
When shredding automobiles, appliances, electronics and other obsolete materials, the size reduction process only starts the effort. Profits are gained and lost depending on how well the resulting shredded material is separated in the next stages of its journey.
Initial installations of an innovative product have demonstrated it to be an increasingly important component of an effective and affordable downstream system: the FINGER-SCREEN manufactured by General Kinematics (GK), Crystal Lake, Illinois.
Alan Grove, director of resource recovery at GK, says sorting plant operators have numerous choices when selecting screens to put toward the front end of their automated systems. The FINGER-SCREEN emerges as a winner, Grove says, for the reasons of performance and cost-effectiveness.
The GK FINGER-SCREEN in scrap applications helps separate inert fines, such as dirt, stones and glass, which can end up contaminating the smaller metal fractions. “Screening fines out by size is an efficient way to increase the value of the scrap product by increasing purity,” Grove says.
“Compared with other common sizing machines like trommels or star screens, the major benefit of a GK FINGER-SCREEN is the low cost to run the machine," Groves continues, citing GK's Two-Mass design as the key to the energy efficiency of its FINGER-SCREEN. "First, our machines typically require less horsepower to run than an equivalently sized trommel or star screen.
“Another benefit our FINGER-SCREEN has over other common sizing machines is lower maintenance cost. This, as well as our heavy-duty design ethos, translates to a greatly reduced cost of preventive maintenance and very low instances of shutdown-causing events.”
These benefits of the FINGER-SCREEN are no accident. “The entire genesis of the GK FINGER-SCREEN in a scrap application was born out of the need to find a replacement for a trommel that was costing an extraordinarily large amount of money in maintenance and downtime,” Grove says.
Joining sturdiness, ease of maintenance and low operating costs on the list of FINGER-SCREEN advantages are product design features that boost its performance.
“One specific benefit of our FINGER-SCREEN in a scrap metal process is its ability to effectively prevent long ‘pokers’ from passing through the screen,” Grove says. Pokers (long, sometimes sharp pieces of metal) can cause major damage to conveyor belts and other downstream equipment. “The design of our screening deck keeps pokers aligned with material flow, and the vibratory motion keeps them flat, both of which keep pokers on top of the screening deck with the overs.”
Grove and GK invite shredder downstream plant owners to investigate the FINGER-SCREEN’s results. “The first screen in a scrap application has now been running for over two years nonstop, and it hasn’t required anything but regular cleaning,” he says. “On top of that, the screening performance is better than the trommel it replaced because it both sizes the material and removes pokers.”
Grove concludes with confidence, “I don’t think there’s really anything more I can say about the machine itself. It just works.”

More information about the GK FINGER-SCREEN and other products for separation systems operators can be found here.
Get curated news on YOUR industry.
Enter your email to receive our newsletters.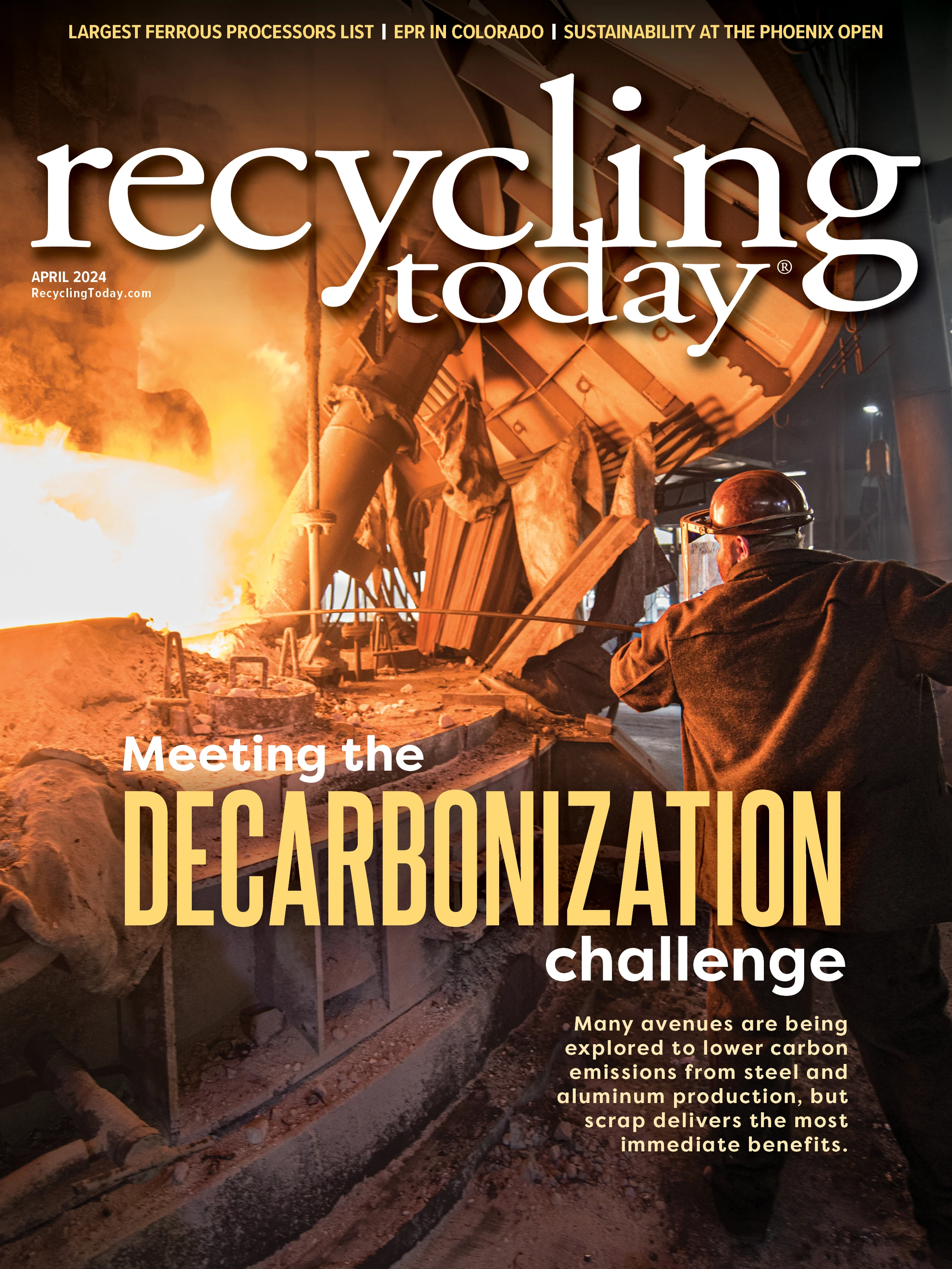
Explore the April 2024 Issue
Check out more from this issue and find your next story to read.
Latest from Recycling Today
- Athens Services terminates contract with San Marino, California
- Partners develop specialty response vehicles for LIB fires
- Sonoco cites OCC shortage for price hike in Europe
- British Steel mill’s future up in the air
- Tomra applies GAINnext AI technology to upgrade wrought aluminum scrap
- Redwood Materials partners with Isuzu Commercial Truck
- The push for more supply
- ReMA PSI Chapter adds 7 members