

The Newell name has become synonymous with metal shredding over the course of more than seven decades, with the family’s namesake shredders increasing in size and scope while earning a global reputation for processing efficiency.
But even as shredders produced by El Paso, Texas-based Newell Recycling Equipment LLC (NRE) have been installed at facilities around the world to process ferrous and nonferrous scrap, there always has been room to improve their design.

Most recently, the use of altered bottom grates in Newell shredders has become a cost-effective tool for operators looking to densify their scrap and increase their total tons processed per hour.
“Since we run so many tons in our plants, and we’re running 1 million tons a year in Newell family-owned plants, nobody had more motivation to try and improve things,” says Scott Newell, chairman and CEO of NRE.
An a-ha moment
Newell says the change in grate design was a long time coming—mostly because this component simply had been overlooked.
“We just didn’t pay attention to it,” he says. “Nobody ever thought about it. All the shredders were working well.”
Newell admits to a mistake he made early in the formation of the new grates: creating slotted grate holes that were intended to get material out easier. The holes were slanted 27 degrees toward the discharge side of the shredder and did allow for material to pass through more easily, but at a much higher velocity, causing pieces to bounce out of the shredder and creating more pokers—long, thin pieces of metal that can damage equipment.
About three years ago, while standing in the feed shoot of a shredder and looking down, Newell could see through the grates to the under-shredder oscillator and discovered why all the high-velocity material was leaving the machine. He redesigned the grates so the holes would be 90 degrees, preventing material from bouncing out of the shredder. “Once you get your spotlight of attention on it, you go, ‘Oh my goodness, it’s better to do it this way,’” he says.
“After I designed these, I hit myself in the head and said, ‘How could I be this stupid for the previous 62 years,’” Newell says with a laugh.
Winds of change

The grate redesign was sparked by a request from one of NRE’s China-based clients. Newell says his company has nearly 70 machines operating in that country, including 20 with more than 10,000 horsepower capable of processing more than 1 million tons per year.
He notes there’s been a movement in China for scrap with higher density, so he went back and looked into the grates.
“I pulled the drawings up on the computer, looked at them and just said immediately, ‘This is stupid,’” he says. “The grate holes are facing the wrong direction. If we slot them so that the hammer passes across the narrow part of the slot, you get an effectively smaller grate, but you can still have more open space. We designed those and made higher-density scrap in China. It worked immediately.”
In essence, by changing the slots’ direction and putting one slot under each hammer pattern and making them wider, Newell found he could increase the total amount of open space in the bottom basket of grates from the anvil to the midsection. The typical range is between 23 percent and 26 percent open space, depending on a shredder’s size, but the new design reached between 33 percent and 36 percent open space with smaller holes.
SA Recycling, headquartered in Orange, California, was one of Newell’s first U.S. customers. The grates quickly made a believer out of company CEO George Adams, who has been integrating them into SA facilities for the past two years. In all, SA operates more than two dozen auto shredders.
“They take up more area than our normal grates, but they have smaller holes,” Adams says. “We’ve been finding it gives us better production but also denser scrap.
“In the past, when we put smaller holes in the grate, then you’d get less production,” he adds. “These are smaller holes, but there’s more of them, and, so, because of the way they’re staggered, we’re finding that we’re still getting the production, but we’re getting denser scrap. We’ve found a lot of success with these grates, and I’m in the process of changing over all my grates.”
Adams notes the changeover of bottom grates has led to better nonferrous recovery, in particular.
“They’re definitely a great idea,” he says. “It’s just logical when you think about it. It’s more open spaces, and the more open spaces you have in the grate, then the more opportunity you have for the scrap to get out.
“Overall, we’re getting denser scrap and we’re not losing tons per hour, and I think that’s really the biggest thing,” Adams continues. “Denser scrap is easier to sell, and you get more nonferrous recovery out of it.”
The grates were first tested at SA’s Anaheim location, and Adams says that facility is on its third set of grates, though the time between grate replacements can vary depending on what material is being fed to the shredder. “If you shred 3,000 tons a month, it’s different than if you shred 20,000 tons a month,” he adds. If you’re shredding more cars, or more tin, your production is going to change.”
Anaheim facility Shredder Manager Omar Bravo says his shredder’s grates get replaced every 160,000 tons, or every five to six months.
“We’ve found a lot of success with these grates, and I’m in the process of changing over all my grates.” – George Adams, CEO, SA Recycling
Getting results
Once NRE’s new grates were installed in his 124-inch shredder, Bravo says he noticed a difference in output right away. The grates themselves measure about 122 inches in length, with openings measuring roughly 4 inches by 7 ½ inches and 5 inches by 7 ½ inches.
“With these new grates, because of the size, we’re very consistent on the tons per hour,” Bravo says. “On the old design, when we’d put in new grates, we used to do probably 150, 160 tons per hour of shredder output. Now, we’re doing 190, 200 tons per hour and that’s consistent.”
He adds that, in addition to the elimination of pokers, the scrap’s density improves and looks much cleaner because it’s coming out smaller and the shredder is consistently working more efficiently. “Your zorba, you’re going to have a smaller material as you’re breaking the steel away from the aluminum, which is a benefit for us,” Bravo says. “You’re also going to see a higher concentration of copper fines. So, you recover more of the fine copper in the process. … Overall, we’ve seen a big difference.”
As the product has made its way around the world, Newell has heard success stories elsewhere.
“Recently I was in Denmark, and we have a machine there that’s 24 years old. They changed to these grates about a year ago, and they’re astounded,” Newell says. “It’s one of the single biggest improvements they’ve ever made to their shredder plant. That’s a big machine there, and they picked up 30 tons per hour with higher density and no other costs. When you look at that in terms of economic value, that’s amazing.
“You get the added bonus that since we started supporting two rows of holes with one support structure underneath it, a set of grates in a 124 shredder costs about $7,000 less with the new design than with the old design,” he adds. “All around it’s been just an amazing improvement. I’m really proud of it.”
The new grate design contributes to electricity savings, according to Newell, who says the grates allow operators to shred to different densities without using as many kilowatt hours.
“Let’s say you want to go from 1.1 density to 1.2 in a 124 machine,” he says. “In a 124 [shredder] it’s 13 kilowatt hours of electricity to get to 1.1. If you want to go to 1.4, you’d use 16 kilowatt hours. But if you go to 1.4 density with these grates, all of a sudden it’s only half of that distance. Instead of going 13 to 16 [kilowatt hours], you’d go to 14 ½ or so. So there’s some real savings involved in doing it this way.”

Spreading the word
Much like NRE’s shredder business in general, the new grate design has spread across the globe.
Newell estimates the grates will be used in 70 machines in China alone, and, including installations in the U.S., Denmark, the Netherlands, Germany and South Africa, nearly 100 shredders will incorporate them by the end of this year.
Despite their increasing popularity, Newell has decided not to patent them. Instead, he’s adopted the philosophy that anything helping the shredding process also helps NRE.
“Our competitors are starting to hear about it,” he says. “But, still, if you don’t know exactly why we did it, then it’s still hard to get that guy who’s an engineer sitting at a computer screen [to understand]. You just don’t see all these things unless you’ve been an operator or you spend time at your shredder.
“We think everybody, including our competitors, will be doing it this way [eventually],” Newell continues.
Additionally, he says, “It’s pretty hard to patent; there’s just too many ways around it. So, I thought my best bet was to go ahead and sell them to everyone I can and let them know that Newell continues to be the innovator.”
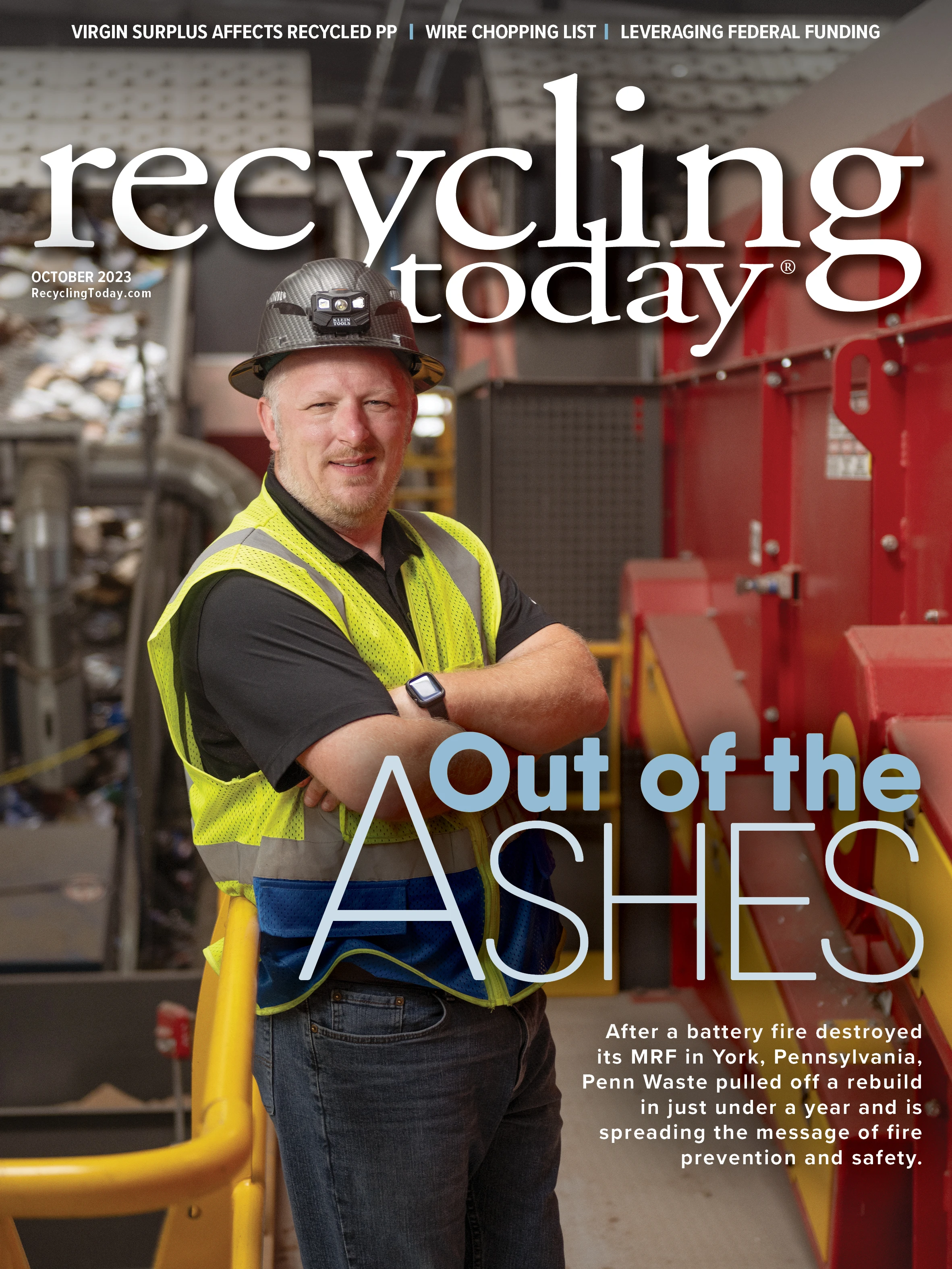
Explore the October 2023 Issue
Check out more from this issue and find your next story to read.
Latest from Recycling Today
- The push for more supply
- ReMA PSI Chapter adds 7 members
- Joe Ursuy elected to NWRA Hall of Fame
- RRS adds to ownership team
- S3 Recycling Solutions acquires Electronics Recycling Solutions
- Nextek, Coveris to recycle food-grade plastic film
- Recyclekaro expands recycling capacity
- USTR hears comments on port fee proposal