
For decades, STEINERT has been helping the materials recycling industry increase recovery rates and purity levels of recovered materials. The STEINERT SteelMaster® combines several technologies to assist processors in maximizing the value of their shredded ferrous streams.
As electric arc furnace (EAF) steel production continues growing across North America and the world, producers increasingly have stringent raw material quality requirements. At the same time, processors want to unlock the value of materials, not leave them as contamination in another stream.
Copper recovery, ferrous upgrade
The STEINERT SteelMaster® uses a combination of ballistic and magnetic forces to separate copper and meatballs from heavy ferrous fractions discharged by drum magnets that follow metal and auto shredder discharges. Because the separation is based on physical principles, it provides a low-cost alternative to sensor-based sorting.
Designed to operate as either an in-line solution or offline as a batch-fed process, SteelMaster® units are available in 1.5- and 2-meter widths. “These units have consistently demonstrated that they effectively extract well over 90 percent of meatballs,” says Kyle Rice, Solutions Sales Manager, metals, at STEINERT US.
“Because the SteelMaster® is so effective, our customers experience reduced labor costs because they eliminate a significant portion of the manual sorting. They also substantially increase ferrous quality, which the mills love. At the same time, the copper-bearing material is liberated, so they can sell copper as copper and steel as steel. This unlocks a lot of incremental value.”
SteelMaster® units extract 90 percent of copper meatballs and free copper wires from the flow, and 80 percent to 90 percent of the volume is furnace-ready clean steel after sorting.
“We find that some 30 percent of the overall volume processed contains high nonferrous content, essentially copper- or aluminum-wrapped ferrous,” Rice says. “This stream can still be hand sorted, or sensor-based sorting can be applied to the stream. Because the volume has been reduced so much, the investment to do sensorbased sorting on this stream is far less, thus much more cost-effective. We find that some 15 percent of this stream is copper.”
The SteelMaster® has evolved thanks to years of development. The adjustable electromagnets within the magnetic head pully include ANOFOL products as a conductor material for the solenoids. Anodized aluminum strip is used in production of the ANOFOL coils, so operators are getting the best of STEINERT magnetic technology at the heart of each SteelMaster®.
STEINERT sorting equipment aids in the production of pure, clean steel. It is the key to unlocking the value of ferrous scrap streams, avoiding potential steel mill penalties and refining the pathway to a circular economy.If you would like to learn more about the STEINERT SteelMaster®, contact Kyle Rice at kyle.rice@steinertus.com.
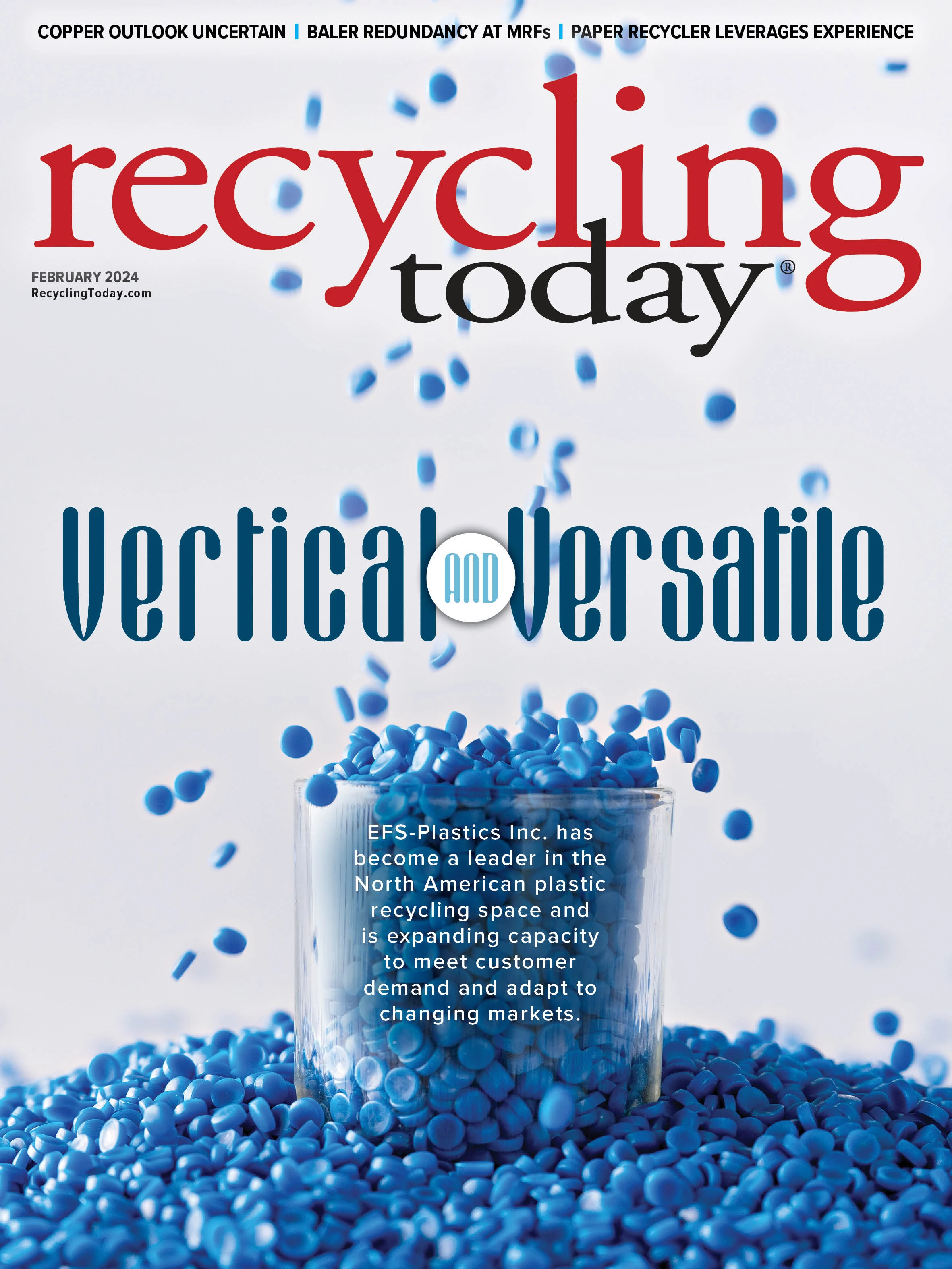
Explore the February 2024 Issue
Check out more from this issue and find your next story to read.