Co-firing biomass and non-recyclable commercial, municipal and industrial waste with coal represents one of the nearest-term and lowest-cost options for CO2 reduction in the electrical power sector.
Using existing coal-fired plants to burn biomass and non-recyclables has proven to be a low-capital investment for utilities that is more environmentally friendly with less pollutant emissions compared to burning coal by itself. Co-firing has been demonstrated successfully in more than 150 installations worldwide.
With the number of co-firing plants continuing to increase, this trend could soon evolve into the preferred and most standard practice for reducing CO2 emissions at power plants.
Biomass, in the energy production industry, refers to living and recently dead biological material that can be used as fuel. Biomass may also include biodegradable material that can be burnt as fuel. Biomass is grown from a number of plants, including Miscanthus, switchgrass, hemp, wheat straw, corn, poplar, willow and sugarcane tops.
Biomass is part of the carbon cycle, where carbon from the atmosphere is converted into biological matter by photosynthesis. On decay or combustion, the carbon goes back into the atmosphere or soil. This happens over a relatively short time, and plant matter used as a fuel can be constantly replaced by planting for new growth. Therefore, a reasonably stable level of atmospheric carbon results from its use as a fuel.
Industrial, municipal and commercial non-recyclable (low-market-value) material includes paper, cardboard, packaging, industrial fiber materials and wood processing scrap. These materials, being carbon-based along with the biomass, when co-fired with coal can reduce the carbon dioxide (CO2) emissions from coal-fired power stations in direct proportion to the quantity of biomass consumed.
FUELING GROWTHThe main reason utilities are burning biomass and non-recyclable material is to generate electricity from renewable energy. Biomass and non-recyclables compete with saltwater, hydro, wind and other forms of renewable energy. One dry ton of biomass, for example, will generate approximately 1 megawatt of electricity. Co-firing with coal reaches a higher temperature and is more efficient, generating about 1.4 megawatts of electricity per ton of biomass.
"The cost per ton of biomass and non-recyclables is still higher than coal, however," says Tom Miles, president of TR Miles Technical Consultants Inc. (www.trmiles.com), an engineering firm specializing in power plant co-firing. "The final kilowatt cost is the fuel, what is actually delivered to the boiler. Most biomass is on the order of $70 per ton by the time it is delivered to the burner. That is a 7-cent-per-kilowatt-hour fuel cost. Coal is at roughly 5 cents per kilowatt-hour and cheaper energy than biomass. Coal prices have been steadily rising, however, gradually closing the gap, which is making co-firing with biomass and non-recyclables more attractive to plants."
Miles explains, "Comparatively, natural gas is more expensive than generating power from coal. It is about the same cost per kilowatt-hour as biomass. Wind, which at one time was in the vicinity of 3 cents per kilowatt hour, is now in the range of 8 cents per kilowatt-hour because many of the ideal sites have now been acquired. All of a sudden, co-firing coal with switchgrass, corn stalks, wood or non-recyclable waste looks pretty interesting to the utilities from an economic point of view."
He continues, "Dedicated biomass and non-recyclable waste plants are not the most cost-efficient option. If a utility wants to generate electricity from a renewable resource, it should look at co-burning that resource with coal, in an existing plant, as opposed to building a new plant that generates power entirely from biomass."
MAKING THE SWITCHOne power facility that has seriously embraced co-firing is Slough Heat and Power Ltd. in the United Kingdom, about 15 miles southeast of London. The power plant is a textbook example of the efficiencies attainable by introducing co-firing biomass and non-recyclable material into an existing coal-fired facility.
Slough Heat and Power was a dedicated coal-fired power station until 2001, when it began co-firing coal with biomass and non-recyclable waste. This change was prompted by increases in the price of coal and the desire to burn a sustainable fuel in the facility. The plant decided at the time to move toward becoming more of a green power station. Today, Slough Heat and Power is recognized as being the greenest power station in the U.K.
Slough Heat and Power supplies electricity, hot water and steam to local businesses and electricity to local residents. The plant is the U.K.’s largest dedicated biomass energy facility, with six boilers and six turbines that can operate on a variety of fuels. The plant uses wood and fiber fuel primarily, but it also can burn natural gas, coal and distillate. Natural gas and coal are now used in small amounts for boiler control purposes.
The facility includes two fluidized bed boilers that drive a 35-megawatt pass-out steam turbine. These are now fuelled with wood, having been converted from coal in 2001. The plant also includes one multi-fueled vibrating grate boiler that drives a 12-megawatt pass-out steam turbine. This is also fueled with wood and fiber fuel.
"We burn about 1,000 tons of coal a month, primarily for the chemistry," says John Watson, fuel manager with Slough Heat and Power Ltd. "It assists us with corrosion properties. The plant uses about 35,000 tons a month of wood chip fuel, which is both wood and biomass, used for the main part of the power station," he says. "We are at the moment about 87 percent green energy."
Watson continues, "Slough Heat and Power uses only clean, uncontaminated wood chips. Much of our wood is from local landscape companies and tree trimmers who perform work on woodlands, forests, parks and roadsides. We purchase chips made from branches, stems and other material, which has few, if any, other economic uses."
Watson adds, "The plant also sources uncontaminated wood from local sawmills, where chips are a by-product from sawing timber. Wood chips are also made from clean pallets, demolition wood, off-cuts, etc., and these are delivered to us."
The burning of the biomass and wood chips produces less sulfur, significantly less CO2 and less ash. Most of the plant’s ash is recycled and blended into road aggregates or used as fillers, as opposed to being put into a landfill.
Slough Heat and Power also operates an on-site subsidiary, Fibre Fuel Ltd., which processes non-recyclable commercial and industrial material into fuel cubes. Waste material is shredded and densified into small, odorless energy cubes. The cubes are then combusted to generate electricity for local businesses and residents. In essence, scrap material is turned into a renewable fuel to generate electricity. These scrap materials include mixed papers, magazines, junk mail, coated papers, laminates, adhesive labels, photographic paper, hygiene product rejects and pre-consumer packaging. The mix includes 15 percent plastic (excluding PVC), which is added to improve the caloric content.
The company processes approximately 8,000 tons of material per month, and 260 tons of fuel cubes are produced each day. The fuel cubes are approximately two-thirds the calorific value of coal. Thirteen tons of the energy product produces 12,000 kilowatts of electricity and 20,000 kilowatts of heat.
"We shred all of this waste material to a fraction of the size, down to 2 to 3 inches," says Watson. "We then run it through high-speed densification equipment to make fuel cubes. In size the cubes are either 1.5 inches by 1.25 inches by 3 inches long or 2.5 inches by 1.25 inches by 3 inches long. These then go directly to the boilers."
POWER CUBEDAt the heart of Fibre Fuel’s cubing is Warren Baerg Manufacturing’s model 250 cubers, which can produce 6 to 8 tons of cubes per hour each, depending on the material and die selection, and can process a wide range of forage and other non-recyclable materials—whether it is biomass, municipal waste or industrial waste—turning it into a cube and ultimately fuel.
The resulting fuel cubes—Cubed Energy—are 1.25 inches or 1 inch square and break off in lengths of 1 inch to 3 inches, depending on the materials used and the components and adjustments selected. Because the characteristics of the fuel cubes are similar to those of coal or hog fuel, they can be used in most industrial boilers along with other fuels.
The range of cubing systems the company manufactures can convert many loose, low-density materials into a dense alternative fuel that is economical to transport and efficient to burn. Non-recyclable papers, newsprint, poly-coated or waxed cardboard, pre-consumer industrial fiber scrap, wood processing and manufacturing scrap and post-consumer combustible fiber scrap can all be processed through the company’s Model 250 Cubers. Secondary additives, such as paper mill short fibers (sludge), coal fines and PET coke can be added to form a blended fuel.
"We are currently running six Warren & Baerg cubers, but have the ability to site eight," continues Watson. "We don’t just feed the raw paper or cardboard directly into the boiler because of two reasons: One, it needs to be decontaminated because it is a waste product; it contains undesirables that have to be removed before it can be cubed. And, two, because the material cannot go in to the boiler in its raw form, it has to be made to a specific specification of cubing for optimized burning," Watson says.
"The contaminants are removed with two systems," he explains. "First, metals, ceramics, aggregates and glass are removed with an air-knife, which introduces an air flow onto the material, blowing the light material forward and allowing the heavy materials to fall out as rejects. Second, with the ferrous metals, we have a whole series of electromagnets. On the nonferrous metals, we have eddy current separators, which work opposite to a magnet, repelling metals like aluminum and brass," Watson says.
The plant then uses a series of conveyors and screw augers to feed the processed material into the cubing equipment.
Fibre Fuel exercises different options for the fuel once it has been cubed. The cubes can be feed directly into the boiler, put into a storage bunker that can accommodate 300 tons of cubes or fed into a truck and transported around the site for alternative use or additional storage.
For Slough Heat and Power, converting to co-firing diverts roughly 250,000 tons of carbon dioxide from being emitted into the atmosphere annually. Also, 100,000 tons of material is kept from being deposited in landfills.
The first tests with co-firing wood and coal were conducted back in 1979. In the early 1980s, co-firing became popular, then waned. The process again gained popularity in the early 1990s and waned. Now, it appears co-firing is back again and has achieved a new level of popularity with power utilities. Recent technology upgrades for handling biomass and non-recyclable material can only add to this momentum and hopefully will help provide the needed efficiencies to prove co-firing methodology sustainable.
This article was submitted on behalf of Warren & Baerg Manufacturing Inc., Dinuba, Calif., online at www.warrenbaerg.com. It originally ran in the March/April issue of Recycling Today’s sister publication Construction & Demolition Recycling.
USDA, DOE Fund Biomass Research Projects |
U.S. Department of Agriculture (USDA) Secretary Ed Schafer and U.S. Department of Energy (DOE) Secretary Samuel Bodman have announced that, combined, USDA and DOE will invest up to $18.4 million, over three years, for 21 biomass research and development and demonstration projects. These projects specifically aim to address critical barriers to making production of biomass more efficient and cost-effective. "These grants help fund the innovative research needed to develop technologies and systems that lead to the production of bio-based products and biofuels," Schafer said at the Washington International Renewable Energy Conference 2008 in March. "Funding new technologies will help make biofuels competitive with fossil fuels in the commercial market, putting America on the path of reducing its dependence on foreign oil." Bodman added, "Continued investments in biomass are critical to furthering the President’s goal of making available clean, abundant and domestically produced bio- Funding for these projects will be provided through the Biomass Research and Development Initiative, a joint USDA-DOE effort established in 2000 to develop the next generation of clean, bio-based technologies. Grant recipients are required to raise a minimum of 20 percent matching funds for R&D projects and 50 percent matching funds for demonstration projects. Of the $18.5 million in grants, USDA will provide up to $13 million, and DOE will provide up to $5 million. Grants are subject to negotiation and will begin immediately, and funding is subject to appropriations from Congress. |
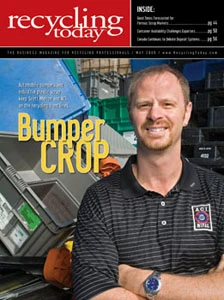
Explore the May 2008 Issue
Check out more from this issue and find your next story to read.
Latest from Recycling Today
- Nucor receives West Virginia funding assist
- Ferrous market ends 2024 in familiar rut
- Aqua Metals secures $1.5M loan, reports operational strides
- AF&PA urges veto of NY bill
- Aluminum Association includes recycling among 2025 policy priorities
- AISI applauds waterways spending bill
- Lux Research questions hydrogen’s transportation role
- Sonoco selling thermoformed, flexible packaging business to Toppan for $1.8B