For the past several years, ferrous shred has been taken for granted as a benchmark scrap grade, but ferrous scrap veterans are aware that the prominence and even existence of the grade is a relatively recent development.
In terms of industrial processes, the shredding of automobiles, washing machines and other large objects is a recent innovation.
NOT A BUNDLE OF JOY
As steel mills during and after World War II looked for scrap metal to make up part of their furnace charge, scrap metal dealers used baling machines to create number two auto bundles.
“In those days, to make a number two auto bundle, the standard practice all over the U.S. was for scrap yards to buy auto bodies from the wrecker yards—they had been stripped to some extent—and they would typically torch off heavy components like the frame and cut those up into pieces,” says Dr. Richard Burlingame, a consulting metallurgist from Cleveland. “Those heavy pieces were called hard steel. Then the hulk that was left had few high-density sections, so it was easily baled. That was your number two bundle.”
Burlingame, who worked for Cleveland-based scrap processor Luria Bros. Inc. from 1961 to 1986, says the auto bundles were a low grade of scrap, but that open hearth furnace operators would still consume the bundles if they could be diluted in a large melt. “Everything in that car got baled together—including plastics and glass,” he remarks. “In the late 1950s, the total amount of nonmetallics and nonferrous metals was up to 15% in a typical body that had been stripped down. This compares to 25% to 30% today. It’s hard to believe now that there was any market for these bundles, but there was much more iron and steel used in cars then, until more and more plastic and composites and nonferrous metals came into the picture. There was no mystery or conniving or dishonesty. Everyone knew what a number two auto bundle was. Steel mills bought them cheap and used them for decades.”
But the low-grade chemistry of the bundles eventually came to the attention of steel mills. According to Burlingame, it was the refusal of an Armco steel mill in Houston to accept number two bundles that inspired the Proler family in Houston to invent the auto shredder.
Mighty Manganese |
A number of factors were needed to make auto shredders work efficiently, but one of the most vital might be the use of manganese-steel hammers. “The widespread practicality of shredders would not have been possible without the manganese-steel that makes up hammers, grate bars, rotor caps and the liners of the mills,” declares Dr. Richard Burlingame, a Cleveland-based metallurgist. The material is essential, he says. “Without it, there would be no auto shredding that would be economical. You can use quenched and tempered steel, but it would not have been economical at that time.” Early shredder operators, including the pioneering Prolers in Houston, learned to use four-way hammers that could be “flipped” repeatedly to get maximum use out of each hammer. Access to hammers that were durable and that could be replaced somewhat affordably “is not a minor point,” says Burlingame. “Hadfield 14% manganese steel was just an absolute marvel of toughness. Without this material, the whole shredding business might be economically unfeasible.” |
PUTTING THE HAMMER DOWN
When an important local scrap consumer—the Armco steel mill in Houston—began shifting away from number two auto bundles in 1957, the four Proler brothers who ran Proler International in Houston began to consider their options.
“We had to find a way in which to remove the residuals that were in auto scrap—like copper, aluminum, lead and the upholstery. The auto shredder was our solution,” says Herman (Hymie) Proler, former chairman and CEO of that company, which has since been disbanded.
The design consisting of a rotor with attached swinging hammers that is at the center of the auto shredder had been in widespread use in the mining industry. The Prolers had already introduced it to the scrap industry with an application making “precipitation scrap” out of tin cans for the copper production market.
“We figured if we could shred these materials, if we could build one big enough, why not try the process with pieces of a car,” says Proler. Brothers Hymie, Sammy, Jackie and Israel (Izzy) Proler played different roles in laying the groundwork for the shredding revolution.
A Slow Burn |
While the Prolers designed and built their first shredders, other scrap companies were trying different ways to make marketable scrap from abandoned automobiles. At a Brooklyn, New York, location, Luria Brothers Inc. experimented with a system to burn away undesirable portions of automobile hulks. “The idea was to burn everything that would burn (plastics, textiles, rubber) to get an improved melting yield,” says Dr. Richard Burlingame, a metallurgist who worked for Luria Brothers in those days. The entire process Luria used in Brooklyn was labor intensive, however. A disassembly line was set up for workers to remove copper wiring and other nonferrous materials, as well as engine blocks and other cast grade materials. In the Brooklyn process, these stripped hulks were sent into a homemade incinerator, where the organics were burned off. “They took the hulks and quenched them, and that released a whole lot of ash,” says Burlingame. “Finally, they put the incinerated and washed hulks into a baler, and called the resulting product Luria Blox.” “They were pretty popular,” says Burlingame of the Luria Blox, “because they did improve melting yield and improved the chemistry by reducing the presence of copper and other contaminants.” But the combination of labor-intensive costs and environmental pressures brought about by the handling of the ash, the run-off water and the incinerator emissions meant, “it really wasn’t a very profitable product,” the metallurgist notes. |
The brothers’ attempts to recruit existing hammer mill manufacturers to help them build a machine were unsuccessful, so they became their own designers, engineers and fabricators, with Sammy and Hymie in particular working up design drawings.
While there was some trial and error involved in designing such things as the bearing housings, lubrication systems and dust control system, Hymie says the results were encouraging from the start. “It was amazing that the first time we built it, the shredder was better than we anticipated,” he comments. “We dropped a whole car in there, and there she went.”
Their earliest models—dubbed Prolerizers—did not lack for horsepower. “The original motors were taken from naval destroyer escort vessels and had 12-foot flywheels and 6,000 horsepower,” recalls Hymie.
The Prolerizer became a trademarked name, and Sammy Proler received a patent for the shredding unit when coupled with the use of bottom grates to produce a sized grade of ferrous scrap.
While today’s shredders produce scrap that is fed into elaborate downstream systems that conduct positive sorts for aluminum, copper and other nonferrous metals, the recovery of iron-bearing scrap was the focus of the first machines.
Sponsored Content
Labor that Works
With 25 years of experience, Leadpoint delivers cost-effective workforce solutions tailored to your needs. We handle the recruiting, hiring, training, and onboarding to deliver stable, productive, and safety-focused teams. Our commitment to safety and quality ensures peace of mind with a reliable workforce that helps you achieve your goals.
“Initially, we tried a lot of things,” recalls Hymie, who notes they experimented with an oven to burn off the upholstery from shredded pieces. “We didn’t know the magnets would do such a good job. Our first magnet was a belt magnet, but we went to drums because the scrap was wearing the heck out of the belt. The drum had to be strong enough to draw the ferrous scrap to the center without also drawing the residue.”
The development of the Prolerizer was watched at a distance with intrigue—and in some cases skepticism—by competing scrap companies. “The rest of the scrap industry was stupefied by this,” says Burlingame. “How could you put a car body in a machine and do anything but just stall the mill? They couldn’t imagine enough rotor radius, horsepower and hammer speed to do this.”
But the Prolerizers were powerful enough not just to do the doors and fenders that typically made up number two auto bundles, but it was soon discovered that they could also handle the steel frames and cast iron engine parts that initially were withheld from the shredder.
Much of the engineering and design behind the Prolerizer was indeed homegrown. “Sam Proler is just a good engineer,” says Burlingame. “The Prolers deserve the plaudits and commendations for starting the shredding revolution,” he adds.
A PREMIUM GRADE
The Prolerizer shredder worked, but would the resulting product be of interest to steel mills? The answer turned out to be yes, and the person who helped steel mills arrive at that answer was Izzy Proler.
“Izzy had to go out and sell the product, and he was able to make the mills understand what this product was,” recalls Hymie Proler. “He was the one who merchandized it, and he did an excellent job of it.”
Armco, the company with the Houston mill that turned away number two auto bundles, was among the most impressed with the new ferrous shred product. According to Hymie, Armco subsequently bankrolled the building of the next Prolerizer in Kansas City to produce feedstock for its mill there.
As downstream shredder systems improved, the grade quickly came to be a premium grade that could be used by electric arc furnace (EAF) mills. “It was terrific EAF feed, because it wouldn’t break the electrodes like bales could,” says Hymie. “With this material, electrodes could just penetrate through it.”
With the acceptance of the grade, the rush was on by scrap companies and manufacturers to join the shredder revolution. Companies that built hammer mills and shredders for other purposes began offering powerful shredders that could handle automobiles and white goods. A variety of manufacturers began working on equipment that could improve downstream separation of shredded materials, most notable being the pioneering work of the Fritz family and Huron Valley Steel of Belleville, Mich.
In Texas, Alton Newell and his family members and co-workers introduced a number of innovations to the shredder, concentrating on ways shredders could operate more efficiently and cost-effectively.
Operators and equipment makers also experimented with wet, dry and damp shredding; different rotor speeds; different grate and liner configurations; and any number of other techniques to shred autos quickly and efficiently while producing a premium grade of scrap.
Today, with some 200 auto shredding plants operating in the U.S., ferrous shred is the grade that dominates the feedstock market for EAF mills in North America and throughout the world.
The author is editor of Recycling Today and can be contacted via e-mail at btaylor@RecyclingToday.com .
Get curated news on YOUR industry.
Enter your email to receive our newsletters.
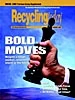
Explore the January 2002 Issue
Check out more from this issue and find your next story to read.
Latest from Recycling Today
- CP Group announces new senior vice president
- APR publishes Design Guide in French
- AmSty recorded first sales of PolyRenew Styrene in 2024
- PRE says EU’s plastic recycling industry at a breaking point
- Call2Recycle Canada, Staples Professional expand partnership
- Circular Services breaks ground on north Texas MRF
- Tariff uncertainty results in choppy nonferrous scrap flows
- CATL, Ellen MacArthur Foundation establish battery partnership