Prompt industrial scrap is handled in many different ways, but seldom is it sent on a 1,000-mile closed-loop journey from the place it is generated back to where the original metal came from, remelted, re-rolled and shipped back as useable aluminum sheet.
But that isn’t stopping Ford Motor Co., Dearborn, Mich., and the Alcan Automotive division of Alcan Aluminum Corp., Cleveland, from trying.
With a $400,000 separation system designed by OmniSource Corp., Fort Wayne, Ind., Ford’s Chicago Stamping Plant segregates the stream of aluminum and ferrous scrap running underneath its thundering stamping lines and ships the aluminum in bulk to OmniSource’s East Chicago, Ind., plant. There it is pressed into 1,000-pound bales and sent directly back to its source—Alcan’s Oswego, N.Y., aluminum sheet mill.
The idea is to slash Ford’s raw material costs for the AA6111 aluminum it uses to stamp hoods, while brightening aluminum’s overall profile among automotive designers looking for economical ways to meet ever-tightening fuel efficiency and strength-to-weight requirements in their vehicles. And while buyback programs between large sheet metal users and suppliers are nothing new, Ford and Alcan believe their latest twist is unique, at least to the domestic market.
"This is the first production application in North America where [aluminum scrap] actually is being reclaimed in its original state," Alcan Vice President Tom Gannon says of the program, which officially kicked off in late summer 2002. "It is indeed a closed-loop system.
"It’s actually better than we anticipated in the sense that we did all the work up-front," he adds. "We were very careful in not rushing into this. We wanted to make sure the scrap met the purity levels as far as iron and moisture content."
DISSECTING THE PROCESS
Indeed, the key to making the plan work for both parties is purity—getting AA6111 and only AA6111 back to Alcan’s Oswego mill efficiently.
As aluminum scrap is cut from blanks in the stamping dies, it drops onto the plant’s scrap conveyor system. The conveyor system carries both ferrous and nonferrous material, so Omnisource developed a series of three magnets and a shaker table that culls the ferrous material from the aluminum. What remains is AA6111 pure enough to be melted and processed straight back into blanks, which are manufactured into hoods for vehicles such as the Lincoln Town Car and F-150 and Ranger pickup trucks.
The new system is a significant improvement over the old separation process, according to Rick Rifkin, vice president of the nonferrous operating group at OmniSource.
"The material coming out of the stamping facility was contaminated with steel; we and Ford did a fair amount of good separation, but it was not what we would call mill quality," says Rifkin, whose company was serving as a scrap processor for the Ford plant and as a supplier to Alcan before the new system was put in place. "As a result, a lot of it was going into secondary smelters [that were] making die-casting alloys. It wasn’t clean enough for Alcan to use to make that grade."
This pointed to a major concern harbored by at least one experienced scrap processor— plants trying to perform the "Closed-Loop Waltz" without the means to segregate material properly.
"The danger I see is that other manufacturing plants that do not have the capability to separate their material or prepare material correctly will get the idea that this is something they can do," says Phil Zeid, president of Universal Scrap Metals in Chicago. "We’ve seen it before, and it’s a very difficult thing. Normally we encourage them to try to do it, but there’s time, effort and cost involved in preparing it correctly."
GREEN DAY
Because remelting is widely considered to us only 5 percent of the energy needed to create primary aluminum from ore, the program makes simple economic sense for both parties—Ford gets a far better return on its recycled scrap, and Alcan saves energy costs and can boast of its use of recycled materials.
"I think it really started with our long-term efforts to reduce the overall cost of aluminum, making it more attractive to the car companies," Gannon says. "When you look at the value stream, if you can get this material and get it back to the facility where it started from, you have the best opportunity of extracting the maximum amount of value from the material itself."
Using somewhat inexact figures, Andy Acho, world-wide director of environmental outreach and strategy for Ford Motor Co., explains that Ford may get 50 cents back for every dollar it spends on raw material when different kinds of scrap are swept up together. In a closed loop system, that payback shoots up to around 85 cents on the dollar when the user, Ford, becomes a supplier of premium quality scrap to its supplier, Alcan.
Gannon explains Ford’s advantage another way: Say Ford spends 65 cents on a pound of primary aluminum and can get one pound of aluminum sheet back for every pound it sends back to Alcan. Given that recycling costs 95 percent less than producing primary aluminum, and that the plant can recover about 50 percent of every blank it stamps, Ford can cut the cost for half of its material volume down to perhaps 15 cents a pound. That, in turn, slashes Ford’s overall material cost to about 40 cents a pound at the end of the day.
And while total costs are not exactly cut in half—the bottom-line savings work out to about 40 percent, Gannon says—it adds up pretty quickly, especially when you consider that the Chicago Stamping Plant is Ford’s biggest aluminum sheet consumer, stamping out 1.3 million hoods a year.
"The math works," Acho says. "When you have that kind of quantity, it does make sense to find a process that allows you to save everything."
And by the way, the math works for Alcan, as well, he noted.
"It’s not coming out of their margins," Acho said. "We’re not asking them to reduce their price. They’re reducing costs.
"It cost us $400,000 up-front to be able to make this happen, [but] we’re saving more than $2.5 million each year over and above the normal aluminum recycling," Acho says.
Acho’s work on making Ford a leader in the green company movement began at the behest of Chairman Bill Ford, who appointed Acho to his current post in 1990. About that same time, the company created its own personal RAT Patrol, short for Recycling Action Team. The group’s directives were to find uses for post-consumer recyclables in products that were as good or better than the ones they were replacing and to make them profitably.
"This [closed-loop program] is consistent with the Ford revitalization plan that Bill Ford talks about—it meets the criteria of reducing waste and enhancing efficiency while reducing costs," Acho says.
A manufacturer would be hard-pressed to find a material that is a better candidate than aluminum for such a closed-loop program. It does not rust and, unlike some other materials, its value does not decrease in the recycling process.
"The plant made the decision to run one alloy; that really gave us a good foundation from which we could begin to pursue a clean segregation system," Gannon says. "The challenge was to try to separate the 6111 from any other contaminants mixed in with it from the other parts produced there. That’s where the investment decision had to be made."
When that decision was made, the three companies spent a full year testing the system privately before they went public with it.
AN ALUMINUM FUTURE
As for fears that such closed-loop programs will shove certain scrap metal processors off the dance floor, OmniSource’s Rifkin says he is confident that companies with a good handle on processing and segregation will have something to offer major users and suppliers.
"I think there’s always going to be a place for the traditional scrap processor," Rifkin says.
"I think scrap in general will be in relatively short supply as manufacturing continues to be more efficient," he adds. "I think as mills and consumers try to continue to drive down raw material costs, demand will remain, and supply will be relatively tight, especially as demand from overseas continues to pull a lot of scrap off North American shores."
Gannon says, "There are other car companies that are stamping in significant volumes, and we’re beginning to get systems in place to recover their scrap, as well."
"It is relatively easy to capture both the stamping offal as well as when you recycle a vehicle [in terms of] the larger components that happen to be aluminum today," says Gannon. "The infrastructure is in place to reclaim the material, and the demands for secondary aluminum continue to be very high.
"There is a demand, there is an infrastructure; but aside from that, look at the economic and environmental benefits," he comments.
As domestic automakers look at aluminum’s weight benefits for larger parts such as SUV tailgates and fenders, Alcan and other aluminum companies can bank on more business, because aluminum alloys offer 50 percent weight savings for material of equal strength.
"The benefits go beyond fuel efficiency and beyond the consumer’s ability to lift or slide a panel," Gannon says. "You get into the secondary weight savings and overall costs to the car companies."
"We hope that this is the beginning," Gannon adds.
Ancho remarks, "I think this well serve as a model for future aluminum recycling. We’re not looking for you [the supplier] to give us lower prices; we’re looking for you to have lower costs. We’ve got to have these companies do this in market-driven ways and make a profit. Then it becomes sustainable."
The author is a freelance writer based in central Wisconsin. He can be reached at lincbrunner@sbcglobal.net.
Get curated news on YOUR industry.
Enter your email to receive our newsletters.
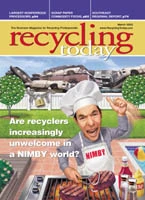
Explore the March 2003 Issue
Check out more from this issue and find your next story to read.
Latest from Recycling Today
- LumiCup offers single-use plastic alternative
- European project yields recycled-content ABS
- ICM to host colocated events in Shanghai
- Astera runs into NIMBY concerns in Colorado
- ReMA opposes European efforts seeking export restrictions for recyclables
- Fresh Perspective: Raj Bagaria
- Saica announces plans for second US site
- Update: Novelis produces first aluminum coil made fully from recycled end-of-life automotive scrap