Material recovery facilities have doubled in number since 1993, as mixed waste processing facilities only increased marginally; MRFs are currently processing less tonnage per facility than they were a few years ago, but are handling more types of materials; and finally, MRFs have not embraced technological advancements in sorting as previously expected. These are just some of the findings in an updated survey to be published as part of the "1995-96 Materials Recovery and Recycling Yearbook: A Directory, Atlas, and Guide" by Governmental Advisory Associates, Inc., Westport, Conn.
This article discusses the results of that national survey on MRFs and MWPFs, which allows for comparisons and the analysis of trends. It is the third such study conducted since 1990. But before discussing the findings in more detail, it is useful to define what is meant by a MRF and MWPF.
The GAA study focuses on the municipal solid waste stream. Thus, to be included, a facility had to process some degree of residential recyclables. Projects that handled exclusively industrial or commercial wastes were excluded. In addition, construction and debris facilities were not included. Finally, recycling centers and drop-off centers where recyclables were returned, but not sorted, were not a part of the study.
A MRF is defined as an installation that separates some portion of commingled recyclables into individual streams of marketable materials. The marketing of the recycled materials to brokers or end users is also an important function of the facilities. MRFs typically use both machinery of various degrees of complexity and human labor to separate the various materials. The processing that occurs at a MRF may be as complicated as separating a single stream of many types of recyclables (paper included) arriving at the facility, or as simple as separating various colors of glass from a pre-sorted glass stream and ferrous metal containers from a commingled metal container stream. The one characteristic that all MRFs in the study share is that they are receiving only recyclable material – they are not processing unsorted municipal solid waste.
In contrast, a MWPF accepts regular municipal solid waste. The waste is sorted from the tipping floor into recyclable materials and non-recyclable residue. The recyclable stream is then sorted further into marketable materials streams, and the residue is transported to a landfill or to other disposal alternatives. MWPFs, on average, tend to handle larger amounts of waste on a daily basis than do MRFs.
STATUS OF FACILITIES
There is no question that recycling processing has been a growth industry. This growth was driven in the early 1990s by political, regulatory and popular demand and is now being driven in part by market demand for certain materials. The strength of certain markets, particularly paper, has created a new interest in the processing municipal recyclables. Under certain circumstances, the adage of "gold in garbage" is becoming reality.
GAA’s 1991 study found 100 MRFs operating or planning to operate in the United States. More than one-half (55 percent) were found in the Northeast, with the other projects distributed over the remainder of the country.
By 1993, this number had just about doubled to 222 projects. The Northeast still dominated with 41 percent of the projects, but the distribution had become more even with respect to other regions. Today, there are 337 MRFs, an increase of 52 percent over 1993, and the dominance of the Northeast has diminished even further. That region now contains 31 percent of the facilities, with the South containing 26 percent, the Northcentral at 25 percent and the West with 18 percent of the projects (see figure 1, page 44).
Both the Midwest and the South have seen great increases in the proportion of projects located there, while the West has remained stable since 1993. Clearly, recycling is no longer restricted to the population centers of the Northeast. It is being done throughout the country.
Interestingly, a predicted national trend towards MWPFs has not occurred. As of 1993, GAA identified 35 mixed waste projects, with the majority located in the Midwest and West. The Northeast had only a few of these facilities.
Today, there are 47 MWPFs, a jump of about 34 percent. The largest proportion of these projects are found in the West. Figure 2 reflects the regional distribution. What is most startling is the degree to which the South has embraced the concept of mixed waste processing.
MWPFs have the advantage of not requiring a separate collection for recyclables. In addition, residents do not have to pre-sort their refuse because all separation takes place at a centralized facility.
The disadvantage is that a high degree of sorting at this type of facility is necessary, and health and safety considerations become paramount when workers are handling raw garbage. Costs saved by eliminating the need for a separate collection may be increased by the additional level of sorting required at a centralized point.
OWNERSHIP AND OPERATION
The study also examines the role of the private and public sector in owning and operating MRFs. There has always been a large degree of private sector involvement in MRFs, mirroring the private sector involvement in municipal refuse collection and disposal.
Private sector firms increased their share of MRF ownership from 55 percent of the facilities in 1991 to more than two-thirds (68 percent) in 1993. By 1995, this proportion had dropped a few percentage points to 63 percent. This drop may reflect some consolidation of projects that has occurred in the industry, and it is too early to tell if the trend will continue downward (see figure 2, page 45).
Although private sector operators have dominated since 1991, there has been an upward trend of public sector operation, particularly during the last two years. Perhaps this development may be explained by the changing markets for recyclables. Local governments may perceive that there are real economic gains to be achieved by recycling processing and, therefore, may be more willing to retain direct control over operations.
Besides private and government, other types of ownership include special authorities, voluntary, non-profit groups, and joint public-private sector partnerships.
FACILITY CAPACITY
MRFs on average are currently processing about 111 tons per day, ranging from 1.8 to 700 tons per day. The total tons processed daily by the 290 MRFs for which this information was available, was about 32,000 tons. On an annual basis, about 9.3 million tons of recyclables flow or are planned to flow through the 299 MRFs that reported these tonnages.
Since 1991, the average reported throughput of a MRF has decreased somewhat. In 1991 and 1993, the average daily throughput of materials was 134 and 131 tons per day of material respectively. By 1995, average tons per day had fallen to 111 tons per day. The probable explanation for this drop is the composition of the sample.
In 1991, only 35 percent of the reporting projects were operational, while the remainder were in planning stages or under construction. In 1993, 75 percent of the projects were operational with the remainder still in planning. And today, more than 80 percent of the reporting MRFs are operating, thus, tonnages reported reflect actual experience.
MWPFs, on the other hand, are much larger projects. On average, they process about 626 tons per day with an annual processing capacity of 10.4 million tons.
Keep in mind, however, that all the numbers being reported also include those given by facilities still in the planning stages.
DEGREE OF MECHANIZATION
One of the factors examined by GAA in its MRF studies is the degree of mechanization involved in sorting materials. One trend forecast by many observers was the increased reliance on mechanical sorting which would lower the need to use human sorters and increase the quality and consistency of the material streams to be marketed.
While the GAA survey documents the specific types of sorting equipment installed at MRFs, for the purposes of categorization MRFs were separated into two main types: those having a high degree of mechanized sorting and those having a low degree of mechanized sorting. Facilities sorting only by hand or using a conveyor belt with a magnetic separator were grouped into the low mechanization category. Facilities having other types of separation equipment in conjunction with a magnetic separator were grouped into the "high" classification.
In 1993, about two-thirds of all MRFs were in the "low" category. As can be observed, this did not change appreciably in 1995. While some MRFs reported their interest in examining new sorting technologies, many have not implemented these technologies yet.
Sponsored Content
Labor that Works
With 25 years of experience, Leadpoint delivers cost-effective workforce solutions tailored to your needs. We handle the recruiting, hiring, training, and onboarding to deliver stable, productive, and safety-focused teams. Our commitment to safety and quality ensures peace of mind with a reliable workforce that helps you achieve your goals.
Sponsored Content
Labor that Works
With 25 years of experience, Leadpoint delivers cost-effective workforce solutions tailored to your needs. We handle the recruiting, hiring, training, and onboarding to deliver stable, productive, and safety-focused teams. Our commitment to safety and quality ensures peace of mind with a reliable workforce that helps you achieve your goals.
Sponsored Content
Labor that Works
With 25 years of experience, Leadpoint delivers cost-effective workforce solutions tailored to your needs. We handle the recruiting, hiring, training, and onboarding to deliver stable, productive, and safety-focused teams. Our commitment to safety and quality ensures peace of mind with a reliable workforce that helps you achieve your goals.
Sponsored Content
Labor that Works
With 25 years of experience, Leadpoint delivers cost-effective workforce solutions tailored to your needs. We handle the recruiting, hiring, training, and onboarding to deliver stable, productive, and safety-focused teams. Our commitment to safety and quality ensures peace of mind with a reliable workforce that helps you achieve your goals.
Sponsored Content
Labor that Works
With 25 years of experience, Leadpoint delivers cost-effective workforce solutions tailored to your needs. We handle the recruiting, hiring, training, and onboarding to deliver stable, productive, and safety-focused teams. Our commitment to safety and quality ensures peace of mind with a reliable workforce that helps you achieve your goals.
If one analyzes the degree of mechanization by region, a different picture emerges. MRFs in the "low" category are well distributed by region. However, MRFs using a "high" degree of mechanization are found mainly in the Northeast, which has 41 percent of these types of projects. This may be because the rest of the country is now catching up with respect to building MRFs, and the degree of mechanization is lagging due to the lack of operating experience.
OTHER TRENDS
Other developments have occurred over the last several years. First, there has been an increasing realization that collection and processing are integral parts of a system. Thus, there have been experiments with various collection approaches.
These include "blue bag" programs where commingled containers are bagged for single-stream collection, whereby all recyclables (including paper) are commingled and collected; and co-collection programs that collect recyclables and regular garbage simultaneously.
In addition, certain localities are experimenting with or implementing automated recyclable collection systems. The GAA study identified 28 facilities that are part of a "blue bag" program, six that are receiving recyclables in a single stream, and six that service co-collection programs.
Second, the complexity of MRFs is increasing in relation to the types of materials that are being accepted and marketed. As of 1990, the average number of materials handled by MRFs was nine. As of 1993, this had increased to 13. In 1995, increases were noted in types of plastics handled, grades of paper accepted, and the recycling of aseptic packaging.
Third, a trend has occurred with respect to processing fees charged by the facilities. In 1990, 51 percent of the facilities did not charge a processing fee, 39 percent charged a tipping fee for materials and 10 percent paid for materials. In 1993, the facilities which did not charge a processing fee held constant at 51 percent, while the number of facilities charging a tip fee increased to 44 percent and those paying for materials dropped to 5 percent. In essence, these changes reflected the weak markets for recyclables prevailing at that time. While the final 1995 numbers have not yet been calculated, the proportion of facilities charging a processing fee for recyclables has dropped, while the percent paying for materials has increased.
This volatility in markets has forced local governments who are sending their recyclables to facilities operated by the private sector to be more adept at fashioning contracts that capture the benefits and contains the risks of market swings. Revenue sharing formulas, risk-sharing, periodic re-negotiation clauses have become elements of the contract relationships between MRFs and material suppliers.
Finally, as experience is gained, MRFs are branching out to take new materials and upgrade with new processing equipment. Older, less efficient facilities are shutting down with the material directed to more modern facilities or larger projects that can capture scale economies and exercise marketing power.
The author is the president of Governmental Advisory Associates Inc. Westport, Conn.
Get curated news on YOUR industry.
Enter your email to receive our newsletters.
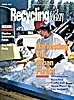
Explore the August 1995 Issue
Check out more from this issue and find your next story to read.
Latest from Recycling Today
- Toppoint Holdings expands chassis fleet
- Lego creates miniature tire recycling market
- Lux Research webinar examines chemical recycling timetables
- Plastics producer tracks pulse of wire recycling market
- Republic Services, Blue Polymers open Indianapolis recycling complex
- Altilium produces EV battery cells using recycled materials
- Brightmark enters subsidiaries of Indiana recycling facility into Chapter 11
- Freepoint Eco-Systems receives $50M loan for plastics recycling facility