
Adopting a single certification for two steelmaking paths—electric arc furnace (EAF) and blast furnace—is proving difficult.
Around 70 percent of crude steel globally is produced via blast furnaces, which emit more CO2 than EAF production, with hopes to reduce this to 60 percent or less of the estimated 2.1 billion to 2.5 billion metric tons of projected annual demand by 2050. Currently, 94 percent of emissions in the sector are produced via blast furnaces.
Considering these figures, can one certification measure green steel? Should considerations beyond greenhouse gas emissions (GHGs) be included? Are assumptions dynamic and driving change fast enough to meet 2050 guidelines?
Scrap Recycling’s series on green steel has covered two leading contenders, Responsible Steel (RS) and the Global Steel Climate Council’s Steel Climate Standard (GSCC’s SCS), as well as the fundamental road maps set out by the International Energy Agency and the Science Based Targets Initiative that are in line with the Paris Agreement to limit global warming to 1.5 C above preindustrial levels by 2050. The World Trade Organization added its perspective with the Steel Standards Principles (SSP), which both entities endorse.
Both certifications realize the importance of using recycled material to decarbonize steelmaking, but blast furnace production has affirmed its necessity in the RS model based on assumed limited availability of recycled material inputs. The forecasting models usually presume limited recycled steel availability of 1 billion to 1.2 billion metric tons annually by 2050, which could, at best, meet 50 percent of the raw material needed for crude steel production, necessitating primary production.
SCS focuses on climate change and has said that without a clear focus on emissions, the 2050 net-zero target is not possible. In contrast, RS seeks to facilitate a transition by including all stakeholders and blast furnace-heavy producers in developing countries but allows the same net-zero label to be used for higher-emissions and lower-emissions steel production through its sliding-scale design, which could limit transformation.
Both certifications can play a major role with only 26 years until net zero must be achieved.
Challenging the assumptions
Philip Bell, president of the Washington-based Steel Manufacturers Association (SMA), says recycled material forecasts in some certifications do not account for technological innovation, elasticity of supply and lower end-of-life cycles per updated data.
For example, when Russia invaded Ukraine in early 2022, pig iron tonnages from the two leading exporters were affected and prices soared. The situation initially looked dire for steelmakers dependent on pig iron, but, within months, the affected mills altered their feedstock to use more recycled steel. “U.S. mills are now consuming 50 percent less pig iron than prewar,” Bell says, adding that the elasticity of ferrous scrap allows more volumes to appear at the right price.
“Financial incentives impact both the development of scrap collection and processing infrastructure as well as obsolete scrap collected,” David D. Hodory, vice president at Cincinnati-based David J. Joseph Co., a subsidiary of Nucor Corp., said during a recent presentation to the Organization of Economic Cooperation and Development Steel Committee. Moreover, new research shows some countries have an average 18-to-20-year recycling cycle, yet some models presume up to 35 years, not fully accounting for consumption growth.
China is a recycled steel reservoir but lacks a distribution network or supply chain. It has a 28 percent obsolete scrap collection rate compared with 57 percent in the U.S. and 47 percent in the EU.

The divergence
EAFs lead the steel industry in terms of carbon footprint, with an opportunity to improve by using renewable energy.
“When looking at other technologies or roots that will lead us to a low-carbon future, we must also look at today,” Bell says. “When we look at the investment, subsidies and incentives by governments in the EU, U.K. and Canada, they include subsidies for blast furnace producers to convert to an existing, proven, low-carbon steelmaking form, which is EAF-based.”
Thus, EAF conversions and developing direct-reduced iron (DRI), which requires lower operating temperatures and much less or no coke during the iron reduction process for improved energy consumption and emissions versus using coke, should be the first steps in decarbonization. To supplement ferrous scrap, EAFs use pig iron, DRI and hot-briquetted iron, which contribute to their emissions.
“The myth of scrap availability is facilitating the longer change period,” Bell says of the EAF transition. “There is plenty of ferrous scrap to support the initial development of a broader EAF industry. For future growth, it is beneficial for governments to look at their incentives and subsidies to develop their scrap markets and supply chains into a more robust system.”
Sustainability and emerging markets
With a background in developing sustainability standards in the forestry, agriculture, marine and mining sectors, Matthew Wenban-Smith of OneWorldStandards, headquartered in London, helped design RS, noting it was developed as a sustainability standard, not a climate change standard. “The right sustainability model develops a balance between pragmatism, corporate interests and civil society in a credible format that maximizes business and ESG [environmental, social and governance] value for the greatest impact,” he says. “In contrast, SCS was designed as a climate change standard.”
Given the exclusion of social factors, some do not categorize SCS as an industry decarbonization standard or a sustainability plan. The Paris Agreement, however, includes financial, technical and capacity-building support to aid developing countries.
SteelWatch, an organization headquartered in the Netherlands with a mission to “turbo-charge” the transformation to a decarbonized steel sector, has not endorsed any standard, noting their flaws—some more severe than others. “We want to see steel become the backbone of a decarbonized economy,” says Roger Smith, the Tokyo-based Asia lead at SteelWatch. “We want a steel industry that works well for workers and the environment without cherry-picking.”
Smith recommends Step 1 should focus on material efficiency, making steel products last longer and lightweighting them, while Step 2 makes sure end-of-life steel is recycled with less contamination.
“The U.S. scrap-based steelmakers are extremely well-positioned,” Smith says. “If they just add renewable energy, they’re essentially at zero emissions today, so they are not our concern.”
According to SteelWatch’s research, regions like Asia are the main source of steel industry emissions, and the organization wants to focus on a standard to drive progress in the region.

A new opportunity
“The Carbon Border Adjustment Mechanism [CBAM] puts a price on the carbon embedded in imports, which is hugely important and sends a powerful message,” Smith says. GHGs also are a factor in the import discussion in the U.S.-EU trade agreement under negotiation.
“A few years ago, the discussions did not explicitly mention the desire to align with the 1.5-degrees benchmark,” he adds. “The era has changed. There’s a revival, and that provides a chance to do things differently and better. That’s what we really want to see.
“RS offers a framework for driving net-zero progress. Certification at the highest Level 4 gives an idea of what that means and the methodology behind it, along with verification.”
However, Bell says that RS Level 4 certification means the steel produced in a blast furnace creates seven-to-eight times more carbon than steel produced by an EAF bearing the same “‘net-zero” label.
SteelWatch favors RS given the multi-stakeholder inputs, with nonprofits and industry building it together with transparency, consideration of limited recycled steel supplies and vast documentation. “On the iron-making side, it’s more complicated, it’s more expensive, and that’s where we really want to see standards driving technology development of things like DRI,” Smith says.
Mindsets must change
SteelWatch says it wants Asian steelmakers to consider investing in noncoal-based technologies and to withdraw from those not meeting certain requirements. Asia is diverse and includes China and the biggest growth market, India, as well as major steel-producing developed economies like South Korea and Japan, which are blast furnace-heavy.
Bell says China has set a 2060 net-zero goal, while India has a 2070 goal, making the 2050 emissions goals difficult for the industry to reach if the steel industries in those countries lag.
“Japan is a good example of the chicken-and-egg conundrum where the steelmaker says, ‘We don’t have the product,’ and the buyer says, ‘Well, if you don’t have it, we cannot buy it,’ and then the discussion fizzles out,” Smith adds.
Japan is a developed country with the opportunity to change more quickly than others in the region, yet it is blast furnace-heavy. As a significant scrap exporter, Japan can increase recycled material consumption domestically.
Despite being certified as an RS company, South Korea’s POSCO could reline a furnace, Smith says, which keeps the same polluting asset for 20 more years, contrary to the goal.
Others criticize Australia-based BlueScope, also RS certified, which has invested in steel sector decarbonization in the U.S. but not in Australia, despite sufficient capital. It proposed a furnace relining as a possible bridge to lower-emissions steelmaking technologies once technically and commercially viable. According to an International Renewable Energy Agency report, 70 percent of the global blast furnace fleet will require relining by 2030.

Opportunity to accelerate
Fundamentally, the climate has changed dramatically in the last five years, so, the idea of sustainability and ESG goals being material to business is new but gaining traction in Asia as evidenced by South Korea, Japan and even China setting their own net-zero goals.
“The biggest difference between Asia and Europe or the U.S. is the pace, which is slow for the former,” Smith says. “Asian companies are not on track for 2030 nor in line with the 1.5 degrees-type scenario for 2050 and are of two minds. On the one hand, their governments are pushing them to decarbonize, providing incentives, and public pressure is building; but, on the other hand, their business models have been built around high-quality steel using coal-based methods.
“There’s a real fear about the shift and what the future looks like for facilities and workers,” he continues. “Companies are inconsistent between their public commitments and statements and their actual business practices. That needs to change. There [are] big goals, but I haven’t seen any companies with clear road maps for achieving them. This decade is going to be a time to take action.”
Government research and development investments should focus on using lower-grade DRI and lower-grade scrap with better results alongside expanded collaborations with public and private partnerships. Per Andersson, head of secretariate for the Stockholm-based Leadership Group on Industry Transition (LeadIT) launched by the governments of Sweden and India at the UN Climate Action Summit in September 2019 and supported by the World Economic Forum, says the group wishes to collaborate on and support recycling and circular solutions as they are central to achieving the net-zero carbon goals.
The certifications could impact several factors, including investor interest, buyer decisions, environmental regulations and trade. For example, the Sustainable STEEL Principles is a set of commitments to adopt a common measurement and disclosure framework designed for banks to support the steel industry in forging a pathway to net-zero carbon emissions, while the Clean Competition Act has been introduced to U.S. Congress, which could add carbon border fees on some imported products, including steel.
All steelmakers need to decarbonize. “If steel from scrap is favored globally, but if those unable to make steel from scrap receive barriers and tariffs, then it’s about protectionism, not decarbonization,” Wenban-Smith says. Steel trade is about 25 percent of global steel production, and barriers to trade should be minimized, the SSP says.
Long term, SCS and RS certifications could work together to sharpen the different approaches each follows. The former’s pace and focus can support the latter’s larger goal of helping move communities toward decarbonizing steel effectively as ferrous scrap and DRI consumption are optimized for blast furnaces and EAFs.
Get curated news on YOUR industry.
Enter your email to receive our newsletters.
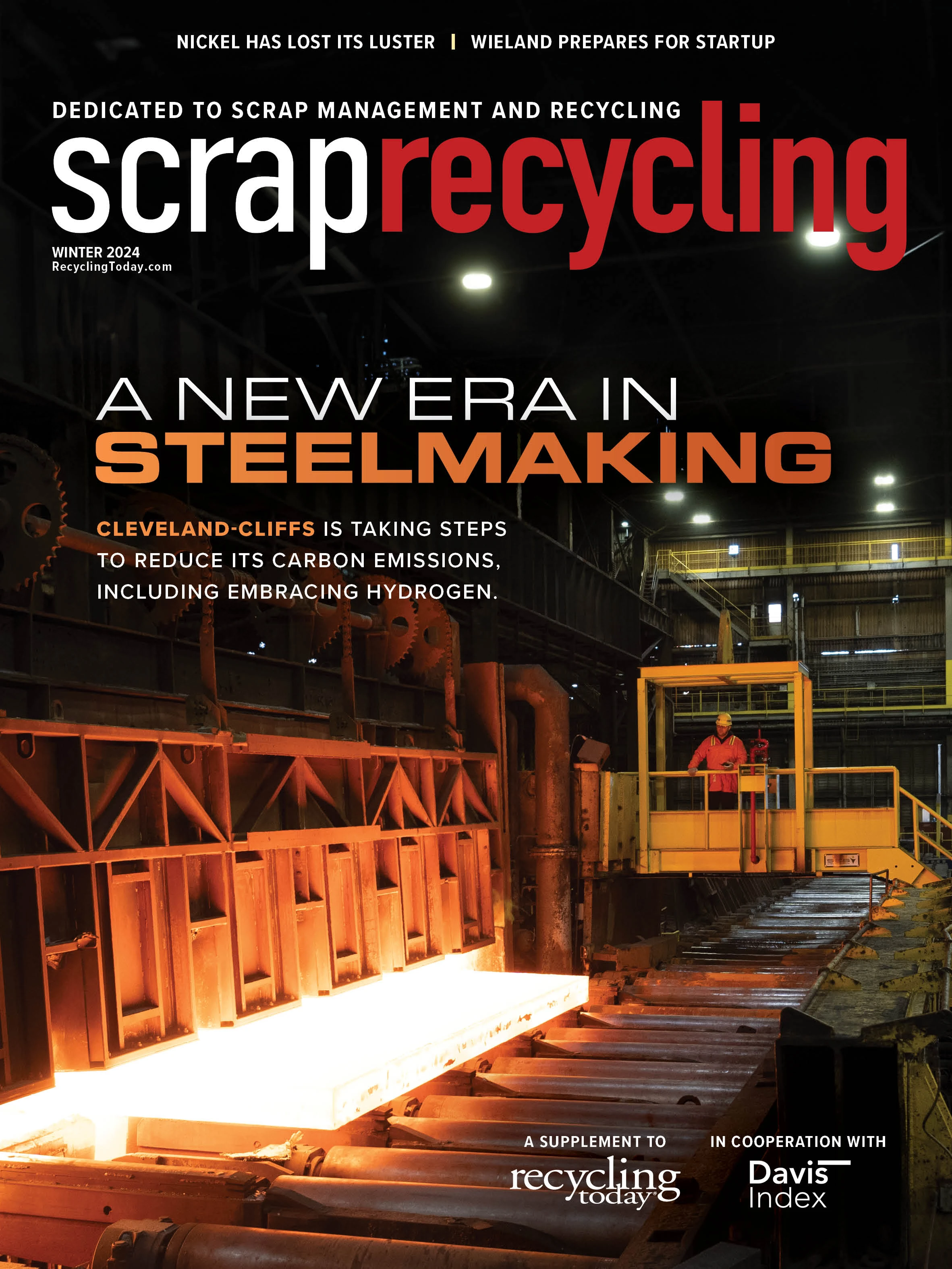
Explore the Winter 2024 Scrap Recycling Issue
Check out more from this issue and find your next story to read.
Latest from Recycling Today
- Nextek, Coveris to recycle food-grade plastic film
- Recyclekaro expands recycling capacity
- USTR hears comments on port fee proposal
- C&D World 2025 hits record attendance and exhibitor numbers
- Denali now offers mobile depackaging service
- Hyundai confirms Louisiana as EAF mill site
- ASCE sees infrastructure progress, but more to be done
- Global steel output tapers downward