
That kayak you rented last summer at the lake might be one of the products that contains recycled linear low-density polyethylene (LLDPE), and Trex Co., Winchester, Virginia, has positioned itself to be able to supply manufacturers of such products with recycled LLDPE pellets.
Trex has long been known for its lumber, decking and railing products manufactured from a blend of 95 percent recycled wood and plastic film. The company consumes recycled LLDPE pellets to develop its products.
In 2010, Trex found itself accumulating a growing surplus of material beyond what the company could use in its core line of outdoor living products. This available excess challenged Dave Heglas, senior director of material resources at Trex, to come up with alternate ways to use the surplus.
MEETING THE CHALLENGE
Leveraging the company’s best-in-class recycling and extrusion capabilities and using equipment downtime to experiment with and test different solutions, Heglas and his team developed LLDPE pellets ideal for use in a variety of products, from bags to flexible tubing and molded plastics, such as bins, totes and even kayaks, he says.
“Turning Trex from a company using recycled plastic into a plastic recycler was something that made perfect strategic sense,” Heglas says.
“We were collecting way more than we needed or could ever use in our deck boards, so we began selling off some of our inventory to manufacturers in other industries,” he adds.
Among those manufacturers were small companies that Trex contracted with to produce plastic pellets. Over time, it occurred to Heglas that Trex could make these pellets in-house rather than outsourcing the job to third parties. With a decade of pellet-producing experience, the company says it capitalized on its in-house expertise and expanded capabilities to produce pellets for additional industries and markets.
EXPANDING THE SCOPE
LLDPE is commonly used in film applications, such as food and nonfood packaging and shrink and stretch film. Typically, this material is recycled into garbage bags, industrial wraps and the like, as well as into Trex’s composite lumber.
While these applications remain the primary uses for recycled LLDPE, other uses are coming, Heglas says. “We are a pathfinder in this arena,” he adds.
One challenge Trex faces in expanding the use of recycled LLDPE pellets is changing the mindset of manufacturers who insist they require a recycled pellet that is identical to the virgin materials they now use. “That is not cost-effective,” Heglas says.
While recycled LLDPE may not fit the rigid specification for virgin material, that does not mean it is not a quality product. “We are supplying consistent, recycled LLDPE pellets,” Heglas says of Trex. “Now we need the other half—users who want to incorporate these materials.”
Trex’s LLDPE pellets are made primarily from packaging material, such as stretch wrap collected from distributors.
Trex is targeting off-spec and wide-spec applications for its recycled pellet. If successful, the company says its new initiative could open the door to greatly increase recycling of LLDPE.

Traditional recycling operations produce a mixed color product that combines various densities, Heglas says. Few manufacturers are looking for such a raw material. Trex’s goal is to produce a recycled pellet that meets the requirements of specific applications that use LLDPE, he says.
“We see a lot of opportunities in film, molding and extrusion applications,” Heglas adds. “In two to three years, we’d hope there will be a lot more incorporation of this material so products have higher recycled content.”
Among other possible applications for Trex’s recycled LLDPE pellets are drip irrigation tape, blown film, trash bags, construction or agricultural film, rotational molded trash bins and totes and extruded applications, such as tubing and garden products.
A CONSISTENT PRODUCT
After extensive research, Trex says it has developed a product with a consistent melt index, color and density, which is available in large quantities though it is made from recycled feedstock.
“Variability was one of the challenges when we were purchasing material on the market,” Heglas says. When the company realized it could produce a consistent product, Trex knew it had a golden opportunity to get into this market.
Heglas, a chemical engineer with a background in rocket science and missile design, joined Trex in 1996 as an engineer responsible for the raw materials and plastic processing side of the business. In 2004, he formalized the company’s recycling operations, which has now evolved into a company within the company.
A Penn State graduate, Heglas is a founding member of the American Chemistry Council’s Flexible Film Recycling Group. He is active with the Institute of Scrap Recycling Industries (ISRI) Film Recycling Group and with the Association of Plastic Recyclers (APR), where he has participated on the association’s board of directors.
Under Heglas’ direction, Trex actively solicits, collects and purchases postconsumer and commercial polyethylene (PE) film from manufacturers, retailers, advocacy groups and eco-minded individuals across the country. Today, he says, Trex is one of the largest—if not the largest—recycler of postconsumer and postcommercial PE film in the U.S.
“We need pull-through from the end user to say they will use recycled content in their products.” – Dave Heglas, Trex
The company’s LLDPE recycling operation is separate from its composite lumber manufacturing operation. At the moment, only Trex’s Winchester plant is producing LLDPE pellets. This operation was chosen mainly because the facility is close to many generators and consumers on the East Coast. Down the road, depending on how the business grows, Trex may expand the process to other areas of the country, Heglas says.
“It falls in with the company’s core competencies of collecting polyethylene scrap films that we’ve been doing for 20-plus years,” he says of the recycled LLDPE production operation, adding that by producing recycled pellets of a consistent quality in large quantities, Trex can grow applications for this product.
Most of the material Trex collects for recycling comes directly from generators—retailers, grocers and distribution centers. The material is consolidated and shipped to the company’s processing centers.
STIMULATING DEMAND
Heglas says he is actively working with manufacturers across a wide range of industries to explore additional uses for the LLDPE pellets Trex produces. “It takes some time,” he says.
He says he hopes to see the company’s product used in more applications as manufacturers become more comfortable with recycled content. The issue, he feels, is not supply, though that must be defined. Instead, Heglas says, “It will take innovation on their end to move from one product with recycled [content] to three or five or six products,” he says of manufacturers.
“For film recycling to grow in the United States, we need pull-through from the end user to say they will use recycled content in their products.”
While Heglas says he sees many companies voicing an interest in using recycled content in their products, those potential customers say they need more clean material supplied in order to do so.
“There is plenty of material out there,” Heglas says.
Yet he sees a disconnect regarding manufacturers’ expectations. “There is a bit of a misconception … for recycled content in general that it is going to be a drop-in,” he says. “The recycled material is not going to be exactly like the virgin material,” Heglas says.
“What is missing—and a challenge—is that the end user has to realize they are not going to find material that is identical to [the virgin material] they are using. They either are going to have to adjust their process or adjust their products,” Heglas says. “That is the biggest challenge.”
He adds that recycled material is a “composite of what is in the LLDPE waste stream right now.” Therefore, it is unlikely that recycled material will match virgin material’s specification identically.
“It has to be an iterative process between the recycler developing the recycled pellet product and the end user and changing their process and tweaking their product to accommodate that difference,” Heglas says.
In fact, that is what Trex did when it first started using recycled content; the company started with a single focus.
“As we grew and developed more products, we opened up different ranges of recycled polyethylene that we can use,” he says. “Something similar has to happen for our users of the recycled LLDPE pellet product.”
Much of a manufacturing firm’s ability to accept recycled material will depend on the equipment in its plant. Newer, more advanced equipment tends to have a wider processing window and can accommodate changes either to the product or process, Heglas says. Manufacturers with older equipment will have a harder time of it.
Much also depends on the application. Heglas has seen companies succeed in using a recycled pellet, while other companies were unable to adjust their manufacturing processes to an identical product. The differences lie in the companies’ equipment, processes and products, he says.
For its part, Trex has the goal of supplying a high volume of consistent material. The company does a great deal of blending to assure consistency from lot to lot and box to box, Heglas says.
“We are very consistent—even more consistent than some wide-spec materials you can purchase,” he says of Trex’s recycled LLDPE pellet.
“We strive to make something that is very consistent, very repeatable and in large quantities,” he concludes.
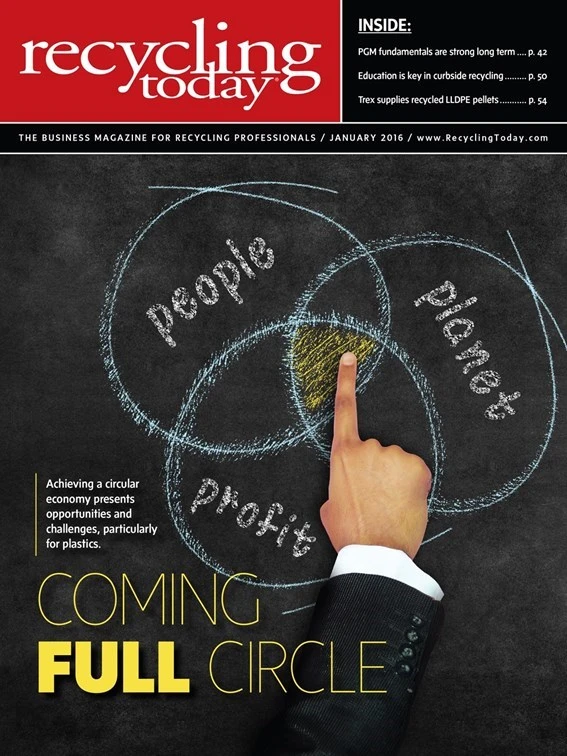
Explore the January 2016 Issue
Check out more from this issue and find your next story to read.
Latest from Recycling Today
- Aqua Metals secures $1.5M loan, reports operational strides
- AF&PA urges veto of NY bill
- Aluminum Association includes recycling among 2025 policy priorities
- AISI applauds waterways spending bill
- Lux Research questions hydrogen’s transportation role
- Sonoco selling thermoformed, flexible packaging business to Toppan for $1.8B
- ReMA offers Superfund informational reports
- Hyster-Yale commits to US production