Steel producers in North America have been using mini-mills with electric arc furnaces (EAFs) to make steel for a number of years. Since 1980, the use of EAFs has grown from about 28% of steel production to more than 40%. However, when steel is produced using these electric furnaces an EAF dust is also produced. The problem is that this dust is considered a hazardous waste in both Canada and the U.S. because it contains small quantities of heavy metals, including lead.
To address this issue, mini-mills have installed elaborate dust collection systems. The simple solution for steel mills was to dispose of the dust at a landfill site. Unfortunately, only a few landfills are able to take the EAF dust.
Furthermore, compared to normal wastes, the disposal of EAF dust is more expensive. Tipping fees at landfill sites that accept the dust cost in the range of $150 to $200 per ton. However, even before the dust can be sent to the landfill, it must be thermally treated. This is an additional cost. As a consequence, mini-mills have paid millions of dollars to remove, treat, and dispose of the EAF dust.
The dust can contain iron, lime and smaller amounts of lead, cadmium and chromium. Facilities that produce materials like stainless steel with lower zinc content can also recover chromium and nickel from the dust.
However, most recovery options are only economically viable for dust with zinc content of at least 15% to 20%. A number of companies have been working on alternative dust recovery processes to reclaim a number of nonferrous metals from EAF dust.
For example, Consolidated Materials Brokers (CMB) from Nashville, Tenn., has developed a process that removes the heavy metals, as well as the zinc oxide, from the dust. It uses the remaining inert material as an ingredient for the manufacture of building bricks. The system was installed in Ohio in October 1997 and is fully permitted by the U.S. Environmental Protection Agency (EPA).
The process involves “boiling” the lead, cadmium and zinc out of the dust material, re-condensing it and collecting it in a baghouse. This fume is then sold to zinc producers for use as a feedstock in the production of pure zinc, pure lead, and pure cadmium. Zinc and lead recovery rates with the process are reported to be more than 97%.
The EnviroPlas process is another system to recover EAF dust. It was developed at Mintek in Randburg, South Africa. The process evaporates the EAF dust and then uses a lead-splash condenser to collect it in a bag filter. Testing by the smelting of EAF dust, zinc-bearing alloy-steel dust, lead blast furnace slag, Imperial Smelting Furnace (ISF) slag and primary leach residue was conducted from 1989 to 1993. More than 95% of all zinc, chromium and nickel were reported recovered from the dust. The slag produced met the criteria of the EPA for safe disposal.
Subsequently, in 1994 a demonstration plant was built that included a plasma-arc furnace and an Imperial Smelting Processes Ltd. (ISP) lead-splash condenser. The plant was successfully commissioned using about 1,000 tons of lead blast-furnace slag. Mintek also developed a process to remove halogens, like chlorine, from the dust. Halogens interfere with the proper operation of the condenser by forming large quantities of dross.
Another process is the one designed by the Horsehead Resource Development Co., Inc. (HRD) in Monaca, Pa. The company has developed a flame reactor system which is a hydrocarbon-fueled, flash-smelting system to treat EAF dust. This reactor processes EAF wastes with gases at temperatures greater than 2,000 degrees Centigrade produced by burning solid or gaseous hydrocarbon fuels in oxygen-enriched air.
The compact, low-capital cost, water-cooled reactor, achieves a high waste throughput because the feed materials react so rapidly. The end products are a glass-like slag, a heavy metal-enriched oxide and, in some cases, a metal alloy. Volatile metals are fumed off and captured in a baghouse, while non-volatile metals may be separated as a molten alloy.
Phoenix Environmental Ltd. (PEL), Montgomery, Pa, has come up with another alternative. The company has built a plant to recycle EAF and other by-products from steel and bearing manufacturing at Timken Co.’s Faircrest steel plant in Canton, Ohio. The PEL process converts by-products such as EAF dust, metal grindings and scale into magnetite. This is sold as a raw material to manufacturers of blasting media, shingle granules, pigments and colorants for paint and concrete and as filler additives for plastic.
Similarly, Midrex Technology Corp., Charlotte, N.C., has reported that it has produced blast-furnace-quality iron from hot-strip-mill and basic oxygen furnace sludge, mill scale, blast-furnace flue dust and filter cake in a new process that uses Midrex’s FastMet process. Presently, steel mills are stockpiling these wastes or are paying $18 to $20 per ton to dispose of them in landfills.
In the Midrex process, the mill wastes are turned into briquettes by a proprietary oxide-briquetting technology developed by National Recovery Systems, East Chicago, Ind. The briquettes, which contain iron oxide and pellet fines, are charged into a Fastmet-process furnace where gas, oil or coal-fired burners reduce the material. After being metallized to 85 to 90 percent, the briquettes are hot-charged into a melting furnace designed by EMC International, Pittsburgh. The resulting liquid iron, which Midrex calls FastIron, has carbon levels of 4.5 percent, the same as blast-furnace iron, with 0.5 percent silicon and less than 0.02 percent sulfur.
While a great deal of progress has been made in the design and construction of systems to recover steel making wastes, more work needs to be done. These new systems will need to be designed to be efficient, economical and environmentally friendly in order for smaller mini-mills to use them. If this isn’t done, EAF dust and other steelmaking wastes will continue to be sent to landfills and the various metals and other materials in them will be “wasted.”
The author was formerly with the communications office of the Canadian Association of Recycling Industries (CARI), Almonte, Ontario. That organization can be reached at (613) 256-8533.
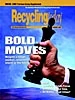
Explore the January 2002 Issue
Check out more from this issue and find your next story to read.
Latest from Recycling Today
- Recycled steel price crosses $500 per ton threshold
- Smithers report looks at PCR plastic’s near-term prospects
- Plastics association quantifies US-EU trade dispute impacts
- Nucor expects slimmer profits in early 2025
- CP Group announces new senior vice president
- APR publishes Design Guide in French
- AmSty recorded first sales of PolyRenew Styrene in 2024
- PRE says EU’s plastic recycling industry at a breaking point