Alternative energy and energy independence as concepts have enjoyed growing support from the American public throughout the second half of this decade.
The forms of alternative energy that have been implemented, researched and proposed are numerous and draw upon sources ranging from the wind, the sun, agricultural products and waste and recyclables.
Low-value commodities handled by C&D recyclers are among the materials that are placed into the last category, often as part of the range of fuel sources known together as biomass fuels.
There are a range of scenarios that could unfold regarding how materials such as scrap wood and land-clearing debris might fit into the nation’s energy future, with some scenarios offering a stable market for mixed C&D recyclers.
THE FOREST FOR THE TREES
Recyclers are not the only ones with an interest in seeing wood-fueled biomass plants claim a larger percentage of the national energy market.
Companies and individuals who own forest land are also asking to be heard regarding how resources from such lands can either be used (or protected, depending on the viewpoint) if this market grows.
The Pinchot Institute is a not-for-profit organization that says it is dedicated to "advancing sustainable forest management." In its Fall 2008 newsletter, Institute President V. Alaric Sample calls on the federal government to recognize the carbon sequestration value of managed forestry, particularly since "new technologies for producing electricity, process heat and advanced biofuels from wood hold significant promise for clean, efficient utilization of this renewable resource."
Sample also notes that while the recent Energy Independence and Security Act could provide a boost to cellulosic ethanol markets, "this policy emphasis on just one of several types of wood bioenergy has overshadowed others that may turn out to be better suited to circumstances in various forested regions of the U.S."
Advocating for wider uses, Sample writes, "If done with adequate foresight and planning, wood bioenergy can become an essential tool for reducing destructive, carbon-emitting wildfires." He adds, "Markets for wood bioenergy can become an important positive force for forest conservation and sustainable management on both private and public lands."
ONE WOOD-FUELED VISION
In a presentation at the "Energy from Biomass and Waste" event, held in Pittsburgh in October of 2008, Scott Miller of Price BIOstock offered one example of how such a biomass network might take shape.
In his presentation, entitled "The Price of Fuel: What Makes Biomass Sustainable?" Miller addressed the price points and volume factors that determine whether biomass energy makes economic sense, as well as describing a network or system of regional facilities.
The Price Cos. Inc., based in Monticello, Ark., provide wood and wood chips for sawmills and pulp and paper mills throughout the United States. The collection of companies has 21 mills, with 19 of those in the Southeastern United States, according to Miller.
The Southeast can be an ideal place for a network of small woody biomass plants, says Miller, because throughout much of the region the material is closer at hand than coal, and the region also contains many small and medium-sized towns that could satisfy a large percentage of their energy needs through biomass.
In terms of resource conservation, Miller noted that wood is a renewable resource thanks to managed forestry. And while the time cycle to grow trees is longer than to grow energy crops such as switchgrass, trees do not need to use fertilizers or irrigated water.
Emerging biomass-to-energy technologies such as gasification are being developed at commercial scale that are more efficient and environmentally cleaner at converting biomass waste streams into bio-power and bio-fuels. Miller listed construction and demolition materials, post-recycled materials, restaurant grease, hurricane forest knockdown, and flood debris as examples of landfilled waste that would not only be more "economically and environmentally sustainable" than using cultivated crops but would also clean up the environment and mitigate against greenhouse gas emissions from decay.
He recalled Hurricane Katrina in 2005 as just one example when the landfilling of large amounts of debris "broke [his] heart." Said Miller of storm debris, "We should make energy out of it," and he said that a network of biomass facilities would be a way to do that.
In Miller’s "biomass feedstock hierarchy," the base of a five-level pyramid is formed by waste—a combination of material that comes from forests, farms and urban generation sources.
He cited industrial residue and the clean-up of forests infested by beetles or other pests as other sources of feedstock that could be handled by a network of biomass facilities. Declared Miller, "The energy value chain could be cradle-to-cradle, just like recycling is."
THE STARTING GUN
Equipped To Take Part |
Greater use of wood products and wood debris as an energy source can be a boost not only for recyclers but also the equipment companies that supply them. Companies like West Salem Machinery (WSM), Salem, Ore., are creating systems designed for the application. WSM’s wood fiber preparation system is designed to convert green chips, sawdust and shavings into pellet fuel. According to the company, "The system handles up to 100 green tons per hour of fiber, and includes pre-screening and shredding/milling of material to an approximate one-half to three-quarter-inch-minus product size." The system consists of two WSM drag chain reclaims, a WSM belt conveyor with overhead self-cleaning permanent magnet, a WSM vibrating screen and a WSM 4272S swing hammer shredder/hammermill. Vecoplan LLC, Archdale, N.C., has installed more than 50 Refuse Derived Fuel Systems at locations such as cement manufacturing plants. According to the company, a Vecoplan RG62U shredder is the heart of the system. The shredder is used to reduce the size of post-industrial plastic and wood scrap to be used as fuel. Vecoplan designs, engineers, manufactures, and installs alternative fuel preparation systems for a variety of industries and applications, according to the company. In addition to the shredder, Vecoplan’s RDF system includes "complete conveying and material handling systems; screening and separation technologies; Fecon, based in Lebanon, Ohio, has introduced the Fecon Bio-Harvester, a machine it says "simultaneously fells, chips and collects small-diameter woody biomass." According to a Fecon news release, the Bio-Harvester "helps provide a non-agricultural renewable biomass energy supply that enhances forest management practices. It harvests fire-prone ladder fuel material, producing wood chips from previously unutilized biomass source. Wood chips can then be used to produce bio-energy via the generation of electricity or liquid fuel production." Contractors and recyclers who already handle land-clearing debris may find such systems useful as ways to source additional material if woody biomass markets heat up and put a strain on supply. Another U.S. manufacturer, Remus, Mich.-based Bandit Industries, has recently exported equipment to help produce biomass fuel of a slightly different variety. Several diesel-powered Beast Recyclers have been working in Poland processing grasses into biomass fuel for a year, according to a Bandit news release, and a new electric-powered Beast went into operation in November of 2008 to convert baled grasses into useable biomass fuel. Bandit’s dealership in Poland has sold machines that are grinding bales of straw, grass and hay. In one case, a 700-horsepower Model 3680 Beast is currently supplying grasses for a cellulose paper plant in Swiecie, Poland. The paper company uses the ground grassy material to fire a boiler that supplies steam and electricity to the plant. A power plant located in Opele, Poland, is using a 540-horsepower Model 3680 Beast Recycler to grind bales of grassy material that is then fed to the power plant. Should biomass feedstocks continue to play a larger role in the energy market, it is likely to provide opportunities for equipment makers who are accustomed to creating machines that work on the difficult applications and in tough environments that are customary in the recycling industry. |
An alliance of timber land owners and solid waste and recycling companies provides one possibility for a partnership to create a biomass energy network.
As energy prices escalated and as public sentiment gravitated toward a favorable view of alternative energies, however, some entrepreneurs and larger companies have decided not to wait.
A report released in 2008 detailed the growth of wood pellet markets in the United States, covering the period from 1997 to 2006.
As of the end of 2006, North America had more than 80 wood pellet manufacturers producing 2.3 million tons of pellets, according to the report from the International Energy Agency (IEA).
It remains to be seen to what extent that market will be boosted by volatile energy prices and any changes in U.S. energy policy.
According to the IEA report, The Energy Policy Act of 1992 provides incentives for "green" energy, with eligible facilities receiving payments of 1.5 cents per kilowatt hour for the first 10 years they produce energy.
Among the eligible facilities include those using wind, poultry waste and closed-loop biomass fuel sources. The Act was renewed in 2004 for another 10 years, and the list of eligible facility types expanded to include open-loop biomass, solar, municipal solid waste and geothermal energy plants.
One company that has been active in the wood fuel market is International Forest Products (IFP) of Foxborough, Mass. IFP, part of the Kraft Group of Companies, which bills itself as one of the largest traders of forest products commodities in the world. The company conducts business globally in 83 countries with offices in North America, Asia and Europe.
Recently, IFP was appointed as the sales agent for Geneva Wood Fuels, a company that is starting up its Strong, Maine, wood pellet facility in the first quarter of 2009. Geneva will be making wood pellets for the home-heating market.
The Geneva facility is being positioned by its operators as one that "will revitalize the timber community in and around Strong, Maine. The area has long been associated with forest products, and this plant, converting a renewable resource into alternative energy sources, is its natural evolution."
Recyclers of scrap wood can face limitations in this pellet market if other parts of the supply chain suspect painted wood and other contaminants are being mingled with clean wood.
Proper sourcing and processing of clean wood supplies, however, can help recyclers handling land-clearing debris, storm clean-up debris and other materials potentially tie in to this global market.
The IEA report describes wood pellet production this way:
"Wood pellets are usually made from dry, untreated, industrial wood waste such as sawdust, shavings or ground wood chips. This material under high pressure and temperature is compressed into small pellets, cylindrical in shape. As a source softwood (e.g. conifers, pines) and hardwood (e.g. oak) may be used. Wood pellets are manufactured at wood pellet mills (as called in North America) or wood pellet plants (as called in Europe). The manufacturing process is determined by the raw material but usually includes the following steps: reception of raw material, screening, grinding, drying, pelletizing, cooling, sifting and packaging."
In the United States, the Pellet Fuels Institute (PFI) established national standards for residential pellet fuel in 1995. The voluntary standard leaves fuel quality certification as the responsibility of the pellet manufacturer, according to the IEA report.
Two different fuel grades, premium and standard, were created. The primary difference between the two grades is in the inorganic ash content, with the presence of too much sodium (salt) being a key consideration. "Natural wood uncontaminated with salt will have less than 300 parts per million of water soluble sodium. Certain fuel made from plywood; particleboard, some agricultural residues, paper and other materials, and wood contaminated with salt may have elevated sodium levels," according to the IEA.
Thus, producers can use these materials but they should identify the sodium level and then label whether products made with such materials meet either the PFI standard or premium grade.
Additionally, pellet manufacturers "are asked to disclose various types of material (e.g. wood, paper, agricultural residues)" in their products.
FIRE EXTINGUISHERS
It is often regulations rather than voluntary standards that provide the constraints for recyclers.
A 2008 study prepared by consulting firm DSM Environmental, Windsor, Vt., for the Massachusetts Department of Environmental Protection expresses concerns about the future of commercial boiler fuel markets in New England.
With paper mills and saw mills facing an economic slump, demand is at least temporarily muted. Additionally, "According to Maine regulators, no new biomass boiler capacity is currently planned in Maine, due in part to political opposition to the existing combustion of waste wood from out-of-state sources," says the report.
It continues, "No waste wood combustion facilities will be developed in New Hampshire given the ban on combustion of waste wood in New Hampshire. DSM is not aware of any waste wood combustion facilities planned for Vermont, and the siting, permitting and construction of a facility in Vermont would take a minimum of three to five years given Vermont’s regulatory process."
Southern New England may prove more hospitable. "New biomass boilers have been proposed in Massachusetts and Rhode Island to take advantage of increased REC credits in Massachusetts. However, it will take a favorable ruling from the Massachusetts Department of Energy Resources on the use of waste wood as a qualifying biomass fuel for these to go forward," says the DSM report.
Gasification technology, such as that being pursued by Boston-based Ze-gen, could provide an outlet. In January, Ze-gen received a $20 million capital boost to help fund it’s first commercial-scale facility to convert C&D scrap materials into what it calls "synthesis gas" using gasification technology.
For all the opportunities that biomass fuel markets offer, strong advocacy at the federal level may be needed to overcome some of the current lids on demand.
Much like predicting the weather one year in advance, calculating just how heated biomass markets will become involves making a forecast that could prove to be more speculation than science.
The author is editor in chief of Construction & Demolition Recycling and can be contacted at btaylor@gie.net.
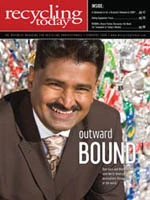
Explore the February 2009 Issue
Check out more from this issue and find your next story to read.
Latest from Recycling Today
- AF&PA report shows decrease in packaging paper shipments
- GreenMantra names new CEO
- Agilyx says Styrenyx technology reduces carbon footprint in styrene production
- SABIC’s Trucircle PE used for greenhouse roofing
- Hydro to add wire rod casthouse in Norway
- Hindalco to invest in copper, aluminum business in India
- Recycled steel price crosses $500 per ton threshold
- Smithers report looks at PCR plastic’s near-term prospects