After (and during) the ferrous market pricing drop of the late 1990s, a pertinent question for many shredder operators was whether there was an overcapacity situation in the auto shredding segment.
The answer to that question can certainly depend on one’s point of view. Operators of auto shredders would rather not have too many competitors chasing a limited supply of auto bodies, white goods and other feedstock.
Auto salvage companies and other businesses that sell their scrap to shredding plants, however, are generally pleased to have a competitive situation in their regions.
WHERE ARE THEY NOW? Matching the Market This shredders-per-capita number does not catch cross-border scrap flow or the level of economic activity that increases or decreases scrap generation in a given state. But looking at the shredder-to-people ratios in several states at the very least shows a fairly wide discrepancy can exist. State # of Shredders Population Ratio (per shredder) Iowa 9 3.0 million 330,000 Tennessee 12 5.7 million 475,000 Ohio 12 11.4 million 900,000 New Jersey 8 8.7 million 1.1 million North Carolina 7 8.0 million 1.1 million Texas 18 23 million 1.2 million Florida 11 16.0 million 1.4 million Nevada 1 2.0 million 2.0 million Massachusetts 2 6.3 million 3.1 million California 8 37.1 million 4.6 million Source: Recycling Today Media Group; number of shredders may include some still under construction
Regardless of viewpoint, a number of scrap yards throughout North America are investing a great deal of money on the premise that there is room for more capacity in the shredding market.
GRAND OPENINGS.
The surging scrap prices of this decade have helped put additional cash onto the balance sheets of scrap recyclers.Many of the recycling company owners who have been investing these profits into operations and capital equipment have done so by expanding their shredding capacity, or entering the shredding game for the first time.
One year ago, at the meeting of the BIR (Bureau of International Recycling) Shredder Committee at the organization’s 2006 World Recycling Conference & Exhibition in Beijing, Jim Schwartz of Metso-Texas Shredder Inc., San Antonio, said that more than two dozen (26) shredding plants installations were underway at that time.
That figure represented only shredder installations or retrofit projects that had been started since the committee last convened in Milan, Italy, in October of 2005.
Schwartz estimated that about 25 percent of these plants represent new shredder locations, while the remainder are expansions or upgrades of existing shredder plants.
"There is a bit of shredder mania going on," said Schwartz, who noted that the world’s scrap recyclers were pushing past more than 100 million tons of shredded scrap produced annually.
In the ensuing 12 months, there is little indication that the pace of shredder plant installations or upgrades has slowed down in any way.
A search of the Recycling Today Web site, at www.RecyclingToday.com, turned up news items covering the following investments from May 2006 to April 2007:
•
In April of 2007, Newell Recycling of Atlanta announced its agreement to purchase industrial property in the Port of Savannah to build a shredding plant there. "This expansion is just part of a larger plan permitted by the recent robust markets for scrap metal worldwide," says Bobby Triesch, vice president of Newell Recycling. The Savannah operation will include a shredder and downstream processing technologies such as eddy currents and metal sensors that will allow for higher recovery rates, according to the company.•
In March of this year, steelmaker Steel Dynamics Inc. announced its agreement to upgrade the shredding plant at its Virginia scrap processing subsidiary. Shredded Products LLC will upgrade its current shredder system located in Rocky Mount, Va. That project will include the installation of a downstream nonferrous sorting plant as well as upgrades such as a new motor and dust suppression system.•
This February, equipment supplier SGM Magnetics Co. announced that three different shredding facilities had invested in new downstream sorting equipment supplied by the company, including two shredder operators in New York state and one in Texas. The company also sold downstream equipment to a Chinese shredding plant operator in January.•
2007 started in January with announcements of new shredders in the state of Alabama (in Phenix City, to be operated by Blaze Recycling); in China (a system being supplied by The Shredder Co. to a recycler in Zhangjiagang, China); and in Saudi Arabia, also being supplied by The Shredder Co., to Al Sale Eastern, a scrap processor in Al Khobar, Saudi Arabia. Back in the United States, a notable shredder upgrade was also announced in January, with Chaparral Steel updating its old shredder with technology from The Shredder Co. that will allow it to increase production while using less energy.•
In November of 2006, Metal Management Inc., Chicago, announced that it had selected Wendt Corp. as the supplier of a replacement high-capacity shredder for its Newark, N.J., facility. Additionally, a new shredding plant location in the Port of Brownsville, Texas, was announced, to operate under the name Rio Grande Shredding Co. A news release from the port authority says a shredder valued at $6 million is being installed. Also in November, U.S. Shredder and Castings announced its involvement in a project that will allow Rifkin Scrap Iron and Metal Co. of Saginaw, Mich., to harvest more nonferrous metal from its shredding plant.•
Shredding-related news in October of 2006 included Joseph Behr & Sons Inc. holding a grand opening for its new auto shredder in Mason City, Iowa.•
During the summer of 2006, two proposed shredders in the same city, Mobile, Ala., made news, as permitting authorities in that city had to consider whether to extend permits to Alter Trading Co. and to David’s Auto Shredding. North Carolina’s Atlantic Scrap & Processing also announced that it was installing a shredding plant made by Harris at its new Wilmington, N.C., facility. A long permitting battle continued in June 2006 for Pacific Rail in Colton, Calif., which was seeking permission to build a shredder.•
In May of 2006, U.S. Shredder and Castings announced the sale of a plant to a recycler in Sterling, Ill., and Metso Texas Shredder announced the sale of plant to a scrap recycler in San Antonio, Texas.CROWDED CORNERS.
With the "shredder mania" continuing into 2007, the notion that excess shredding capacity must exist in some market regions seems tough to refute.Among states or regions that have seen the number of shredders multiply are Iowa, Texas and the Southeast.
In Iowa, new shredders this decade include the Behr plant in Mason City, which opened last year; the Shine Brothers Co. Inc. plant in Spencer, which opened in 2004; Alter Trading Co.’s revamped plant in Waterloo; and a shredder run by Clayton County Recycling in Monona, which was installed in late 2005 and early 2006.
If the data maintained by the Recycling Today Media Group is correct, there are currently nine shredding plants operating in Iowa to serve a population of about 3 million. This would seem to give Iowa one of the smallest people-to-shredder numbers in the nation, with a ratio of one shredder for every 330,000 people.
Contrasting numbers can be provided by Wisconsin, where six shredders serve a population of 5.5 million, for a ratio of one shredder to every 900,000 people.
Similarly, in Ohio, 12 shredders chew through the scrap generated by 11.4 million people, for a ratio that is again much closer to one shredder for every 900,000 people rather than fewer than 400,000, as occurs in Iowa.
In Texas, the number of shredders online will soon stand at 18.
With Texas having some 23 million people, this would seemingly provide it an operator-friendly 1.27 million people-to-shredding plants ratio. Yet scrap buyers in the state have long complained that competition for adequate material is fierce, which could be attributable to the fact that most of the shredders in Texas are large-production super-sized shredders.
In the Southeast, shredding capacity may be catching up to the swelling population and increased industrial and commercial activity in that region.
New shredding plants in Georgia, the Carolinas and Alabama are serving populations that are growing in number and affluence. Census data shows that in metropolitan Atlanta, some 1.5 million people have moved in during the past decade, placing it among the fastest growing U.S. regions.
CASH FLOW.
If the shredder-to-population ratio in any given market region dips below 900,000—as has happened in Iowa—is that a signal of an overcapacity situation?That answer has several variables, although what it can ultimately boil down to is how much material must be obtained for a shredder each month to allow it to operate profitably.
Variables in figuring that out are also many. On the expense side, operators must pay for power, labor, wear parts and other operating costs when deciding what they can afford to pay for material as shredder feedstock.
Without a profit margin, there is no point in ramping up a shredder. But can a shredder be run profitably if it operates at less than a full-time clip?
That’s what several shredder operators are finding out. In some cases, noise and zoning ordinances or energy use agreements are affecting how many hours certain shredding plants can run throughout the week.
The limitation for other operators, however, can be finding suitable material. Even with record-high scale prices, some plants are running fewer hours because they have chewed through their inventories and are not seeing a sufficient flow of material to maintain a 30- or 40-hour shredding week.
By previous standards that would seem to indicate that there is, in fact, a shredder overcapacity situation.
However, in the short-term, operators have been helped by pumped up prices. The ability to fetch more than $200 per ton for ferrous shred and record prices for red metals and aluminum shred have given operators a more comfortable margin as well as built up cash to re-invest in operations.
Additionally, operators of heavy-duty shredders are expanding their feedstock options by including more plate and structural scrap into their shredded grades.
As a number of the shredder upgrade summaries above indicate, some of these investments are being made in downstream systems. Shredding plant operators with even the most deep and loyal ferrous scrap roots have begun to maximize the nonferrous they mine from their operations. As shredding plants increasingly harvest not only ferrous shred with a desirable chemistry but also nonferrous grades that can meet the expectations of a growing range of consumers, this can boost the an operation per-hour revenue.
Such a conclusion is far from being reached—record-high prices can make future assumptions debatable. However, a number of scrap recyclers are putting their money into shredding plants and sorting systems with a primary goal based not strictly on volume, but rather on the production of several high-value materials (ferrous and nonferrous) derived from one complex operation.
Should this model prove sustainable, it could mean that old assumptions about shredder capacity must be reconsidered.
The author is editor in chief of the Recycling Today Media Group and can be contacted at btaylor@gie.net.
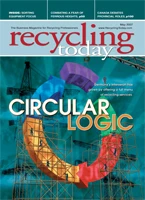
Explore the May 2007 Issue
Check out more from this issue and find your next story to read.
Latest from Recycling Today
- Nucor receives West Virginia funding assist
- Ferrous market ends 2024 in familiar rut
- Aqua Metals secures $1.5M loan, reports operational strides
- AF&PA urges veto of NY bill
- Aluminum Association includes recycling among 2025 policy priorities
- AISI applauds waterways spending bill
- Lux Research questions hydrogen’s transportation role
- Sonoco selling thermoformed, flexible packaging business to Toppan for $1.8B