From the packaging of 10-ounce grocery items to sizable automotive parts, the plastic industry has enjoyed market share gains almost across the board in the 1990s. But as more plastic is used, will more plastic also be buried in landfills? Or will innovators both within and outside of the plastic industry increase the attention being paid to plastics recycling?
SEVEN DEGREES OF SEPARATION
The supply, demand and pricing structure for recycled plastic varies greatly depending on the resin used. The telltale symbol and number on the bottom of plastic containers and products denotes a tremendous difference to processors of plastic scrap.
The very separate markets for PET #1, HDPE #2, PVC #3, and the other four categories move in their own directions based on demand, pricing, and recyclability. And even beyond the seven resin categories, differences within a resin type based on color, purity of sorting, and degree of processing can further complicate the picture.
In terms of demand and the establishment of a recycling infrastructure, clear PET and HDPE are among the more mature markets. Gerry Claes of Graham Recycling, York, Pa., said of PET earlier this year, "Most plastic recyclers cannot get enough material to keep their plants running at capacity. A few years ago, the problem was finding end markets. Today, there is plenty of demand for recycled plastic but not enough is being collected."
Alan D. Logan, marketing manager for Ensley Corp., North Canton, Ohio, says his company also works hard to procure adequate post-consumer HDPE supplies. "There’s never really been [an overabundance] available," says Logan. "We need more collection. The demand is there for recycled HDPE containers—there’s more demand than there is supply." Logan adds that Ensley Corp. has "brought in raw feedstock (post-consumer containers) from as far away as Vermont" to its North Carolina plant.
One of the largest processors of scrap HDPE baled bottles is the KW Plastics Recycling Division in Troy, Ala. General manager Arthur Ferguson says the company has accepted scrap from throughout North America and beyond. "We take it in nationwide. We have also imported from Europe, Mexico and Canada," he remarks.
Like Logan, he feels the collection percentage can be improved. "There’s plenty of plastic out there, but it’s just not being collected. It’s a four billion pound per year industry," Ferguson says of the HDPE container and film market.
Logan is certain—and packaging industry statistics back him up—that the plastic containers exist to keep post-consumer HDPE processors and consumers well stocked. "What everybody needs to do is get the word out directly or through trade associations to the public and to grass roots collectors that we need more collection and that there are markets for the material," he remarks.
While end markets for PET and HDPE are fairly well established, the markets for other resins are often far spottier. PVC in particular has been singled out by some as the plastic compound with the least chance of finding a second home with recyclers. Earlier this year, PVC was pointed to as a recycling non-performer by the Association of Postconsumer Plastic Recyclers, Washington.
"We are being told that it is not economically feasible to convert PVC bottles into pellets. We say that it is too expensive for us to process PVC bottles only to throw them away. It’s time to tell it like it is: PVC bottles have no place in post-consumer plastic bottle recycling," APR board member Gary Pratt, who is also president of P&R Recycling Industries Inc., Youngsville, N.C., declared in an APR press release.
The Vinyl Institute, Morristown, N.J., says it is taking steps to find end markets for post-consumer PVC, and points to a project it is undertaking with East Coast Recycling Associates, Millville, N.J., and several flooring manufacturers to develop a tile product using post-consumer PVC bottles.
THE PRICE ISN’T RIGHT
No matter what type of demand exists for a given recycled plastic commodity, pricing seems to be uniformly disappointing. Pennies-per-ton pricing continues to make plastic processing a difficult business proposition.
While prices have never been dramatically high for post-consumer containers or the resins produced from them, some upward momentum that had been building in early 1998 reversed during the summer. "Plastic scrap got priced rather high due to the demand side all through the spring and early summer," says Logan. "Scrap was bid up proportionately high to what it should have been. Just one or two players bowed out and the whole thing came down like a house of cards," he continues. "We saw that fall start in the first week of June. It’s been getting progressively worse ever since then." Logan cites "the overcapacity of PET worldwide" as a critical factor in price drops.
The primary mechanism that keeps scrap plastic and secondary resin pricing low is the continuing affordability of virgin plastic resins. Even manufacturers with good intentions who might consider using secondary resins seem to hold off in the face of the continuing affordability and availability of virgin resins—a commodity they are familiar with and used to working with.
The depressed pricing structure has been tough on processors like Ensley Corp. "It makes it difficult," says Logan. "You try to maintain the same margin. It makes it difficult to buy the raw materials—you can’t offer the price you would like. It’s very tough to compete against the low virgin prices. We’re hoping for a resin price increase to take hold."
At KW Plastics, Ferguson says the company also faces challenges due to pricing. "Right now, the market is pretty depressed because of the availability of lower-priced virgin material. We have survived but it hasn’t been as good as it has in the past."
KW Plastics faces competitive pressures for what it can charge for its pelletized product, but can also pay less for its baled plastic scrap when markets are down. "The pellet price seems to always fall more rapidly than the bale price, so it seems like you’re always trying to catch up. But you lose on one end and try to make it up on the other," he says.
Those collecting plastic scrap are suffering the most in the down market, both Ferguson and Logan seem to agree. "Right now, MRFs are taking the hit for the fall in prices," says Logan. "We need to spread that out."
MORE END MARKETS EMERGING
If the key to the long-term viability of plastic recycling is a sizable end market, then there is some good news to be found. Entrepreneurs throughout North America are finding uses for recycled plastic resins in a broad range of applications.
Dura Products International Inc., Toronto, is using a mixture of roughly 50% wood cellulose wood fiber and 50% HDPE flake to make Duraskid pallets. The composite pallets have met a friendly reception in the marketplace, according to Duraskid president Craig Prentice. "The cellulose mixed with the plastic increases the strength of the pallet, so you can rack large loads, even in extreme temperatures. Yet the pallets also have the resiliency to take hits and be dropped, which of course happens with pallets," says Prentice.
The company currently operates a pallet-making plant in Toronto, and is in the process of retrofitting a building in Andover, Mass. as its second Duraskid production facility. According to Prentice, each facility will take in 800 tons of HDPE per month at peak production. (Prentice also notes that the manufacturing process has been designed to accept other types of plastic if desired or necessary.)
Currently, Duraskid is taking in a mixture of post-consumer and industrial plastic scrap. "It’s a moving target," Prentice says of the post-consumer percentage. "Right now most of our plastics are post-industrial, but our plans are to use more post-consumer. We have purchased a wash line which is not yet installed," he notes.
The company’s officers believe global growth is possible for the Duraskid product. The company is making plans not only to open more plants beyond the Toronto and Andover facilities, but is also considering joint ventures "We’ve had huge interest from Europe, South America and Asia," says Prentice. "We get two or three serious inquiries from around the world a week. We’re pursuing them, but we’re focusing on North America first," he adds.
Will the company remain true to recycled plastics if it adopts a rapid growth mode? "Of course we could use virgin resins, but we’re an environmental company," says Prentice. "That’s a big part of our mission and our philosophy. I don’t see a circumstance where we would use virgin materials."
The company has also designed its manufacturing process to accept returned Duraskid pallets for recycling.
In Schaumburg, Ill., A. George Staniulus founded AGS Technology Inc. three years ago to take advantage of what he felt was a widely available and affordable commodity—scrap plastic. The company uses an injection molding process to turn scrap plastic flake into such items as automotive interior parts, children’s furniture and plastic piping.
"Right now we’re using a lot of HDPE flake, some polypropylene and some engineered plastics," says Staniulus. "We purchase based upon what we need to manufacture for our customers. It does change. We buy based upon quality and price, whether it’s post-consumer or post-industrial we really don’t differentiate. We want it to be of a certain density and a certain cleanliness. How our suppliers achieve that is up to them."
For AGS, scrap plastic is being used because it makes economic sense. "We use scrap plastic for price reasons," says Staniulus. "The environmental reasons are a plus—it’s frosting on the cake. What drives the whole thing is economics. We win business based on the differential of recycled cost versus the cost of virgin materials. In injection molding, 40% to 60% of the cost is in the raw material. If you can shave off raw material costs, you can benefit as a company."
Staniulus says that right now the company is seeing a cost advantage in the engineered plastics segment in particular. "We’re seeing bigger differences there for scrap over virgin—more like 40 cents per pound instead of 15 cents per pound."
EMPTYING BOTTLES INTO THE RECYCLING STREAM
While some plastics processors see a shortage of material as a problem, scrap consumers have not seemed to perceive such a shortfall.
In Toronto, Duraskid’s Prentice says, "there’s a good supply here—far beyond what we would need for this facility. We did our research into the Boston market as far as the raw material side. There’s enough collection in both markets."
And in Illinois, Staniulus says, "availability is never a problem."
He believes that technology advances will need to continue for the plastic recycling rate to match that of aluminum cans or other forms of scrap metal. "The problem is developing the right markets for the material. You have to remember in plastics, sooner or later—and usually sooner for packaging—the part has served its function and is available for recycling. The economics involved in extracting the material from the waste stream and converting it into a useful form has been the challenge."
Staniulus says AGS has "been able to streamline that process and make the recycling more cost-effective" by routing scrap flake directly into a man-ufacturing process without using an outside company to perform an extrusion or pelletizing step. "We’ve been able to carve out that middle operation and combine that middle step with our molding. Now some of the commodities that were not economical to recycle before maybe can be recycled."
Major corporations such as The DuPont Co., Wilmington, Del., and British Petroleum, London, are pioneering methods that might completely change the way plastic is recycled in the future.
DuPont has developed a method to convert some polyester-based items into reusable liquid chemicals. The Petretec process has been used with scrap Mylar window film. According to DuPont’s Mary Ruth Johnson, "the Petretec process unzips the polyester molecule and breaks it down into its raw materials. Because these monomers retain their original properties, they can be reused over and over again in any first-qualty application. A popcorn bag can become an overhead transparency, then a polyester peanut butter jar, then a snack food wrapper, then a roll of film, then a popcorn bag," she says.
The BP Chemicals division of British Petroleum is planning a facility in Scotland that will recycle 2,000 metric tons per month of mixed plastic by shredding it and then breaking polymer molecules down into petrochemical feedstock through what the company is calling a "polymer cracking" process. According to the British trade magazine Materials Recycling Weekly, construction of the plant may not proceed until the year 2001.
Whether through steps such as Staniulus’ or due to a leap by a corporate giant, such advances are what is needed to put plastic recycling into a fast forward gear.
The author is managing editor of
Recycling Today.Upping the Recycling Rate
Please recycle your empty bottles—the end markets exist. That was the message the American Plastics Council (APC), Washington, brought to Americans this past Earth Day. The trade organization asked Americans to "pitch in and recycle more plastics to help close the gap between the strong demand for recycled plastics and the amount being collected."
While price structures in no way reflect it, there is a strong demand for particular post-consumer containers, including clear PET and HDPE bottles. "While collection of HDPE milk and water bottles has been strong in communities that collect plastics, capture rates for many detergent, shampoo and fabric softener bottles are much lower," according to the APC.
As of press time, a comprehensive study sponsored by APC and the Charlotte, N.C.-based National Association for PET Container Recovery (NAPCOR) has not been released. But plastic recycling trade groups seem unified in their efforts to increase collection rates of post-consumer plastic.
The Association of Postconsumer Plastic Recyclers (APR), has designed a process that it hopes will be adopted by packaging manufacturers. The "Champions for Change" program is geared toward helping package designers create containers that can be recycled by plastics processors. "In the past, recyclers have had to settle for what packaging manufacturers have handed down to them," says APR chairman Dennis Sabourin, who is also vice president with Wellman Inc., Shrewsbury, N.J. "APR’s future direction will be to strengthen its position in the industry with regard to how packaging will be designed for recyclability."
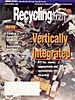
Explore the September 1998 Issue
Check out more from this issue and find your next story to read.
Latest from Recycling Today
- Aqua Metals secures $1.5M loan, reports operational strides
- AF&PA urges veto of NY bill
- Aluminum Association includes recycling among 2025 policy priorities
- AISI applauds waterways spending bill
- Lux Research questions hydrogen’s transportation role
- Sonoco selling thermoformed, flexible packaging business to Toppan for $1.8B
- ReMA offers Superfund informational reports
- Hyster-Yale commits to US production