sophisticated recycling plant that produces high-quality recycled material.
Commercial volumes are limited, but the number of press releases from big names in the petrochemical market and newcomers announcing plans to build plants suggests that significant increases in supply could be just five or 10 years away.
At United Kingdom-based Greenback Recycling Technologies, we plan to drive innovation to empower the circular economy, creating a greener future for all. The plants we are building are scalable and agile and can be quickly established in modular units set up at landfill sites or there where scrap has originated or exists. This allows for a more streamlined collection process and creates jobs around the local area, increasing economic productivity in developing nations.
It also avoids the highly inefficient transportation of scrap, providing an improved footprint and allowing us to verify that all materials collected are post-consumer scrap. We use pioneering blockchain technology to store data about the materials we process in a way that’s both open and secure, so its provenance can be verified at all levels of the supply chain. This allows scrap to be digitally tracked on its journey to becoming packaging again, so brands can easily verify the recycled content of all their packaging.
Supporting the growth of a circular economy is a challenge, but it presents a wealth of opportunities for retailers, converters and manufacturers who use plastic packaging. It encourages continual innovation, and chemical recycling proves that these innovations can result in new revenue streams and improved profitability for everyone in the plastics industry.
We’re incredibly determined to establish a decentralized network of collection and recycling plants near sources of post-consumer plastic scrap worldwide. And through smart contracts, we ensure a fair distribution of value to all actors in the supply chain, including the scrap collection sector.
This is particularly pertinent as we are beginning to see a decoupling of the recycled market from its virgin equivalent. The recycled market can now price at a premium to the virgin market.
Economics will be the leading factor in determining the success of these innovative technologies. existing extended producer responsibility (EPR) models must be redefined to integrate this new reality and promote vertical integration of the various actors. Whether through mechanical or advanced, or chemical technologies, reaching tomorrow's targets for plastics recycling might mean the era of cheap plastics is over.
With further progress in plastic manufacturing and recycling being forecast, we should recognize that mechanical recycling alone cannot meet this problem. Now could be the time to understand plastic-to-plastic chemical recycling better. We should employ a holistic approach to understanding the function it might play within the journey to an extra sustainable future for plastics.
The author is CEO and founder of United Kingdom-based Greenback Recycling Technologies. That firm’s chief revenue officer will be taking part in a panel discussion at the 2022 Paper & Plastics Recycling Conference Europe event, being held in Rotterdam in mid-November.
Latest from Recycling Today
- Lindner shredders prepare Brazilian plastic for recycling
- China ups steel output while other nations cut back
- ReElement, Posco partner to develop rare earth, magnet supply chain
- Comau to take part in EU’s Reinforce project
- Sustainable packaging: How do we get there?
- ReMA accepts Lifetime Achievement nominations
- ExxonMobil will add to chemical recycling capacity
- ESAB unveils new cutting torch models