
The Original Günther SPLITTER®

With over 400 installations worldwide and the original spiral shaft screening design (patented in 2004), Günther’s original SPLITTER® screen has entered the North American market with the ability to process a variety of common material streams.
Aligned, interlocked screws perform a corkscrew motion with the ability to separate different materials by size. The screen’s flat design allows oversized material as well as film or long stringy parts to swim over the screws. Smaller materials fall through the shafts. (The size of this material is adjustable by changing the distance between screws.) The SPLITTER® also can be angled and is customizable in length and speed, with multiple configuration options available.
“We encourage customers to ask us about the different possibilities with this screen,” says Adam Lovewell, process engineer for Van Dyk Recycling Solutions. “This is another great tool for our equipment toolbox, and there is lots to consider. The specific application, type of material, preparation of material, feed to the equipment, and collection of outputs are all factors that influence the design and proper implementation of this machine.”
Multiple possibilities

Primary goals of the SPLITTER® can be to skim off oversized materials or screen out fine materials that pose a challenge to downstream operations. It is particularly good at long part separating, as those materials carry over the screws effortlessly. “This is a game-changer in the preprocessing of material,” says Ryan Cournoyer, process engineer for Van Dyk Recycling Solutions. “It perfectly complements our other machinery by taking care of tough material upstream so that the downstream machinery can process more effectively.”
Low-maintenance wonder

Due to the lateral motion of the screws and the “open-sided” design, the SPLITTER® naturally purges any material that would wrap in a traditional screen.
“One plant I visited said they have been operating their SPLITTER® for over 8,000 hours and have not needed to clean it once,” says Cournoyer. “Absolutely nothing wraps.”
Additionally, no star changes are required, and cost of ownership is very low. Heavy-duty construction makes for resilient screws that do not bend or incur wear, even when processing heavy materials.
For more information on the Günther SPLITTER®, contact Van Dyk Recycling Solutions at 203-967-1100 or info@vdrs.com.
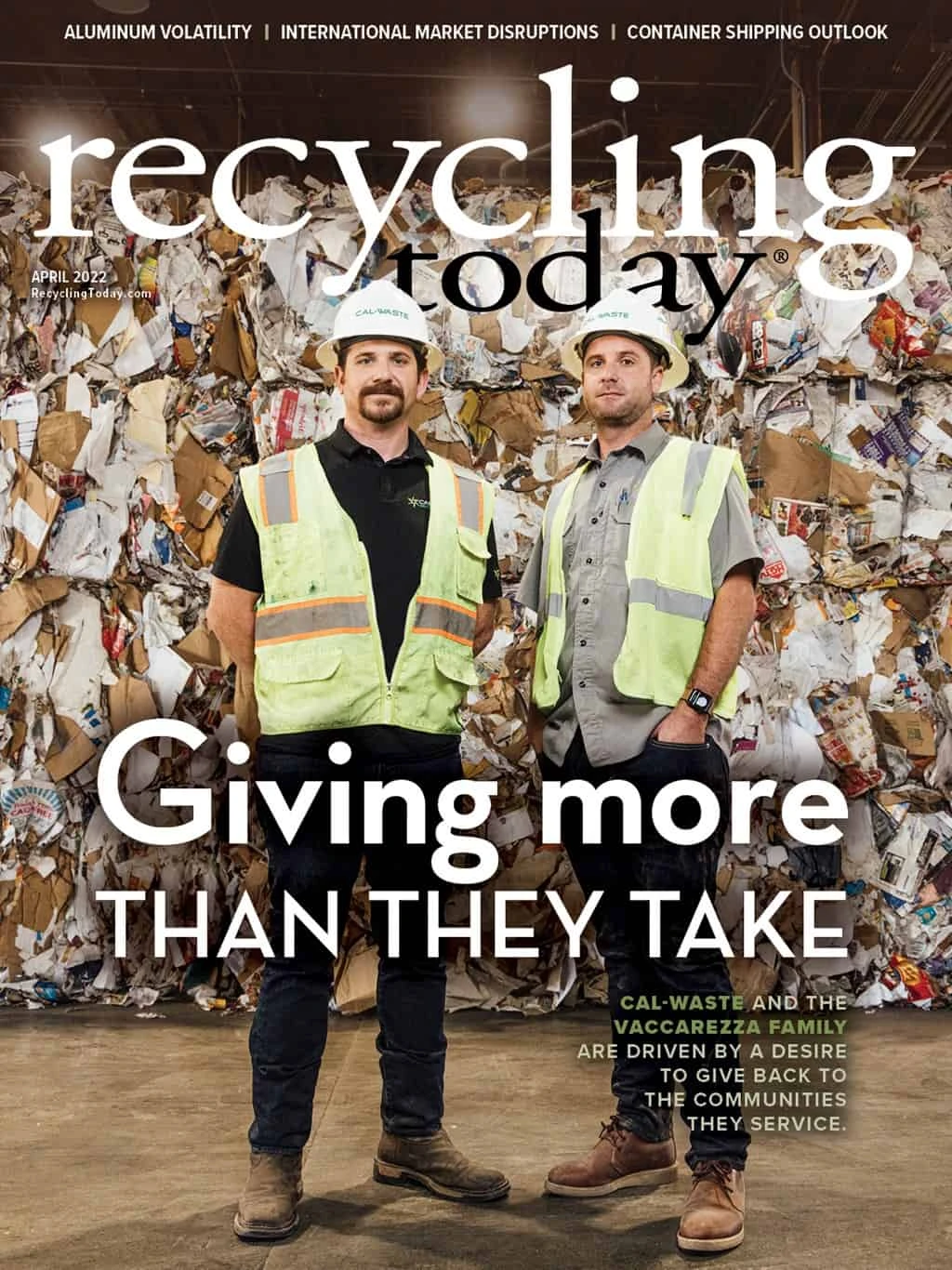
Explore the April 2022 Issue
Check out more from this issue and find your next story to read.
Latest from Recycling Today
- APR, RecyClass release partnership progress report
- Clearpoint Recycling, Enviroo sign PET supply contract
- Invista expanding ISCC Plus certification program
- Redwood partnership targets recycling of medium-format batteries
- Enfinite forms Hazardous & Specialty Waste Management Council
- Combined DRS, EPR legislation introduced in Rhode Island
- Eureka Recycling starts up newly upgraded MRF
- Reconomy Close the Gap campaign highlights need for circularity