

Recycling glass at the curb has been commonplace since the 1990s. If you remember the famous Labrie truck, you also will remember employees source separating recyclables on a truck at the curb. The side bin containing the source-separated materials would ascend the side of the truck, dumping the commodities with a resounding crash of broken bottles. This was music to the bottling and fiberglass insulation industries, which demand cullet in their manufacturing processes.
Fast forward a few years, and most curbside recycling programs in the country adopted single-stream collection at the curb, allowing all acceptable commodities to be commingled in the same bin. This created a significant increase in the amount of recyclables collected and made separation the responsibility of the material recovery facility (MRF). With advances in sorting, MRFs became highly technical, allowing commodities to be sorted using conveyors, eddy currents, optical sorters and, now, robots. The advances in technology and the single-stream collection system assisted in increasing the quantity of each commodity recovered.
Changing rebate games
The recycling industry is rooted in economics, with fluctuations in supply and demand ultimately affecting commodity values and pricing.
For years, MRF operators had convivial relationships with their customers, often “sharing” the upside of commodity values with them. However, with the economic downturn in 2008-2009, commodity values were so low that suddenly haulers and MRFs began eliminating certain commodities from their “acceptable materials list,” glass being one.
Within the next decade, in an effort to protect revenue, haulers and some MRFs began to renegotiate contracts with their customers. In some cases, the new contracts reflected the new cost of processing recyclables, and much of the revenue sharing that once existed with customers disappeared, or the financial thresholds could not be met. Customers were now paying more to have recyclables processed and recovered, in the $100-plus per ton range in some cases.
Better cleaning equipment
Artificial intelligence, optical sorters, robots and peopleless MRFs are changing sorting in the recycling industry. While some programs removed glass in the recent past, the equipment industry did not give up on designing and further developing equipment aimed at glass recovery. Improvements were made by strategically placing glass-cleaning equipment. Once glass was removed from the stream at the beginning of the process, it was less likely to be an impediment to the MRF.
Manufacturers designed better trommel screens to produce cleaner glass output at MRFs, creating a slightly higher value before transporting the material to a secondary glass processor.
These technological advances, coupled with renegotiated contracts, where MRFs now were getting paid to process material, allowed a second look at the economics of glass recycling.
Return on investment
Return on investment (ROI) for glass-cleaning equipment is important. According to The Recycling Partnership’s “2020 State of Curbside Recycling Report,” glass makes up 20.4 percent by weight of residential curbside-collected recyclables. If the glass processor is nearby, charges for further cleaning the glass often are less than what it costs to dispose of the glass in a landfill.
In a scenario in which MRFs accept glass, proper glass-cleaning equipment investment, maintenance costs, transportation costs and diverted landfill savings can be calculated to determine the true ROI of keeping glass in the collection stream. The data can be compared with the per-ton glass processing cost to make an economically based argument for glass inclusion.
The New York-based Closed Loop Foundation says glass cleaning equipment can cost $350,000 to $1 million but often has an ROI of within two years.

Source-separated collection
Curbside residential glass collection provides for greater quantities of glass to be recycled, but an additional step is required to clean the glass and separate the cullet by color in some cases before it is made into new products. Another collection method uses 20-, 30- or 40-cubic yard containers. These containers accept glass either as mixed colors or sorted by individual colors. The collection method chosen is most likely determined by the technology at the local glass processor. More advanced technology includes the use of optical sorters to separate glass by color.
While the recovery of source-separated glass does not result in similar recovery by population when compared with the convenience of curbside single-stream collection, the resulting glass is much cleaner and could be sold directly to market.
Several companies have realized the value of being associated with glass recycling and are entering the market to provide source-separated glass collection. They are proactively recruiting sponsors that can have their logos on containers, providing marketing not only at the drop-off facility but also in transport to the glass processing facility.
Supporting zero-waste goals
As municipalities develop zero-waste goals and residents demand more recycling, it is important to understand glass’ role. A poll by The Glass Recycling Coalition, Ann Arbor, Michigan, shows 91 percent of respondents would like to see glass recycled. Removing glass from a typical curbside program would cause municipal recovery rates to decrease by around 20 percent by weight. Filling that void with another easily recycled commodity in a curbside program would be difficult.
The use of recycled glass reduces emissions and decreases the quantity of virgin raw materials used in the manufacturing process. Whether the glass is made into more bottles, fiberglass insulation or other products, the energy used is significantly less when compared with using virgin materials. According to the Glass Packaging Institute, Arlington, Virginia, more than 1 ton of natural resources are saved for every ton of glass recycled. When higher quality glass cullet is recovered, end markets have a more sustainable supply, resulting in more high-quality end uses.
Many industries want more recycled glass. Sometimes it takes more communication throughout the recycling value chain, wherein the hauler, the MRF, the glass processor, the municipality, the policymakers and the end markets identify mutually beneficial outcomes. For a commodity that is endlessly recyclable, we must identify an economically viable path beyond the landfill.
Get curated news on YOUR industry.
Enter your email to receive our newsletters.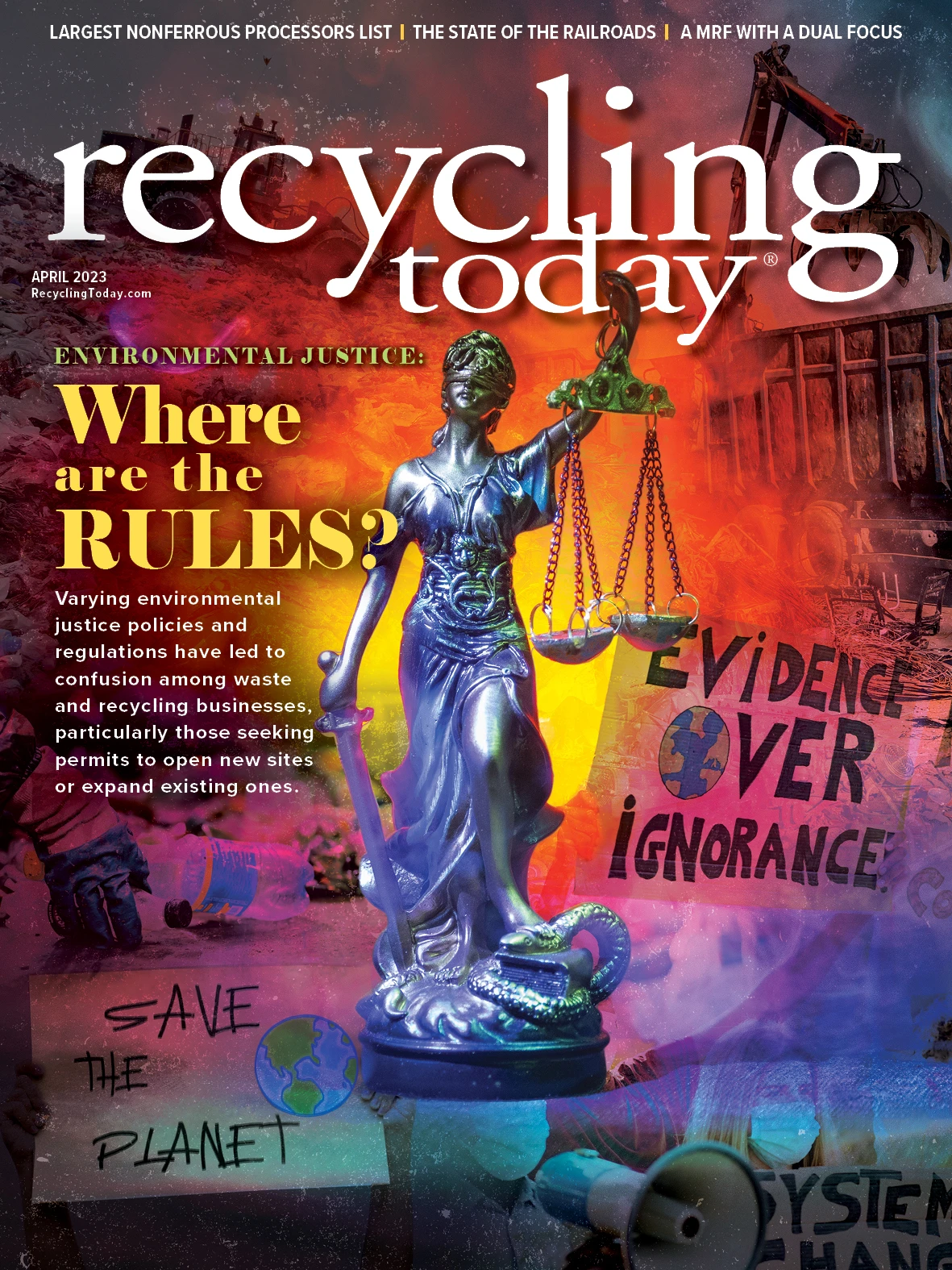
Explore the April 2023 Issue
Check out more from this issue and find your next story to read.
Latest from Recycling Today
- Athens Services terminates contract with San Marino, California
- Partners develop specialty response vehicles for LIB fires
- Sonoco cites OCC shortage for price hike in Europe
- British Steel mill’s future up in the air
- Tomra applies GAINnext AI technology to upgrade wrought aluminum scrap
- Redwood Materials partners with Isuzu Commercial Truck
- The push for more supply
- ReMA PSI Chapter adds 7 members