Although stronger domestic demand for ferrous scrap has lessened the amount exported from the U.S. during the past 18 months or so, developing economies in Far East and Pacific Rim countries are expected to provide strong scrap demand for the foreseeable future.
While the number of scrap processors and brokers involved in export activities is not expected to increase significantly, competition for export opportunities is fierce, leading exporters to look for the best available equipment and location in order to operate in the most efficient manner possible.
"The situation is not what I would call bullish for exports, since there is a better domestic market for scrap," says Gerald Houck, ferrous commodity expert for the U.S. Bureau of Mines, Washington. "You see more exports from the Northeast Coast, the West Coast – places where domestic demand is weak. On the other hand, Gulf Coast exports have disappeared, since there is so much demand there. It’s hard to find materials to export when Bayou Steel is right there and Nucor is a few hundred miles away soaking up every ton of steel in sight."
Near the West Coast, however, he says, there is a plant under construction in Kingman, Arizona, which will require quite a bit of scrap from the Los Angeles area. In addition, Korea and other Asian countries are providing steady demand for U.S. scrap.
DEEP WATER
There are some facility characteristics that make for a successful export operation, according to Gary Schnitzer, executive vice president, Schnitzer Steel, Oakland, Calif.
"Basically, it’s essential to have a good-sized piece of property on deep water with first-rate loading equipment," says Schnitzer. "We use a combination of conveyors and whirly cranes. It’s important to have first-rate, recent models that can handle lots of tons per hour."
The company uses the cranes for heavy scrap and the conveyors for shredded scrap, Schnitzer explains. "We like conveyors because they are fast, but they are also high-maintenance. You do see problems with dust and noise associated with conveyors, but ours are all completely enclosed."
Schnitzer has three waterfront sites, in Tacoma, Wash., Portland, Ore., and Oakland, Calif. "If you’re not on deep water, it’s hard to be in the export business," says Schnitzer. "You get into too many extra handling and transportation expenses, and it eats into your profits on an already slim margin. It’s particularly difficult when markets are weak if you are double handling materials."
It’s unlikely that many new companies will break into the export business, says Schnitzer. "It’s so expensive, you can’t get involved overnight. You have to acquire a 20 or 30 acre site, dock, cranes – it can cost millions.
"There are limited applications, limited facilities, and limited scrap that can go abroad since the domestic demand is so strong," he adds. "There are not too many areas where it’s more efficient to ship materials abroad instead of selling them domestically, and existing exporters compete fiercely for orders, especially in soft markets."
Schnitzer Steel exports grades such as bonus grade scrap, heavy melting scrap and busheling to the Pacific Rim, Southeast Asia, India and Pakistan. "All these markets are firm now, and we see good growth," says Schnitzer.
A special configuration of the port facility is not essential, says Schnitzer – the important thing is having access to deep water. "We work with what we have," he says. "Our property in Portland is 200 acres, Tacoma is 20 acres and Oakland is 30. The bigger the better because you can stockpile more scrap. Twenty to 30 acres is optimal, and deep water is good, so you can accommodate larger ships and benefit from the cheaper freight rates.
"We’re lucky enough to have first-class cranes and conveyors," Schnitzer continues. "We move scrap right from the stockpiles to the ships in Portland and Tacoma, but not in Oakland. We’re always looking at upgrading our equipment – we spend a lot of money upgrading equipment. It’s essential to have state-of-the-art equipment if you’re going to be a survivor in this industry."
One Northeast ferrous scrap processor and exporter says his company hasn’t particularly stepped up their exports over past few years – exports have remained fairly constant. Although the company recently opened a new port facility, it was "just another facility to do business out of," not a result of increased export opportunities.
"Overall, the export business has been pretty good over the past few years," he says. "Demand overseas will continue to improve, although there will be the usual setbacks from time to time."
A complete operation for export includes the use of equipment such as cranes, magnets, loaders, and shears, says the processor, but the ideal setup for an export facility is "whatever works. A lot of people load by pan, some by grapple, some by conveyor. You go for whatever is the most efficient and aim for minimal handling."
The smart exporter will take advantage of modern technology, he adds. "It helps to be technologically advanced. It means you’re more up-to-date and more efficient, so your chances of survival are better."
DOCKSIDE STOCKPILING
For companies in the export business that load materials on ships, having the capability to stockpile materials dockside is "absolutely critical," according to Les Krohnfeldt, executive vice president of Hiuka America Corp., Port of Long Beach, Calif., a large exporter of ferrous scrap to Japan, Korea, China, Taiwan, Thailand, the Phillippines, Singapore, Malaysia, Indonesia and India.
"Without that, you have the double handling of bringing materials forward for shipping, and also if materials are not stockpiled, it’s probably going to have an impact on the type of ship loading system you select," says Krohnfeldt. "On the East Coast and in some places on the West Coast, if you don’t have a stockpiling system, you have to have additional equipment we’re not using."
Hiuka America had the great advantage of being able to set up a system in its Port of Long Beach facility that exactly meets the company’s needs, he adds.
"Port land is valuable and scarce," Krohnfeldt explains. "But if you do get property, the ideal is to have a parcel of land that is wider and narrower, as opposed to narrow and deep. The longer a facility is and the shallower, the more it forces materials to be stockpiled closer to the water’s edge. This minimizes handling. Our facility is 900 feet long and 600 feet deep."
After the property has been selected, it’s a matter of selecting the proper ship loading equipment, he says. There are differing opinions in the industry about what equipment works best, and it also depends on the types of material being loaded.
"In our case, a large portion is Number 1 heavy melting steel, so it made good sense environmentally and logistically to use a whirly crane mounted on tracks that can move up and down the yard," says Krohnfeldt. "It has an 18.5 cubic yard mechanical grapple that picks up material and loads it directly into the vessel. It serves a number of purposes, and it’s a very effective loading system, minimizing the handling of the material."
The whirly crane can load more than 10,000 tons per day, according to company statements, and it can place large dozers inside a ship’s hold to evenly distribute cargo inside, allowing the company to maximize the amount of cargo per shipment.
The alternative system, which is particularly suited for bulk loading, he adds, is the conveyor system.
After choosing the appropriate ship loading equipment, says Krohnfeldt, "it’s not a matter of special equipment – just dependable equipment. For backup, we have cranes using magnets and grapples for truck and rail receiving and stockpiling. We support that with front-end loaders that can move materials."
Although Hiuka America has done some baling of scrap in the past, the company now relies more on shearing to get materials to the proper size, says Krohnfeldt.
ENVIRONMENTAL ISSUES
As in any scrap processing operation, environmental and land use restrictions have to be considered in export facilities, especially those located at ports.
"Both the Port of Long Beach and the Port of Los Angeles have restrictions against any shredding operations, because of potential environmental problems," says Krohnfeldt.
Environmental protection measures the company has instituted include covering the entire site with a layer of concrete over a geomembrane liner. The port site slopes away from the wharf, and runoff is fed into drainage area and then reclaimed.
"We also employ along the dockside a 12-foot-high concrete retaining wall," says Krohnfeldt. "This serves multiple purposes. It protects materials and keeps them from scattering on the dock and potentially ending up in the water if not handled properly. It also provides a significant sound barrier. Another key thing is that by being able to stockpile against a 12-foot wall, we increase our stockpile capacity for the crane."
The future of ferrous scrap exports looks very favorable, according to Krohnfeldt. "There’s the balance of trade issue, the generation of scrap metal, the geographic specifics of that – in Southern California, transportation determines that export is more favorable than domestic sale of the materials. Also, the demand in Asia and the Pacific Rim is ever-increasing."
Sponsored Content
Labor that Works
With 25 years of experience, Leadpoint delivers cost-effective workforce solutions tailored to your needs. We handle the recruiting, hiring, training, and onboarding to deliver stable, productive, and safety-focused teams. Our commitment to safety and quality ensures peace of mind with a reliable workforce that helps you achieve your goals.
COMPETITIVE MARKET
Exporting ferrous scrap is very competitive through the U.S., according to a spokesperson for a West Coast scrap exporter. "There’s a lot of competition out there with buyers in terms of price and service," she says.
She notes some scrap processors getting into exports because prices are higher now than they’ve been in a long time. "Scrap companies may be getting into exports as a way to expand their base now that scrap prices are high."
But even though some processors new to the market may be getting involved in exports, in general the market remains unchanged.
"There really hasn’t been any change in the companies involved in exporting scrap ferrous here in California," says Joe Massey, executive director of the Northern California chapter of the Institute of Scrap Recycling Industries.
What's new is that many scrap processors are making equipment purchases now because the markets are up, he adds. "It’s a very cyclical industry – when things are going well, equipment purchases go up because people can afford the investments. They’re buying equipment such as new shears, new balers, and normal material handling machines such as forklifts and grabbers."
KNOW THE CONSUMER
Although some items, such as ship loading equipment of some type, is obviously critical for export facilities on ports, in general no special equipment is needed to prepare materials for export, according to one prominent equipment dealer.
"We deal with quite a lot of customers that export," he says, "and there’s virtually no difference between the equipment needed to sell scrap domestically and for export."
The most important consideration, when buying equipment for an export facility, he says, is to know the consumer’s requirements.
"The caveat is the same no matter what market you sell to – the consumer dictates the type of product they need and the size they want, and then you make the decision about the appropriate equipment to meet those needs. No particular piece of equipment can open up export markets for you."
As for the future of U.S. ferrous scrap exports, most say the future looks promising.
"Things look good – there’s good demand," says one industry observer. "People say it will continue through 1996, but you just never know. Currencies could experience a blip. If the dollar goes down, who knows what could happen?"
The author is editor of Recycling Today.
Get curated news on YOUR industry.
Enter your email to receive our newsletters.
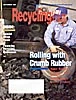
Explore the September 1995 Issue
Check out more from this issue and find your next story to read.
Latest from Recycling Today
- AF&PA report shows decrease in packaging paper shipments
- GreenMantra names new CEO
- Agilyx says Styrenyx technology reduces carbon footprint in styrene production
- SABIC’s Trucircle PE used for greenhouse roofing
- Hydro to add wire rod casthouse in Norway
- Hindalco to invest in copper, aluminum business in India
- Recycled steel price crosses $500 per ton threshold
- Smithers report looks at PCR plastic’s near-term prospects