
You work in recycling and know how tough the environment can be on equipment. In fact, it is one of the harshest applications possible for a forklift. Debris, dust, uneven surfaces and weather all can cripple a forklift, bringing your operation to a standstill.
This article helps fleet managers understand a few of the main factors that need to be considered when choosing the right forklift for a recycling environment.
Not your typical forklift environment
The majority of the forklifts in use today are operated within supply-chain-related environments, such as warehouses or cross-docking facilities. While each one of those facilities can offer their own unique set of challenges and hazards, it’s fair to say that few of those compare with the challenges and hazards confronting forklifts in recycling environments daily.
The recycling process by nature generates debris beyond the typical dust, which can cause skyrocketing maintenance costs and unexpected downtime for forklift fleets. Metal scrap, such as baling wire, strapping and chunks of iron, can damage the underside of a forklift. Paper and plastic scrap, along with dust, can plug up radiators, causing overheating of the forklift’s
Often, the recycling process is performed completely outdoors, which introduces additional challenges. The changing and unpredictable nature of the weather means that forklifts and operators could be working in extreme heat, freezing temperatures, falling snow or pounding rain. And, because the operation is outdoors, the machines are not traveling on smooth, flat warehouse aisles but on (often) dirt pathways filled with gravel and potholes and ruts. When it rains, these dirt paths turn to mud, offering little traction.
It’s for these reasons and more that it takes a special kind of forklift to withstand the rigors of working in a recycling environment. Managers should consider a number of important factors when choosing forklifts for their recycling operations.
Overheating
One of the most damaging hazards for forklifts in recycling environments is the dust and debris constantly in the air. It can clog radiators and lead to overheating, deteriorated performance and even
Performing in these hot, dirty, heavy-use environments requires a heavy-duty cooling system. Not all forklift cooling systems are up to the task. Some are designed with automotive-style radiators (with thin aluminum fins) and plastic coolant and transmission fluid tanks.
Look for a cooling system that provides a separate radiator for the engine and one for the transmission. Large openings between cooling fins also help reduce clogging. Keeping your engine and transaxle cool is key to longer component life and less downtime.
In these environments, it’s also not uncommon for operators to have to take time from their tasks to manually blow out the radiators at least once per shift. Each blowout can take 15 to 20 minutes and requires that the forklift
Some companies have tried other ways to deal with this problem, such as regularly cleaning radiators with brushes and high-pressure water. However, this type of continual cleaning may cause additional damage the radiator.
While this is a problem that has plagued forklift operators for years, the solution is pretty simple: Enable the cooling fan to be controlled independently of the engine speed. This allows the system to automatically clear the radiator of dust and debris every time a user starts the forklift by reversing the fan direction. The forklift essentially cleans its own radiator, saving operators and maintenance technicians hours of time each month.

Durability
The rough, uneven surfaces in recycling facilities—often littered with metal and concrete pieces, as well as potholes and ruts—can damage a forklift’s
Forklifts that can withstand the harsh environments and extended operating hours require an industrial design that factors these conditions into the product. This can include an industrial engine with a cast iron head and larger, more robust components; fully enclosed brakes that are protected from debris and that have fewer moving parts to break down; pneumatic (super-elastic) tires that can withstand the rough surfaces; rugged cast iron housing to provide thermal and impact protection for the transmission and axle; and a protected undercarriage that helps prevent damage from scrap metal.
Operator comfort/safety
For many forklift operators, the forklift is their office. Outside of personal breaks and maintenance stops, they spend the majority of their days on a truck, and the way they interact with that equipment has a big impact on overall productivity and safety. For recycling environments with extreme, unpredictable weather and operating conditions, the forklifts must be designed to keep your operators comfortable, safe and productive.
One way to keep operators comfortable is with a hard cabin that is designed around the operator to provide a quieter, more comfortable environment and optimum visibility in all directions. This is especially important in outdoor and extreme applications,
Other features that can improve productivity and reduce operator fatigue are floorboards that absorb vibrations, seats that can be adjusted for comfort and provide shock absorption, an open mast design for better visibility and intrinsic stability features that provide operators greater control and confidence as they maneuver through the recycling environment.
Maintenance/service
Regardless of how well your forklifts are designed and your operators trained, accidents can happen, and equipment wear and tear occurs. Given the performance demands and potential hazards in harsh recycling environments, having a good maintenance program is essential.
Correctly managing service intervals can spell the difference between a profitable or an unprofitable operation. Regular service intervals should be set and strictly followed, with special attention given to those parts that are affected most by the harsh environment. The goal is to keep the forklifts in operation while minimizing unplanned maintenance issues.
It is important to note that true industrial engines typically have greater oil capacity and sometimes come equipped with an external oil cooler, which helps maintain oil viscosity, extending engine life and potentially enabling extended oil change intervals as well. Service intervals also can be reduced through the use of a gear-driven camshaft and valve train as opposed to the typical automotive approach of timing belts and chains that require replacement or service.
One method of ensuring that the forklifts are properly maintained is through an operator and fleet management system that can monitor the health and performance of the trucks. These systems guide operators through their checklist inspections, ensuring they are done correctly. They also monitor impacts and send event codes and service notifications.
A case in point
The PRI Group, Bensenville, Illinois, is a full-service recycling company primarily handling paper and plastics. In its 110,000-square-foot facility, the company collects, sorts, bales
The company operates three shifts, 24 hours per day, six days per week to handle a heavy workload, consisting of incoming material being taken to processing stations and baled material being loaded for outbound shipment by truck and rail.
The recycling process generates a great deal of dust and debris in the PRI Group facility, both on the floor and in the air. Baling wire and strapping material often fall within the aisles, and the fine paper dust works its way into every piece of machinery. The company’s previous forklift fleet often suffered drivetrain failure when debris on the floor became entangled under the forklift. Hydraulic failures, caused when paper dust infiltrated the forklift’s hydraulic system, became commonplace, while trucks struggled with overheating when the radiator became coated with debris.
PRI Group routinely performed planned maintenance with every 500 hours of use, but skyrocketing maintenance costs and unexpected downtime were becoming a consistent headache, especially with the facility consistently running at full capacity.
The PRI Group selected the Crown C-5 Series LPG forklift and Crown InfoLink Fleet Management system to help address its downtime issues. The forklift’s under-chassis protection shields drivetrain components from debris, while its dual radiator and optional On-Demand Cooling make overheating a thing of the past. The fleet management system helps PRI Group monitor usage of each forklift in its fleet, ensuring that the planned maintenance schedule is routinely observed.
The durability and performance of the C-5 Series LPG forklift, paired with maintenance alerts generated by the fleet management system, has helped PRI Group reduce its overall maintenance costs by up to 60 percent.
Recycling environments are no ordinary environments. That’s why it’s important that the forklifts used in these facilities are no ordinary forklifts. They need to be designed and built to withstand the rigors of this environment to minimize downtime and keep their operators safe and productive.
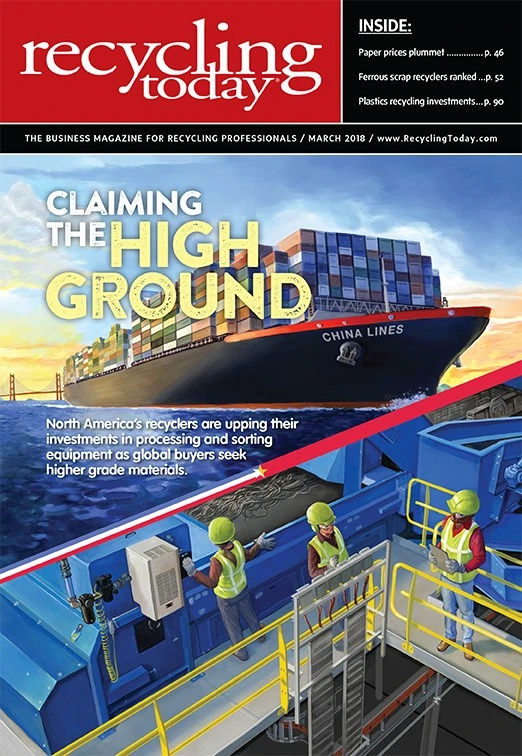
Explore the March 2018 Issue
Check out more from this issue and find your next story to read.
Latest from Recycling Today
- Sofidel agrees to purchase Royal Paper assets
- US Plastics Pact report charts expansion path for recycled content in packaging
- USTR announces phased measures designed to address China’s shipbuilding dominance
- APR, RecyClass release partnership progress report
- Clearpoint Recycling, Enviroo sign PET supply contract
- Invista expanding ISCC Plus certification program
- Redwood partnership targets recycling of medium-format batteries
- Enfinite forms Hazardous & Specialty Waste Management Council