Foundries have long looked at themselves as the nation’s recyclers. Since metals were first poured, it was recognized that recycling old iron castings was the easiest manner to remake another casting and re-use society’s unwanted cast articles. Later, steel scrap was introduced into our charge mixes as an additional feedstock to achieve the same goal. This recycling trend extended to most other metals cast, including aluminum, copper and lead.
Because of our recycling of metals, most foundries have long considered themselves a part of the green technology movement before the term “green” was even coined. In reality, the foundry industry has only scratched the surface of being green and has yet to achieve the higher level of sustainability that the future will demand. We are an energy-intensive industry, handle massive quantities of processed waste materials often destined for landfills and have the potential to emit a large quantity of carbon dioxide and other pollutants into the atmosphere.
GREEN TECHNOLOGY
What is a green technology? Green technology encompasses a large body of concepts whose definition may vary by group or industry. Synonymous with sustainability, green technology is broadly defined as technology that, when properly implemented, allows an organization to meet its present needs without compromising its future needs. Green technology can include energy and material waste reductions in the manufacturing process and the use of alternative manufacturing technologies with the least impact to human health, the earth and its natural resources. Sustainability and the application of green technology means finding smarter ways to use our finite natural resources, both in manufacturing materials and in the energy reserves used to manipulate them.
Waste reductions in the manufacturing process can take on many forms. All waste streams that leave the facility, regardless of media, must be evaluated for potential reductions. Manufacturing processes need to be as self-contained as possible, with process materials recycled without an undue addition of energy demand.
Energy reductions in the manufacturing process pose significant potential improvements in total energy usage and the reduction of carbon emissions resulting from the combustion of fossil fuels. To become greener, one must find ways to increase the efficient use of energy in the complete manufacturing process and not merely shift energy use up or down the manufacturing stream.
GREENING THE INDUSTRY
What about our industry? Have we given green technology the attention it requires? Many of us may believe the idea that simply recycling our region’s available scrap makes us a green industry and we need not go further.
Spent molding sand has received a lot of attention in the past couple of decades. It can be reclaimed internally or beneficially re-used by another industry. Sand reclamation usually requires a combination of mechanical and/or thermal processes to recondition it for re-use in the coremaking process or greensand system. To date, both reclamation processes have required significant demands in energy to make spent green and core sands reusable within the foundry. Nonetheless, the beneficial re-use of foundry sands and recovery of their additives has gained a lot of popularity in recent years in light of its other environmental benefits. Spent foundry sands have been successfully used as a source of silica for cement production, flowable fill for construction, roadbeds and geotechnical fill for a variety of projects. A more recent development for spent sands has been in the use of soil amendments for croplands in the agricultural industry. In addition to the completion of these worthy projects, every ton of foundry sand or slag used in this manner results in a reduction of native materials that must be mined or landfilled elsewhere. A website promoting these wide uses of spent foundry byproducts can be accessed at www.foundryrecycling.org.
Today’s efforts cannot be considered the pinnacle of the green effort for our industry. Modern society demands more from us. It is time to recognize that many industry paradigms restrict us from acting. However, new paradigms are being created.
We can become a much a greener industry. Much of the technology to become greener exists now, and we have the resources to become increasingly sustainable in the future.
There are many barriers to be broken, but with focused research we can find a way to break down those barriers. The choice to avoid becoming greener now will result in consequences for our industry in the future. Our customers will require an accounting of our greenness (either formally or informally) as a precept to placing orders for our castings. This is understandable, as they will be experiencing similar pressures from their own customer base. Our customers and communities desire and expect us to be good corporate citizens.
WHERE DO WE BEGIN?
How do we as foundries begin to become greener organizations? As with all well-founded and lasting corporate projects, it requires top management support. Top-level management needs to establish it as a priority right along with all of the key metrics such as safety, quality and profitability. Management must create the vision and work to put the tools in place to achieve that vision.
A management culture needs to be established to foster the goal of being green and sustainable. To do that, many things need to become a part of a company’s everyday work habits. These go beyond just designating a “green department” or authorizing token green projects. People must be encouraged to develop and implement green process changes without the fear of potential failure from the pursuance of a path less taken. The time necessary to learn new technologies and to train on and optimize new equipment must be granted to ensure the highest level of efficiency.
The removal of concern for making informed but nontraditional decisions can be a powerful incentive to employees to innovate the foundry to a greener level. This culture, along with an associated accounting process that gives credit to green thinking departments is necessary in fostering green improvements.
STARTING THE PROCESS
A critical tool for success is the designation of a specific person to facilitate the expanded effort of green and sustainable activities for the company. Preferably, the person’s sole job responsibility should be the development and implementation of green activities. If the organization’s size does not permit this dedicated staff position, then oversight of green activities may need to be designated as a specific individual’s part-time responsibilities.
From the bottom up, every employee needs to see and believe that the company demands a significant improvement in how materials and energy are used. Policies and procedures that define the proper daily actions need to be established in all operational areas, including purchasing, marketing, engineering, maintenance and production.
MEASUREMENT SYSTEM
An important step in green management is the creation of a measurement system for greenness. In the example of energy, our traditional engineering system uses terms such as Kwh (kilowatt hours), therms and Btus (British thermal units) consumed. While still excellent units of measure, new green energy terms have become popular to assist in the public’s understanding.
Measurements described in cars taken off the road, trees planted and numbers of homes heated have become popular comparisons to gauge a company’s success. For the pure engineer, these new energy terms may be hard to adapt to, but they have become the language of the green community that must be used to communicate. A good example of these types of comparison systems can be accessed at http://www.epa.gov/cleanenergy/energy-resources/calculator.html.
At a rapid pace, energy-use measurement systems are becoming more advanced and specific to your operation. Besides data available for a wide spectrum of industries, data is now available for specific regional energy providers. The result of this is the potential for the development of a relatively unique carbon footprint for the production of your facility’s electricity. Utilizing the specific carbon information for your energy provider can be as easy as using a reference such as the U.S. EPA’s eGRIDweb at http://cfpub.epa.gov/egridweb/. The availability of these tools can provide great assistance in communicating green energy improvements with external parties.
It is becoming common that measurements for tracking many attributes of greenness (energy use and beyond) need also be put in place for communication to the public. Providing the public with transparent information that measures the quantitative aspects of resource management within the organization is making sense to many forward-thinking companies. Even though it is an important aspect of our industry, this type of reporting goes beyond energy use to also include aspects such as material recycling and social due diligence efforts as an example. Organizations such as the Global Reporting Initiative, http://www.globalreporting.org/Home, are working to provide accepted reporting methods that assist in rolling all of this information together into a sensible format for reporting to interested external parties.
It is now time to roll up our sleeves and start becoming greener. The possibilities for operational improvements are endless to achieve a greener foundry operation. None of us is exempt from the potential to make significant improvements in energy savings and waste minimization. The tendency is to tell ourselves that we already have good programs in place, do a good job of being energy efficient and are leaders within our industry. The truth is we all have big opportunities ahead of us, whether we are a large mega-foundry or a small-to-medium-sized casting operation.
GOING FORWARD, FINDING WAYS
Significant capital spending is not the only way to realize savings and improvements. However, it must be recognized that we can work within our own model. We don’t need to wait for the silver bullet of new facilities or a new foundry. Gary Thoe, past President and CEO of ThyssenKrupp Waupaca and an AFS Gold Medal winner, was fond of saying, “Continuous improvement beats postponed perfection.” Many projects will yield only 1 percent to 2 percent savings in either waste reduction or energy conservation, but several of these projects in cumulative will add up to substantial improvements.
Recently, several foundries made a pledge with the U.S. Department of Energy’s “Save Energy Now” Leader Program to cut their energy use by 25 percent in 10 years. While this goal may seem daunting, many of these companies will find their success will be measured by the incremental identification and completion of a multitude of smaller projects, not full-scale facility overhauls.
To achieve these continuous improvements, a clear strategy must be developed and followed. A six-step method can be used as an effective strategy to realize results:
- Audit—perform an energy and/or waste reduction audit. This can be done either internally or externally. In either case, be critical, thorough and honest. Don’t be hampered with questions or concerns about how reductions can be made, but focus on identifying areas of waste within your process.
For those identified areas, estimate the energy use or waste quantities by using the best current information available. The tabulation of these findings can be done for an entire facility, department by department or by production process. Don’t be overly concerned about a high degree of accuracy; just get a relative estimate of the size of the use or waste. - Benchmarking—for organizations with multiple facilities, compare your initial findings with those from other facilities. If public or trade group data is available, it can also be enlightening to compare your findings with those from other organizations with similar processes.
- Possible Solutions/Reductions to identified wastes should be researched. Here the possibilities are endless:
- Remember; never underestimate the level of knowledge and ideas that may already exist on your plant floor. Some of the best waste reduction ideas come from those who operate and monitor the process on a daily basis.
- AFS has been very proactive in publishing numerous articles in Modern Casting, AFS Transactions and other publications regarding the improvement of foundry operations. Additionally, several AFS committees are actively working on waste reduction projects and publishing results of committee activities. Any committee chair should be able to assist in providing a contact with the most up-to-date ideas available.
- Numerous organizations have informational resources available to foundries. Organizations like your electric utility, gas supplier and “Focus on Energy” (a Wisconsin-based program) all have assistance personnel and energy reduction programs. Websites like AFS-FIRST (Foundry Industry Recycling Starts Today), www.foundryrecycling.org, can provide valuable information on potential methods of re-using spent foundry sands.
- Both supplier representatives and contract experts in numerous disciplines are also available in both the foundry and environmental industries to assist in waste reductions and energy savings.
- Remember; never underestimate the level of knowledge and ideas that may already exist on your plant floor. Some of the best waste reduction ideas come from those who operate and monitor the process on a daily basis.
- Prioritize Projects—not all projects can be launched at one time. Recognize that available time and financial resources means priorities need to be established. Priorities aren’t always based on the biggest savings. Project selection might be for initial “low hanging fruit,” corporate/community visibility or to launch a project that will act as a focal point to changing the organization’s culture.
- Implement the Plan—each project will have a different path, be it one requiring capital expenditure approvals, equipment design or acquisition, process engineering, specific timing of equipment downtime, or a host of other requirements. It is important to communicate the plan to all stakeholders and work to get them vested into the reduction effort. Doing so will only raise interest across the board and help ensure project success.
- Measure the Change—as the old adage describes, it is hard to manage what you cannot measure. It is just as important to document conditions before the change as it is to measure those conditions following the change. As discussed, we are going to be held accountable for the improvements we make. It is critical to record that we are both making improvements and realizing the resulting savings for interested stakeholders.
Metering/recording instrumentation for electrical, gas and water systems can be of great assistance in improving a facility’s knowledge of both existing energy usage and the result of any following changes. Simple metering and recording instrumentation can be added to practically any energy delivery system with no system modifications and at a reasonable cost. Once baseline measurements are established, well-designed metering can be a tremendous advantage in identifying and monitoring facility improvements, which in turn helps steer the ongoing continuous improvement effort.
Maintain an awareness that secondary benefits will result from many facility improvements. These benefits (sometimes pre-recognized, sometimes not) will manifest in the form of improved safety, employee morale, increased productivity, reduced labor and other related savings. This lies at the very heart of being green. The proactive foundry will quickly learn to appreciate the multifaceted returns on their effort.
STARTING AT “HOME”
Let’s look at some of the specific areas in our operations that are ripe for improvement.
Re-use of Waste Heat. Returning to energy savings, one of the most significant areas for achieving energy reductions is in the re-use of waste heat from many foundry processes. The re-use of waste heat can often net energy savings of 15 percent to 25 percent or more. While technologies exist for converting waste heat energy to electric power (or, indirectly, compressed air), these often prove costly in terms of the required capital expenditures and extended payback. A simple and less costly approach is to directly recover captured waste heat for use in an area that requires heat. This can be performed by transporting heat via air-to-air, air-to-liquid, liquid-to-air or liquid-to-liquid conversion. Taking this approach greatly simplifies the process by logically using an available heat to provide heat elsewhere as needed.
Several successful projects have been completed that utilize waste heat from melting operations for building heat, core drying and/or shower water heating. With proper design, these systems can also use heat pump principles to utilize waste heat for air conditioning or chilling, to maximize the year-round benefit of the facility’s investment.
The simplest approach to re-using baghouse heat energy is the direct reintroduction of the exhausted filtered air back into the plant. This reintroduction of waste air is feasible if there are no additional gaseous pollutants in the waste air stream. The superior performance of modern baghouses and the advent of broken bag detection technology have eliminated the concern of re-introduction of particulates back into the workplace. In fact, well-run dust collection equipment regularly contains a lower particulate count than what may be experienced in the general workplace. Using this strategy provides a two-fold benefit, the re-use of available heat for space heating and the reduction of the need for additional heated makeup air.
Air Handling Systems. Emissions requirements imposed on the metalcasting industry in the 1970s caused many foundries to put into service extensive air capture and baghouse systems. Many of these systems may have not undergone any significant redesign since their initial installation. The average foundry emission system may consume 20 percent to 25 percent of the total energy usage in a foundry. In recent years, many improvements in piping, engineering, components, baghouse design and bag materials have taken place. Our industry now has a greater understanding of the role of mass flows through ductwork, pressure drops across various components, fan and motor operating curves and the computer monitoring and control of actuating devices.
Many systems have been put in service reusing existing fans and motors and other components, to facilitate installation cost savings. Other systems were placed within the limitations of existing plant layouts. These choices, which may have been the best option at the time, have resulted in higher pressure drops, wasted horsepower and lower system efficiencies. We need to step back and re-evaluate the use of best engineering practices and available strategies to lower pressure drops, reduce horsepower consumed and improve system efficiencies.
Lighting Systems. Plant and office lighting can also be a significant source of energy savings. Here, management will most likely be confronted with some capital costs to realize energy savings, though the ability to tackle those costs in manageable steps can be realized.
Today’s lighting technologies are highly efficient in their use of electrical power as compared to the past lighting technologies available. If this technology has a fault, the fault is in that it is improving so rapidly it makes recently installed upgrades “obsolete.”
However, the cost of not acting now to streamline your lighting systems far outweighs any concerns in this area. Because lighting is universal to all industries, and its improvement is easily measured by the difference between the previous and new fixtures, many governmental agencies and power providers have made this an area with significant available rebates and tax incentives.
Today’s lighting fixture designs drive light deeper into the plant and provide truer colors for better employee comfort. Beyond the selection of appropriate fixtures, lighting fixture layout acts as a primary tool for efficiency improvements via a qualified engineering review. Motion sensing and centralized automated control also offer opportunities for significant improvements, in both energy usage and in maintaining consistent levels of light where and when it is needed.
Both the deposition of dust and high heat can be a problem with incompatible lighting fixtures and sensors in an operating foundry if not managed properly. Tolerant specialized fixtures exist that will perform well in these areas. However, “easy” plant areas such as offices, core rooms, pattern vaults, shipping warehouses, maintenance shops and similar low-dust areas are prime candidates for the first phase of lighting retrofits.
Compressed Air Systems. Compressed air also represents a significant area of potential energy efficiency improvement. The generation and delivery of compressed air is highly inefficient, with one-third of all compressed air horsepower being lost in the process. Every foundry should develop an in-depth understanding of the functioning and limitations of their compressed air system, and work to improve its performance. A supply and demand side audit, as well as a system leak evaluation, can yield tremendous benefits. Savings are typically realized in these low-capital activities such as leak repairs, piping changes, air storage sizing and proper compressor sequencing.
Many of us are guilty of just tapping new processes into an existing system without much thought on how they may add to the inefficiency of air delivery. Beyond the modest improvements just described, a well-designed evaluation and re-engineering will often yield even greater benefits in energy use reduction and system delivery/reliability.
Melt Savings. Never forget that every area of the foundry operation is fertile ground for green savings. Buying the right scrap can net energy savings even before melting materials are received at the foundry. Ferrous foundries have long been comfortable with receiving post-consumer steel scrap that contains a moderate amount of surface rust, paint, adhering nonmetallics and other non-steel attachments. Sheared scrap can contain 5 to 8 percent by weight of tramp nonmetallic materials. Eliminating the nonmetallic materials can yield significant savings. The savings in this example are experienced throughout the melting process. Energy is consumed in shipping this material. Charge weights are affected by nonmetallics. One often unrecognized energy loss is that it takes 1.7 to 2 times the energy to melt slag than iron. Thus, by purchasing a clean scrap created by shredding rather than shearing, one reduces energy consumption (of the steel scrap portion of charge) by 15 percent to 20 percent. Shredded materials often cost more than sheared scrap but paybacks in other areas can offset these costs while promoting the plant’s sustainability effort.
Further melting savings can be achieved by cleaning gates and risers of sand by passing them through a properly designed rotary drum or, for very clean returns, a quick shot blasting of the returns. Reclamation of this sand may be desirable from the aspect of recovering the thermally expanded and, therefore, more dimensionally stable sand adjacent to the gating.
Keeping scrap yard sand/dirt to a minimum and away from the charge bucket will provide not only energy benefits but also reductions in potential fugitive dust and the dust collection required to capture it.
Sponsored Content
Labor that Works
With 25 years of experience, Leadpoint delivers cost-effective workforce solutions tailored to your needs. We handle the recruiting, hiring, training, and onboarding to deliver stable, productive, and safety-focused teams. Our commitment to safety and quality ensures peace of mind with a reliable workforce that helps you achieve your goals.
The same principles can be applied to the nonferrous foundry. Returns entering a gas melting furnace should be as clean as possible. Ingots should be introduced into the bath directly and not placed on the hearth and allowed to oxidize.
OTHER AREAS FOR SAVINGS
The maintenance of insulation on all heated ductwork keeps process heat where it belongs. In the winter months, heat leakage might be considered acceptable as a supplemental building heat source, but in the summer, it adds to the plant temperature load and will need to be exhausted from the plant. Perform regular inspections on all ductwork and calculate the heat losses. In almost every case, the value of insulating ductwork and piping will be recovered quickly.
Cores/Binder Systems. Corerooms are particularly good candidates for improving your greenness. The U.S. Environmental Protection Agency (EPA) is required to regulate hazardous air pollutants (HAP) from major sources including foundries under the Clean Air Act of 1990. The Casting Emissions Reduction Program (CERP) was created to evaluate the HAP emission potential of various coremaking processes and binder systems. Phenolic urethane no-bake and coldbox systems were identified as having the highest emissions, largely because of the solvent-based nature of both systems. The binder industry responded with options to replace some or all of the aromatic solvents.
In ferrous applications, the substitution of aromatic solvents in Part 1 and Part 2 urethane coldbox resins by methyl esters derived from vegetable oils results in a reduction of volatile organic compounds (VOCs) of nearly 50 percent for both parts. These binder versions, often referred to as “biodiesel” from the use of methyl esters used to oxygenate diesel fuels to render them cleaner burning, can reduce benzene, toluene, xylene and naphthalene emissions at pouring, cooling and shakeout by 20 to 30 percent.
Development of resin systems have not been limited to the reduction of VOCs; the reduction of odors from foundries is becoming increasingly important. Foundries have traditionally relied on abatement and/or treatment systems such as scrubber and regenerative thermal oxidizers to eliminate pollutants and odor-causing substances. In nonferrous applications, tetraethyl orthosilicate (TEOS) replaces aromatic solvents in Parts 1 and 2. Although the VOC emissions are similar to traditional aromatic-based solvent resins, the primary advantages of this silicate-based solvent are reduced condensate formation and reduced smoke and odor at pouring, cooling and shakeout. This is especially important in lower pouring temperature aluminum semi-permanent molding; excessive smoke and condensate (tar) formation in the die are not only environmental but also productivity concerns.
Even with the substitutions mentioned, the continued use of phenolic resins is threatened by lower emission standards. This has given rise to a new generation of inorganic systems, such as heat-cured sodium silicates or ester-cured no-bake sodium silicate. The original CO2 gassed system introduced in the U.S. in 1952 suffered from sensitivity to moisture, low strength and poor shakeout. The latest-generation systems all use some form of aluminosilicate (geopolymer) or other inorganic additive to reinforce the water-soluble silicate. These systems have little to no VOCs, are generally non-flammable, generate no odor during mixing, coremaking and shakeout. They generate little to no smoke during casting. While these systems are quite advanced for nonferrous applications, further development for ferrous is required.
Many efforts have taken place to remove core washing from the coremaking process. In many cases, it can successfully be eliminated with improved coreroom process controls, while for other castings it is a necessity. If a core wash is desired, then a novel way to cut core drying costs is to use a color-changing indicator in the core wash to determine when a core wash is dry. Drying time can possibly be cut by 50 percent and, therefore, gas consumption could be cut by more than 50 percent. Core ovens are typically very inefficient. Making a number of modifications, like adding air turbulizing devices to break up laminar airflows or introducing air to both top and bottoms of the drying belts, greatly speed up core drying and improve efficiency.
System Efficiency. In looking at cutting energy, we always need to be mindful of the efficiency of the system. Much like the widely accepted casting process simulation, modeling of the core making process can result in fewer shop floor hours spent developing and optimizing tooling. The efficient placement of blow tubes and vents may result in lower binder levels, by reducing the compensation used to make up for inefficiencies in current methods.
These examples are not used to endorse any product or system but to show how simple ideas can significantly contribute to going greener, enhance the process and become beneficial quality control tools.
WHAT ELSE CAN BE DONE?
Energy reductions in the molding process represent a bigger challenge for going greener. The easiest savings are in the efficient use of power. Utilizing high-efficiency motors should be the first consideration. High-efficiency motors or even ultra-high-efficiency motors can save 2 to 5 percent on operating energy. When considering the cost of high-efficiency motors, remember that the original purchase price will probably be no more than 5 percent of the operating cost of the motor over its life span, and the cost of electricity will be more than 95 percent of the cost of operation. As a general note on motors, a foundry needs to have a very specific procedure on the rewinding of motors. In most cases, the rebuilding of motors should not be done except in the case of very unique motors or a long lead time for a new motor. Studies have shown that rewinding motors nearly always results in a motor that is not as efficient as the originally purchased motor. If rewinding must be done, a carefully written set of engineering instructions and procedures, as well as an approved source for carrying out the work, must be in place. Another consideration is using variable frequency motors for operations that have widely varying loads throughout a cycle, for example, mulling of sand.
In the nonferrous foundry, industry conservation of water in diecasting operations offers opportunities for significant savings. Far too often, cooling water is used once and passed down the drain. This hot or warm water has heating value for many applications. As discussed previously, BTU content can be pulled from any liquid. Creative use of this heat recovery is a matter of looking for the best use for the heat.
Additionally, water of varying temperatures may be suitable for re-use. One fallacy is that cold water draws more heat out of a mold. Temperature pickup is uniform over a very wide range of incoming water temperatures. Going greener often requires some research to break a paradigm and change a popular belief.
What technical barriers exist in the foundry process that prevents us from becoming much greener? Are there some areas of the foundry process that have technical challenges, for which we have no current solution? The fact is there are technical barriers to the casting process that have yet to be broken, and these barriers are preventing us from achieving really significant energy savings or waste reductions.
One example of a technical barrier is the lack of a rapid prototyping system for green sand molded iron castings. There are no complete systems to make a casting in a day’s time that will replicate a production casting. There are some programs that will replicate the geometry of a mold, but usually not in a binder system suitable for iron pouring. Duplicating the surface finish, draft, ingate and riser locations and mold pouring and shakeout conditions are also considerations. The other major component of a rapid prototyping system must be the duplication of iron properties from a small furnace, where chemistry can be varied to tailor casting properties.
CONCLUSION
Many of these ideas are not so new and we have all talked about implementing them. However, time passes and maybe we have not pursued these ideas because of other current concerns or we have done so only in an inconsistent manner. Reaching the point of determined action and embracing the possibilities of sustainability may prove to be one of our greatest challenges. Once we have achieved the focus to think green in all aspects of our industry, we are open to the possibilities that were only waiting for us to seize them. This focus, along with the pragmatic application of existing technology, will guarantee that the foundry industry is recognized as a sustainability leader by other industries and the public.
Gary Gigante is president and CEO of ThyssenKrupp-Waupaca, Waupaca, Wisc.
Get curated news on YOUR industry.
Enter your email to receive our newsletters.
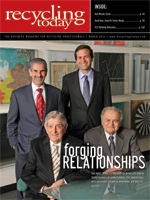
Explore the March 2011 Issue
Check out more from this issue and find your next story to read.
Latest from Recycling Today
- Altilium produces EV battery cells using recycled materials
- Brightmark enters subsidiaries of Indiana recycling facility into Chapter 11
- Freepoint Eco-Systems receives $50M loan for plastics recycling facility
- PET thermoform recycling the focus of new NAPCOR white paper
- Steel Dynamics cites favorable conditions in Q1
- Hydro starts up construction in Spain
- Green Cubes unveils forklift battery line
- Rebar association points to trade turmoil