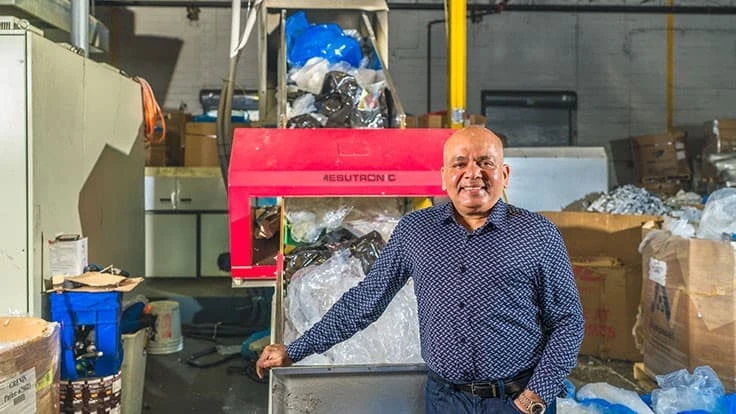
Photos: Creative Click Photography

GDB International Inc. plans to expand its film recycling capabilities this year with the addition of three lines supplied by Erema of Austria. Prior to 2018, the New Brunswick, New Jersey-based company primarily exported the polyethylene—low density (LDPE), linear low density (LLDPE) and high density (HDPE)—film scrap it collected from various generators, including retailers. But when China stopped accepting plastic scrap imports in 2018, Sunil Bagaria, president of GDB International and the current chair of the Institute of Scrap Recycling Industries’ Plastics Division, knew the company needed to alter its business model. After installing three lines supplied by a Chinese manufacturer, GDB began producing postconsumer resin (PCR) in late 2018.
He says China’s plastic scrap import ban led to the realization in the U.S. that for the plastics supply chain to be circular, PCR had to be produced domestically.
In addition to producing PCR, the company ships some plastic scrap to overseas consumers in compliance with rules laid out under the Basel Convention and strongly encourages preshipment inspections. It also supplies scrap to other domestic reprocessors.
Bagaria says GDB handles roughly 200 loads, or 8 million pounds, of plastic film scrap per month. (The company also trades other forms of plastic scrap.) Of the 96 million pounds of film scrap it handles annually, GDB reprocesses roughly 20 percent. “We are restricted by the number of machines that are working,” he says. “And that will change once the new machines are put in.”
Getting the feel for it
Established in 1993, GDB historically was a trading company, exporting the plastic film scrap it collected from industrial and commercial clients. In a typical year, the company would ship approximately 3,600 containers of plastic scrap overseas.
Prior to starting up the first of its pelletizing lines, GDB sorted, baled and shipped the plastic scrap it collected to domestic and overseas operations for processing into flake or pellets. But with China’s import restrictions, Bagaria says the only enduring solution was to develop domestic recycling and reprocessing capacity. “There is more value to be realized and shared,” he said in 2018. “We will help them see that recycling can pay. It has to make economic sense; only then will the recycling story be successful.”
When GDB decided to begin producing PCR, Bagaria, who has a master’s degree in polymer engineering, knew the transition would involve trial and error. Unlike polyethylene terephthalate (PET) and HDPE bottles, he says, film scrap can vary considerably in melt index and density. “The feedstock could be from so many generation streams, but the end product has to be consistent,” he says. “The biggest challenge was producing a consistent final product.”
The company’s New Brunswick plant is 110,000 square feet. Approximately 60,000 square feet house GDB’s current pellet production operation, with lines consisting of metal detectors, inline densifiers, vented extruders equipped with automatic screen changers and underwater pelletizers supplied by Jiangsu Fangsheng Machinery Co. Ltd.
The company did not invest in top-of-the-line equipment to start, Bagaria says, because it needed to learn to work with its feedstock to produce a consistent product. “These machines taught us that,” he says of the initial equipment GDB purchased. “We could not afford to learn on the Erema machines.”
Now that GDB has perfected its in-house recipes and production processes to produce PCR with consistency, Bagaria says the company is ready to advance to the next level with its investment in the Erema equipment.

New equipment, new locations
The Erema lines will be installed in a building the company has purchased about 40 miles away from its New Brunswick site, which lacked the space to expand, in Mount Holly, New Jersey. Bagaria says once the new machines are up and running later this year, GDB will relocate its three original lines from New Brunswick to the Mount Holly site as well. “We will have a dedicated PCR production facility,” he says.
The company is hiring an additional 15 people to work at the new location, including two to three operations managers and machine operators.
Bagaria credits GDB’s staff for the success the company has achieved so far. “I still consider our business as a family business,” he says. “And I think our philosophy is that our people’s expectations should be met. I think my biggest responsibility, my biggest job, is to make sure these people are happy. We value our people so much, and we really appreciate their contribution in the company.”
GDB will work with Erema to train its new employees for the Mount Holly site at the equipment supplier’s Massachusetts facility.
Regarding Erema, Bagaria says, “They do go out of their way.” He adds that Erema views its role as more than an equipment supplier. “Their main role is making sure that you are successful with their machine. So, they extend all kinds of help, all kinds of assistance and support.”
GDB’s expansion plans go beyond the new PCR production site and the new Erema equipment. Bagaria says the company is adding warehouses to join those it already operates in Ohio, Wisconsin, Florida, Illinois and Tennessee.
“This is what the recycling industry needed: consistent demand for PCR. And these mandates will help decouple the price of PCR from the price of virgin.” – Sunil Bagaria, president, GDB International
“We are strategically opening collection points or collection warehouses,” he says, adding that GDB plans to have 10 warehouses of considerable square footage by the end of 2023. “So, if there is a load available, a light load—10,000, 20,000 pounds—available in Florida, the generator will have the ability to deliver to our Florida warehouse. We cannot afford to bring that load here to New Jersey.”
Each of these warehouses will be equipped with two-ram balers and will give GDB the ability to better serve generators of plastic film and other forms of plastic scrap. Bagaria says the company expects to hire 40 employees to staff these sites, bringing its total number of employees to 320.
“We are very much focused on infrastructure development,” Bagaria says. “You know you are only as strong as the suppliers that you have when it comes to making PCR.”
He continues, “Ultimately, there will be [pelletizers] put in those locations, too. But, right now, we are focused in New Jersey. We want to reach our 100-million-pound target in New Jersey.”
Bagaria says the company’s warehouses in Ohio and Wisconsin will be its next PCR production sites.

Growing demand
GDB’s investments in new capacity respond to the growing demand for PCR in the form of voluntary commitments as well as government mandates. GDB’s home state of New Jersey recently passed legislation that mandates recycled content in rigid plastic containers, glass containers, paper and plastic carryout bags and plastic trash bags.
New Jersey Gov. Phil Murphy signed S2515/A4676 into law in mid-January. Beginning five years after the effective date and every three years thereafter, the percentage of PCR required for rigid plastic containers will increase by 5 percent until it reaches 50 percent. Plastic carryout bags will be required to contain at least 20 percent PCR beginning two years after the law’s effective date and 40 percent PCR after five years. Beginning two years after the law’s effective date, all plastic trash bags must contain at least 10 percent PCR, increasing to 20 percent in five years.
“This is what the recycling industry needed: consistent demand for PCR,” Bagaria says. “And these mandates will help decouple the price of PCR from the price of virgin.
“Demand and decoupling are good things,” he adds. “It is giving us a lot of satisfaction in our hearts that we are moving on the right track.”
Bagaria says production costs account for 20 percent of virgin plastics costs, while raw materials are 80 percent. The ratio is flipped for recyclers. “The cost of feedstock is only 25 percent to 30 percent of the final product cost,” he says.
Bagaria says GDB’s PCR production for the year is committed. “We can’t sell on a spot basis.”
Given that and the growing demand for PCR, GDB’s investments are well-timed. Bagaria says GDB is “excited about the shape of things to come. ... 2022 will be a big year for us in the sense that we will have these machines put in.”
He says GDB’s PCR production will increase from 18 million pounds in 2021 to at least 8 million pounds per month, or 96 million pounds annually, with the Erema machines.
“We are excited about what we have learned,” Bagaria says of the last three years. “And we are excited about the future. Our country is going in the right direction. When this China problem happened, it seemed like oh, my gosh, this is the end of it … [But] I think it’s the best thing that has happened for our country.”
Get curated news on YOUR industry.
Enter your email to receive our newsletters.
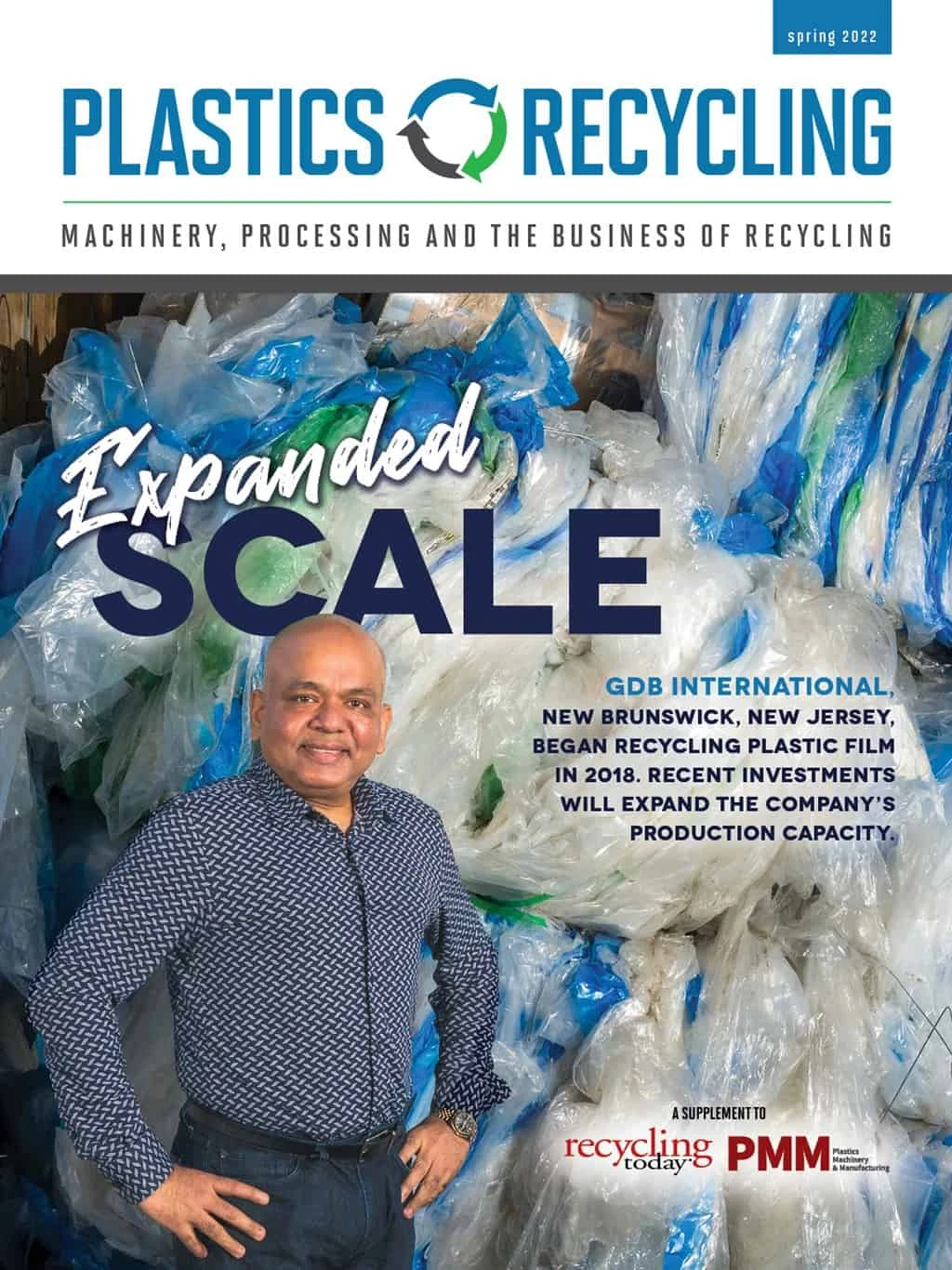
Explore the Spring 2022 Plastics Recycling Issue
Check out more from this issue and find your next story to read.
Latest from Recycling Today
- ReMA opposes European efforts seeking export restrictions for recyclables
- Fresh Perspective: Raj Bagaria
- Saica announces plans for second US site
- Update: Novelis produces first aluminum coil made fully from recycled end-of-life automotive scrap
- Aimplas doubles online course offerings
- Radius to be acquired by Toyota subsidiary
- Algoma EAF to start in April
- Erema sees strong demand for high-volume PET systems