
Jake Woolfenden
MRF manager at Veolia
When Jake Woolfenden left England to pursue a bachelor’s degree in atmospheric science from the University of Cape Town in South Africa, he promised his family he would return to the United Kingdom to start his career.
Woolfenden stuck to that promise and became involved in Veolia’s U.K. Graduate Trainee Program in 2016. While managing material recovery facilities (MRFs) was not a career option on Woolfenden’s radar when he first started the program, he says it connected well to his studies in Cape Town.
“I studied atmospheric science and climate change, and that led naturally to renewable energy and recycling,” he says.
Veolia’s Graduate Training Program gave him a broad introduction to job opportunities within the company. He spent that two-year period shadowing senior managers within different parts of the business.
“The grad program was such a great introduction into the work that Veolia does,” he says. “I remember, towards the end of my program, I had a sit-down with my manager at the time, and she said, ‘Now that you’re finished, what do you want to do?’ I was umming and erring a lot, so she said, ‘Look, there’s a position running a shift in our MRF that might be a good fit.’
“With AI, I’m excited about detection surrounding quality and being able to work out what is in a section of mixed recyclables instantaneously.”
“I decided to give it a shot.”
Since that point, Woolfenden has held management positions at various Veolia MRFs. He currently oversees the MRF in Southwark, London.
Recycling Today (RT): What is the MRF setup like in the U.K. compared with MRFs in the U.S.?
Jake Woolfenden (JW): I think there are quite a few differences. Scale is one of them. … MRFs in the U.S. tend to be bigger in scale, whereas in the U.K., our MRFs tend to be between 20,000 and 100,000 tons per annum. We have the odd 300,000-ton-per-annum MRF; but, as a rule, MRFs here are smaller than they are in the U.S. The reason for that is in the U.K., we have a lot of urban areas and space is a constant challenge.
RT: Contamination is a challenge for MRF operations. What are some of the biggest contaminants you’re seeing?
JW: For us, I think food is a big one. Food is really difficult to take out mechanically, so the key with food is that you have to stop it from getting to the MRF in the first place. This means you have to be incredibly reliant on consumers not putting their food in their [dry mixed] recycling. The best way to do that is through education and communication.
RT: Is there any new equipment that you’re excited about?
JW: The obvious one is robots and artificial intelligence (AI) coming into the MRF space. Robots are on the horizon—if not already here—with many in use here in the U.K. As prices come down, we’re going to see this more and more. With AI, I’m excited about detection surrounding quality and being able to work out what is in a section of mixed recyclables instantaneously.
At the moment, we test our material quality when it comes to the plant with a physical sampling regime, and we have an average on a monthly and weekly basis. But it’s a very time-consuming process, and the feedback is not instant, so it’s quite hard to react in time.
But the tech is nearly there to automate, and this will be so powerful.
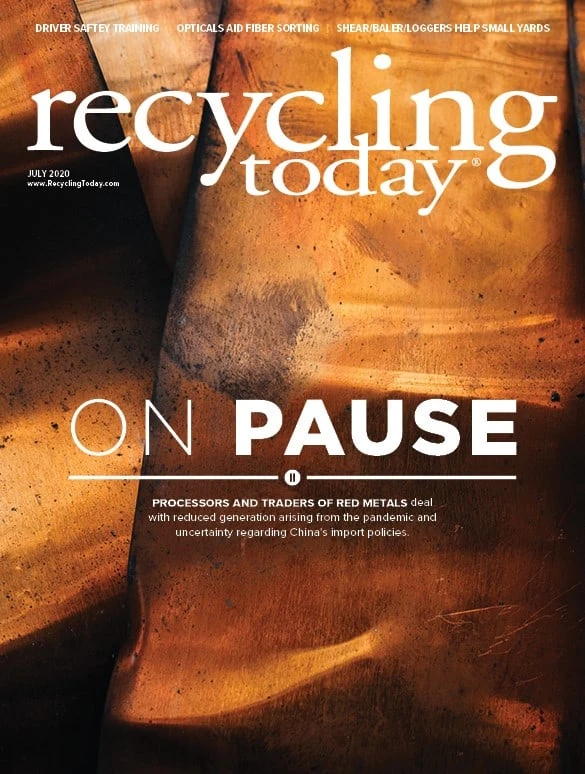
Explore the July 2020 Issue
Check out more from this issue and find your next story to read.
Latest from Recycling Today
- Circular by Shapiro releases "5 for Five" sustainability series
- Graphic Packaging set to close Ohio CRB facility
- Ameripen voices support for Maryland EPR bill
- Maryland county expands curbside recycling to include electronics
- California EPS ban will be enforced
- YKK AP America introduces BetterBillet
- Fresh Perspective: Cameron Keefe
- The problem solver