A little over a year ago, Eureka Recycling was faced with a major pre- dicament. The Minneapo- lis-based recycling firm had to figure out how to improve the purity of its recyclables and handle an increase in volume at the same time. Luckily for Eureka, it knew exactly where to turn.

Machinex Technologies was its go-to company, and for good reason. The Plessisville, Quebec-based recycling equipment manufacturer had a history of working with the firm and its staff. It knew precisely what needed done and how to get it done efficiently. In late 2016, Machinex installed a MACH ballistic separator, a scalping screen and an eddy current separator to Eureka’s existing single-stream materials recovery facility (MRF).
The combination of equipment addressed Eureka’s two primary goals. The first was to maintain and improve fiber purity, and the second was to increase efficiencies in preparation for increased volumes from its new contract with the city of Minneapolis and renewed contract with the city of Saint Paul. Running the extra loads on the existing system had the potential to impact quality.
A ‘no-brainer’
Eureka Recycling is a nonprofit social enterprise that’s mission is to demonstrate waste is preventable not inevitable. “Our Zero Waste mission informs how we operate our MRF, from paying our employees a living wage with benefits and paid time off to using best management practices towards achieving high-quality material,” Kate Davenport, Eureka Recycling co-president, says.
Achieving the high-quality material that is so important to Eureka’s business model requires well managed employees as well as equipment that can meet the performance standards. Eureka Recycling was well aware of that fact when it made the switch from a dual-stream system to a single-stream system supplied by Machinex in 2014.

When Eureka Recycling won the contract to process Minneapolis’ recyclables in 2016, Eureka wanted to increase the efficiency of the system by increasing throughput by 30 percent. At the same time, Eureka has a long history of quality material so maintaining and improving purity was just as important.
When it came time to decide which company to turn for help solving Eureka’s processing challenges, Davenport says, “It was a no-brainer.”
“Machinex has been a key partner since installing the single-stream system,” Davenport says. “They weren’t just the equipment vendor, but a true partner who works with us on a regular basis on continuous process improvement.”
“We have been able to increase our tons per hour by 35 percent and have decreased our already low cross contamination of our paper by 40 to 50 percent.” – Kate Davenport, co-president, Eureka Recycling
Eureka moment
Not only did Machinex have the solution, it also made a concerted effort to install the additional equipment in a manner that would minimize disruption to the operation. Machinex spent a couple of long weekends in November 2016 installing the new equipment and built the addition largely in parallel to the existing system to further reduce downtime.
Machinex added a scalping screen after the old corrugated container (OCC) line and before two newspaper (ONP) screens. The scalping screen removes the 5-inch-minus materials and directs it to the second, new ballistic separator.
This addition allows the ONP screens and the original ballistic separator to produce a better-quality fiber and process a higher capacity. It is possible because the 5-inch-minus materials—a stream with a high concentration of containers and contaminants—have already been removed.
Sponsored Content
Labor that Works
With 25 years of experience, Leadpoint delivers cost-effective workforce solutions tailored to your needs. We handle the recruiting, hiring, training, and onboarding to deliver stable, productive, and safety-focused teams. Our commitment to safety and quality ensures peace of mind with a reliable workforce that helps you achieve your goals.
Sponsored Content
Labor that Works
With 25 years of experience, Leadpoint delivers cost-effective workforce solutions tailored to your needs. We handle the recruiting, hiring, training, and onboarding to deliver stable, productive, and safety-focused teams. Our commitment to safety and quality ensures peace of mind with a reliable workforce that helps you achieve your goals.
Sponsored Content
Labor that Works
With 25 years of experience, Leadpoint delivers cost-effective workforce solutions tailored to your needs. We handle the recruiting, hiring, training, and onboarding to deliver stable, productive, and safety-focused teams. Our commitment to safety and quality ensures peace of mind with a reliable workforce that helps you achieve your goals.
Sponsored Content
Labor that Works
With 25 years of experience, Leadpoint delivers cost-effective workforce solutions tailored to your needs. We handle the recruiting, hiring, training, and onboarding to deliver stable, productive, and safety-focused teams. Our commitment to safety and quality ensures peace of mind with a reliable workforce that helps you achieve your goals.
Sponsored Content
Labor that Works
With 25 years of experience, Leadpoint delivers cost-effective workforce solutions tailored to your needs. We handle the recruiting, hiring, training, and onboarding to deliver stable, productive, and safety-focused teams. Our commitment to safety and quality ensures peace of mind with a reliable workforce that helps you achieve your goals.
Sponsored Content
Labor that Works
With 25 years of experience, Leadpoint delivers cost-effective workforce solutions tailored to your needs. We handle the recruiting, hiring, training, and onboarding to deliver stable, productive, and safety-focused teams. Our commitment to safety and quality ensures peace of mind with a reliable workforce that helps you achieve your goals.
A new Machinex eddy current separator was the last part of the upgrade. Not only does its addition further remove aluminum from the paper, it increases the recovery of that high-value nonferrous commodity.

Davenport couldn’t be happier with the results a year later. She says throughput is up and less aluminum and PET (polyethylene terephthalate) are getting into the paper grades. “We have been able to increase our tons per hour by 35 percent and have decreased our already low cross contamination of our paper by 40 to 50 percent.”
Looking ahead
As Eureka continues to adapt to stricter requirements and the changing materials stream, Davenport sees Machinex as a critical ally. The relationship helps Eureka Recycling keep up with recycling’s evolution while staying committed to its mission.
“Eureka believes that we recycle not just to reach a diversion goal, but to truly contribute to the decrease in extraction of natural resources. Thus, material quality, low residual and the ability to sell material into its highest and best use is in our core daily management practices,” Davenport says. “Machinex continues to be a key partner to help us design our system to achieve those objectives and to help us develop metrics and dashboards to continuously optimize our system.”
Get curated news on YOUR industry.
Enter your email to receive our newsletters.
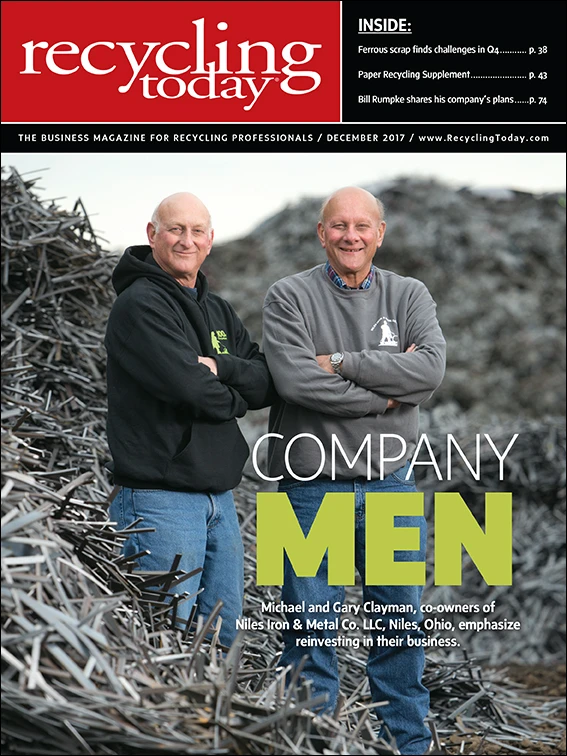
Explore the December 2017 Issue
Check out more from this issue and find your next story to read.
Latest from Recycling Today
- Athens Services terminates contract with San Marino, California
- Partners develop specialty response vehicles for LIB fires
- Sonoco cites OCC shortage for price hike in Europe
- British Steel mill’s future up in the air
- Tomra applies GAINnext AI technology to upgrade wrought aluminum scrap
- Redwood Materials partners with Isuzu Commercial Truck
- The push for more supply
- ReMA PSI Chapter adds 7 members