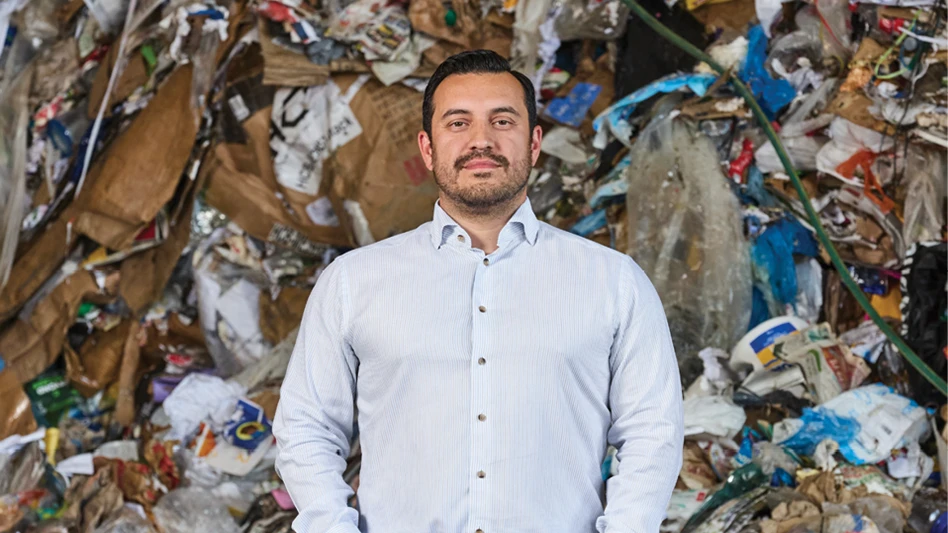
Photo by Joanna Wojewoda

GFL Environmental was founded in 2007 but made its first major entry into the United States market five years ago with a move that quickly made the Vaughan, Ontario-based company one of the largest diversified environmental services providers in North America.
In 2018, GFL merged with Raleigh, North Carolina-based Waste Industries in a deal worth $2.83 billion, and the company now operates in all 10 Canadian provinces and in more than half the United States.
It’s kept busy since then, too.
GFL officially went public in March 2020. At that time, CEO Patrick Dovigi said the plan was for the company to double in size over the course of five or six years, but thanks to organic growth paired with strong merger and acquisition (M&A) activity, GFL had doubled in size by the end of last year, just two-and-a-half years since its first public offering.
Since starting operations 16 years ago, the company has completed more than 200 acquisitions. After ramping up M&A the last two years, it has emerged among the heavy hitters in the North American waste and recycling space.
“Our disciplined ability to identify, execute and integrate value-enhancing acquisitions has been a key driver of our growth to date,” Dovigi says. “We have continued to make investments in sophisticated sorting technologies and have expanded our sorting capacity to meet the increasing customer demands in the marketplace.”
Rapid evolution
Dovigi says GFL has grown to be the fourth-largest diversified environmental services provider in North America since its merger with Waste Industries and has implemented a growth strategy that includes five key priorities: driving organic revenue growth, leveraging its asset base to drive margin expansion, reducing the cost of debt, executing on its M&A strategy and maximizing value from its sustainability initiatives.
Last year was a particularly strong M&A year for GFL as the company completed approximately 40 acquisitions, nearly all of which were smaller, tuck-in acquisitions, it says have meaningfully densified its solid waste footprint within the markets it serves.
GFL reports $480 million in annualized revenue generated from its 2022 M&A activity.
“We focus on selectively acquiring premier independent regional operators to create platforms in new markets,” Dovigi says. “We then seek to build scale by making and effectively integrating [those] tuck-in acquisitions … by increasing route density and [driving] margin expansion by leveraging our scalable infrastructure and centralized administrative capabilities.”
In addition to its acquisition strategy, GFL has streamlined its operations as part of a portfolio rationalization plan.

In June, it announced it would divest its solid waste operations in Colorado and New Mexico as well as in Nashville, Tennessee, in two separate transactions. Phoenix-based Republic Services acquired GFL’s operations in Colorado and New Mexico, including its recycling, collection and disposal assets in four Colorado markets—Denver, Colorado Sprints, Durango and Cañon City—and in the Bloomfield, New Mexico, market.
By July, GFL also had divested its solid waste operations, including nine hauling operations, one transfer station and one material recovery facility (MRF) in Pennsylvania, Maryland and Delaware, to Rutland, Vermont-based Casella Waste Systems in a deal worth $525 million.
“We believe our network of assets and market selection position us for high-quality, organic profitability growth, and we remain focused on our M&A strategy of densifying our existing footprint across Canada and the United States through our robust acquisition pipeline,” Dovigi says in the June news release announcing the planned divestitures.
GFL has restructured and streamlined in the last several years, too, in line with its strategy of maximizing value.
In April 2022, GFL divested its Infrastructure Services division and merged its Soil Remediation division with its Liquid Waste segment, renaming the division Environmental Services.
The company significantly has expanded its reach, going from 98 collection operations in 2018 to more than 230 collection operations to date, as well as adding more than 100 transfer stations, several MRFs and increasing its number of employees by about 46 percent as of Dec. 31, 2022.
“Several strategic recycling acquisitions and investing in our workforce have enabled us to grow into a leader in recycling in North America,” Dovigi says.
“We have a long-standing commitment to investing and developing the increasingly innovative and advanced environmentally responsible solutions our customers are looking for. ... We believe we are well-positioned to respond to changing customer needs and regulatory demands to maintain our success, [including] being able to respond to applicable regulations and customer demands for more sustainable solutions [like] resource recovery through recycling.”

Investing in recycling
As noted in its “2021 Sustainability Report,” GFL recovered more than 1.2 million metric tons of recyclables in 2021 at its more than 30 North American MRFs. One of the company’s primary goals in its comprehensive sustainability plan is to increase GFL MRFs’ recovery of recyclables by 40 percent by 2030.
Vice President of Recycling Stephen Miranda says the pathway to meeting this goal is through increasing the volume of recyclables received at GFL facilities while continuing to make investments in sophisticated sorting technologies and expanding its sorting capacity at existing and yet-to-be-constructed facilities.
Currently, more than 15 artificial intelligence vision systems and 59 optical sorting units are deployed in GFL MRFs, which Miranda says have allowed it to deliver higher recovery rates for materials like fiber, glass, metal and plastics.
“We are continually reviewing our existing recycling technology and assessing and implementing new technology to improve our sorting capabilities,” he says. “We have invested in state-of-the-art technology … including auger screens, elliptical fiber separation, optical sorting, fully automated high-speed sorting robots and other mechanical separation processes that allow us to … produce high-quality processed recyclables.”
The investment in the latest technology has earned GFL industrywide recognition. In 2020, its Winnipeg, Manitoba, MRF earned Recycling Facility of the Year from the Arlington, Virginia-based National Waste & Recycling Association, an award recognizing MRFs for innovation, partnership, public education and environmental impact. Last year, GFL’s multimaterial recycling campus in Toronto earned that same honor.
GFL worked with Machinex, Plessisville, Quebec, on the design and implementation of the sorting systems at the Winnipeg and Toronto sites and also partnered with Norwalk, Connecticut-based Van Dyk Recycling Solutions. The Winnipeg MRF is 80,000 square feet and features seven optical sorters and a Machinex SamurAI robotic sorter.

The multimaterial recycling campus in Toronto is even more elaborate. The site houses two MRFs that include 22 optical sorters, eight balers and three fully automated sorting robots. Currently, the campus provides recycling services to more than 4 million residents in the Greater Toronto area as well as commercial and industrial recycling services.
GFL’s most recent investment is an extension of the award-winning designs it has developed with Machinex. The company finished construction last year on what Miranda says is a state-of-the-art MRF in Pontiac, Michigan, modeled after its Winnipeg facility. That site came online at the end of last year.
With extended producer responsibility (EPR) legislation dominating much of the current conversation in the recycling industry, GFL also has used its MRF investments to position itself as a leader in that space.
In 2020, the company was awarded a contract from Recycle BC, a nonprofit organization in British Columbia responsible for residential paper and packaging recycling throughout the province. The stewardship group is funded by about 1,200 businesses, including retailers, manufacturers and restaurants, and facilitates fulfilling its responsibilities under British Columbia’s EPR system, which requires paper and packaging producers to fully finance and manage residential curbside and drop-off recycling programs for nearly 5 million residents.
GFL facilitates postcollection services for Recycle BC, managing the processing and marketing of 200,000 metric tons of material annually. Recycle BC says GFL’s investments in its own recycling infrastructure have helped to reduce contamination in the province.
In 2021, Ontario also released final regulations for establishing an EPR regime for printed paper packaging and products. Beginning this July, responsibility for managing such materials was transitioned to producers, and GFL is working with them through their respective producer responsibility organizations to find opportunities to maximize sorting of blue box materials, drive innovation in sorting and processing technologies, recycle more cost-effectively and help producers achieve regulated material performance targets.
“We continue to use the expertise we’ve gained from operating this program in other jurisdictions looking to implement EPR,” Miranda says.
“We expect that EPR legislation as it is adopted in more states across the U.S. and in other jurisdictions in Canada will undoubtedly impact the recycling market. Each jurisdiction is adopting its own version of the program, which means different materials will be covered in different jurisdictions, creating either standard eligible materials or packaging based on the final distribution. MRFs in the impacted jurisdictions will have to adapt to the resulting changes in the material stream and varying contamination levels based on source collection.”

What’s next?
Miranda says GFL continues to look for public-private partnerships as well as to build MRFs in what it deems key areas.
“We also will continue [using] the expertise we’ve gained from operating the Recycle BC program … in other jurisdictions looking to implement EPR,” Miranda adds, noting the company also will continue to invest in its workforce.
With a network of nearly 20,000 employees, GFL has set labor-related goals as part of its Sustainability Action Plan. Initiatives are aimed at building on the company’s “Safe for Life” program, which provides risk assessment, coaching and training, technology adoption and performance assessment to ensure a healthy and safe work environment.
“As it relates to the labor market, we continue to invest in our employees and are committed to being a place where they start and live out their careers,” Dovigi says. “Our talented workforce has enabled us to grow into the environmental solutions leader we are today.”

Explore the August 2023 Issue
Check out more from this issue and find your next story to read.
Latest from Recycling Today
- ReMA opposes European efforts seeking export restrictions for recyclables
- Fresh Perspective: Raj Bagaria
- Saica announces plans for second US site
- Update: Novelis produces first aluminum coil made fully from recycled end-of-life automotive scrap
- Aimplas doubles online course offerings
- Radius to be acquired by Toyota subsidiary
- Algoma EAF to start in April
- Erema sees strong demand for high-volume PET systems