As America’s manufacturing sector ramped up its reopening in late June and early July, the additional scrap supply helped quell the upward pricing momentum that characterized the market in May and early June.
Indexed pricing calculated by Fastmarkets AMM saw the prompt scrap No. 1 busheling Midwest Index price fall by more than $45 per ton in July after auto parts stamping plants came back to life in June.
That’s not to say scrap flows are anywhere near pre-COVID-19 levels, according to recyclers, but they have returned to a level that can meet demand that is tied to a 56 percent domestic steel mill capacity rate and intermittent overseas demand.
“Scrap flows are decent at this point into this pandemic crisis,” says a recycler in California. “I wouldn’t say times are booming, but our long-term customers in our area, which are mostly agriculture-based and manufacturing-based, continue to operate at a decent level.”
A recycler in the lower Midwest also says activity has increased since April and May, when it “was a blessing to be able to clean up some material that had been around for a long time.”
“I wouldn’t say times are booming, but our long-term customers in our area continue to operate at a decent level.” – a scrap recycler in California
As of early July, he says his facility is “rocking and rolling again; demand is good on the sale side as well.”
In mid-July, however, new concerns emerged in several states as to whether more manufacturing shutdowns and restrictions could be looming with infection rates rising.
America’s steel mills are only very slowly raising their output and their demand for scrap. The Washington-based American Iron & Steel Institute reports that 1.27 million tons of steel were made in the U.S. in the week ending July 4. That represents a 2.3 percent increase from output the previous week, ending June 27.
The mill operating capacity rate rose to 56.6 percent in early July from 55.4 percent in the final week of June. These figures also represent a slight rebound from the 51.1 percent capacity rate for the week ended May 2.

Steel production figures in the U.S. remain far below their pre-COVID-19 counterparts from 2019. For the week ending July 4, total output was down 31.6 percent from the comparable week in 2019. In early July 2019, the mill capacity rate was 79.7 percent.
Longer term, a study released in early July sees a growing electric arc furnace (EAF) steelmaking sector in the U.S. as likely to lead to a strain on high-grade ferrous scrap and a viable market for domestically sourced ore-based metallics (OBMs), such as direct-reduced iron (DRI) and hot-briquetted iron (HBI).
The 15-page analysis by Arlington, Virginia-based B. Riley FBR Inc. sees increased demand for HBI and DRI in part because of new EAF melt shop capacity that is under construction and because of the potential scarcity of prime ferrous scrap grades.
The report, co-authored by Lucas N. Pipes, Matthew Key and Daniel Day, states in its summary, “As scrap prices move higher and an increasing number of EAFs look to move up the value chain into higher value-add products, demand for OBMs is nearing an inflection point, in our view.”

OBM projects that could find takers for their output include the HBI facility under construction by Cleveland-Cliffs Inc. in Toledo, Ohio, and coking metallics made by SunCoke Energy Inc. of Illinois.
EAF steelmaking is projected to grow thanks to several projects underway by Steel Dynamics Inc. in Texas; Nucor Corp. in Kentucky; U.S. Steel Corp. in Alabama; and Big River Steel (BRS) in Texas. (U.S. Steel partially owns BRS.)
EAF capacity expansions are underway or planned by Nucor in Kentucky; BRS in Arkansas; North Star BlueScope Steel in Ohio; and JSW Steel in Ohio and Texas.
If all those projects come to fruition, they would require as much as 3.7 million tons of prime scrap, putting a supply strain on a scrap commodity the authors say already is “dramatically reduced” in available volume.
The analysts say shredded or other forms of obsolete scrap are unlikely to plug the gap because of melt shop chemistry issues.
“As high-quality scrap has become increasingly scarce and the volume of higher value-add steel produced by EAFs continues to rise, demand for prime scrap and OBMs is, we believe, set to inflect higher,” the report notes.
In the heat of this summer, the analysis may seem a little distant after two different companies announced the closing of three scrap-melting iron foundries, eliminating scrap consuming options.
Media reports and federal Worker Adjustment and Retraining Notification Act filings indicate Southfield, Michigan- based Grede Holdings LLC plans to close foundries in Columbiana, Alabama, and Waukesha, Wisconsin, while Wisconsin-based Waupaca Foundry Inc. announced plans in late May to close its Lawrenceville, Pennsylvania, ductile iron foundry.
Get curated news on YOUR industry.
Enter your email to receive our newsletters.
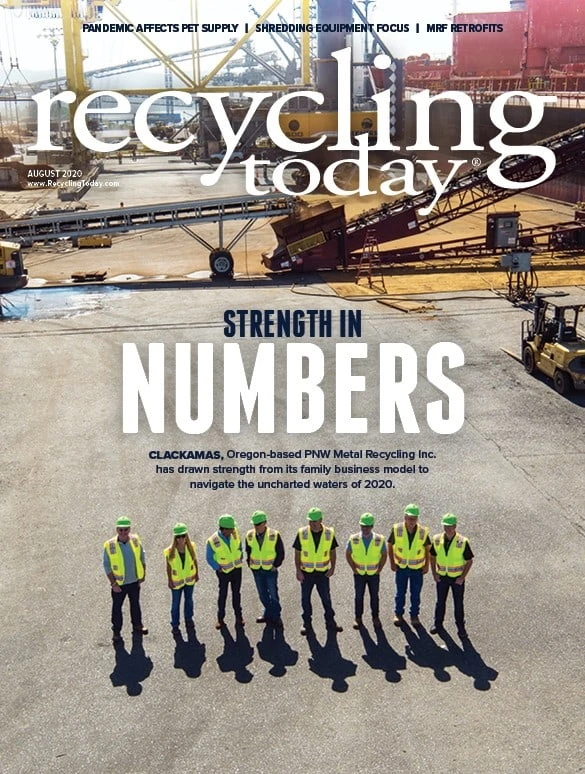
Explore the August 2020 Issue
Check out more from this issue and find your next story to read.
Latest from Recycling Today
- ReMA opposes European efforts seeking export restrictions for recyclables
- Fresh Perspective: Raj Bagaria
- Saica announces plans for second US site
- Update: Novelis produces first aluminum coil made fully from recycled end-of-life automotive scrap
- Aimplas doubles online course offerings
- Radius to be acquired by Toyota subsidiary
- Algoma EAF to start in April
- Erema sees strong demand for high-volume PET systems