
quicker and easier to remove ferrous material captured by its high-strength
tube magnets.
Bunting Magnetics Co., a Newton, Kansas-based company that designs and manufactures magnetic separators, metal detectors, material handling and magnetizing equipment with locations in the United States, United Kingdom and China, has developed a quick manual-clean magnet insert it says significantly reduces the time needed to clean captured ferrous material off high-strength tube magnets, and an early user says the new equipment is improving its resin quality.
MBA Polymers UK, part of United Kingdom-based EMR, installed Bunting’s quick-clean FF-MSCI system into one of its existing drawer filter magnets at its plastics recycling facility in the town of Worksop, England. The facility is one of the largest in the world that focuses on shredder residue—a byproduct from the shredding and metal recovery processes for end-of-life appliances, automobiles and other large metal-bearing goods that traditionally are recycled for their high metal content. Shredder residue also frequently is sent to landfills.
The Worksop recycling facility uses four Bunting drawer filter magnets. Each drawer filter magnet contains two rows of high-strength, rare earth neodymium tube magnets mounted in a sealed outer housing. Shredded plastic measuring less than 6 millimeters falls from the top of the drawer housing and over the tube magnets. Metal-free material falls past the tube magnets, while metal particles are captured.
The tube magnets periodically must be removed so captured metal can be cleaned off, and the high strength of the tube magnets sometimes makes removal of the metal contamination difficult and time-consuming. The potentially piercing nature of the metal also can pose a safety risk.
But the new quick-clean magnet insert fits into the existing drawer filter magnet, and operators can remove the entire insert and pull the tube magnets through a front cover made of Perspex—an acrylic plastic—which scrapes the metal bits off the magnets, while plastic washers block metal from moving outside the housing. As the tube magnet is withdrawn completely, the captured metal no longer is magnetically held and falls into a collection chute.

40-second task, and operators don’t have to clean metal by hand.
Bunting says cleaning a tube magnet grid takes about 40 seconds with the new insert and, because operators do not have to remove the captured metal from the surface of the tube magnets by hand, the insert is safer to use than more traditional methods.
“With the new magnet system, we can ensure that contamination is removed prescreen, allowing an even higher-quality product,” Guy Hughes, extrusion manager for MBA Polymers, says in a news release.
A Bunting spokesperson says the FF-MSCI can be used in applications that include recycling, compounding, injection molding and extrusion.

It can be specified when a new magnetic drawer system is purchased or
retrofitted into an existing drawer.
The FF-MSCI fits Bunting’s FF4, FF6 and FF8 magnetic drawer housings and it can be specified when a new magnetic drawer system is purchased or retrofitted into an existing drawer.
“It is a simple solution for a longstanding problem,” Bunting Sales Manager Bradley Greenwood says in a September 2023 blog post on the manufacturer’s website. “However, our aim was to design the insert so it can be easily fitted into existing FF drawer filter magnets. Our FF drawer filter magnets operate successfully for long periods with no reason for replacement. With the insert, customers can simply replace the front plate for simpler and safer metal cleaning.”
WANT MORE?
Enter your email to receive our newsletters.
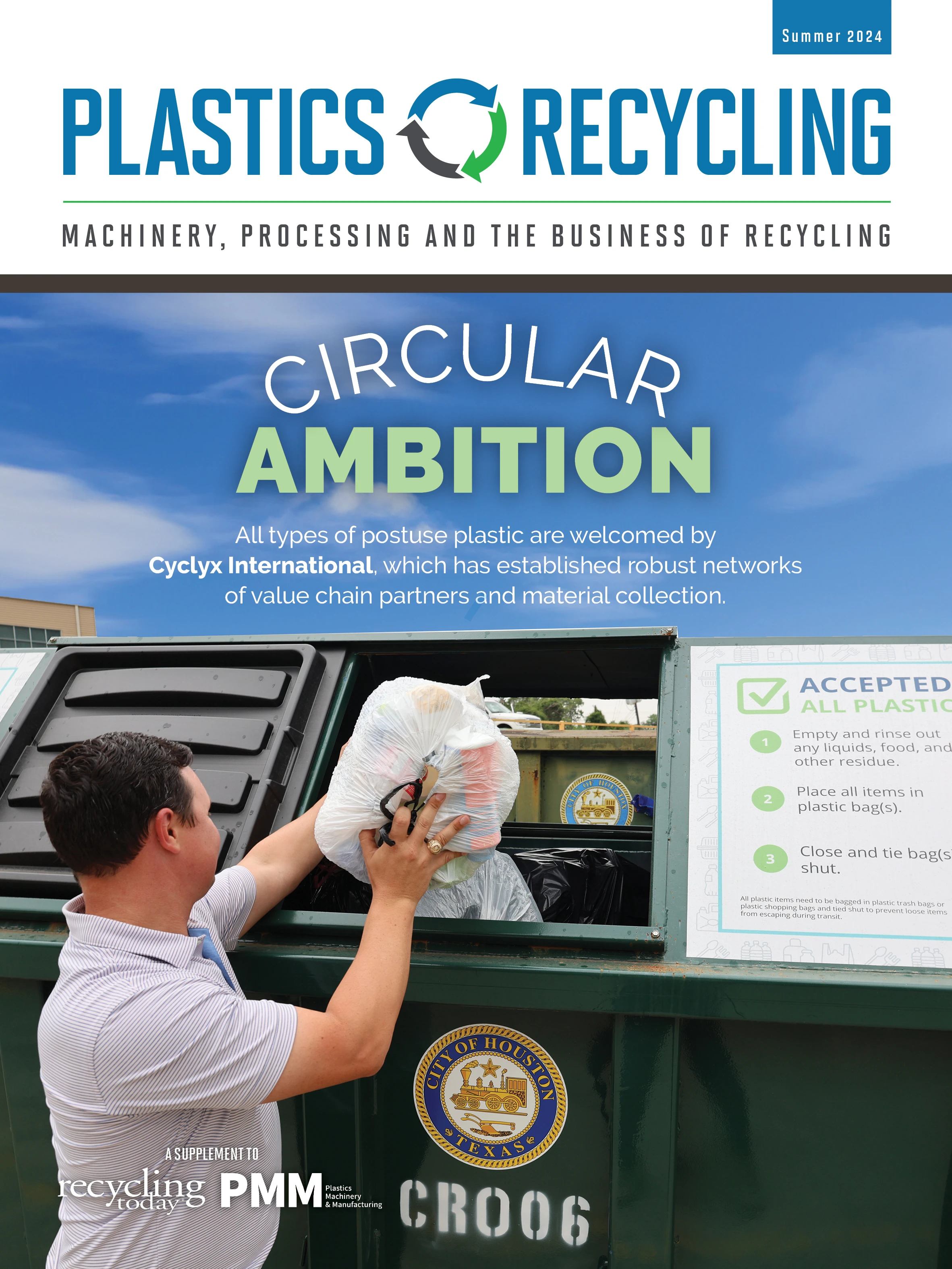
Explore the Summer 2024 Plastics Recycling Issue
Check out more from this issue and find your next story to read.
Latest from Recycling Today
- WM to debut 4 recycling, RNG projects
- Celsa Group welcomes new Spanish investor
- Ferrous price hikes could be poised to pause
- BIR prepares for Spanish exhibition
- Copper exempted from latest round of tariffs
- Interchange Recycling's EPR stewardship plan approved in Yukon
- Making the case for polycoated paper recovery
- Novolex, Pactiv Evergreen finalize merger