Operating iron foundries when the transportation sector is in a trough has historically proven to be a difficult proposition. In the current downturn, a group of investors has used the lull to combine, reorganize and reinvest in three former companies now operating as one.
Grede Holdings LLC, Novi, Mich., was formed in the first quarter of 2010 through the combination of the assets of the former Grede Foundries Inc. with Citation Corp., which had previously acquired Blackhawk Foundry of Davenport, Iowa.
The newly combined company operates 14 foundries and two machining plants with its strongest regional presences in the Upper Midwest and Alabama.
Grede can draw upon historic foundry operating roots tracing back 90 years while also touting a number of innovative processes that company leaders say will help Grede remain competitive in the decades ahead.
SPREADING ITS ROOTS
According to Doug Grimm, the new company’s chairman, president and CEO, the Grede Holdings LLC legacy dates to 1920, when William J. Grede started an iron foundry known as Grede Foundries.
That company grew and added several other foundries to its operations, but the automotive and truck sales slump that started in 2007 caused the former Grede Foundries to file for Chapter 11 bankruptcy protection in June of 2009.
In a deal that closed in February of 2010, six of the Grede foundries were purchased by an investment group known as Wayzata Investment Partners. Wayzata was already familiar with the foundry industry, as it was also a shareholder in Citation Corp. along with the GSC Group.
Citation had been based in Novi (in suburban Detroit) as a privately held corporation with 1,100 employees at 11 casting and machining plants in Alabama, Indiana, North Carolina and Wisconsin. Citation had been led by Grimm as its CEO since 2008.
“The combination of Citation, Blackhawk and Grede creates what we believe is the most diversified foundry company in North America with one of the strongest balance sheets in the industry,” Grimm remarked when the deal was concluded in February. “We expect revenue to reach $600 million in 2010 through our combined business in the automotive, industrial and heavy truck markets.”
The new Grede has 3,000 employees, two machining facilities and 14 foundries with nearly 600,000 tons of iron casting capacity. The company has the ability to produce and machine ductile iron, gray iron, lost foam and high-silicon molybdenum cast component parts and assemblies ranging from 1 pound to 2,000 pounds in size, says Grimm.
“The objective in combining these three great companies is to harness the best of each companies’ people, assets and technologies to provide an unparalleled array of products and capabilities to the iron castings market,” says Grimm.
MARKETS MATTER
Grede foundries and plants are capable of making materials and components for a number of industries and applications, but historically the automotive market has been the big wheel. This mirrors the iron foundry sector overall.
According to Grimm, Grede sales by market are 45 percent automotive, 27 percent medium- and heavy-duty truck and 28 percent are classified as “industrial,” which includes several sub-categories.
Although this means 72 percent of the company’s sales are going into the transportation market, Grimm indicates that the mix makes Grede “the most diversified casting supplier in North America.”
The catch-all “industrial” category includes the mining, construction, wind energy and railroad and agricultural industries as some of its larger sub-categories, says Grimm. A company goal, he says, will be to grow Grede’s presence in these sectors as well as in the heavy truck sector. “We’d like to see our sales at roughly even in one-third segments in those three main categories, so we’d like to grow the two non-automotive sectors to be more balanced in our diversity,” he comments.
The company’s “lost foam” iron casting process and high silicon molybdenum application comprise a growing portion of its business and are likely to remain growth areas, says Grimm, because the processes produce the lighter-weight components favored by vehicle makers trying to meet CAFE (Corporate Average Fuel Economy) standards. These components include turbo housings, diesel engine manifolds and integrated axle assemblies.
In the process, foam patterns are combined into one assembly to create near-net casting components for engine, chassis, suspension and steering applications in the transportation and industrial markets, says Grimm.
During the process, the molten metal evaporates the foam pattern to form the desired part. The lost foam process can be used to create complex parts that traditional casting processes can have difficulty replicating, according to Dale Weeldreyer, Grede’s vice president of purchasing and facilities engineering. Additionally, the process provides up to a 25 percent cost reduction and up to a 30 percent weight reduction, reduces the complexity of the part, can create more consistent part quality and even improved part stiffness, strength, balance, durability and performance.
Grimm and Weeldreyer say they are confident that the lightweight components produced by the lost foam process will continue to gain favor. Regarding overall demand for cast foundry products, Grimm says, “We are approaching the markets we serve with cautious optimism and are looking at a ‘Nike swoosh’ type of recovery over time. We expect our heavy-duty and industrial businesses to grow somewhat, while automotive is just starting to surge upward again.”
ON THE SCRAP SIDE
The 14 foundries operated by the new Grede Holdings LLC combine to serve as a major consumer of ferrous scrap at destinations as far south as Brewton, Ala., and as far north as Kingsford, Mich., in that state’s Upper Peninsula.
The company has 600,000 tons of annual iron-making capacity, and ferrous scrap is the key ingredient.
To make its ductile iron and gray iron castings and components, Grede uses a combination of several types of scrap, according to Weeldreyer, including shredded black clips, steel stampings, skeleton scrap, cast scrap, alloyed scrap, slitter and other busheling and bundled scrap.
“Steel scrap and other components are melted to exacting customer specifications for metal chemistry, strength and mechanical properties for their applications,” says Weeldreyer. “Scrap steel, pig iron and other alloying elements are melted and poured in controlled conditions to cast to the shapes required. These ‘recipes’ give customers various grades of gray iron, ductile iron and high silicon molybdenum castings for incorporation in their products.” He adds, “Grede products are known for their quality, and our control of the chemistry and of the processes will continue that tradition of quality.”
Weeldreyer says that in recent months, the newly combined Grede Holdings has been consuming from 22,000 to 25,000 tons of scrap per month. “We typically purchase from brokers and dealers situated in the Southeast and the Midwest,” he notes, which matches up with the company’s presence in those two regions.
Scrap sellers’ concern with the credit and payment situation has not been lost on Grimm, who says, “Grede is a new company with considerable backing and a highly de-leveraged balance sheet—suppliers need to know that.”
In Grimm’s 26-year career, he has become familiar with many layers of the automotive industry supply chain, having worked in sales, quality, production and materials management positions with companies such as Visteon Corp., Metaldyne, Dana Corp. and Chrysler Corp.
Similarly, Weeldreyer’s 40-year career has spanned foundry production and engineering positions with several manufacturing companies, including Navistar, John Deere and General Motors.
Grimm says he has a favorable impression of the scrap industry. “Our suppliers provide good quality materials, and we’re happy with their day-to-day operations; we’ve had good shipments lately.”
THE ROAD AHEAD
For Grimm, Weeldreyer and the 3,000 employees of Grede Holdings, the task will be to manage a company in an industry that has been considered by most observers to have too much capacity.
“There was too much capacity in the foundry industry,” Grimm acknowledges. “In the sector we deal in, there has probably been 1 million tons of capacity taken out in the last two years—either shuttered or idled. The most efficient and productive players make up the remaining capacity as the market warrants,” he adds. “There is a little bit of Darwinism or survival of the fittest taking place, which is why we always want to strive for continuous improvement.”
Beyond market conditions, Grimm says, “Our guiding principles focus on building lasting relationships with people and treating them fairly and honestly. We expect a lot of ourselves in terms of meeting our customers’ needs and, in turn, we strive to maintain a strong working bond with our stakeholders and customers. The customers deserve it.”
Grimm says he is confident the newly configured Grede Holdings LLC can serve its customers from a platform of financial strength and operational excellence.
Grede is a diversified foundry company “with one of the strongest balance sheets in the industry,” Grimm says. “The significant equity investment from Wayzata and the GSC Group has reduced total funded debt of the two companies by 80 percent, or $110 million. This gives us a best-in-class financial profile, allows us to invest appropriately and weather economic cyclicality moving forward.”
“The essential value proposition in creating the new Grede is taking the best people, assets and technology and applying the strengths of each organization to the overall new company,” says Grimm. “I anticipate there will be a lot of back-and-forth communication to create a bigger, stronger company.”
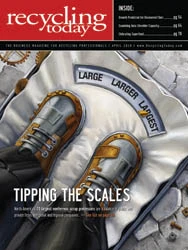
Explore the April 2010 Issue
Check out more from this issue and find your next story to read.
Latest from Recycling Today
- LumiCup offers single-use plastic alternative
- European project yields recycled-content ABS
- ICM to host colocated events in Shanghai
- Astera runs into NIMBY concerns in Colorado
- ReMA opposes European efforts seeking export restrictions for recyclables
- Fresh Perspective: Raj Bagaria
- Saica announces plans for second US site
- Update: Novelis produces first aluminum coil made fully from recycled end-of-life automotive scrap