Scrap metal is used for making new steel at mills and minimills across the country, but there is another use for the material that is quietly eating up thousands of tons of shredded scrap metal (frag) a day. That other source is the foundry. The Ford Motor Company, headquartered in Dearborn, Mich., and with plants throughout North America and the world, is a major user of frag at its foundries. One of its largest plants is in Cleveland, directly across from that city’s airport.
CUPOLA HEAT
The Cleveland Ford foundry is called a "grey iron" foundry because it produces ductile iron. The plant operates five Cupula-type furnaces that are basically large stacks filled with layers of coke, lime stone and scrap metal. Each furnace is capable of producing 70 tons of molten metal per hour, and the plant typically produces 2,000 tons per day. Most of that comes from fresh steel scrap, and most of the scrap is in the form of frag.
"We have about a 54 percent yield rate," says Terry Clark, resident materials engineer at the plant. "By the nature of casting, a lot of the metal is removed and trimmed from the final product, plus there is some spillage. We just collect it all and put it back in the furnace."
Besides the frag and the scrap generated at the foundry, the plant uses cut plate and blast furnace runout from steel mill furnaces. But it is the frag that Ford really likes. "We prefer the frag," says Clark, " because it has most of the alloys in it that we need. Some operations don’t like frag because of those alloy impurities, but we need it. It saves us from having to add the alloys ourselves."
In recent years, though, the foundry has had to compete for scrap metal because of all the new minimills coming on line.
"The competition is good for the scrap industry and industry in general, but it has increased our costs because prices have gone up," says Clark. "However, it is still more cost-effective than using pig iron."
Clark claims that at times, the foundry has had to tap sources as far away as Florida for frag. "Naturally, the farther away we go, the more expensive the scrap becomes because of the transportation costs," he says.
Another change that is affecting the foundry is the push towards lighter vehicles. Because of that, more engine parts are being cast out of aluminum and even composite and plastic materials.
"We are not at the capacity that this foundry is capable of, and I am not sure whether we will ever return to full capacity in the future, " says Clark. Occasionally, the plant has even closed for several periods at a time because of reduced demand.
SUPPLYING SCRAP
Currently, the foundry gets much of its material from a Luria Bros. scrap and processing yard directly next to the foundry, and from Atlas-Lederer and Atlas Iron Processors, both in the Cleveland area.
However, it is the Luria Bros. facility that is the foundry’s biggest supplier.
"We like having the Luria facility next door," says Clark, "because we can have better quality control and the transportation costs are minimized. There is a lot of value in that."
The Luria Bros. yard operates a heavy-duty shredder to keep up with the demand. The shredder is close to the railroad tracks and the frag can be loaded directly from the shredder to gondola cars.
In addition, a long row of frag is piled in the yard as a reserve.
Currently, most of the scrap and frag comes into the foundry on rail in gondola cars, but the recent shortage of cars concerns Ford officials, so these officials have taken the matter into their own hands.
"We have been worried about the gondola car shortage and do not want that to disrupt our flow of frag into the foundry, so we will be leasing 10 gondola cars so that the scrap yards will be assured of transportation."
The cars will be leased for a two-year period. Clark says the plant was going to set up its own trucking program to haul the scrap, but found that the initial investment was excessive and not worth the effort.
"Leasing the gondola cars is better," he says.
The foundry can accept scrap metal as big as 2 feet diagonally, but it cannot have any hooks that would tangle it in the charging system.
Engine blocks, heads, flywheels, bearing caps, and exhaust and intake manifolds are produced at the foundry.
Many of the parts go next door to a Ford engine machining and assembly plant, and the rest go to other Ford engine plants throughout the Midwest and Canada.
The author is managing editor of Recycling Today.
Foundry Basics |
There are several types of foundries in the United States, but the majority consist of iron, steel and aluminum. Many of the larger ones are operated by the automakers, but there are some large independent ones, too, like American Cast Iron Pipe Co., Birmingham, Ala., that makes sewer grates and pipe. ACIPCO operates the largest pipe foundry in the world with 55 acres of manufacturing under one roof. The American Foundrymen’s Society of America, also based in Chicago, says that there are about 3,000 foundries in the U.S, with the majority being iron, steel and aluminum. Total capacity of the foundries is 17.5 million tons of castings, with iron constituting 12.5 million tons, aluminum 2.1 million tons and steel 1.5 million tons. The majority of that tonnage is derived from scrap material. Scrap processors interested in finding out more about foundries can call AFSA at (708) 824-0181, The Steel Founders Society of America, Chicago at (708) 299-9160, the Investment Casting Institute at (214) 368-8896, or the Non-Ferrous Founders Society at (708) 299-0950. |
Get curated news on YOUR industry.
Enter your email to receive our newsletters.
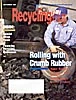
Explore the September 1995 Issue
Check out more from this issue and find your next story to read.
Latest from Recycling Today
- Altilium produces EV battery cells using recycled materials
- Brightmark enters subsidiaries of Indiana recycling facility into Chapter 11
- Freepoint Eco-Systems receives $50M loan for plastics recycling facility
- PET thermoform recycling the focus of new NAPCOR white paper
- Steel Dynamics cites favorable conditions in Q1
- Hydro starts up construction in Spain
- Green Cubes unveils forklift battery line
- Rebar association points to trade turmoil