
For Green Metals Inc. (GMI), with headquarters in Georgetown, Kentucky, safety is a driving force behind the company’s operations.
“Safety is the No. 1 criteria in all decision-making at GMI,” says company President and Chief Operating Officer Steve Cecil. “We are open to any source that may enhance the safety/well-being of our associates and suppliers.”
This focus on safety led GMI to join the Circle of Safety Excellence (COSE), a program developed by the Institute of Scrap Recycling Industries (ISRI), Washington.
ISRI introduced the COSE program in 2014. COSE is designed to help improve worker safety in the recycling industry over time by establishing “a platform—called the Circle—within which like-minded companies voluntarily come forward to share safety data and best practices for the betterment of their own safety operations and at the same time be recognized by ISRI for their commitment to safety,” ISRI notes on its website.
The association says it formed COSE “to help demonstrate the recycling industry’s commitment to the safety of all of our employees and the communities we serve.”
All members welcome
Participation in COSE is open to ISRI member companies in the U.S. and Canada that are committed to safe operations. ISRI says this means “having a safety management program—with certain key elements as defined by OSHA (Occupational Safety and Health Administration)—in place at all their facilities” as well as a willingness to share injury data annually and participate in a group benchmarking program.
The association offers an annual application process through which companies agree in writing to submit lost-time injury (LTI) frequency rate; days away, restricted work activity and/or job transfer (DART); total case injury rate (TCIR); and Compliance, Safety, Accountability (CSA) data for those companies that operate fleets by the published due date. This year’s application period, which extends to new and returning applicants, began Feb. 15 and ends March 15, ISRI says.
COSE members also agree to attend at least one COSE meeting per year and must be willing to work with ISRI to reach out to other companies in the industry to promote safe practices.
ISRI says benefits to COSE members include the ability to benchmark their progress against one another and network to share safety best practices. They also are permitted to use the COSE logo on company letterhead, websites
The association says its long-term goal is for all its member companies to be COSE members. Therefore, ISRI says it “is committing to providing the resources to assist any interested company in attaining membership through ISRI’s Safety Outreach program.”
“GMI constantly examines opportunities to improve safety. As an example, we receive over 100 suggestions per month from our 13 divisions on possible safety improvements.” – Steve Cecil, Green Metals Inc.
Getting started
More than 85 companies participated in COSE in 2017. Among them was GMI, which operates 13 locations in the U.S. and Canada. The company’s metals division handles busheling, steel, cast, cast iron borings, machine shop turnings, No. 1 and No. 2 heavy melt, No. 2 steel, aluminum, aluminum turnings, copper, brass, 400 stainless, 300 stainless and production maintenance. GMI’s nonmetals division handles cardboard and paper, various plastics, rubber, glass, wood, nonhazardous waste, paint, paint solvents, universal waste
GMI has participated in COSE since July 2015, Cecil says.
“The ISRI training aids that were represented to Circle of Safety Excellence participants were of great interest to our safety team and GMI management,” he adds.
Cecil describes the criteria for applying to the program as “relatively simple.” He says, “An interested participant has to be an ISRI member, complete an application, provide the required safety historical information for benchmarking purposes and be a consistent participant if accepted into the program.”
Continual improvement
COSE’s focus on continual improvement is of particular interest to GMI. “GMI constantly examines opportunities to improve safety,” Cecil says. “As an example, we receive over 100 suggestions per month from our 13 divisions on possible safety improvements. We also participate in safety-related activities via our parent companies, Toyota Tsusho America Inc. and Toyota Tsusho Corp. (Japan). Last year, GMI achieved a 50 percent reduction in lost-time injuries.”
He adds, “While we did engage two ISRI related safety audits of our operations, we could do more evaluation of opportunities within the scrap industry itself.”
Through its COSE membership, GMI has received several ISRI Blueprint Safety audits of its facilities, Cecil says. Its facilities in Texas and Alabama were audited through this program in 2017.
ISRI says its Blueprint Safety audit involves a scoring system that provides facility management with a definite metric for each safety element. The blueprint and the element scores can be left with each facility, so members can do a self-review annually to track their safety program improvements.
Cecil says most of the accidents that occur at GMI are related to ergonomics. “Thus, we see sprains and strains too frequently,” he says.
“The safety audits conducted by ISRI have allowed dialogue on possible options to minimize such accidents even more,” Cecil continues. “We then challenge ourselves to examine possibilities of weight reduction in equipment,
Benchmarking its operations
One of the benefits of membership in COSE is the ability for members to benchmark their safety operations against those of other members. For GMI, the comparisons have been favorable, Cecil says.
“What we have learned is our safety program, which is geared especially toward team member involvement, exceeds industry standards,” Cecil says of GMI’s experience in COSE. “GMI has a policy of reporting 100 percent of accidents/incidents, which I am not sure all firms do in our industry. While at times this seems excessive, if
“However,” he continues, “until we experience zero accidents/incidents, then we have room for improvement and must look for opportunities.”
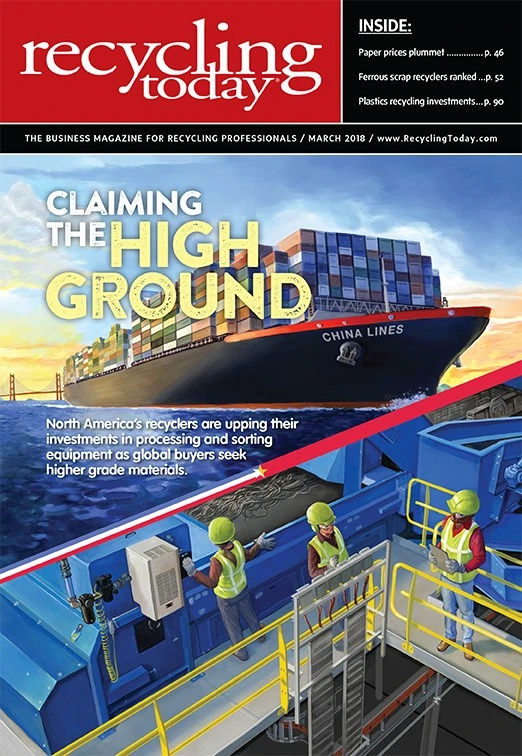
Explore the March 2018 Issue
Check out more from this issue and find your next story to read.
Latest from Recycling Today
- Tomra applies GAINnext AI technology to upgrade wrought aluminum scrap
- Redwood Materials partners with Isuzu Commercial Truck
- The push for more supply
- ReMA PSI Chapter adds 7 members
- Joe Ursuy elected to NWRA Hall of Fame
- RRS adds to ownership team
- S3 Recycling Solutions acquires Electronics Recycling Solutions
- Nextek, Coveris to recycle food-grade plastic film