While oil filters are a valuable source of scrap steel, their recycling rate is hampered by a variety of obstacles.
The oil filter recycling industry was still learning to crawl in the mid-1990s as it struggled to establish a reliable infrastructure. In the years since, the infrastructure has matured somewhat.
According to several sources, the industry has weeded out unreliable processors, and those that remain have worked to establish relationships with their generators and consumers based on the quality and reliability of the processed filters.
STRENGTHENING AN INFRASTRUCTURE. "Over time, the ‘fly-by-night’ companies have been eliminated, especially with the economic conditions seen over the past few years," says Brent Hazelett, executive director of the Filter Manufacturers Council, Research Triangle Park, N.C. "Additionally, competition has driven many players out of the industry. Consequently, there are less outlets for processing, transporting and recycling used filters."
A Tale of Two Programs |
The Delaware Solid Waste Authority (DSWA) launched the first statewide oil filter recycling collection program in the U.S in 1996. Around that same time, the Used Oil Management Association launched an industry-led initiative in Canada. While both programs are recovering oil and oil filters for recycling at roughly the same level, they are managed in very different ways. DSWA, a quasi-state agency that receives no funds from the state’s general assembly, launched its program with funding from landfill tipping fees. The agency provides roughly 500 commercial establishments and state fleets with collection containers and transportation services in addition to hosting 50 drop-off centers that accept used oil filters from do-it-yourselfers. Of the 1.4 million filters generated annually in the state, 1.2 million are recovered for recycling, Rich Von Stetten, manager of recycling, says. DSWA owns two machines marketed as Krunchers that it uses to process the oil filters. A local refinery collects the recovered waste oil, an average of 6,000 gallons monthly. The compressed filters are taken on a weekly basis to CitiSteel USA in Clayton, Del., for recycling, Von Stetten explains. He says having a market for the steel filters is critical. "The worst thing to do would be to get involved with a program of this magnitude and not have an outlet," Von Stutten says. CitiSteel pays $5 per ton for the processed filters, but it costs DSWA $90 per ton to process them. He says the agency receives approximately $800,000 annually for its marketed recyclables. With a budget of $4 million, the DSWA is in the red yearly by approximately $3.2 million. However, the industry-led program managed by Canada’s Used Oil Management Association, is financially successful. At this time, four of Canada’s western provinces—Alberta, British Columbia, Manitoba and Saskatchewan—participate in the program. Dennis Hambleton, executive director of the Alberta program, says the association has not had any bad debt since it began six years ago. "It’s really providing an environment where the private sector recycling industry can be successful and expand their coverage," he says. The program also accepts oil containers for recycling and includes institutional, industrial and commercial volumes, as well as those generated by the do-it-yourselfer. A levy at the wholesale level finances the program. "We then use that levy exclusively for the purpose of developing and managing programs to improve the collection and recycling of those three products," Hambleton says. A 50-cent levy is charged on oil filters measuring fewer than 8-inches long, while $1 is assessed on filters 8 inches and longer. The collection incentive program is based on zones within the provinces. "Those zones are set so that the demographics and the distance from recycling are taken into account, making it just as profitable to collect these materials in the remote zones as it does in the central core," he says. "We view the collector as the vacuum that sucks these things out of the environment, so the return incentives in our programs go to the collector," he continues. Currently, 70 collectors and processors participate in the program, which has a recovery rate of 89 percent, or 6 million of the 6.7 million filters sold annually. "We had set 80 percent as a target of success, and we were cautioned by the experts who said that if we tried to go after the final 5 percent, we may crater the program," Hambleton says. "You get to a point of diminishing returns. We think we’re there. I think 85 percent is where we’re going to settle out." |
Greg Crawford, vice president of the Steel Recycling Institute, Pittsburgh, also notes that the number of oil filter processors has thinned, eliminating the less diligent processors. "Some of the people that were a little less stringent in doing what needs to be done are not in that business any more, or they have had to grow up and learn how to do it properly," he says. "It’s probably fair to say that the successful operators have found the markets and determined what [type of] processing is required to satisfy the requirements of those markets," Crawford adds.
"Used oil filters, just like steel cans, are a scrap grade themselves in terms of chemistry," he continues, "which makes them a good commodity, [if] there are no ensuing problems by way of faulty processing."
The reductions in processing, transportation and recycling outlets have at times created difficult market conditions for used oil filters, Hazelett notes. "The public infrastructure is still lacking—It is still very difficult for do-it-yourselfers to find places to take their used oil filters."
Mike Skurauskis, vice president of sales and marketing for USFilter Recovery Services, Naperville, Ill., says the company collects approximately 15,000 tons of used oil filters per year. "This tonnage includes used oil trapped in the filter and filter media, as well as the metal portion of the filter," Skurauskis says.
USFilter services drive-through oil change shops, car dealerships, trucking companies and many municipalities in Pennsylvania, Delaware, New Jersey, Maryland, Virginia, North Carolina, South Carolina, Florida, Louisiana, Arkansas, Texas, Tennessee and Oklahoma.
Skurauskis continues, "In the regulated states like Florida and Texas, 95 percent of the filters are collected and recycled, with a few DIY customers throwing them in the trash. In unregulated states, probably less than 30 percent are recycled, based on our collection experience," says Skurauskis.
While Hazelett notes that the commercial collection and processing infrastructure is more sophisticated now, he says that the end results have been largely the same in that the oil filter recycling rate today ranges from 45 percent to 50 percent. Hazelett says part of the problem can be the difficulty filter processors have had in finding end markets.
FINDING EAGER MARKETS. "One major issue some processors have struggled with over the last few years is finding adequate end markets for their product," Hazelett says. "We get calls every once in a while from companies that simply cannot find anyone to accept their processed filters. This is a very frustrating trend but has become more and more common," he says.
"Companies that used to have four or five [destinations] are down to far more limited options," Hazelett continues. "The frustrating part is knowing you have gotten that far—educating people, getting them to pay to have [the oil filters] disposed of properly, to have them properly processed, transported, etc.—and then have the market collapse on some of these companies."
Crawford says the Steel Recycling Institute will provide interested processors with a list of steel mills and foundries that are either accepting or evaluating used oil filters as feedstock. "If someone is looking to market used oil filters, we will work with them toward that end," he says.
Much of the problem could stem from how collectors handle and process their filters. If the filters are shipped to a scrap dealer or a mill and still contain too much oil, this casts the processor in a bad light.
However, Crawford notes that the organization has received few inquiries regarding used oil filters during the last five years. "That means to me that they are finding homes," he says. "That may be the wrong conclusion, but that is my conclusion. A distressed or challenged scrap grade, one that has trouble finding homes, is going to be complaining and looking to find alternatives to paying to have them buried in landfills."
Crawford says he thinks oil filter processors are savvy enough to uncover local markets. "Local markets translate into fairly rare deals with a steel mill or a foundry. But much more commonly, the vendors who collect and process used oil filters are going to ship them to a ferrous scrap dealer to move the material," he says, remarking that scrap processors will often blend them into an auto shredder along with hulks to enhance chemistry.
"It’s incumbent upon the used oil filter collector/processors to make sure they do a very good, consistent job of processing the used oil filters. A collector/processor typically has one opportunity to move material along to a particular ferrous scrap dealer or a particular mini-mill or foundry," Crawford continues. "If they blow it, they won’t be going back there again."
The quality of the processing is judged by the amount of oil that remains in the filter.
PROCESSING FOR QUALITY. The most inexpensive form of processing (and at one time the most common) involves crushing the filter, Hazelett says. "Essentially, the filters are just compressed, which removes a large percentage of the oil from the filter. However, this form of processing has been less and less popular, largely because the end users want more oil removed than simple crushing can accomplish," he says.
USFilter uses such a cubing device, Skurauskis says, that, under high pressure squeezes the oil out of the filters and forms a dense cube of multiple filters. "We then market the cubes to a foundry operation that replaces other forms of scrap steel with them."
Tolerances vary by end user, and have changed over time. "Many mills used to accept filters, then they had to be crushed, then they had to be shredded or burned, then often they quit accepting them altogether," Hazelett says.
Skurauskis notes that prices for processed filters vary by preparation methods. "Cubes are not as high priced as shredded and cleaned steel."
Tamco Steel, an electric arc furnace (EAF) steel mill in Rancho Cucamonga, Calif., has been accepting used oil filters since 1991. Currently, 10 California-based companies send their processed oil filters to the steel mill for melting. From January through November 2003, Tamco accepted 6,500 tons of oil filters. According to Tamco’s figures, each ton of used oil filters yields 1,800 pounds of steel, for a 90 percent melting yield.
Leonard Robinson, Tamco’s environmental and safety manager, says the used oil filters have been drained and either crushed, condensed into a bale or shredded. "Tamco currently pays for used oil filters that have been shredded with paper and other nonferrous material removed," he adds.
Robinson notes that consolidation within the industry has increased the quality of the processed filters. "In the ‘90s there were literally hundreds of companies that were getting involved in recycling of filters in California. This consolidation added a quality control aspect to the industry while still allowing for healthy competition," he says.
Adding oil filters to the melt involved a learning curve for Tamco and its oil filter suppliers. "In the beginning of the program, the used oil filters would cause overheating in the electric arc furnace due to the oil in the filters. Over the years, the companies delivering used oil filters to Tamco have done an excellent job of draining and squeezing the oil from the filters," Robinson says. "More and more companies are shredding the used oil filters. In addition, the production department at Tamco has developed a recipe for the used oil filters that mitigated any challenges."
Crawford notes that U.S. Foundry, Medley, Fla., wants to increase its use of used oil filters. The foundry benefits not only from the scrap value of the steel but also from the fuel value of the filters’ oil-impregnated paper and neoprene.
While these examples may be encouraging, oil filter recycling must face a number of obstacles before the recycling rate is to grow beyond 50 percent.
DEFINING THE OBSTACLES. Hazelett says the public is unaware that used oil filters can be recycled and this remains one of the largest roadblocks, along with limited access to drop-off facilities for the do-it-yourselfer.
Commercially, the cost associated with recovering oil filters is also a hindrance. "For businesses, it’s cheaper to throw them away than it is to recycle," Hazelett says.
"The cost it takes to get the oil out of the filters so they become a product end users want is an obstacle to recycling as well," he says. "There are so many other products out there that are easier to prepare for recycling."
State regulations can also affect the way in which oil filters are managed at the end of life.
"It is a fact that unless the state regulates the recycling of oil filters and requires compliance, we will continue to see lower levels of recycling in unregulated states," Skurauskis says.
"It is a matter of economics," he continues. "If it costs extra, and there is a cost to collecting and recycling, the market will generally choose the lowest cost legal alternative: landfill disposal."
"Many states have over-regulated the management of used oil filters to the point where the laws that are meant to protect the environment are actually hindering recycling," Robinson says. "Other states allow the used oil filters to be landfilled, causing the industry to pursue this management option."
Crawford is optimistic about the outlook for oil filter recycling. "People are inventive. If there is a way to get it done, and it’s to their economic advantage, they will be doing it," he says.
The author is associate editor of Recycling Today magazine and can be contacted via e-mail at dtoto@RecyclingToday.com.
hampered by a variety of obstacles.
Get curated news on YOUR industry.
Enter your email to receive our newsletters.
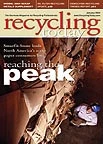
Explore the January 2004 Issue
Check out more from this issue and find your next story to read.
Latest from Recycling Today
- Steel Dynamics cites favorable conditions in Q1
- Hydro starts up construction in Spain
- Green Cubes unveils forklift battery line
- Rebar association points to trade turmoil
- LumiCup offers single-use plastic alternative
- European project yields recycled-content ABS
- ICM to host colocated events in Shanghai
- Astera runs into NIMBY concerns in Colorado