"I should have bought one 10 years ago!" That was the reaction of Bob Weinstein, owner of Bob’s Metals Inc., Portland, Ore., when asked to assess the benefits of his metal analyzer.
Bill Fisher, director of U.S. Operations for ELG Metals Inc., McKeesport, Pa, says the several instruments ELG owns are "an integral part of our business. We utilize them every single day to determine whether or not the material is what it’s supposed to be and what we are supposed to ship to our end consumer."
Bob’s Metals is a one-man operation. ELG is one of the largest stainless steel scrap recyclers in the United States. Not only these two, but also several in-between-sized recyclers, confirm the profit-building value of these instruments.
Perhaps the strongest endorsement came from a California recycler specializing in high-temperature alloys who asked not to be identified. "I don’t want it out in the industry what I’m using and how I’m using it. I don’t want to tell people how I am sorting things, why I’m sorting it and what my results are with different instruments," he says.
The instruments used by recyclers employ either of two technologies—X-ray fluorescence (XRF) or optical-emission systems (OES)—but knowing the details about how they work isn’t completely necessary.
FINDING THE "GOODIES." A primary reason metal analyzers are so widely used by recyclers—small and large—lies with the various ways in which they help recyclers generate profits.
"In the last couple of years, I’ve been getting a ton of stainless in and paying a high price… and I knew some of the lots I was buying had some better alloys in them than stainless," says Weinstein. "A couple of months ago, I went to an auction for a few hundred thousand pounds of stainless—divvied up into something like 900 lots, all merely called ‘stainless.’ I was able to go through with my (analyzer), and I picked out higher grades of stainless; I picked out nickel alloys; I picked out cobalt alloys. So it gave me an edge from the standpoint of knowing that maybe 10 percent nickel was in there—something higher than stainless. So, I was able to bid higher than the next guy," he says.
"The other place it helps is with some industrial accounts," Weinstein continues. "Once in a while they have to have a particular material in their shop for working on a finished product; and instead of them sending it out to have it analyzed—to make sure that it’s 304 or 316 or whatever—they call me. And I go down there (with my analyzer) and I do it free in the hopes that I keep the account. If someone were to call on them, they might say, ‘Bob helps us out. We don’t want to talk to anybody else.’"
Joel Denbo of Tennessee Valley Recycling (TVR) in Decatur, Ala., has his own reasons for using analyzers in the yard.
Denbo, who is also chairman of the Institute of Scrap Recycling Industries Inc. (ISRI), says, "Over my business career, we called it finding the ‘goodies.’ Our operation is what I’d call generalist. We handle a lot of non-homogeneous type materials. We see all sorts of different things coming in and we need to be able to identify what we have."
TVR used to send material out to independent labs for analysis or use an in-house spectrograph, though time was often a factor, Denbo says. "Being able to have an analyzing piece of equipment available at a minute’s notice is obviously well worthwhile. Also, being able to take the machine to the work instead of the work to the machine is a big advantage," he adds.
"If you handle any significant amount of stainless steel and if you can ferret out the different grades, obviously, it takes you down the right road. It allows you to prove or identify what something is—instead of assuming. Instead of guessing, you know what it is. They’re right expensive, but all you have to do is one or two tricks and you’ve paid for it."
Joel Fogel of Cohen Bros. Inc., Middletown, Ohio, says he uses two different analyzers. "We generally use [one] to differentiate carbon from chrome and the different stainless alloys and nickel alloys…and the other for pretty much the same purpose—although it likes aluminum and can break it down into 3000, 5000, 6000 and 7000 classes."
With respect to segregating stainless from nickel alloys, Fogel also says: "Nickel alloys, in some cases, are worth $2 to $5 more per pound than stainless ." Analyzers, which can be more reliable than grinders, help spot this key difference. Fogel says the instruments Cohen Bros. has bought "are definitely worth the money that we spent."
While analyzers can help to increase a recycler’s profitability in the long run, some recyclers may dwell on the initial investment.
INVESTING IN ANALYSIS. "The cost, probably, is a big stumbling block for a lot of people because they’re not cheap—[some are now] in the $30,000 range, I’d imagine," Fogel says of analyzers. "But, if there’s enough tonnage generated, and the smaller dealer would be handling a lot of stainless or, potentially, a lot of alloys, the payoff would be rather quick. It would definitely make sense. I would say just don’t be afraid of the price tag."
Bob Weinstein echoes Fogel’s comment about instrument prices. "Just do it, and you’ll find a way to make it pay for itself," he says. "I figured I would have this thing paid for within six years; that was my hope. Well, when stainless shot up from 25 cents to 80 cents, and you’re able to pick out 316 over 304 and you’re able to add 10 or 15 cents per pound [of value] to something, it doesn’t take that long to pay for [something] like this.
He notes that prior to the interview for this feature, the analyzer was making a profitable difference at his facility. "In fact, when you were calling me, I was checking some stuff, and on this pile there were maybe 150 pounds—but 50 pounds turned out to be 316—worth 20 cents per pound more." Weinstein says he was able to upgrade the value of material by $10. "Then there was one piece that weighed about 20 pounds and turned out to be 400 Monel. That would add maybe $25. And then one piece turned out to be 6-4 titanium. So, I would say that just for that one pallet, it probably upgraded the value by at least $50 to $75," he says.
Analyzers may also help recyclers guarantee furnace melt chemistries, i.e. guarantee that undesirable "tramp" materials are absent from a shipment. The most feasible way to accomplish that is to use an instrument that can accurately and quickly analyze a lot of material.
Guarantees of furnace melt chemistry justify a higher price for the shipments, thereby justifying the instrument’s purchase. In these cases, a company’s competitive stance rests heavily on using these analytical instruments.
CHOICE FACTORS. When asked to cite the key factors that led them to choose their analyzers, the most frequently cited factors were portability and ease-of-use.
The recyclers interviewed also cited the following factors as influencing their analyzer purchases: detectable elements; accuracy, reliability and ruggedness; response speed; suitability for use in inclement weather; price and ownership costs; and the vendor’s financial strength.
Among the costs of ownership are any potential regulatory burdens—and that burden weighed heavily on Joel Denbo. "Based upon the advent of the Homeland Security Administration, I just felt that I didn’t want to have to fool with all the government red tape associated with a nuclear source," he says. "I operate in two states and I didn’t want to have to go through a lot of regulatory red tape to register the item in both states."
Denbo continues, "We live in northern Alabama, when you cross over into Tennessee, theoretically, you’re supposed to tell them that it’s coming and all that kind of stuff. With the machine that I have, it’s just an X-ray [tube] machine; you don’t have to go through that hassle. And the licensing and whatever in the two states is much less restrictive for the type instrument that I have as opposed to the nuclear source instrument."
The instrument’s ruggedness also contributed significantly to Denbo’s choice. "(The vendor) has come up with a new type tube that is much more durable. The scrap business is still the scrap business, and we’re not in a laboratory environment; we’re out in the field. And it seemed to me, based on the information that the sales people were telling me—and we sometimes take that with a grain of salt—but they demonstrated that it’s not an item that will fail, because if you jar the old-style X-ray tube, it can break. But the one they developed will not break. That was what led me to make the decision to buy the particular item I bought."
Denbo adds, "I think they’re all high-quality instruments." He suggests looking for an analyzer that makes you think "you’re making the right choice for your own operation" based on the manner in which you’re going to use the instrument.
Arming yourself with a little knowledge and a few words of advice from other scrap recyclers may prove helpful during the selection process.
SOME CAUTIONS. ELG Metal’s Bill Fisher offers some important cautions that should be heeded by all users—old and new.
"In the world of analytical devices, we, as a major player in the field of stainless steel, have looked at literally every device that’s available. Each of the devices has merits; and unfortunately, each device has what I would call some demerits. Because of that, you need to find out whether or not a device is suitable for your particular applications," Fisher says.
"Probably the biggest caution I’d give anyone is because you see an answer on a screen, it doesn’t necessarily mean that you have an accurate answer. It takes time to know the device; it takes standards to measure against. In other words, a known certified standard to be sure that your calibration is proper for the material you’re getting an analysis on [is necessary]," he adds. "Talk to other people who have the instrument you’re potentially looking at."
Emphasizing that point, Fisher continues: "Anyone who buys one of these devices and does not get a full training course as to what the machine will do and how it responds is only kidding themselves. You can buy an instrument, turn it on and get a result. Just because you get a result does not mean it’s correct. It requires an education!"
A California alloys recycler (who wishes to remain anonymous) echoes Fisher’s advice. "We use about six different instruments to test our metals. One instrument is not good enough to do what we do. They’re all useful, but they’re all useful in different ways."
Denbo also has some advice that all users may wish to heed. "Because the instrument is expensive, we’ve limited it to supervision. I had a lanyard made for [users] to put around their necks so that they won’t drop it when they go out into the yard," he says. "And also, we have it individually insured. Something of that value that you can just walk around with or walk off with is something that [has to be protected]."
WIDER REACH. The majority of the large recyclers have been using metal-analyzing instruments for some time; some, as indicated, use several in their operations. Because there is less market saturation within the segment of the recycling industry comprise of smaller yards, a larger percentage of current sales are going to these smaller recycling firms.
Still, vendors say larger recyclers also offer significant sales—sales now generated by the replacement of isotope-based instruments by newer X-ray tube instruments. However, the hassles, red tape or regulations associated with these instruments apply to users large and small.
Despite the responsibilities and costs associated with their ownership, without question, analyzers should continue to bring financial returns to those recyclers who use them properly at their yards.
The author is a freelance writer based in Cleveland. He can be contacted by e-mail at BenNagler@sbcglobal.net.
SELECTING AN ANALYZER |
The following questions should be considered prior to purchasing a metals analyzer. 1. What alloys will be tested? While optical emission systems (OES) analyzers work well for aluminum and its alloys and for low-alloy steels, X-ray fluorescence (XRF) analyzers are considered best for high-alloy/stainless steels, nickel alloys and cobalt. 2. How should samples be prepared? To get an accurate analysis anything not representative of the material (e.g., dirt, paint and scale) should be removed. XRF instruments can be more forgiving than OES instruments. When using an OES system in arc-mode, inspection areas should be ground smoothly and consistently. 3. How easy is the instrument to use? Compared to XRF instruments, OES instruments generally need operators with a greater level of technical expertise. 4. What kinds of readouts are available? With most analyzers, the standard mode is a grade-identification followed by the chemical composition. Some users prefer a match-mode that gives only a grade identification as compared to a reference sample. Others prefer just a "Yes/No" or "Pass/Fail" reading, which is also compared to a reference sample. 5. How can the findings be recorded? All the analyzer models available can store results internally. Data can then be downloaded to a (Windows-compatible) PC. Many models will download to an Excel spreadsheet, which is importable into the Mac environment. 6. What local regulations apply to XRF instruments? In most of the United States, X-ray tubes are subject to less regulation than radioisotopes. Radioisotopes require a license, while X-ray tubes need only registration in most states. In Colorado and South Carolina, however, it’s actually easier to ship a radioisotope-based instrument and the user has less regulatory burden. In Canada, portable X-ray devices were not allowed until just recently. Still, the paperwork/regulations are stiffer than for isotope devices. |
Get curated news on YOUR industry.
Enter your email to receive our newsletters.
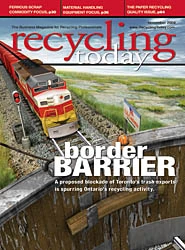
Explore the November 2004 Issue
Check out more from this issue and find your next story to read.
Latest from Recycling Today
- ReMA opposes European efforts seeking export restrictions for recyclables
- Fresh Perspective: Raj Bagaria
- Saica announces plans for second US site
- Update: Novelis produces first aluminum coil made fully from recycled end-of-life automotive scrap
- Aimplas doubles online course offerings
- Radius to be acquired by Toyota subsidiary
- Algoma EAF to start in April
- Erema sees strong demand for high-volume PET systems