
Using recycled plastics in a manufacturing process can show not only environmental consciousness but also economic savvy.
Fiberon LLC, a composite decking manufacturer headquartered in New London, North Carolina, opened its own plastics recycling plant in 2014 and expanded it most recently in 2017. The 200,000-square-foot facility turns recovered plastics into recycled pellets that the company mixes with wood to create Fiberon’s composite decking and cladding.
“Beyond the obvious reason of being a good steward to the environment, it’s certainly a competitive cost issue,” says Mike Huskey, Fiberon vice president of manufacturing. “If you compare recycled polymers to virgin polymers, there’s certainly a cost advantage to using recycled. To be competitive in today’s market where a lot of our materials and products are becoming more of a commodity, you have to be very cost conscious.”

“In addition to benefiting the environment, our recycling efforts benefit our local community and economy.” – Mike Huskey, Fiberon
On being environmentally conscious
In 2013, Fiberon made the decision to manufacture its own recycled plastic pellets for use in its composite decking. The company installed the first extruder at its New London recycling plant by April 2014. Huskey says the second extrusion line was installed in February 2015 and the third in January 2017. Now, Fiberon reprocesses around one-quarter million pounds of recovered plastics daily.
Fiberon reprocesses globally sourced postconsumer and postindustrial high- and low-density polyethylene (PE). The company also regrinds scrap produced during its manufacturing process.
“If we hadn’t made the decision to move to recycling in 2013, we would have been in a less competitive position,” Huskey says. “Virgin [resin] went from 60 cents per pound
He continues, “The decision to do our own recycling, buying lower cost streams and creating a new product with it, was an easy one.”
Fiberon’s decision to open and operate its own plastics recycling facility rather than outsource that work comes back to the two factors Huskey repeatedly
“In addition to benefiting the environment, our recycling efforts benefit our local community and economy,” he says. “Anybody can buy the low-density and high-density polymer streams, and there’s a certain conversion cost on that, but you also pay a price for someone else to do it for you.”
From start to finish
Some material arrives at the facility
“We test for critical physical properties,” such as strength, Huskey says, and for contaminants, such as polyvinyl chloride and polypropylene.
“You can’t have high-level contamination for the next process—a wood composite product—it won’t process properly.”
He adds, “You need to have a certain strength characteristic; you can imagine that deck boards need a certain amount of strength.”
Fiberon blends the high-density and low-density PE together. “It’s all about a blend of material that works with the process,” Huskey says.
After the incoming materials have been tested, a series of conveyors
“We want [metals] removed so they won’t damage the screws and other equipment,” Huskey says. “We also have a flop gate that has a metal detector. And, if it detects metal, it will abort that whole section of material and drop it in a container.”
The conveyor system then moves the material from the shredder to another piece of equipment that Huskey describes as a “preparatory-type chamber that either shreds the material further or heats it up.”
Once shredded and sorted, the material is melted using the torque created by a large single-screw extruder and pushed through a filter screen that will remove any other possible contaminants. The material is fed through a second, similarly sized single-screw extruder and screen before it’s pushed through a pelletizer, which is equipped with a blade that cuts the pellets at 2,000 revolutions per minute (rpm). The pellets are either air-cooled or water-cooled and then stored in silos.
The pellets are transported to Fiberon’s nearby manufacturing plant. Huskey says, “Fiberon Recycling is within 3 miles of the New London plant, so the recycled pellets don’t have far to travel. The added efficiency means less fuel is consumed by our trucks, and less carbon dioxide is emitted into the atmosphere.”
The recycled pellets also are shipped to a second Fiberon manufacturing facility in Meridian, Idaho, Huskey says.
Sponsored Content
Still relying on manual sorters?
Let AI do the heavy lifting. Waste Robotics delivers reliable, high-performance robots tailored for complex waste streams. They require minimal maintenance, are easy to operate, and are designed to boost your recovery rates. Smarter sorting starts with the right partner. Waste Expo Booth #1969 & REMA #2843
Click here to see our robots in action!At the company’s manufacturing facilities, wood flour made from postindustrial wood scrap is mixed with the plastic pellets and coextruded to create Fiberon’s products.
“When you take two materials like wood and man-made polymer, there needs to be a lot of mixing that happens,” he says. “They aren’t readily compatible.”
Keeping it in-house

Fiberon consumes all the recycled pellets it produces in its manufacturing process and does not sell its pellets to other end users.
Aside from the environmental and cost benefits the company has seen by vertically integrating its operations, Huskey says Fiberon also appreciates the control it has from creating its own recycled plastic pellets.
“You can control your own streams of materials and your own freight,” he says.
In terms of disadvantages, it costs more for the additional brick-and-mortar building and overhead of operating a plastics recycling facility. Yet, despite recent struggles and the bumps along the way, Huskey says, “the advantages weigh out the disadvantages.”
He adds, “Using recycled content in our products means we can divert more than 60,000 tons of wood and plastics from landfills and incinerators each year, as well as reduce the negative environmental impacts of processing virgin materials.”
For more information: Fiberon, 800-573-8841, www.fiberondecking.com
Get curated news on YOUR industry.
Enter your email to receive our newsletters.
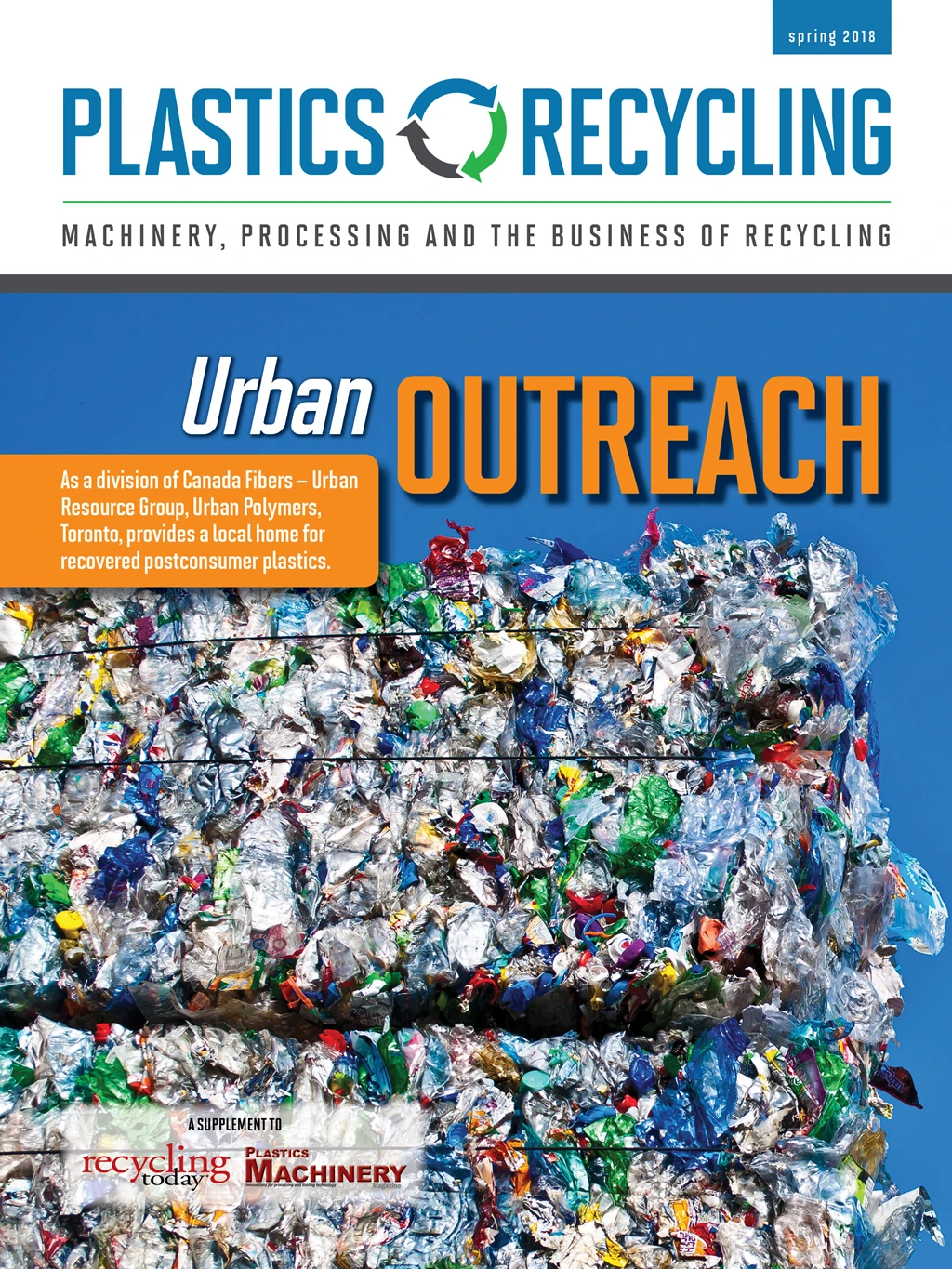
Explore the May 2018 Plastics Recycling Issue
Check out more from this issue and find your next story to read.
Latest from Recycling Today
- Enfinite forms Hazardous & Specialty Waste Management Council
- Combined DRS, EPR legislation introduced in Rhode Island
- Eureka Recycling starts up newly upgraded MRF
- Reconomy Close the Gap campaign highlights need for circularity
- Nickel carbonate added to Aqua Metals’ portfolio
- EuRIC, FEAD say End-Of-Life Vehicle Regulation presents opportunity for recyclers
- Recyclers likely to feel effects of US-China trade war
- BCMRC 2025 session preview: Navigating battery recycling legislation and regulations