STANDING ORDERS
Pricing momentum seems to have swung back to scrap dealers as March has progressed, as overseas buyers and domestic mills have been dueling to snap up available supply.
Many dealers were claiming in early March that their supply was already committed for the rest of the month. "I’ve got a home for everything in my yards," says one Midwestern dealer of his ferrous scrap inventory.
The same dealer reports that domestic mills are back in the markets for higher grade scrap, after spending the last several months melting more pig iron, iron alternatives and lower grade scrap in an effort to avoid costly premium grades.
In March, buyers in many parts of the country worked their way through their supply chains to find ferrous scrap that was not yet spoken for.
Steel mill capacity figures are indicating that mills continue to have full order books as they melt at a healthy 90 percent or more of capacity on average.
Good news from the U.S. economy in mid-March may fuel even more optimism and spending, keeping the steel-intensive auto and construction segments healthy.
Their situation has not been helped any by increased demand from China. While Chinese steel mills have been buying from the North American market for some time, Chinese foundries are now also part of the equation.
While not needing to buy in bulk shipping amounts, Chinese foundries have been increasingly willing to buy container shipments of ferrous scrap. This type of overseas order has been steadily building for the past several months.
Market watchers are split on whether global supply to feed hungry Chinese steel furnaces is catching up with demand. Scrap suppliers might be getting a preview of the push and pull forces that will affect their market for the rest of the year by watching iron ore pricing negotiations between steel mills and their suppliers.
In March, these negotiations started off with some iron ore suppliers asking for higher pricing for throughout 2005. It appears, though, that steelmakers may be able to suppress the price increases because several major suppliers have ramped up production to meet the new global reality of China as the new number one consumer of iron ore and ferrous scrap.
(Additional news about ferrous scrap, including breaking news and consuming industry reports, is available online at www.RecyclingToday.com.)
China's Anshan Iron Merging with Benxi Steel Group
Anshan Iron & Steel Group, the second largest steel producer in China, has announced plans to merge with Benxi Iron & Steel Group. The combined production of the two companies will bring it close to the level of Baosteel Group, the largest steel company in China.
According to published reports the combined capacity of the two mills will be around 20 million metric tons, compared to 21.4 million metric tons Baosteel presently has.
The merger of the two steel companies follows a trend sweeping the global steel industry, as the largest steel companies are looking to grow their capacity through a host of acquisitions.
The combination of the two steel companies could give them a better position to negotiate for the raw materials needed to feed their furnaces.
BAYOU STEEL REPORTS Q1 FINANCIALS
Bayou Steel Corp., LaPlace, La., has reported its financial results for the first quarter of fiscal year 2005. The company emerged from bankruptcy pursuant to a reorganization plan that became effective Feb. 18, 2004.
The company reported net income of $4.2 million for the first quarter of fiscal 2005. The predecessor company reported a net loss of $0.6 million for the first quarter of 2004.
Sales for the quarter were $63.1 million on shipments of 113,080 tons. This was sharply higher than the $51.7 million in sales on shipments of 151,184 tons for the comparable quarter for fiscal year 2004.
The average selling price for the quarter increased from $339 per ton to $552 per ton, or 63 percent, compared to the first quarter of last year. The selling price increase has generally been related to the sharply escalating prices for scrap and the increasing prices for alloys and fuel, which Bayou has been successful in passing through to its customers, according to a release from the company.
"Earnings in the first quarter of fiscal year 2005 have increased significantly as compared to the prior year quarter. Despite a decline in shipments, the strong selling prices contributed to the growth of sales and earnings," Bayou President and CEO Jerry Pitts says. "This favorable turnaround is largely the result of increased demand for our products, particularly in 2004, which allowed us to raise our product prices at a higher rate than the unprecedented increases in the cost of scrap," he adds.
Pitts says that while Bayou experienced significant increases in the cost of electricity, natural gas and alloys, the company’s margins have improved because its product pricing increases have outpaced operating cost increases. "Given the challenges of the last four years in the steel industry, it is especially pleasing to see a healthy market," he adds.
Bayou shut down its furnaces in December to conduct equipment maintenance that was partially deferred in light of limited funds during the company’s bankruptcy. Pitts says that since the start-up, the mill’s production and efficiencies have increased at its Louisiana and Tennessee plants. "This will enable us to better capitalize on current great market conditions," he says.
In December, Bayou opened a remote scrap processing location. "After a ramp-up period, we expect this facility to provide the Louisiana plant with additional scrap metal," Pitts says. The company was also able to increase capacity use by 15 percent at its Tennessee plant because it was able to buy billets economically in the fall.
UKRAINE CUTS SCRAP EXPORTS
Ukraine reduced its ferrous scrap exports by more than 20 percent for the first month of the year, compared to the previous month. For January, the country exported 162,900 metric tons, compared to the previous month’s figure of 175,700 metric tons.
According to Interfax, the country expected to further reduce its ferrous scrap exports in March, with the expectation than no more than 150,000 metric tons of ferrous scrap exported for the month.
Meanwhile, steel mills in Ukraine have taken in around 465,600 metric tons during January.
Ukrainian ferrous scrap exports increased by 35.2 percent last year to 2.44 million metric tons. At the same time, supplies to the country’s own steel mills grew 15.6 percent to 6.91 million metric tons.
SMORGON UPBEAT ON MARKETS
Australia-based Smorgon Steel Group says its outlook for 2005 remains positive despite continued pressure from the high cost of raw materials.
Smorgon Managing Director Ray Horsburgh says the company has achieved higher prices for its products, helping it to rebuild margins that had declined in the preceding year in light of the escalating cost of scrap metal and other raw materials.
Horsburgh says hot-rolled coil prices were still strong and looked set to rise again in the year ahead.
While Smorgon has little room left to increase its tube prices, demand is strong for the group’s products, ensuring healthy volumes.
Horsburgh also says the dumping of cheap imports that impacted the company’s results in the last six months should ease in the next six months.
"We have not seen any material weakness in demand for our products and, so long as we do not again experience the irrational trading conditions we faced for much of 2003/04, we expect our second half financial performance to be better than the first half," he says.
Smorgon reported a net profit of $48.09 million for the six months period ending Dec. 31, 2004, up 94 percent on corresponding period for the previous year.
Horsburgh says that while ferrous scrap prices have not continued with the extraordinary growth rates from the previous year, demand for hot rolled coil was still strong, pushing prices higher.
"The market remains buoyant and we expect that to continue right through this calendar year. There’s no indication from any of our sectors of any slowdown," he says.
Smorgen says the commissioning of a new mega-shredder for its recycling operations in New South Whales is scheduled for the quarter ending June 2005. Once it is complete, two smaller New South Whales shredders will be relocated to South Australia and Western Australia.
Wheeling–Pitt Announces 2004 Results
Wheeling-Pittsburgh Corp., the holding company of Wheeling-Pittsburgh Steel Corp., has reported its financial results for the year and quarter ended Dec. 31, 2004.
For 2004, the company has reported net income of $62.5 million. Net income for the fourth quarter of 2004 totaled $6.4 million. This compares with a net loss of $23.7 million in the fourth quarter of 2003, and net income of $35.6 million for the third quarter 2004.
"Our strong financial performance in 2004 and successful secondary public stock offering significantly strengthened our liquidity as we entered 2005," says James G. Bradley, chairman, president and CEO. "Additionally, production from our new Consteel electric arc furnace, which began operation in the fourth quarter and is exceeding the manufacturer's production guarantee, is bringing about our transition to a hybrid steel producer."
The company says net sales for 2004 of $1.4 billion on shipments of 2.1 million tons, with an average steel price per ton shipped of $661. Cost of goods sold in 2004 totaled $1.2 billion, averaging $568 per ton shipped.
Wheeling-Pitt’s net sales for the fourth quarter of 2004 were $373.7 million on shipments of 503,000 tons of steel products, with prices averaging $743 per shipped ton, down slightly from the third quarter. Cost of goods sold totaled $336.4 million and averaged $669 per shipped ton.
Costs in the quarter included maintenance spending in connection with planned outages at the company’s hot strip mill and finishing mills, as well as costs incurred during 12 days in December following a BOF ductwork collapse, during which there was minimal production. Raw material costs increased slightly above third quarter levels despite significantly less purchased coke in the fourth quarter, Wheeling-Pitt reports.
The company says it expects shipments for the first quarter of 2005 to be between 500,000 to 515,000 tons, with the average selling price comparable with the fourth quarter.
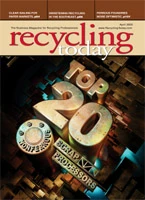
Explore the April 2005 Issue
Check out more from this issue and find your next story to read.
Latest from Recycling Today
- Fitch Ratings sees reasons for steel optimism in 2025
- P+PB adds new board members
- BlueScope, BHP & Rio Tinto select site for electric smelting furnace pilot plant
- Magnomer joins Canada Plastics Pact
- Out of touch with reality
- Electra names new CFO
- WM of Pennsylvania awarded RNG vehicle funding
- Nucor receives West Virginia funding assist