
The recycling industry has acknowledged for several years what national statistics have borne out: The occurrence of serious injury and fatality (SIF) accidents in the sector is out of proportion to its size.
Trade groups including the National Waste & Recycling Association (NWRA), the Solid Waste Association of North America (SWANA) and the Institute of Scrap Recycling Industries (ISRI) have created programs and educational materials in attempts to measurably reduce such tragic incidents.
Kristen Bell, a partner with Ojai, California-based Krause Bell Group, says the waste and recycling industry might not enjoy complete consensus on how to address the issue, but adds, “What we’ve learned through research is that if you want to prevent fatalities—and that’s usually the first goal—that requires a special focus on situations that lead to fatalities and life-altering incidents.”
Words and deeds
As the waste and recycling industry has produced materials and messaging to address workplace safety issues, the word “culture” has been applied generously to the list of factors that can create the needed improvements.
Bell says establishing a strong safety culture includes everyone—executives, site managers, employees and even customers and vendors.
“What’s not well-understood is how each person connects to reducing risk in their organization or creating that culture. That can be difficult for people to understand,” she says.
The industrywide attention to safety has led to more frequent meetings devoted to the topic, but, Bell says, if employees “have a safety chat in the morning” followed the rest of the day by talk of adhering to schedules and “how quickly can we get this material processed,” that second message is the one employees will internalize.
“There is a role for every single person in the organization to create a safe workplace,” she continues. “Everyone is connected to it, even people outside the company.”
That being said, Bell acknowledges that executives might be in a position to influence safety in ways they do not always consider.
For example, Bell notes the impact of hiring for an operations or facility management position and asking about the candidate’s qualifications or intentions to emphasize safety. “One of the most important decisions an executive or manager can make relative to safety is who they hire—it’s crucial,” she says.
The company that hires a manager who is an excellent safety leader also is likely to be happy with that person’s leadership in general, according to research conducted by Krause Bell.
“The same type of employee who feels safe and supported by his or her leaders also coincides with the type who will put his or her best effort forward, and the business will thrive,” Bell says. “Being reassured that the effort that goes into safety improvement will benefit the business in general is a big deal. [That happens] through culture.”
A clear motive
Awards and other forms of recognition often are part of corporate and organization safety programs, and some choose to reinforce or incentivize this with a financial reward.
When it comes to the recognition aspect, Bell says her company indeed views it as helpful to recognize good safety practices and track records, “especially when people go out of their way to do the right thing.”
As far as financial incentives, Bell says, “They are very, very tricky. You could easily incentivize the wrong behavior, and you shouldn’t have to pay people or bribe people to work safely.”
Rather, Bell says of employees at all levels, “We’re already motivated to protect ourselves and each other. We want to protect people and keep them from being injured. If nothing else, we’re going to keep people whole and alive and not having a life-altering injury.”
With that motivation being essentially intrinsic, Bell says her firm’s experience is that incentives such as gift cards or raffle contests are “not really necessary and can be harmful.”
Budgets and attention might be better focused on messaging that builds a safety culture from top to bottom. “Every minute of every day is sending a message about safety,” she says. “We want to develop great awareness of the impact of our messages on people and how they’re hearing [these messages].”
For executives and managers, “It means we’re creating culture every time we’re interacting with someone,” Bell continues. “It’s kind of daunting as a leader. The implication is we have immense power, and we may not realize how we’re affecting people.”
Communication on safety is not a one-way street. While company leaders can endorse a safety message, they cannot create a culture alone.
Feedback loop
In the recycling sector, associations produce materials that are made available to member companies. Posting and distributing such materials, however, might only be a half measure. “Our experience is [employers] are sending plenty of that material out, but there needs to be more listening,” Bell adds.
Her advice to executives and facility operators is to be more in tune with what their workforces are communicating: “Focus more on what you’re hearing from other people; focus on getting messages percolating up from your workforce. It will help improve your safety and your culture.”
The importance of listening extends to daily or weekly safety meetings. “You want to have a safety meeting that is a conversation. Ideally, you won’t be waiting until the end for questions. You’d be formatting it as a dialogue,” Bell says.
Most Krause Bell clients hold such meetings “every single day and before every big task,” she adds.
Managers who are seeking out and hearing safety concerns might be more likely to keep the topic in mind during their own workdays. The attention to safety then might more easily extend beyond staff to regular facility visitors.
Bell adds, “Every interaction you have with a delivery driver or a customer is an opportunity to influence them. What do they see at the gate? What do they hear from the person at the [scale house] booth? For a vendor, it can be what is in the contract. Every interaction is a chance to influence.”
Underlying the cultural aspects, she says companies need to be keenly aware of just where the SIF risks lie. “A really great place to start is with senior leaders asking the question: How much exposure to SIFs do we have?” This can be especially crucial when looking from the vantage point of employees “who are just starting out,” Bell says.
Despite efforts to make workplace safety a focus in recent years, national workplace SIF statistics have too often demonstrated the recycling sector remain a dangerous place to work.
Pointing to the oil and gas industry as one example, Bell adds, “The good news is, other industries have paved the way toward better safety; we can apply what we’ve learned.”
Get curated news on YOUR industry.
Enter your email to receive our newsletters.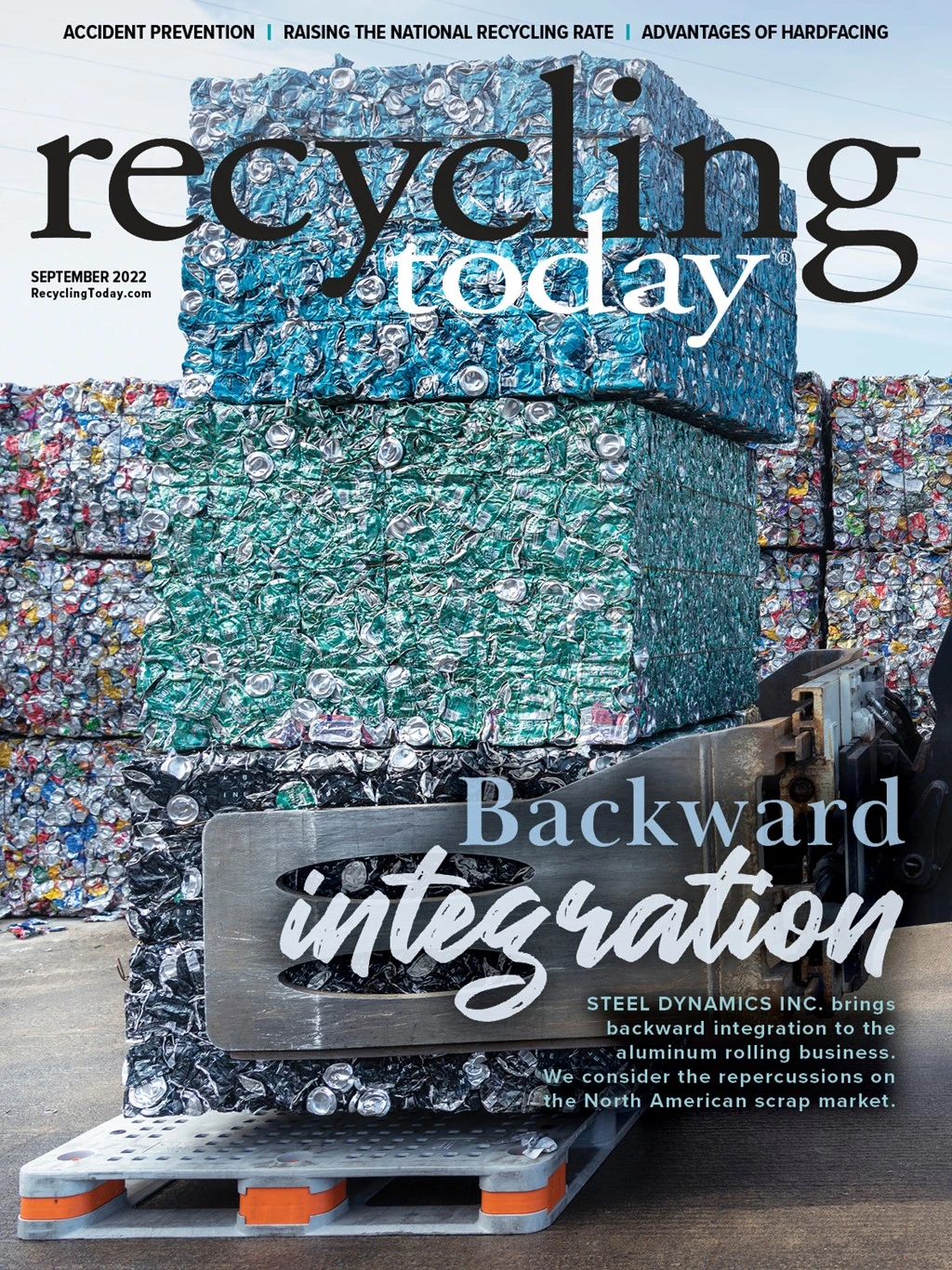
Explore the September 2022 Issue
Check out more from this issue and find your next story to read.
Latest from Recycling Today
- European project yields recycled-content ABS
- ICM to host co-located events in Shanghai
- Astera runs into NIMBY concerns in Colorado
- ReMA opposes European efforts seeking export restrictions for recyclables
- Fresh Perspective: Raj Bagaria
- Saica announces plans for second US site
- Update: Novelis produces first aluminum coil made fully from recycled end-of-life automotive scrap
- Aimplas doubles online course offerings