At a Glance: SCA Tissue NA |
PRESIDENT AND CEO: Joe RaccuiaDIRECTOR OF FIBER PROCUREMENT: David Knight LOCATIONS: Based in Neenah, Wis. Mills in Barton, Ala.; Flagstaff, Ariz.; Alsip, Ill.; South Glens Falls, N.Y.; and Menasha, Wis. Additional converting plants or regional offices in Bellemont, Ariz.; Gary, Ind.; Greenwich, N.Y.; and Oakville, Ontario, Canada TONS OF SCRAP PAPER CONSUMED ANNUALLY: More than 530,000 metric tons NUMBER OF EMPLOYEES: Approximately 2,600 at plant and office locations combined |
T
he statistics have been discouraging in recent years regarding the number of paper mills operating in the U.S. In the late 1990s and so far this decade, paper companies have been slashing capacity, with more than 50 mills in North America shutting down from 2000 to 2003, according to Atlanta consulting firm Moore & Associates.To open a new mill in these circumstances might seem to be a contrarian maneuver, but the leaders of SCA Tissue North America say there are sound reasons why they opened a new $240 million recycled fiber tissue mill in Barton, Ala., in 2004.
SOUTHERN EXPOSURE. Capacity cuts in the U.S. paper industry have often been made because demand for many types of paper has stabilized.
At the same time that overall demand for paper has been relatively static, though, there have been changes within the market that caused SCA North America to reposition its mill capacity.
The demographic population center of the U.S. has been moving steadily south for the past few decades. Much of SCA’s North American mill capacity, however, was in the northern U.S.
SCA North America is headquartered near Philadelphia in Eddystone, Pa., and its SCA Tissue division is based in Neenah, Wis., the site of one of the company’s tissue mills. According to SCA Tissue Division President and CEO Joe Raccuia, though, the Southeast was becoming the company’s largest and strongest market for its tissue and packaging products.
Transportation and logistics issues dictated a production shift from the North to the South. "Our Barton facility positions the company to serve our Southeast markets," says Raccuia. "Barton is the regional manufacturing platform for a 10-state area with the fastest growing demographics in the nation," he comments.
When the Barton mill came online in 2004, Don Lewis, SCA Tissue senior vice president of sales and marketing, said, "This is good news for SCA and for our customers. We are strong in Southeast markets today, and an integrated facility will create supply chain efficiencies which will ensure the highest level of service to our customers."
SCA Tissue converted the first reels of paper at its Barton mill in April of 2004, just 17 months after announcing plans to build the tissue mill in October of 2002.
At the time, Raccuia called the feat, "A remarkable team effort. SCA has gone from ‘shovel in the ground’ to cases of Barton-produced paper products on the truck in 17 months. We are very pleased with this accomplishment."
The timetable went like this: SCA broke ground on the Barton tissue facility in late October of 2002. Tissue converting operations began in April 2003; the distribution warehouse opened in December of 2003; paper production began in late March 2004. The first case of Barton-produced paper products was sold to Dee’s Paper Supply in Mobile, Ala., in early April of 2004.
Swedish Accent |
Sweden’s Svenska Cellulosa Aktiebolaget (SCA) started building its SCA Tissue North America division in 2000 when it acquired the assets of Georgia-Pacific Tissue when GP was forced to sell them off to comply with the U.S. Department of Justice approval for the GP-Fort James merger. The company broadened its presence in North America throughout this decade through acquisition with the 2001 purchase of the former Encore Paper Co. in South Glens Falls, N.Y. The opening of the Barton, Ala., mill last year was designed to strengthen SCA’s position in the U.S. market and to help it become a producer of more than 500,000 tons of tissue products each year. SCA Tissue North America, led by Joseph Raccuia, is part of the larger SCA North America. The Tissue Division accounts for about 55 percent of SCA North America’s overall sales of some $1.5 billion. The company’s Packaging and Personal Care divisions account for the remainder. Globally, SCA has about $13 billion in product sales each year, with tissue and hygiene products, packaging and forest products being its primary industry segments. Western Europe is its largest market, with North America now the second largest. Some 53,000 SCA employees work in more than 40 nations. The company’s stock is traded on the London and Stockholm exchanges. |
The Barton mill is producing white and brown paper towels and napkins, primarily for the away-from-home market, such as restaurants, commercial office buildings, schools and hospitals. The production line features a tissue machine made by Voith-Andritz.
The company uses a variety of secondary paper grades as feedstock, according to SCA Tissue Director of Fiber Procurement David Knight, including office grades as furnish for its white towels and napkins and OCC and residential mixed paper for its brown towel products.
HUNGRY FOR FIBER. The opening of a new mill that may consume more than 100,000 tons per year of recycled fiber has meant a lot of work for Knight and the buyers who work along with him.
Knight works out of SCA Tissue’s Neenah, Wis., offices but spent a considerable amount of time in 2003 and 2004 working to secure supply lines for the Barton mill.
With the plant’s ability to accept office grades, OCC and curbside mixed paper, Knight has the ability to knock on many different types of doors. "We’re working with a pretty good variety of suppliers," he says. "Suppliers include paperstock plants and some municipalities, plus we have been working with the document destruction industry, as we see it as an evolving source of furnish."
The mill’s front-end (pre-pulping and fiber-prep) system has been designed with sufficient screening capacity to handle mixed paper and shredded grades produced by confidential shredding firms, says Knight. "Because we have a state-of-the-art cleaning system, we can handle a lot of things that other mills can’t handle," he remarks.
Award-Winning Ideas |
SCA Tissue’s mission to put napkins, tissues and towels in the hands of away-from-home end users may get a boost from an award-winning product introduced by the company. At the IFDA (International Foodservice Distributors Association) conference earlier this year, SCA Tissue showcased its Xpressnap ® dispenser system, which won the 2004 Grand Prix Award for innovative products in the paper, plastic and foil category.Xpressnap, which was introduced to the marketplace last year, is a napkin system that dispenses only one napkin at a time to users. The system is designed to increase personal hygiene because patrons only touch the napkin they take. SCA Tissue guarantees a 25 percent reduction in napkin usage, but actual reductions often are 50 percent or more. While this may mean fewer napkins are used (cutting into overall napkin sales), SCA’s strategy is to gain market share from users eager to cash in on the system’s benefits. "The judges loved Xpressnap, and so have the end users," says Andrew Conger, a field market segment manager with SCA. "In a little more than a year, Xpressnap has established itself as the most successful product launch in SCA Tissue’s history." |
This designed-in ability can offer an advantage to SCA’s buyers. Knight says that curbside programs and document destruction firms produce grades with "contaminants that are small and hidden, but that are there in fairly great number—things like plastic cover sheets that accompany the scrap paper."
Knight sees the mill’s ability to pulp grades produced by document destruction firms as particularly important. "We see the document destruction industry growing by leaps and bounds," he says. "I don’t have a precise projection of what percentage of our furnish will be shredded paper, but that percentage is going to increase in the next few years," Knight ventures.
Sourcing fiber for a new mill has provided additional work for Knight and other members of the SCA Tissue North America team, which is spread out in several locations throughout the United States (plus one office in Oakville, Ontario, Canada).
The tissue mills that SCA acquired are in Flagstaff, Ariz.; Alsip, Ill., South Glens Falls, N.Y.; and Menasha, Wis. There are also converting operations in Bellemont, Ariz.; Gary, Ind.; and Greenwich, N.Y.
The ramping up of the Barton mill has prompted SCA to increase its purchasing presence in the Southeastern United States from a combination of sources, including not only document destruction firms but also municipal programs and traditional paperstock dealers.
Sourcing in the Southeast has been a little bit different, says Knight, because a high percentage of fiber is already being harvested by mill-owned recycling subsidiaries. "The biggest difference down here is the smaller number of packing plants that are owned independently," he notes. "A lot of fiber is collected by integrated mill groups with packing plants that they manage."
The domestic competition presents just one challenge. The other comes from increasingly hungry Asian buyers. "I see challenges there. The Chinese demand is growing and changing," says Knight. "Their purchasing methods are getting much more sophisticated."
The reach of Chinese buyers into the interior of the United States is also apparent to SCA North America. Knight notes that he and his buyers "compete against export containers out of Nashville, Tenn., Columbus, Ohio—really it’s anywhere, even in the Midwest."
START TO FINISH. The papermaking machinery in place in Barton is among the newest to be found in the United States. "The automation and the speed of the machines when they are in operation is pretty amazing," says Knight.
As noted earlier, SCA made a conscious decision to deploy screening and cleaning equipment that allows it take in a wide array of fiber varieties. "There are two schools of thought on this: You can fight tooth and nail against mixed collection streams or you can, to a reasonable degree, figure out ways to handle this material," says Knight.
"We come from a European background, where the collection stream is mixed, so our tendency is to find ways to work with mixed material," he adds.
Technological advances provide part of that solution. "The mill’s ability to filter out contaminants involves a multi-step cleaning process after the pulping takes place; it’s wet cleaning, not dry sorting," Knight explains.
On the technical side, the early reviews of the Barton mill have been good. "Its cleaning abilities have exceeded our expectations. We’re able to make a very bright napkin or towel out of material that is farther down the supply chain than we initially projected," he says.
While the technical capabilities give SCA an edge, Knight says the company is not willing to fall into a pattern of being a destination for marginal suppliers. "We look for suppliers who can take a long-term partnership point of view as opposed to a short-term ‘fight over the last penny’ point of view," he notes. "Instead of fighting over the last penny, let’s cut out costs in the middle."
For the partnership analogy to work, suppliers should understand that their production practices actually mark the beginning of SCA’s manufacturing process. "One of our philosophies is to look at the packers, shredding companies, municipalities and even the generators as extensions of our production process rather than just someone from whom we’re buying paper," says Knight.
With the Barton mill now ramping up to serve the booming Southeastern U.S. market, Knight hopes his message will get through to potential suppliers through the Gulf Region stretching from South Florida and southern Texas and as far north as Tennessee.
His message: Potential suppliers are welcome to schedule a visit to Barton to learn more about working with SCA. "Let’s figure out a way to grow both of our businesses while reducing the cost of doing business," says Knight. "We’d like to hear from more paper recyclers."
The author is editor of Recycling Today and can be reached at btaylor@gie.net.
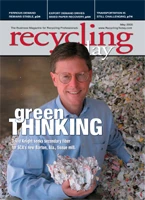
Explore the May 2005 Issue
Check out more from this issue and find your next story to read.
Latest from Recycling Today
- Nucor receives West Virginia funding assist
- Ferrous market ends 2024 in familiar rut
- Aqua Metals secures $1.5M loan, reports operational strides
- AF&PA urges veto of NY bill
- Aluminum Association includes recycling among 2025 policy priorities
- AISI applauds waterways spending bill
- Lux Research questions hydrogen’s transportation role
- Sonoco selling thermoformed, flexible packaging business to Toppan for $1.8B