
Photo courtesy of Winkle Industries

Industrial lifting magnets are critical to material handling in scrap processing facilities, and they sometimes are misunderstood. It is imperative that operators understand that the lifting magnet’s role is critical to the success and profitability of their businesses.
If a magnet is used per the manufacturer’s specifications and recommended best practices are followed, it can lead to increased production, a lower occurrence of unscheduled downtime, lower overall maintenance costs and greater service life, not only for the magnet but also for related equipment.
Proper sizing
The first thing for an operator to understand is how to properly and safely size a magnet to optimize the capabilities of the crane or material handler. This can be done using lift charts provided by the crane manufacturer. To determine the carrier’s lift capacity relative to the size and weight of the magnet, use the lift chart to find the carrier’s capacity when the boom and stick are fully extended over the side at ground level, then subtract the weight of the magnet as well as the maximum weight of the material being lifted. If the combined weight is less than the carrier’s capacity, safe operation is assured. It is important to note that all crane manufacturers have various combinations of boom and stick lengths, which also must be considered when making this calculation.
Today’s material handlers are designed to be nimble and functional in many different environments. Whether you have a rubber-tired machine, a tracked machine or even a pedestal crane, weight is an important consideration in magnet selection.
Magnet construction can vary by application, but in the scrap processing industry, magnets wound with aluminum strap or aluminum wire are more common. With an aluminum-wound magnet, not only can speed be increased when combined with the functionality of today’s cranes, but the lower weight of these magnets will cause less long-term wear and tear on the carrier. Today’s machines can be operated so efficiently, a lighter weight aluminum-wound magnet is a great option and also has become an industry standard.
On the other hand, copper-wound magnets are an excellent option for industries that use overhead cranes because they do not have the capacity limits that material handlers do. Although copper-wound magnets offer advantages, they are not the most viable or cost-effective solution for scrap processors.
Lifting capacity factors
Operators also need to be aware of the key factors that can affect a magnet’s lift capacity. The lift capacity is determined by the ampere/turns in the coil as well as by the surface area of the bottom of the magnet. The number of amps times the number of turns equals the magnetic field. A greater bottom surface area allows for a larger magnetic field to be generated, thereby creating a superior lift. The caution here is related to air gap. The denser the material with less air gap, the better the lift capability of the magnet.
The sizing of pole shoes also affects the magnet’s lift capacity. The magnetic field produced by a magnet coil needs the proper amount of steel section in the center pole shoe and outer pole shoe but also in other areas of the magnet to force the magnetic flux down to the material being lifted. If the pole shoes are not properly designed to allow for maximum flux density, the magnet’s lifting capacity will be negatively affected.
_fmt.png)
Duty cycle is critical to understand as it affects the performance of lifting magnets. Duty cycle is simply time on versus time off and is generally measured in 10-minute intervals. A 50 percent duty cycle magnet should be on for five minutes and off for five minutes. A 75 percent duty cycle magnet can be on approximately seven minutes out of every 10 minutes. Exceeding duty cycle will have a negative effect on the productivity and life of the magnet.
Keys to extending service life
To extend the service life of lifting magnets, training programs designed to help crane operators understand the consequences of mishandling or abusing a magnet and the benefits of developing and maintaining a consistent magnet inspection program are recommended.
Operators are the frontline defense in preventing premature magnet failures. If they truly understand the potential consequences of misusing a magnet, they can be your best ally in extending service life.
Consistent and systematic inspection programs also are key in identifying a magnet that is in the early stages of failure. Magnets should be visually inspected at the beginning of every shift for obvious mechanical damage to welds, wear depth and chain wear. The leads and connectors also should be inspected. A damaged lead or connector could lead to a short in the magnet, necessitating a rebuild.
The magnet inspection program also should incorporate measuring and documenting electrical readings, such as current, resistance and meg-ohms, at consistent intervals.
A regular inspection program identifies small problems and allows them to be corrected before they become big problems, allows major repair work to be planned around the production schedule and helps identify whether operators require additional training.
Heat and abuse are the main causes of magnet failure. It is extremely important that a magnet be allowed time to cool and dissipate the heat generated by the coil. Using the magnet improperly, including using it as a battering ram, for instance, also will contribute to early failure.
The magnet’s resistance can be tested with an ohmmeter, and the reading can be compared with the magnet’s nameplate data to determine the integrity and condition of the conductor. Additionally, Megger readings can test for grounding between the coil and case. These two field tests will give you a good indication of what is happening inside the magnet.
Damage to magnet power leads also causes premature magnet failure. This type of damage can be prevented by using a cable protection system, which prevents abrasions, nicks, cuts and heavy impacts.
Magnet monitors and magnet meter packages aid in safe use of the magnet and prevention of premature failures. Both devices help operators measure electrical performance. The primary difference between the two is that the monitor provides alerts when magnet currents have been exceeded and will disable subsequent lifts, where the meter package measures voltage and amperage to help determine when magnets should be removed from service.
Magnet controllers are devices that energize and discharge electromagnetic fields. The two options are direct current (DC) constant potential and solid state. The DC constant potential controller uses electromechanical components to safely charge and discharge the magnetic field. These units can require periodic maintenance but are relatively easy to understand and repair. However, solid-state controllers are virtually maintenance-free “intelligent” devices that protect magnets, power systems and personnel. These devices also can increase cycle times and throughput with faster charge times and cleaner drop cycles.
Lifting magnets and their related components are critical to the operation of many scrap processing facilities. The bottom line is, if you take care of them, they will take care of you.
![]() | The Garden Center Conference & Expo, presented by Garden Center magazine, is the leading event where garden retailers come together to learn from each other, get inspired and move the industry forward. Be sure to register by April 17 to get the lowest rates for the 2025 show in Kansas City, Missouri, Aug. 5-7.
|
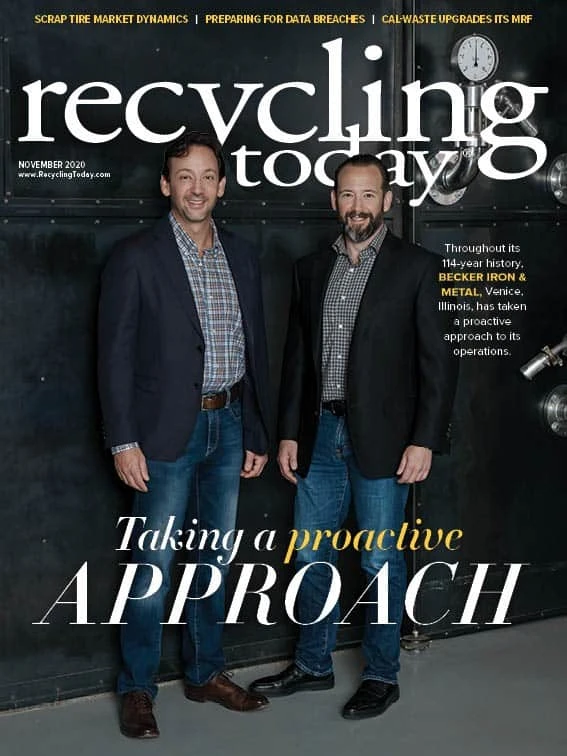
Explore the November 2020 Issue
Check out more from this issue and find your next story to read.
Latest from Recycling Today
- ReMA board to consider changes to residential dual-, single-stream MRF specifications
- Trump’s ‘liberation day’ results in retaliatory tariffs
- Commentary: Waste, CPG industries must lean into data to make sustainable packaging a reality
- DPI acquires Concept Plastics Co.
- Stadler develops second Republic Services Polymer Center
- Japanese scrap can feed its EAF sector, study finds
- IRG cancels plans for Pennsylvania PRF
- WIH Resource Group celebrates 20th anniversary