As the price of ferrous scrap began hitting historic highs earlier this decade, the first instances of putting ferrous scrap into containers and exporting it struck most observers as a curiosity.
To a great extent, the curiosity factor has disappeared as recyclers in virtually all geographic regions have taken advantage of a way to reach export destinations that was largely untried just a few years ago.
As the decade nears its end, many ferrous scrap recyclers have begun to face some new decisions every 30 days. One involves how many export containers to seek for their ferrous scrap shipments while the other is tied to determining how reliant a company wishes to become on the ferrous containerized export market.
A NEW OPTION
As the United States has tilted toward becoming a net exporter of scrap, the trend has changed the way scrap recyclers ship their outbound volumes.
On the nonferrous side, with red metal scrap in particular, preparing export containers has been an important part of the business for several decades. It is on the ferrous side of operations that shipping scrap long distances via container is a newer phenomenon.
Traditionally, ferrous scrap recyclers who wished to reach the export market sent their material to the handful of ocean-going bulk cargo loading locations on either the Pacific or Atlantic coasts.
The system has served large recyclers and large overseas mill companies well for several decades, providing an affordable way to ship large amounts of material over long distances.
The heated demand scenarios of this decade, however, put several factors into place that created the conditions for containerized ferrous scrap shipping to take hold.
Asia’s booming steel industry emerged this decade, with China’s steel production in particular growing exponentially until that nation became the largest steelmaker in the world.
The Chinese steel industry consists of a number of steelmaking firms and mill locations, not all of which are convenient to bulk cargo ports.
Additionally, steelmakers competing with Chinese mills for ferrous scrap in nations like India and Vietnam reached farther and farther out geographically for feedstock, with brokers and agents searching North America for material.
Such buyers were not necessarily well-served by the ocean-going bulk cargo system, leading eventually to requests for containerized shipments of ferrous grades going directly from North America to purchasing agents or mill locations overseas.
Many recyclers had to be convinced the math made sense, but as ferrous prices escalated throughout 2007 and much of 2008, the profitability of the endeavor became clear to many.
READY TO SERVE |
Several equipment companies were quick to identify the growing trend of ferrous scrap being shipped internationally in enclosed containers. The process involved was different enough from what recyclers were used to that these companies saw opportunities to fabricate specialized systems to increase the efficiency and ease of loading loose ferrous scrap into closed-top containers. For recyclers who may be interested in what is on the market in this vein, write-ups on several of these products and systems can be found at www.RecyclingToday.com. If you work for an equipment supplier with a container loading system for the industry, help us spread the word by sending product information to Assistant Editor Zack Lloyd at zlloyd@gie.net. |
An advantage for North American recyclers included an ability to work with an entirely new set of customers to reach the export market without having to go through the handful of large recycling companies that have come to dominate the bulk cargo trade.
One of the barriers has included learning operationally how to best load containers with loose grades of ferrous scrap, though it did not take long for equipment suppliers to respond with a number of loading and tilting options for this application.
CONSIDERATIONS
It is nothing new to scrap recycling veterans to consider their scrap purchases and sales from every conceivable angle. The emergence of the containerized ferrous scrap export market has added an additional angle to be considered.
“It’s really all price-based,” says Ben Abrams, president of Consolidated Scrap Resources (CSR), York, Pa., regarding decisions to fill orders for containerized ferrous scrap.
Howard Glick of Tri-State Iron & Metal, Texarkana, Ark., cites the same logic. “For us it’s a function of price; when we get a better price, we do it.”
Abrams says serving this market can involve additional expenses, but if the purchase price is right, it can often be the most profitable option for sales of ferrous scrap.
A scrap recycler in the Southeastern United States notes that Indian brokers spurred demand for containerized ferrous scrap in November 2009.
Abrams also identifies India as a key market for CSR’s ferrous scrap. He says demand from that part of the world “ebbs and flows,” with some months featuring bountiful requests for orders, while other months are relatively dry.
He adds that containerized buyers were active in the market in the first half of 2009, which worked out well for CSR. “When the domestic market was dead in March, April and May, the brokers buying containers came in and we shipped a heck of a lot of containers.”
Container buyers are price sensitive, says Abrams. Speaking in mid-December 2009 as ferrous scrap prices were rising for the second consecutive month, Abrams remarked, “When the prices get up higher like they are today, the brokers buying containers are not around as much, at least in our neck of the woods.”
Location is nearly as big of a factor to reach the containerized export market as it is to ship scrap through the bulk loading ports. Abrams says of CSR’s York and Harrisburg, Pa., locations, “We have a pretty favorable trucking rate to the port,” says Abrams, whose company is closest to the port of Philadelphia.
Favorable trucking rates to ports are not as available for Mervis Industries, Danville, Ill., according to that company’s President and CEO Adam Mervis. “If you look at our geographic location, we’re not on water and our yards are a significant distance from a major intermodal railhead,” Mervis comments.
The situation is different for scrap companies in Chicago, notes Mervis, who can save on the freight costs of hauling containers from a relatively remote city like Danville.
But for Mervis, “We’re going to pay $550 freight just to get that container to the railhead, and that’s before paying the rail freight to the coast and then the steamship fee.”
In Texarkana, Glick says, “For us, it’s pretty comparable to shipping by truck or rail to a domestic steel mill.”
For recyclers who can make the math work in the containerized ferrous market, the next set of considerations can involve how to best prepare the scrap and load the shipping containers.
PREP AND LOAD
For recyclers who process nonferrous metals or scrap paper, loading material into enclosed box cars is likely a familiar process.
In most of those cases, however, the nonferrous and paper materials being loaded are baled or in large Gaylord boxes or bulk bags.
Many of the ferrous scrap container export orders are for shredded scrap or plate and structural grades that are not conducive to being baled. Recyclers are more comfortable loading such grades into open-topped rail gondola cars, trucks or river barges.
Loading enough loose ferrous scrap into a closed-top container to make the ideal export weight is not an insurmountable trial, but some recyclers have learned the pitfalls firsthand.
“It can be difficult to load containers versus open-top trucks or railcars, and it costs a couple dollars more in the scheme of things,” Abrams says.
Thus far, CSR has not invested in a specialized loading system, Abrams says. “We basically push the scrap in using a skid-steel loader,” he comments. “It’s very efficient to do it that way and basically takes only 15 minutes or so to load for our experienced operators.”
He says there are “nuances” to loading the containers to achieve a maximum weight. “I think our employees have done a great job with it,” Abrams remarks.
CSR favors sending shredded scrap in containers for operations reasons. “You don’t have the sharp edges with shred that you will with No. 1 heavy melt or plate and structural grades,” says Abrams. “You can really damage containers or even tear a hole in the wall with those types of scrap, so it’s a little less desirable to load those grades.”
CSR has worked with new trucking companies and drivers who specialize in hauling intermodal containers and had to make adjustments in terms of scheduling these drivers to work in sync with the company’s crews who were preparing the loads.
Abrams says CSR is almost certainly better off for having taken part in the developing trend of containerized ferrous scrap shipments.
“It has been a good way to work directly with brokers representing countries in emerging markets like India, Thailand and Vietnam, and for them to buy scrap from individual yards like us who aren’t on deep water,” says Abrams.
“I think shipping ferrous scrap in containers is around to stay,” Abrams says. “Instead of being beholden to domestic brokers, it has opened up new markets for us.”
The author is editor-in-chief of Recycling Today and can be contacted at btaylor@gie.net
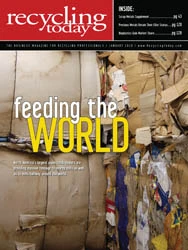
Explore the January 2010 Issue
Check out more from this issue and find your next story to read.
Latest from Recycling Today
- Nucor receives West Virginia funding assist
- Ferrous market ends 2024 in familiar rut
- Aqua Metals secures $1.5M loan, reports operational strides
- AF&PA urges veto of NY bill
- Aluminum Association includes recycling among 2025 policy priorities
- AISI applauds waterways spending bill
- Lux Research questions hydrogen’s transportation role
- Sonoco selling thermoformed, flexible packaging business to Toppan for $1.8B