Ernesto Valencia
Plant manager at Diversified Recycling Inc.

Ernesto Valencia began his recycling career 13 years ago as a sorter at Diversified Recycling Inc.’s material recovery facility (MRF) in East Hazel Crest, Illinois, a suburb of Chicago. “I didn’t think I would be playing with garbage my whole life, but here I am,” he jokes.
Valencia says he worked his way up the ladder, starting on a temporary basis as a sorter. He then became a baler operator before becoming a MRF supervisor, operations manager and finally plant manager in March 2020. “As doors opened, I was able to fill those positions,” he says. “You’ve got to keep that motivation and [be] able to keep trying to knock on someone else’s door and keep trying to take different positions.”
”The more you know, the more valuable you are. Knowledge is everything.”
Since becoming plant manager two years ago, Valencia has had to navigate his new position within the MRF and the onset of the COVID-19 pandemic and the related changes to the labor force and the traditional working environment. Employee retention has been a point of emphasis at Diversified, as it has across most companies, and Valencia says he’s worked hard to maintain employee morale while ensuring limited disruptions to the MRF’s operations. He says, “That’s where you think outside the box again and start moving people around in different positions or coming up with different ideas [like] more automation.”
Valencia shares the lessons he learned working his way through the recycling industry, the importance of continuing education and how automation has helped the MRF navigate labor shortages.
Recycling Today (RT): When you first were hired as a sorter, was there a lot to learn about the industry?
Ernesto Valencia (EV): When I first started, I knew the basics of how to turn a wrench [or] how to turn a screwdriver, but it’s all the detail work. … Just because I’ve been doing this for quite some time, I still don’t know everything. I try to be out there and continue to learn. I’m actually going to baler school, optical school, stuff like that. Education is everything. I try to teach and show [people] that you can never learn enough. The more you know, the more valuable you are. Knowledge is everything.
RT: It seems like employee retention, or just keeping up morale, is a big challenge right now. What have you found works for your facility?
EV: The pandemic was something that just came out of the blue. That really made things super difficult in so many different ways [and] companies realized, “How many employees can I run the system with?” It really kind of created a lot more jobs [in some ways], but it really broke it down in terms of how things can really work in a company.
Since the pandemic, we’ve lost half our shift and we were able to move things around, and that’s when you think outside the box, start moving people around in different positions ... [and use] more automation.
RT: What are some new technologies you hope to see embraced more?
EV: I would like to see more optical [sorters]. We just replaced a few, like a PET (polyethylene terephthalate) one, and they work great. ... Everyone who’s dealing with a labor shortage, [robotics] would be great in different facilities … and that helps labor costs.
… Fires in this industry today [also] are incredible. I couldn’t tell you how many fires we’ve had already this year to where Fire Rover has helped out [and] employees have helped out. It’s amazing how just a simple battery can cause a fire in the system or on the tip floor. I would love to see more fire-suppressing ideas out there, and robotics to help and sort; I think those will be big players.
Get curated news on YOUR industry.
Enter your email to receive our newsletters.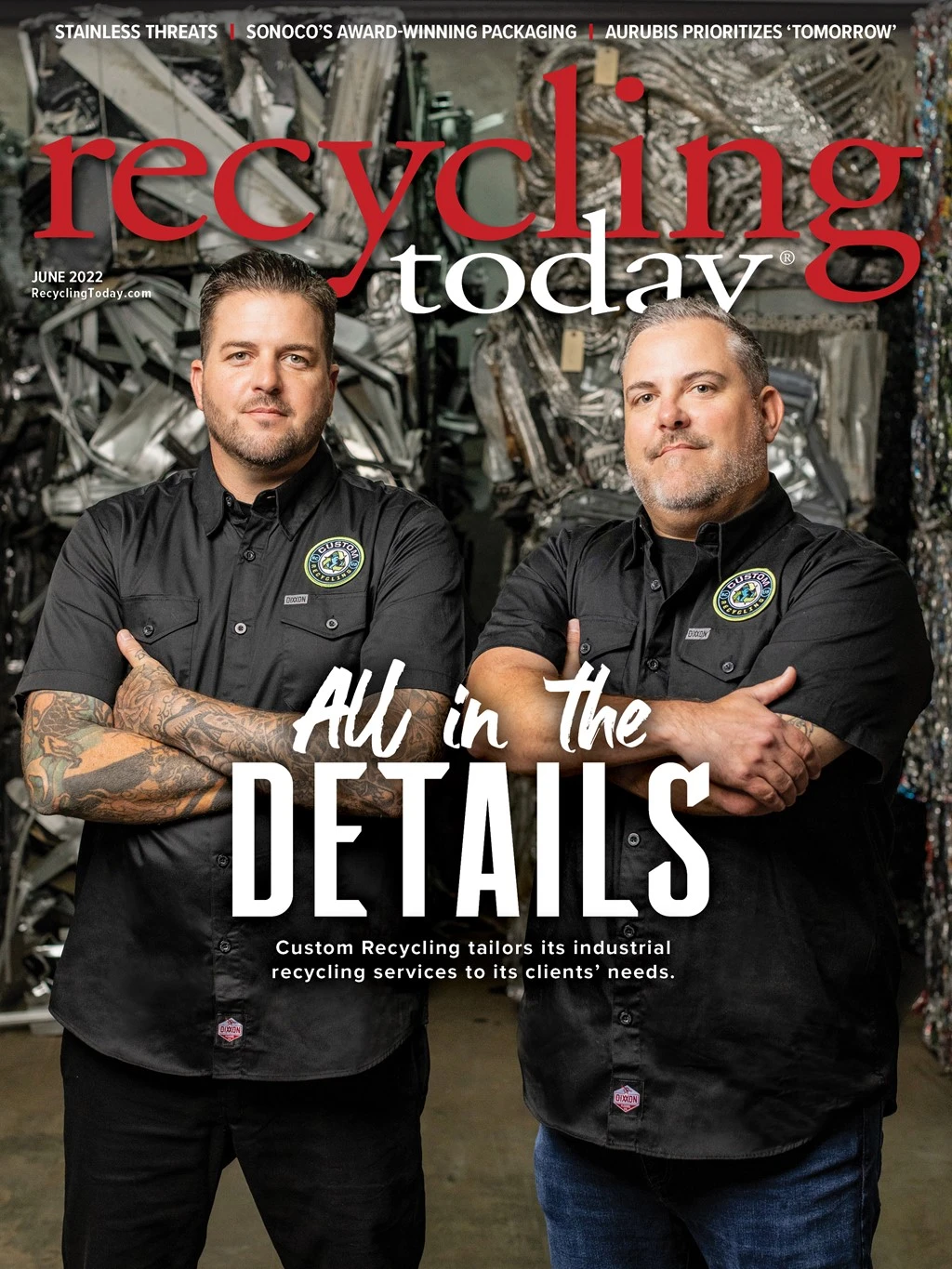
Explore the June 2022 Issue
Check out more from this issue and find your next story to read.
Latest from Recycling Today
- Enfinite forms Hazardous & Specialty Waste Management Council
- Combined DRS, EPR legislation introduced in Rhode Island
- Eureka Recycling starts up newly upgraded MRF
- Reconomy Close the Gap campaign highlights need for circularity
- Nickel carbonate added to Aqua Metals’ portfolio
- EuRIC, FEAD say End-Of-Life Vehicle Regulation presents opportunity for recyclers
- Recyclers likely to feel effects of US-China trade war
- BCMRC 2025 session preview: Navigating battery recycling legislation and regulations