Ware Disposal is an established, independent hauling company based in Southern California’s Orange County. The 35-year-old company has seen many changes in the hauling industry, especially the rise of recycling requirements in the state. Currently, under Assembly Bill 939, municipalities must recycle at least 50 percent of all the waste they generate. Most struggle to get there. Their municipal solid waste (MSW) recycling rates may be topped out, but it isn’t enough. Many are looking at C&D recycling as the way to reach the 50 percent requirement. And many municipalities are looking to their haulers for help doing that.
|
"It is difficult to be in the hauling business now in California and not have some sort of a recycling facility," says Judy Ware, president of Ware Disposal. "With all the new regulations and state laws, you need a recycling facility in order to stay in business."
Ware Disposal’s answer to that situation is the recently opened Madison Materials, a subsidiary recycling plant in Santa Ana, Calif., that can sort more than 500 tons of C&D materials per day. Despite only being in operation for a few months, the plant has a diversion rate of about 80 percent.
AN ADVANTAGE
Besides giving Ware Disposal an advantage, Madison Materials (a member of the Construction Materials Recycling Association [CMRA]) provides the cities it serves with an advantage as well.
For example, in Santa Ana Ware Disposal is one of two haulers of C&D debris (Waste Management is the other). "We are required to send 100 percent of what we pull to a C&D recycling center," says Jay Ware, general manager, Madison Materials. "We were taking it to other facilities outside the city. But now we just take it our plant. This gives the city an 80 percent diversion rate, important to meeting AB939. Now the city wants WM to bring their material here." Judy Ware adds that favorable contractual terms to local municipalities may also be available in the future.
This nice deal is what Ware Disposal/Madison Materials is now able to offer to other cities. Orange County itself is having trouble making its 50 percent diversion requirement, the same situation facing many towns in the county. "A lot of cities are just barely making their 50 percent, and they are taking all their MSW to a MRF (material recovery facility)."
Residential curbside recycling alone may only be able to recycle 35 percent of MSW, he adds, "and if we can show an 80 percent diversion rate, perhaps cities will realize that MRFs are not the only way to go. Maybe then we would get more C&D facilities taking in and recycling the tonnage in order to meet state-mandated recycling goals. I think MRFs are great, and we would like to have one so that we can go after residential contracts, but they simply don’t get the recycling tonnage needed."
According to Jason Bryce Rush, Ware Disposal’s legislative director, many municipalities must be feeling the pinch of the AB939 requirements. A simple flyer mailed out by Madison Materials got a positive response from more than 10 C&D haulers in Southern California. "Some cities are more stringently enforcing the franchise agreements that require haulers to recycle. So people are looking to find facilities that really recycle in order to get to the diversion requirements," he says.
ON THE JOB
Ware Disposal encourages its customers to source separate at the job site, and offers its customers financial incentives to do so. But in the real world at the crowded job site, one box may be all the contractors have room for on the site. This commingled material is taken to the company’s new C&D recycling plant, allowing the contractor to still get an 80 percent recycling rate.
Madison Materials sorts C&D on a 3-acre site in a heavily industrialized area of Santa Ana. The site had been vacant for more than a decade and was nothing but dirt and vegetation before Ware came along. Jay Ware says at first the company considered just doing a simple dump-and-pick application. "But when you think about it, having 30 or 40 guys standing on the ground and a couple of excavators to move stuff, how fast is that application?" Madison Materials wanted to move more tons and decided to use a more mechanized sorting system.
The entire site is paved with concrete. The headquarters building for Ware and Madison are here, as well as a five-bay truck repair shop for the hauling end of the business.
C&D debris is brought in, weighed and dumped on the concrete. The recycling system, designed and installed by Ptarmigan Machinery, San Antonio, Texas, and Olympic Wire & Equipment, Newport Beach, Calif., begins with a John Deere excavator with grapple sorting out the unwanted material, such as carpet. "But we have a market for the padding; they make an animal bedding from it," Jay Ware points out. "Carpet is heavy, anything we can get out really helps the diversion rate. We ground sort it because the line doesn’t provide us the ability to handle it effectively."
Pallets that can be reused are another object pulled immediately. In one month alone, the company was able to reclaim 40 tons of pallets.
The remaining material is fed onto a steel-belted conveyor from Ptarmigan. It proceeds to a vibrating finger screen made by General Kinematics, Barrington, Ill., that removes 4-inch minus unders. The small stuff drops onto a conveyor, passes a crossbelt magnet made by Dings Co., Milwaukee, and anything left goes into a General Kinematics de-stoner that air knifes the dirt from the rock. "We end up with the material in the air box being a mulch-type of material," says Jay Ware. "We can either mix that in with our green waste or send it back through the system by itself and sell it for clean dirt."
The 4-inches and larger material is sent up to a picking line with 14 sorters stationed along the sides. The first material pulled is wood. "We have a good market for that," says Jay Ware. "We can sell it to grinding companies that process it to a 4-inch minus for the fuel market."
The second station is for OCC. "We want all that out so you can see the rest of what is on the sort line," says Ware. Madison Materials does not even bale this material, as a company just down the street takes it in loose, as is.
Wood and green waste are pulled at the third station, with concrete removed at the fourth.
There is a good and improving market for the paper that is pulled at the fifth station, according to Ware. At first, the sorters were just getting all the paper they could and putting it in one container. "We talked with our paper recycler where we were sending all our paper, and he said to get out all the newspaper and we would get a better price," Ware said. "That allowed us to upgrade our paper market.
The same idea applied at the sixth station, where metals are pulled. Five different metal classes are now sorted, leading to higher profits.
Plastics were a challenge for Madison Materials. "We get a lot of stretch film, as everything at the construction site is wrapped," says Ware. "It doesn’t bother the line any; we don’t have to pick it out before it enters the line." Fortunately, the company currently has a market for the plastic.
AN EVEN KEEL
As all C&D recyclers with picking lines know, it is important to get an even flow of material on the picking line to make it easier for the pickers to pull the material. Ware says, "It all comes down to running the equipment at the proper speed. We are able to run the system at maximum speed because our pickers don’t have to pick through dirt; all the fines go off right away."
|
Because of its location in Santa Ana, which hosts probably the largest selection of recyclers in Orange County, Madison Materials does not do a great deal of grinding, shredding, baling or other processing of what it sorts into end products. The separated raw products are sent to established crushing, grinding and paper baling firms for them to develop the finished products, for a couple of reasons.
First, space is limited at the site and there isn’t a lot of room for crushers and grinders. Second, "We want to stay focused on the recycling and sorting, and just truck it back out," says Ware. "If we lose focus and start trying to figure out how to make and sell road base or hog fuel, then we are focused on the wrong area for us. We don’t want to worry about marketing the materials."
There are many good companies with already established markets, the company decided, and Madison Materials would be hard-pressed to compete with them. One example is CMRA member Ewles Materials in Irvine, which takes in Madison’s concrete and makes road base. Ewles has been crushing concrete for more than a decade.
The new recycling efforts have not hurt the efficiency of the company’s 50-truck hauling sector. After full roll-offs come in and are unloaded, the trucks can proceed over to accept separated material that has gone through the Madison Materials system for transfer to the crushing, grinding and baling facilities the company does business with. Loaded up, the trucks drop off the roll-offs on the way to the processor and empty them there.
All the pickers are employees of Madison, rather than from a temp agency. "We know sorting can be monotonous, so we set up goals for them to keep them motivated," says Ware. "We let them know how much material they have done, what we are doing with the material. It helps give them an incentive to do more and better."
Ware Disposal and Madison Materials are motivated to do better, if only for tip fee avoidance. The company owns no landfill, and admits it is fortunate that the county owns the local landfill and keeps tipping fees reasonable, at around $27 per ton. Even at that level Madison Materials makes economic sense, says Ware, because it helps Ware Disposal meet recycling requirements in hauling contracts and saves on trucking costs to the landfill.
And who knows who will own or manage the landfill in the future and what the tipping fee will be? At least the company is positioned well for any eventuality.
The author is associate publisher of C&D Recycler and executive director of the CMRA. He can be contacted via e-mail at turley@cdrecycling.org.
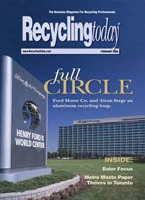
Explore the February 2003 Issue
Check out more from this issue and find your next story to read.
Latest from Recycling Today
- Joe Ursuy elected to NWRA Hall of Fame
- RRS adds to ownership team
- S3 Recycling Solutions acquires Electronics Recycling Solutions
- Nextek, Coveris to recycle food-grade plastic film
- Recyclekaro expands recycling capacity
- USTR hears comments on port fee proposal
- C&D World 2025 hits record attendance and exhibitor numbers
- Denali now offers mobile depackaging service