The article that started this series last month looked at many different kinds of "recycling" that can occur with each individual electronics recycler. Unlike the recycling of, say, aluminum cans, which generally move from collection point to broker to smelter, electronics and their components can literally travel to several destinations before, or if ever, parts of the device reach a smelter.
The process of electronics recycling—from the "reuse" of equipment and components to the recycling process involved in the separation of metals, plastics and glass—is very complex. The methods for getting those products to a state where they can either be reused, refined or used as sources for conserving energy resources can be expensive and complicated.
THE CALIFORNIA ALPHABET. As the previous article did, this one will look at three pieces of "hardware," a computer’s central processing unit (CPU), a monitor (with a cathode ray tube or CRT device) and a printer. These pieces of equipment contain most of the constituent components (metals, plastics and glass) as well as the hazardous materials found in most electronic scrap today.
The first step occurs when an individual or company has unplugged an old computer, or 2,000 of them, and has called the e-recycling company.
California’s new recycling law has loosely defined a few categories of electronics "recyclers"—designated A through D. The staff of the California Integrated Waste Board (CIWMB) and Department of Toxic Substance Control (DTSC) did an honorable job of working with hundreds of biased recyclers to come up with as agreeable a definition as they could get from "the experts."
An "A" recycler is a company that basically does very little disassembly and is using nothing more than a screwdriver to get to other workable parts that can be sold or recycled.
THE REUSE SHORT LIST |
Reusable items handled by electronics recyclers most commonly consist of the following devices and components: Computers Primarily — Hard drive, memory module, processor or DVD or CD device Secondarily — Floppy drives, power supply Printers/Fax Machines Toner cartridge, ink cartridge, paper tray, other smaller items Monitors/ CRT Devices One can use the CRT (cathode ray tube), but generally and practically, the monitor is left intact before it is shipped to a facility that will use only the CRT. Otherwise it is prohibitively expensive to remove the CRT, properly package it and ship it overseas. |
A "D" recycler is generally a fully permitted disassembly, shredding and smelting operation. There are many variations, but below are three basic categories of "recyclers" that will most often be encountered.
One type of "recycler" you may encounter is very similar to the person who recycles aluminum cans by picking them out of the garbage (or your garage, closet, storage room, warehouse, as the case may be). These recyclers package the electronics and ship, or deliver, them to whomever pays them the most money. They are simply brokering materials to processing facilities or even to another broker.
Another type of electronics recycler, an "A-Processor" by California’s standards, has designated its services mainly for the collection of equipment that can be refurbished and resold. Dismantling is done on a limited basis, only to access valuable usable components from equipment that has no reuse value as a complete unit. An old computer that has a good hard drive device that can be removed and reused is an example. (Note: Recyclers must always watch that labor costs to remove, clean and test certain components do not exceed the recoverable value of the components.)
OEMs and other specialized facilities "harvest" much more from equipment because of their specific capabilities and requirements. A company that repairs and refurbishes newer monitors will in fact remove plastic housings, bases, circuit boards and other items as potential replacements, perhaps as a part of an OEM repair/replacement program. A company that specializes in one particular type of computer will harvest buttons, bezels, wiring harnesses and other items for use as replacements on warranty returns. However these are distinctly specialized cases where specific products less than five years old are their core business, and they do hundreds of the exact same units.
SIMS GROUP ACQUIRES E-SCRAP RECYCLER |
The Sims Group, based in Australia, has acquired the Mirec Group, one of Europe’s largest electronics recyclers. Mirec, headquartered in Holland, operates throughout the Benelux countries, Sweden and the U.K. It recovers and recycles electrical, electronic and computer-related equipment and also operates a plant dedicated to the recycling of cathode ray tubes from TVs and computer monitors. Mirec sources material through contracts with government- and manufacturer-sponsored programs already established in the Benelux countries and in Scandinavia in compliance with the EU’s Waste and Electronic Equipment (WEEE) Directive. "The acquisition of the Mirec Group elevates our Recycling Solutions Division to the status of a meaningful earnings contributor for Sims," Jeremy Sutcliffe, Sims's chief executive, says. He says the acquisition offers a strong platform for growth in the U.K. when the WEEE Directive is introduced into local legislation. Sutcliffe says Sims’s knowledge of WEEE goods recycling "will be critical in assisting governments and manufacturers in Australia and elsewhere to introduce appropriate legislation and solutions for the ever-increasing environmental problem of end-of-life electronic and electrical manufactured goods." |
Many companies will have leftover parts and pieces collected in bulk bins, such as Gaylord boxes. The leftover items will have residual plastics and metals value and can be picked up by a broker or by a recycler defined in California as a "B-Processor."
In California, a "B-Processor" recycles electronics equipment for the recovery of usable electronics and components. The company may handle very large contracts with companies for the recovery of excess and obsolete inventories and may provide for end-of-lease equipment management and other large-volume equipment acquisitions primarily for reuse recovery. This company may also "harvest" usable components from equipment that may be damaged "New Returns." These items can be reinstalled into other repairable returns. Today’s OEM is quickly and effectively seeing the value in creating this kind of program either within its organization or through partnerships.
"C-Processors," according to the classification system in place in California, can offer the services detailed above and additionally may have a shredder, hammer mill or some other sort of destruction equipment. They do not carry hazardous materials treatment permits or other permits to meet smelting requirements.
A "D-Processor" may perform some of the tasks above as well as meet the environmental standards necessary to offer smelting.
DOING THE MATH. Depending on labor costs and the value of the component, it can be more equitable to remove components for reuse in addition to being an environmentally responsible practice.
This recovery practice is managed on a fine economic value line, but these areas of added recovery and reuse or recycling are an integral part of any recycler’s business model.
However, the "D-Processor’s" primary and original business model may be that of a secondary or primary smelter. In layman’s terms, a secondary smelter is a company that collects, shreds and melts a sample of the bulk materials to assess the recoverable metals content for payment. The material is then sent to a specific primary smelter for the recovery of the "primary" metals.
A "D-Processor" is likely to be fully permitted to transfer, store, treat and properly dispose of hazardous wastes (TSDF) and will retain required local, state and federal permits to do specific work where byproducts of the process might contaminate air, water, land and/or persons as a result.
This company may also specialize in treating materials such as lead and may even specialize in recovering the lead from CRT glass, recycling it for new product uses. This company will undoubtedly carry several specific insurance policies—workers compensation, liability and environmental insurance that ensures effective cost coverage should an accident occur at its facility or at a downstream processing facility where financial assistance is needed in the cleanup. The company is "for-profit" and impressive in its size and in the amount of equipment needed to provide these services, care for its employees and protect the environment.
RAW MATERIALS MARKETS. So, here’s the fun part—or certainly the part that most interests traditional recyclers. After all the good components have been removed and harvested or the equipment is determined to be too old to make this worthwhile, the process of liberating the metals, glass and plastics for recycling begins.
Hazardous materials, such as batteries (especially lithium) and older products containing beryllium, must be managed differently and must be removed from most shredding and smelting processes.
THE CRT BREAKDOWN |
While cathode-ray-tube (CRT) devices do not generally disassemble easily, they come apart in fairly big pieces that fall into these categories: plastic – housing, base; CRT – without yoke—clean glass, leaded glass, iron, some phosphorous; iron – protective insulation, band on the glass, electron gun; copper – yoke, wiring and circuit board; aluminum – heat sinks, capacitors; and stainless steel – screws. Disassembly must be done with extreme care. Basically, a very large bubble of glass is under vacuum pressure, which, if improperly handled, can implode, sending glass, leaded glass and phosphorous flying. Smelters will shred CRTs separately and magnetically separate the iron shroud within. The silica in the glass is used as flux in the smelting furnace. A lead smelter will recover the lead and use it in products. Smelters will also shred the copper bearing items—circuit boards, wiring and yokes—to begin the reduction process required for smelting. The iron and plastic will be sent to recycling and smelting facilities, as will other materials that can be separated effectively prior to shipment to the smelter. Technologies exist to separate leaded glass from clean panel glass in a CRT. Cutting the funnel glass (leaded) away from the panel glass (clean), can reduce the expensive treatment of leaded glass by more than one-third of the weight and enables quick removal of the iron shroud within and quick cleaning of the phosphorous from the panel glass. However, the cost involved has prohibited its widespread use in the United States. |
The computer shreds quite easily. Steel is the largest single material present. When a company runs a shredding operation, the materials are screened so as to break them up into pieces small enough to separate iron, copper, aluminum and plastic from each other, but large enough to keep from having to over-shred.
Once the materials exit the shredding mechanism, they pass along vibrating conveyors that help to evenly disperse items for separation. The first separation is for iron using a mechanical magnet. The resulting material is often shredded two or three more times to reduce and to separate remaining metals and plastics by means of eddy currents, sand systems, floatation systems and other methods.
A computer generally contains a lot of steel. A select few manufacturers use aluminum for the case. A good portion of aluminum is contained in the hard drive and in heat sinks on the circuit board. The remaining material containing the circuit board and what’s left of the power supply is generally shredded to a much smaller particle size before being run through an eddy current or through other separation methods that help liberate the organics (such as plastics and fiberglass), from the copper, stainless steel and aluminum. Some OEMs today seek to manufacture their products for more efficient separation in the recycling process.
Printers, fax machines, scanners and similar equipment are not as conducive to shredding. A lot of plastic is mixed with metal and rubber. There is stainless steel and iron. And, there is glass, which for the most part is "clean," or should I say, unleaded. The biggest problem is the ink and toner that cannot be completely removed from many of the units. This substance can make quite a mess. Even disassembly is potentially a messy process.
Monitors, or CRT devices, helped spur many of the electronics recycling requirements in the first place. They have created the biggest challenge in recycling history and environmental stewardship.
In the "old days," the entire monitor was shredded and sent to a primary smelter. The entire glass portion was used as a flux in the smelting operation (which is a good thing, by the way), the plastics were incinerated as a BTU source, thereby reducing the requirement for natural gas or coal to bring the furnace up to temperature, and the remaining metals were collected and separated for use in new products. The glass, by the way, is able to be used for quite some time as a flux, until it is then disposed of as a slag.
However, the handling of lead became a prominent issue. The old saying, "Get the lead out," was not so old anymore. Primary smelters were now pressured to keep leaded glass from the slag mix and that began to reduce the ability for recyclers to send leaded glass there.
Today, most monitors that do not work or do not contain a salvageable CRT are disassembled to begin the recycling process. In this process, larger components are recycled differently depending on which material makes up the largest percentage by weight or volume.
Taken from A to Z (or perhaps, A to D in California), electronics recycling can offer terrific opportunities for individuals to be a part of the recycling process without actually having to do all of it. Like other forms of recycling, it offers the ability to use our minds and to create technology that improves the products, making them more recyclable and environmentally friendly, and to create technology that enables us to create new methods of recycling.
Nothing in this article should be considered "written in stone." It is filled with possibilities, generalities and "maybes" that are not necessarily all the exact processes involved in every facility.
Many recyclers fit somewhere in between all of these aforementioned examples, performing a number of similar operations or none of them.
I am an electronics recycler by trade, but as a private citizen I recycle glass, metals and plastics, and compost and perform some methods of re-use and reduction as a form of recycling, like re-using grocery bags or putting all my vegetables in one bag instead of six to reduce the need to use as many bags.
In most of these cases (except for composting), my family and I are simply amassing items, separating them and sending them to places where I am "assuming" they are being recycled.
Many people involved in electronics recycling are at that same level—they do not see the end picture.
The final part of this series will review the economic, ethical and environmental issues that sway the decision-making processes in electronics recycling. After all, someone said to me: "Don’t kid yourself, Tom, it’s all about money." Is it?
The author is vice president and general manager of United Datatech/ECS Refining, Santa Clara, Calif. He has been an active stakeholder helping the California Integrated Waste Management Board and the Department of Toxic Substance Control implement the state’s Electronics Recycling Law, known as SB20.
Get curated news on YOUR industry.
Enter your email to receive our newsletters.
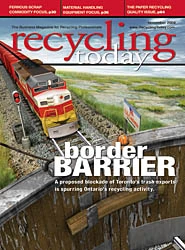
Explore the November 2004 Issue
Check out more from this issue and find your next story to read.
Latest from Recycling Today
- ReMA opposes European efforts seeking export restrictions for recyclables
- Fresh Perspective: Raj Bagaria
- Saica announces plans for second US site
- Update: Novelis produces first aluminum coil made fully from recycled end-of-life automotive scrap
- Aimplas doubles online course offerings
- Radius to be acquired by Toyota subsidiary
- Algoma EAF to start in April
- Erema sees strong demand for high-volume PET systems